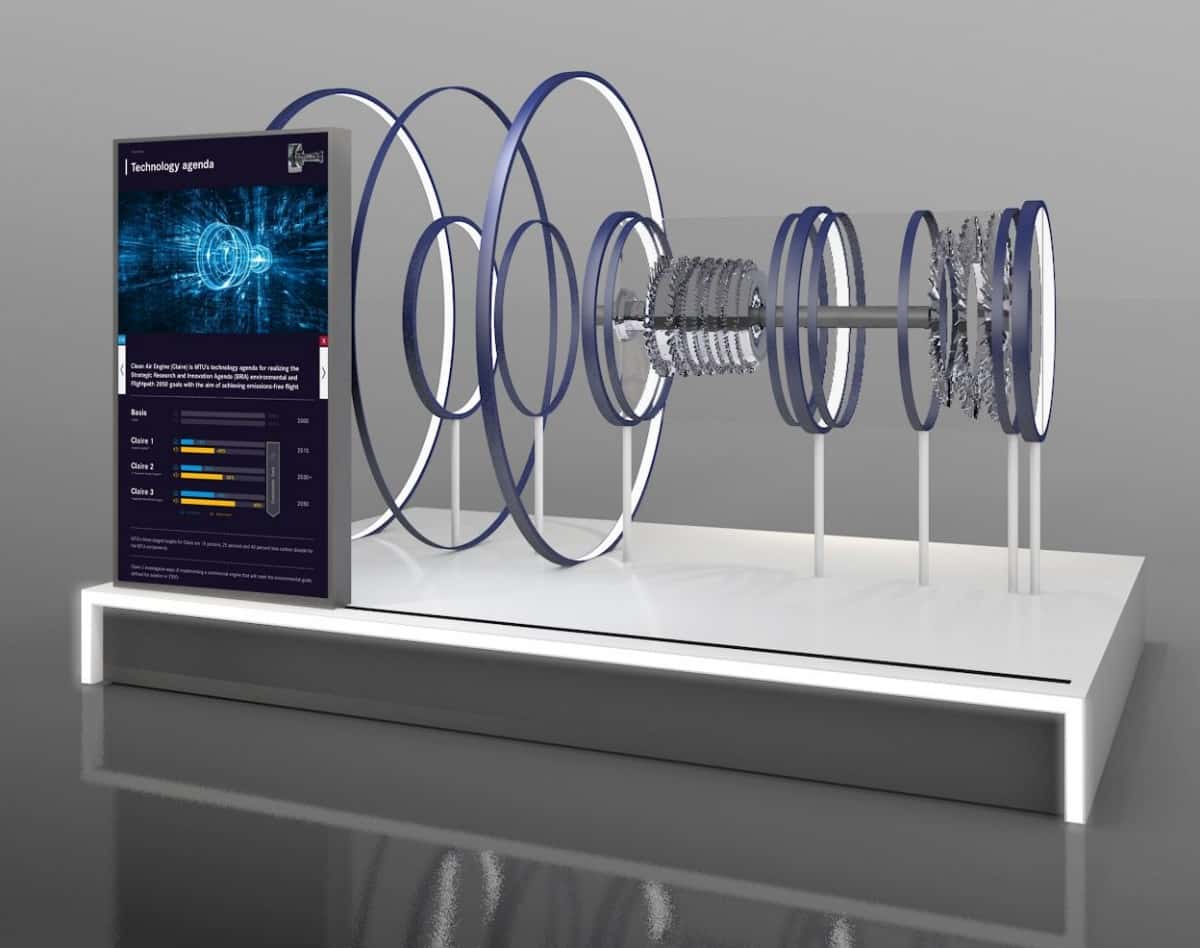
In the wake of climate change, even aircraft engines seems to need a change. The engine manufacturer mtu used this year’s Aero Salon in Paris to present some of its concepts for the next generation of jet engines and beyond.
At Paris, mtu showcases new engine concepts
As passengers, we usually don’t notice much of it. But the engines powering the Airbuses and Boeings must become quieter and more economical in order to meet the climate goals put forward by politics. As early as 2011, the EU White Paper on Transport set a target of reducing greenhouse gas emissions by at least 60 percent by 2050 compared with 1990 levels. In addition, aviation is to use up to 40 percent CO2 fuels from sustainable production by 2050.
mtu already produces the ecologically-friendly geared turbofan engines together with Pratt&Whitney. Geared turbofans use two or even three drive shafts. A reduction gear operates between the low-pressure turbine and the large fan installed at the front of the engine.

Foto: Tosaka via Wikimedia Commons.
This allows the fan to run more slowly and the low-pressure turbine to run faster. Thus, both engine components operate in their optimum power range. This makes the entire engine quieter and more economical. Compared to conventional engines, fuel savings of around 10 percent are possible.
Climate change demands new solutions
However, according to the mtu managers, the targets set by policymakers can only be achieved with new technologies. The company’s developers are working on two new solutions. The so-called composite cycle approach adds a piston compressor and engine to the high-pressure compressor. “This would enable us to significantly increase thermal efficiency,” explained Dr. Stefan Weber, Head of Technology and Preliminary Design.

Illustration: mtu
The STIG Cycle Engine uses the energy taken from the exhaust gas to generate additional power. STIG stands for “Steam Injected Gas turbine”. Water vapour is injected into the gas turbine, which in turn comes from a heat exchanger at the engine outlet. This wet combustion process has made it possible to significantly reduce both CO 2 and nitrogen oxide emissions.

Illustration: mtu
Long-term goal: Flying without emissions
A further step towards climate-neutral aviation are sustainably produced synthetic fuels, which could be manufactured using solar energy. They would not require new infrastructures.
The mtu developers are also looking at electric drives. Provided that the electricity used would be generated in a climate-neutral way, emission-free flying would be possible in this way. However, the output of today’s battery systems is not yet sufficient to power a large commercial aircraft.
One possible approach would be using turbo-electric or hybrid-electric systems. Gas turbines and generators in den fuselage would generate electricity. This, in turn, would drive fan propellers distributed along the wings, a solution that is already used in several air taxi concepts today. However, these concepts still have to prove their feasibility.