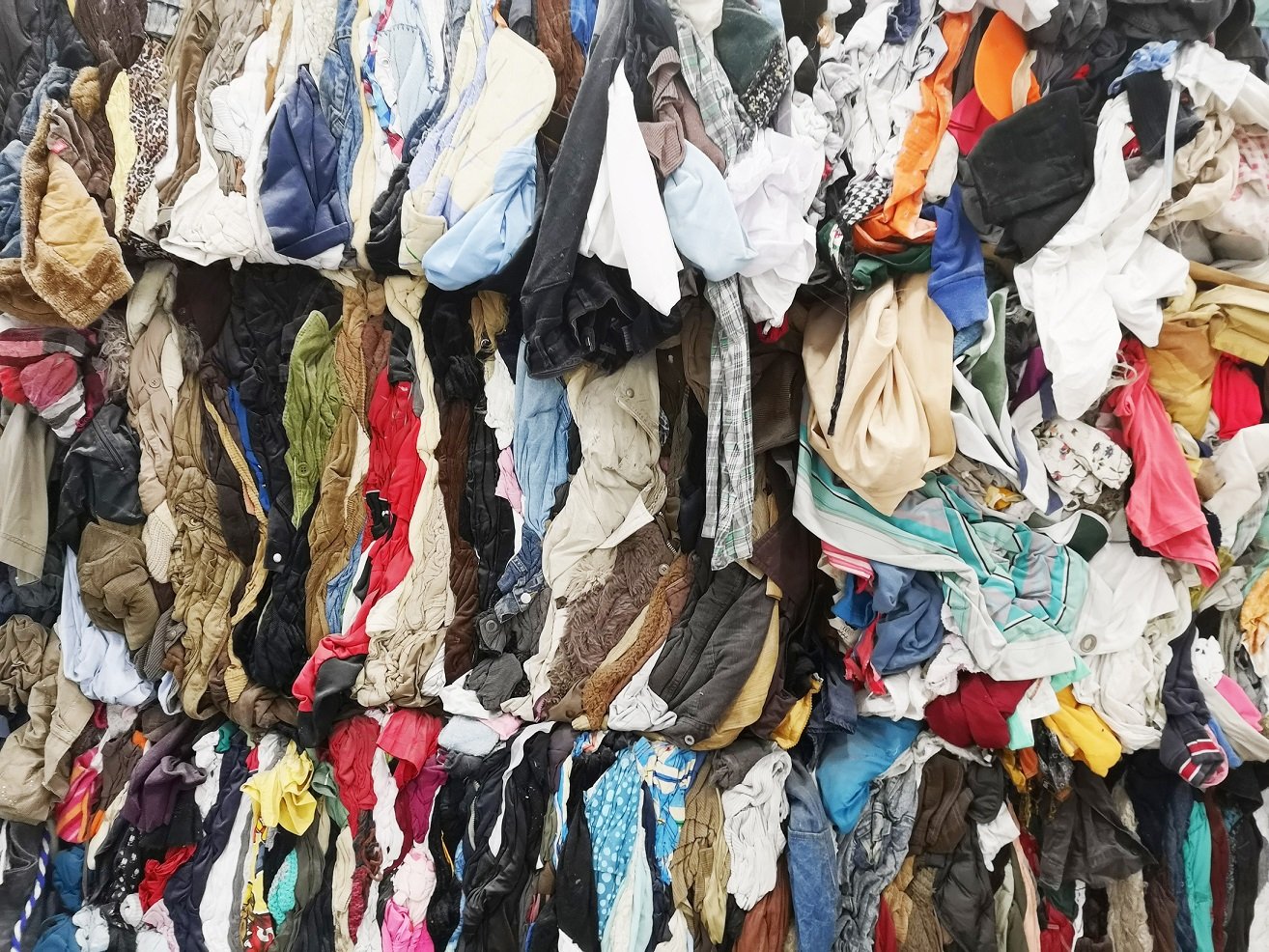
According to one of the statistics from the German Federal Association for Secondary Raw Materials and Disposal (BSVE), 10.01 metric tons of old clothes, and new clothes that have never been worn, invariably end up in the trash every year. Most of this is incinerated or processed into low-quality non-wovens, as there is no way to recycle the fabrics back into high-quality materials. The composite textiles cannot simply be separated out again. Or, when this can be achieved, it is only through elaborate, chemical (and therefore not very environmentally friendly) processes.
But this could all change thanks to a new, mechanical process that the engineering and development service provider imat-uve is working on in conjunction with a German-Dutch project consortium. The resulting recycled yarns and woven fabrics will be used primarily in the automotive industry, but also in sectors such as architecture, home textiles, and clothing.
High-quality recycled yarns
In the new process, composite fibers are torn very finely and, thanks to new spinning preparatory technologies, are processed into a particularly soft, smooth, and uniform card silver that is ideal for spinning. The high-quality yarns (Nm15 and Nm28) that are produced from this process should be suitable for further processing. According to the company, these could then meet various requirements, depending on how the polyester is blended.
“In the trials of the project, 12 yarn qualities in different mixing ratios have been spun in the meantime. All approaches to spinning, both in the pilot plant and on industrial spinning machines, led to very good results. The raw material for the production of the yarns consists of sorted used workwear (made of 60 percent polyester and 40 percent cotton) and old clothes (made of unknown fiber blends) as well as raw polyester,” the company went on to state in their press release.

The inventors are pleased to report that it has even been possible to weave yarn from 100 percent composite fibers on an industrial scale without any complications. “There were no thread breaks and hardly any fiber
abrasion during weaving.” Earlier tests with the new technology had already successfully passed standard tests for the automotive industry, “where high demands are placed on the durability and comfort of the
textiles.” Imat-uve is now confident that future test results for existing fabrics will be even more promising.
Also interesting: Old T-shirts are given new life as elegant viscose clothing
In further weaving trials this year, yarns made of 100 percent composite fibers are to be processed not only as weft but also as warp threads. “A yarn spun with open-end technology in a gauge of Nm28/2 will be used as a
warpable variant in the next series of tests.” In addition, mixed fiber recycling is also interesting for sophisticated designs, since mixing materials and colors in the raw material leads to attractive hues in the yarn and fabric. “Special color compositions are also possible through targeted pre-sorting of the old clothes.”
A push for the textile industry in the border region between Germany and the Netherlands
The joint project of the partners imat-uve, C2C ExpoLab, FBBasic, the Texperium Foundation, and Trützschler aims to reduce the CO2 footprint of textiles and strengthen the textile industry in the Rhine-Meuse region. Furthermore, the process and product innovation shall be used “to establish the textile industry in the border region between Germany and the
The Netherlands as an innovation leader in the field of mixed fiber recycling and textile recycling management.”
The project is supported by the European Union within the framework of the INTERREG Germany-Netherlands programme and co-financed by the German Ministry of Economic Affairs of North Rhine-Westphalia (MWIDE NRW), the Dutch Ministry of Economic Affairs and Climate (EZK) and the Dutch provinces of Limburg and Overijssel.