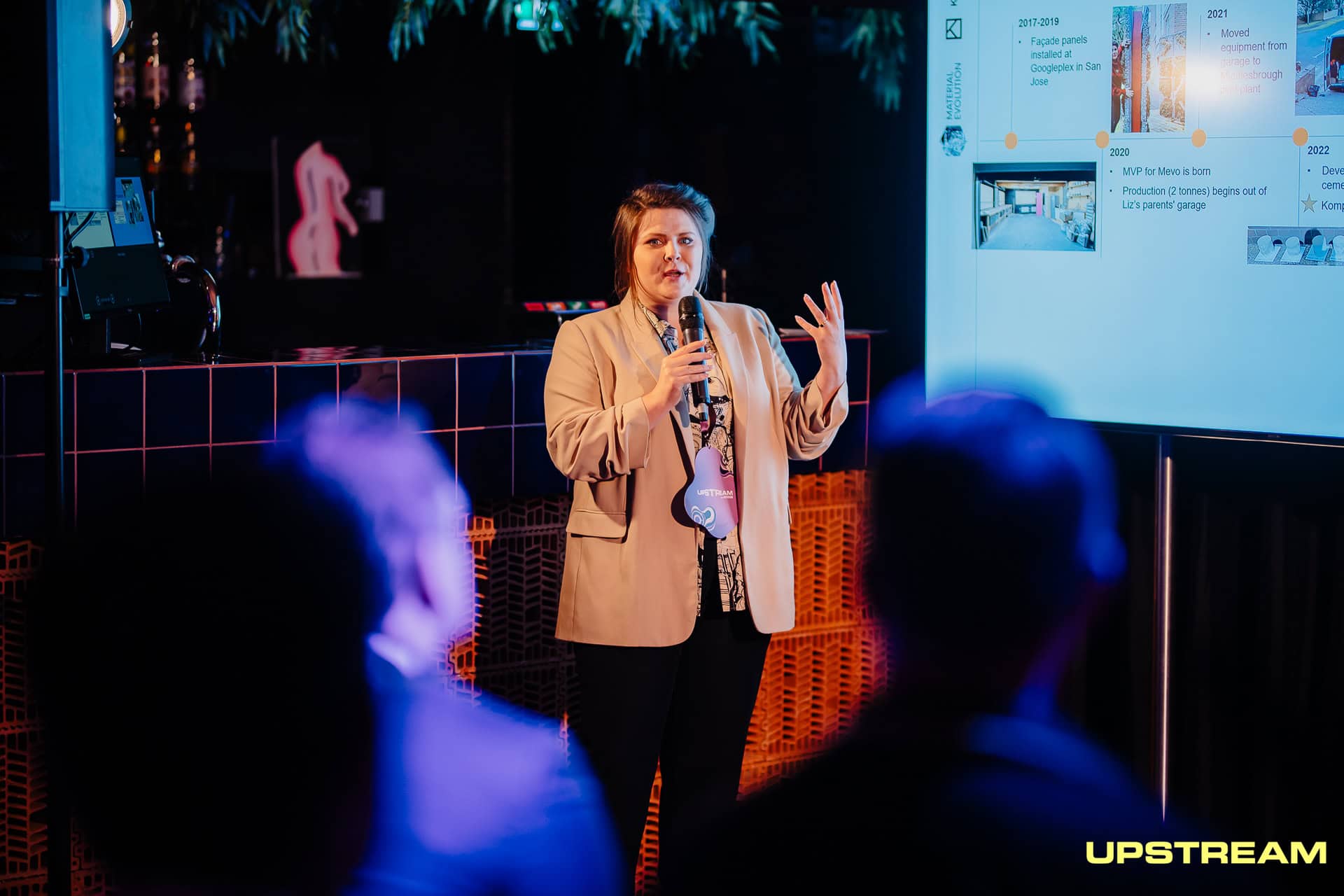
The cement industry is behind 8% of global CO2 emissions. Mining materials, but most importantly, the high energy inputs to reach the temperatures needed in the chemical processes to produce it—with kilns getting heated over 1400°C and limestone burning—are the main drivers behind the staggering emissions figures. If cement were a country, it would be the third largest carbon dioxide emitter, right after China and the United States.
Why this is important:
The construction industry is by far the world’s largest emitter of greenhouse gas emissions – 37% of the global amount. As Europe and the world aim to reduce their footprint and achieve climate neutrality, greening cement production means taking an important step ahead.
Material Evolution is setting a new standard. It manufactures cement from industrial byproducts through a special reactor that operates at room temperature. The process results in a product that can deliver 85% less emissions than conventional cement production. As the team explores different waste streams to analyze which can be best used for cement production, it also leverages machine learning algorithms to achieve consistency.
Elizabeth Gilligan is the company’s CEO and founder and chose entrepreneurship over a career in academia. She was also a speaker at the Upstream Festival, one of the main startup events in the Netherlands, where she told more about her journey as a founder and entrepreneur. Gilligan spoke to IO right after her speech on stage.
How does Material Evolution technology work?
“At Material Evolution, we don’t think there will be one material to save the world. Instead, we think many materials will help solve the climate crisis. We produced a reactor that uses alkali fusion – a process used in metallurgy to make materials further treatable, ed. – to force phase changes in particles, getting them to stick together and become cement. You can think of it as a giant Nutribullet that spins these materials, coats them, and more to transform industrial waste, such as steel slags and mining tailings, into cement. Currently, our process results in 85% less emissions than conventional cement, but we are working on a carbon-negative process.”
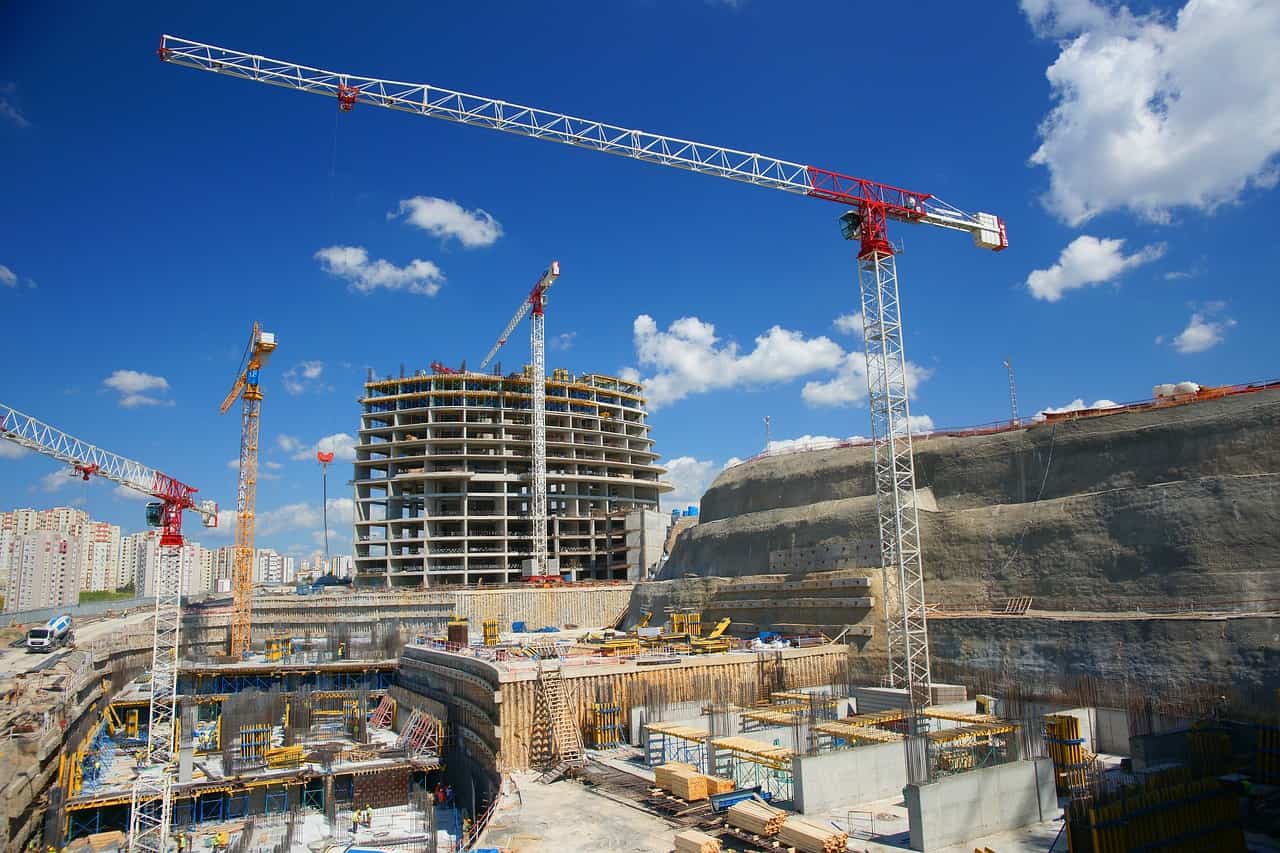
How did the idea come to be?
“Material Evolution was the side hustle of my Ph.D. on sustainable cement, and it originated from some questions: What if you don’t need heat to make cement? What if you can blend hardware and software? What happens? So that’s how the idea formed. I was offered a route to professorship, but it felt morally unjust not to be doing something impactful.”
How did you realize that it was the right thing to do?
“It wasn’t straightforward. I feel like you fall into it; I knew climate was super important and something I wanted to work on. Back then, I wasn’t realizing the value and the impact of the idea, and it kept evolving over time. I used to ask people I met to tell me if the concept was bad, just because I didn’t want to waste time on a not-so-good idea and rather focus on something more impactful.”
Still, we struggle to get more research out of labs and have an impact. How do we get academians to take the step you took?
“Undoubtedly, it’s a hard pathway to see, but more support would help. In our case, we got lucky as I got grant funding during my Ph.D. and also a Google fellowship that helped me see this possibility. Back then, I could choose between teaching and an entrepreneurship course, which I decided to pursue. It helped me open my eyes, realizing I was good at it. In my opinion, academics usually make good entrepreneurship.”
How can an academic become a good entrepreneur?
“You have to be curious. I think you want people who are happy being uncomfortable and being the dumbest person in the room. There has to be a way to get fundamental science into startups. I think a lot has to do with the way teams are built. Maybe the technical person doesn’t need to be the CEO. So, how do you build a team around the idea you have? How are you okay with things failing? As an academic, you don’t really want your research to fail.”
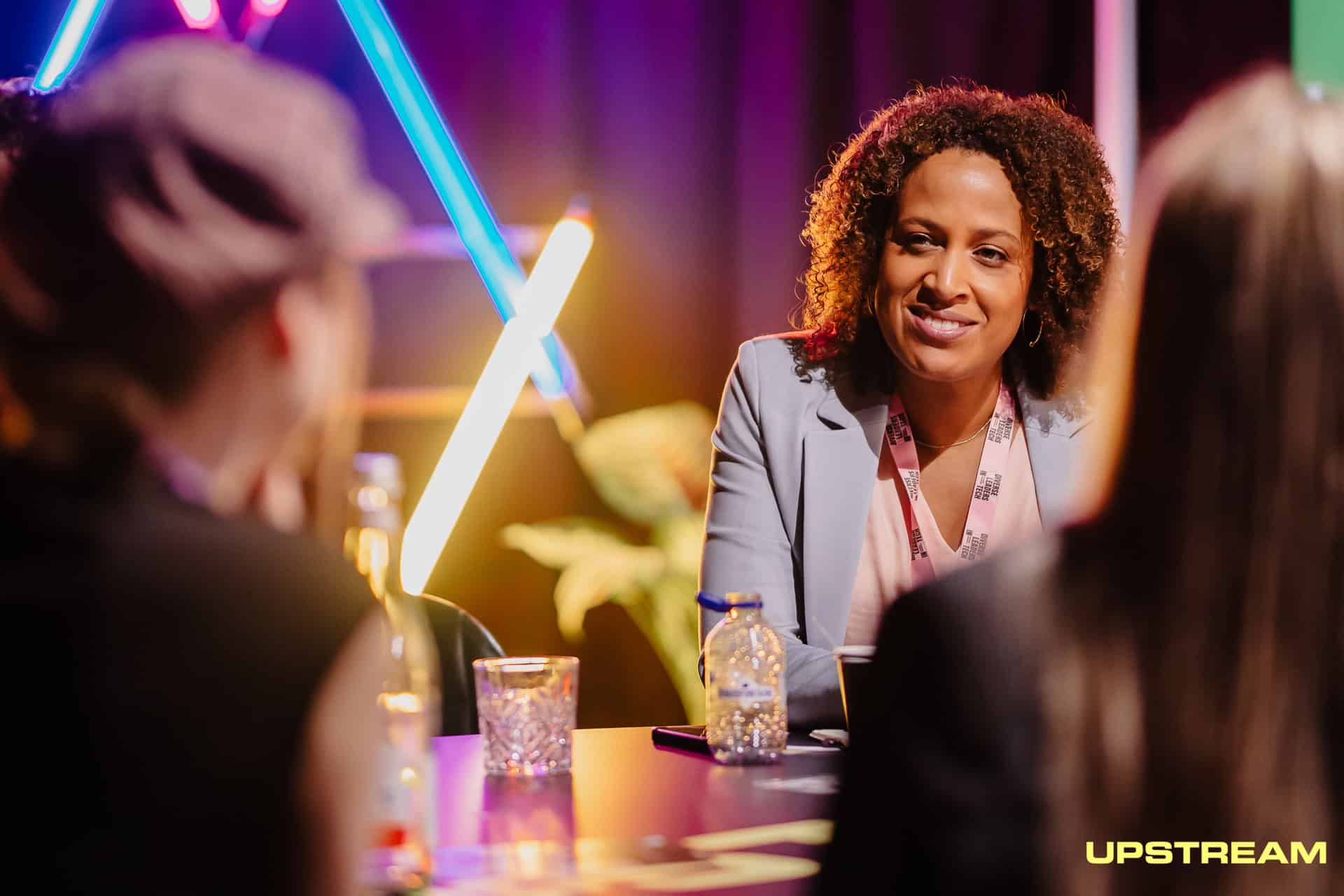
Your company was founded in 2020. Can you take us through the past four years?
“It was 2020, and we hoped to rent some lab space to scale up, then COVID-19 hit. So, I convinced my parents we should convert the garage into a lab because we had work to do. We did it, and we bought the first machine from eBay. During that time, it was all about talking to customers and building the tech. And in the garage, we produced the first two tons of cement without any ventilation. We gassed everyone up, but we made it.
After the first customer tests, everyone got excited, building important relationships. Then, we received a £1.8 million grant funding and learned how to raise money and talk to VCs. Afterward, we built our four-ton-an-hour pilot plant and hired the first people. Now, we are on track to build a 25-ton-an-hour plant.”
As a founder, how do you see the British innovation ecosystem responding to Brexit?
“At this point, it’s hard to tell what the effects of COVID are and what the effects of Brexit are. Many companies are still looking and working with Europe as if nothing happened, and materials imports and talent hiring are harder. As a company, we are lucky to be able to support visas for people, but I know of many smaller businesses that can’t. But also, we have been working with a Spanish company, and getting the permits for them to be able to do work became so hard that it seems pointless.”
In your opinion, how can the concrete industry change?
“The industry will change with partnerships. As much as I’d love to be that idolized founder who changed the industry, we can’t do this alone. We have disruptive technology, but we are partnering with the industry because they are very knowledgeable. They know how to move millions of tons of powder; we don’t have to reinvent that. Also, we prefer establishing deeper relationships with customers as we look to be seen as a partner in the industry and the climate transition.”