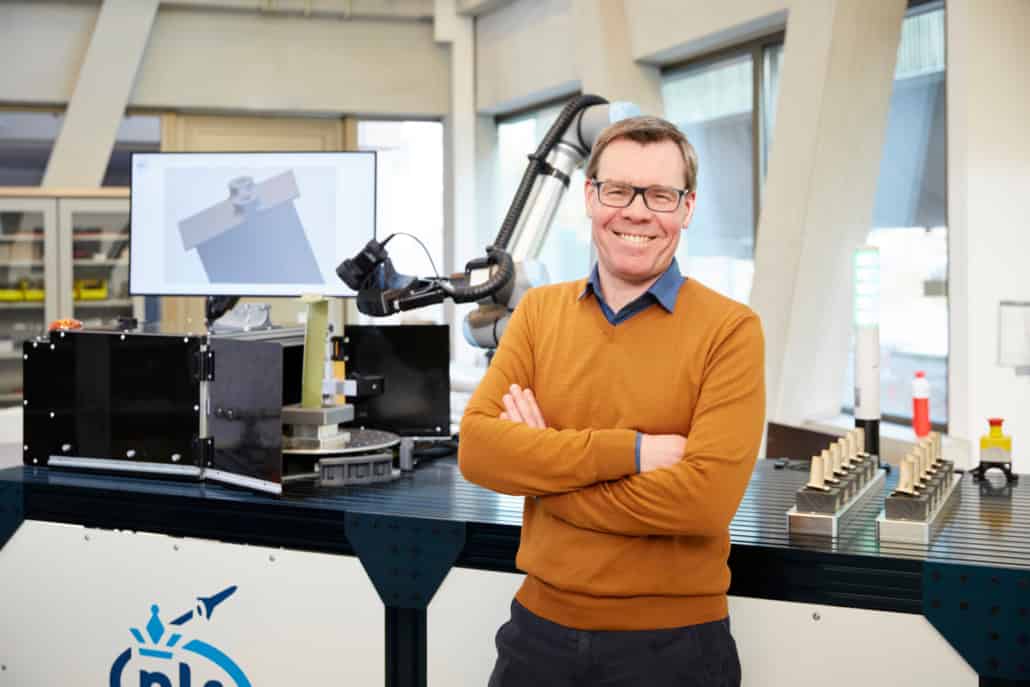
The pilot announces that the descent will commence in ten minutes. The flight attendant checks that all seat belts are fastened, tray tables are stowed, and seats are in the upright positi. The cabin crew are the customer-facing staff who keep the aviation sector going. They are backed up, though, by maintenance technicians who are the invisible backbone of aviation.
To give you an idea: on average, an aircraft is grounded for several days once every couple of months for detailed checks, in addition to the relatively small servicing tasks. Once every two years, all components are examined in greater detail and updated, and an aircraft is turned virtually inside out every six to ten years. So it is pretty clear that maintaining an aircraft takes a lot of time and manpower. It is becoming increasingly common for airline companies to cancel flights because they have no choice but to keep part of their fleet grounded. One of the key reasons? A shortage of maintenance technicians.
Why this is important:
As a structural integrity specialist, Arjan de Jong helps keep aviation safe. His work contributes to innovation and progress in this industry.
Using technology and scheduling to reduce the burden of maintenance
Keeping aviation operational is therefore a complex, crucial and above all “really interesting” puzzle to solve, if you ask Arjan de Jong. He is a Principal R&D Engineer at the Maintenance and Engineering Technology (MAE) department of NLR, the Netherlands Aerospace Centre.
The staff at the MAE department work on smart solutions for optimising maintenance operations, maintenance scheduling and allocating resources, spare parts and staff. In other words, how aviation companies and the Defence Department can get the most out of their fleets. An example of a tool that helps them do this is FlexPlan. This scheduling tool from NLR automatically creates smart maintenance plans, based on maintenance schedules and flight schedules. The aim is to optimise the planning of maintenance activities so that aircraft have to be kept on the ground as little as possible.
An inspection robot that uses infrared images – thermography – for analysing composite structures, rotors or turbines can be a good solution.
“At the moment, a mechanic sometimes spends an entire day tapping the rotors of a helicopter with a hammer to check them,” says Arjan. “Inspection robots can take over some of this work. That lets us avoid having the technicians do boring and repetitive work, and we can use them for more useful and more challenging activities. On top of that, we are improving the working conditions by automating the dull, dirty and dangerous work.”
One misunderstanding that Arjan would be glad to see the back of is that aircraft maintenance goes no further than checking the engine or the rotor blades. “If you put an aircraft on a platform without any people there, that plane isn’t going to repair itself. You need qualified staff for that, and spare parts too. You have to plan the maintenance. We look at the people as well as the machine. How do you manage your assets? How do you carry out your tasks?”
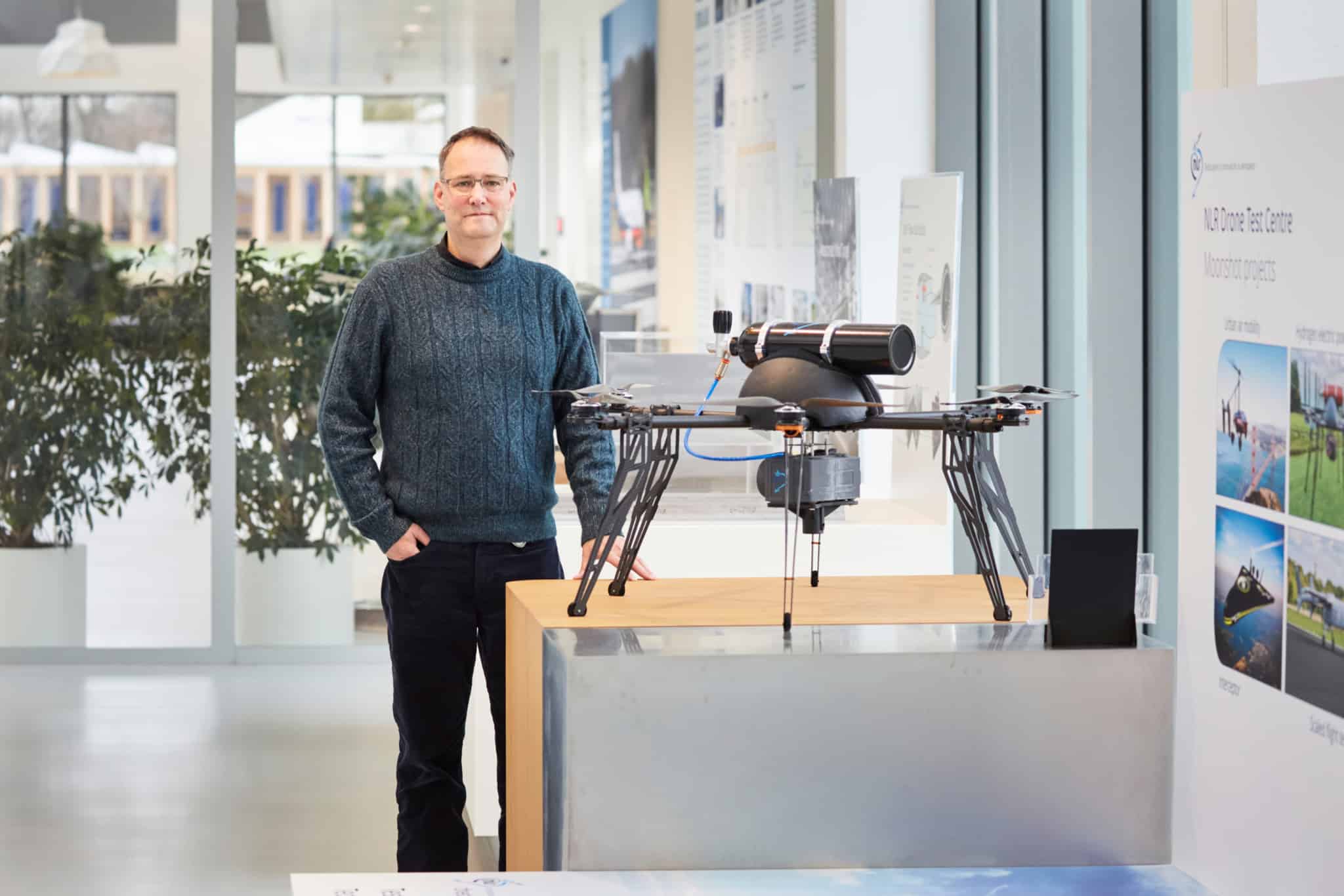
From the Air Scouts to NLR
It’s no coincidence that Arjan works in the aviation sector. From the moment that he joined the Van Weerden Poelman Air Scouting group at the age of twelve, it was clear that he would do something with planes later in life. He never hesitated for a moment in registering for the aviation engineering course at the college in Haarlem.
He ended up “doing something with planes”, that’s for certain! After college in Haarlem, Arjan ended up working for the helicopter operator Schreiner Airways (later CHC Helicopter Corporation). During the same period, he took a master’s in Aviation Management in Southampton. He then worked for CHC are several years in Canada, where he was responsible for setting up all the non-European maintenance organisations. At the same time, he completed his doctoral research into contractual relations in industrial maintenance. He started work for NLR in 2009.
“At the time I was finishing college, ‘innovation’ and ‘maintenance’ were diametric opposites. We used to define maintenance schedules by sticking knitting needles through a stack of punch cards. Innovation has now really taken hold in maintenance, though.”
Arjan de Jong
The transition to sustainable aviation
Whereas Arjan was working with just a single colleague in 2017 on innovative solutions for maintenance, a deliberate strategy has now been rolled out for mapping out the maintenance techniques of the future. There are now thirteen people in his department and students from higher education colleges and universities can often be found working on the projects too.
The transition to greener aviation is an important theme for MRO and large numbers of new technologies and systems are being looked at. Hydrogen is one of the key examples. “Aircraft with hydrogen propulsion systems also need maintenance. We’re looking at a strategy for how we can roll out maintenance activities in that market.”
It is what is called “design for maintenance” in the sector jargon: building a plane in a way that allows maintenance to be carried out as easily and efficiently as possible. “You can design a component so that it can’t possibly break,” explains Arjan, “but developing a system that you need to replace or inspect periodically can be a valid choice too because it’s then cheaper or more lightweight. So there are always several maintenance concepts, each with its own economic considerations.”
From knitting needles and punch cards to inspection robots
The key demand from the sector is a reduced maintenance burden so that aircraft have to be kept on the ground for less long and so that maintenance technicians – who are becoming increasingly difficult to find – can be deployed more efficiently. “That can mean that we integrate computers or sensors that raise the alarm if the condition of a component deteriorates,” says Arjan. “In the future, we’ll be moving towards integrated systems that monitor themselves, with built-in equipment. This also lets you replace components before they break as well as scheduling maintenance more efficiently.”
That was inconceivable when he began his career in the nineties. “At the time I was finishing college, ‘innovation’ and ‘maintenance’ were diametric opposites. We used to define maintenance schedules by sticking knitting needles through a stack of punch cards. Innovation has now really taken hold in maintenance, though. I think it’s wonderful to see this happening and I’m convinced that this is only the beginning.”
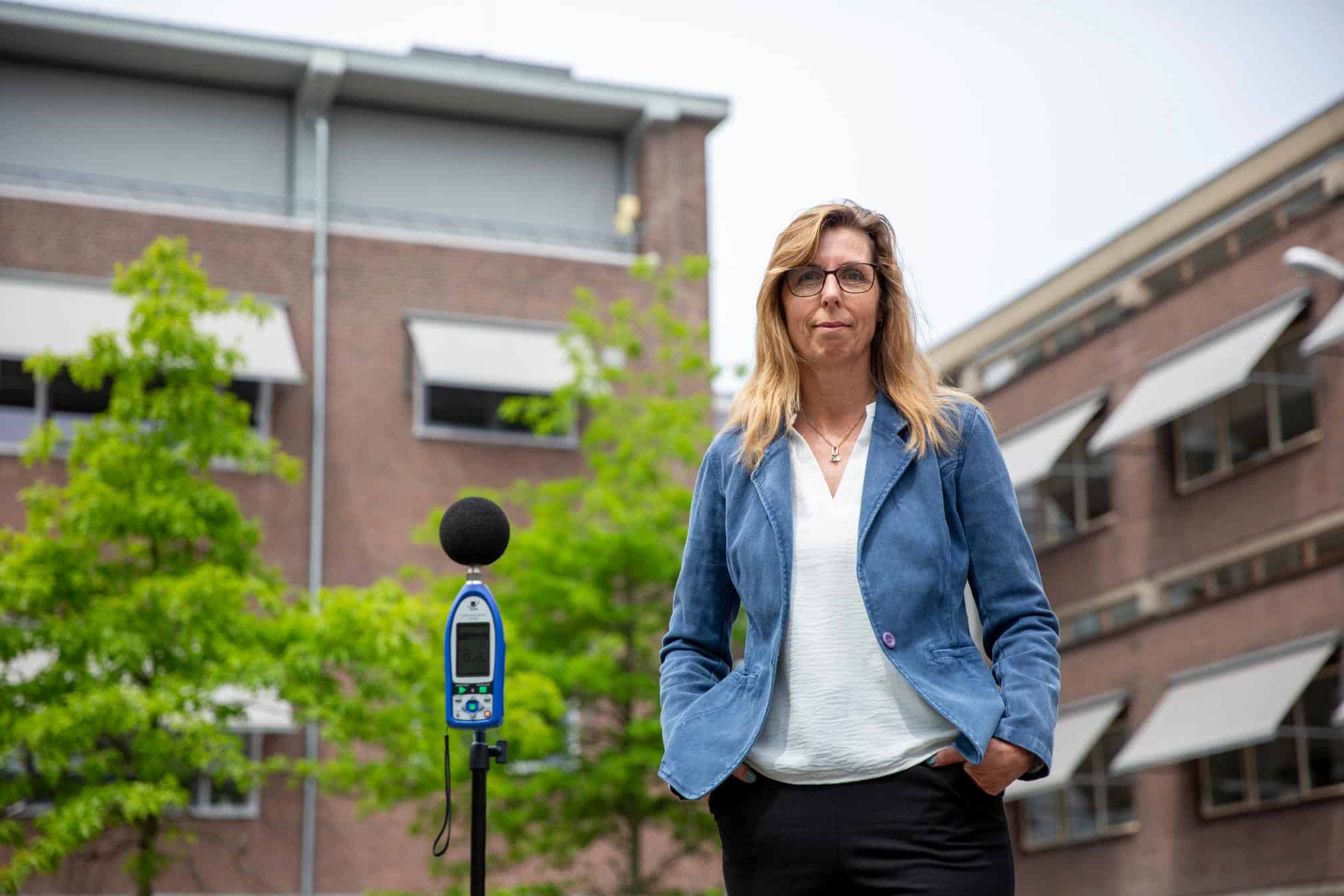