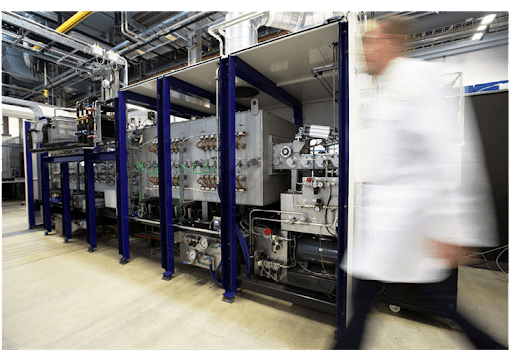
Green hydrogen produced by splitting water using renewable energy, such as solar and wind energy, plays an important role in the transition to a sustainable future. The demand for electrolyzers that enable the generation of hydrogen is increasing. The best suited technology to produce green hydrogen is proton exchange membrane water electrolysis (PEMWE), but it requires the scarce material iridium. “We have extreme control over the amount of it with our technology” said Dr. Mahmoud Ameen, program manager for Thin Films for Energy at TNO in Holst Centre.
Green hydrogen gas is produced by splitting water with renewable electricity. This gas is a key enabler of the transition into a sustainable society because it can serve both as a fuel and a raw material. PEMWE is the best suited technology to produce green hydrogen because it can handle the intermittence of renewable power. However, the technology makes use of iridium, which is one of the scarcest elements on earth. The global iridium production per year is not enough to sustain large scale hydrogen generation with the available PEMWE devices. In order to achieve climate goals, the usage of iridium in PEMWE therefore needs to be reduced significantly.
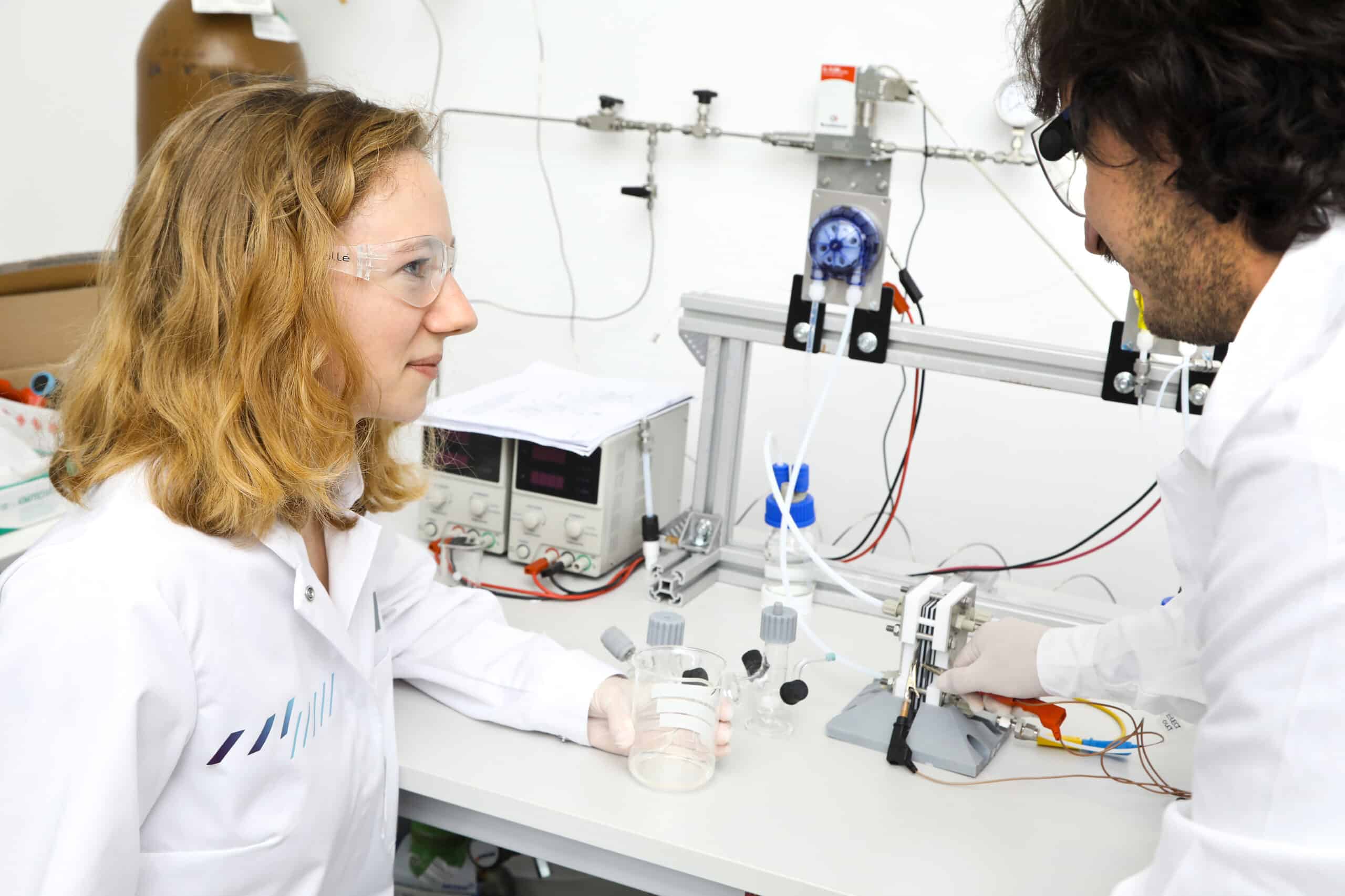
Major breakthrough
TNO researchers have now made a major breakthrough to overcome the iridium constraints for large scale green hydrogen production and are the first to develop a PEMWE that operates with 200 times less iridium. The device can currently achieve a performance of 25 to 46 percent of the current generation of electrolyzers. The key to reducing the usage of iridium was the fine-tuning manufacturing achieved by Spatial Atomic Layer Deposition (sALD) technology.
TNO at Holst Centre played a key role in the design and development of the sALD manufacturing process. TNO in Holst Centre and the researchers of the unit Energy Transition of TNO specialized in electrolysis have been working in recent years on the deployment of sALD in electrolyzers, where extremely thin layers of materials are deposited on large surfaces. “Thanks to sALD, we can deposit high quality iridium layers, as well as other metals, in a quick and cost-effective way. In doing so, we can control the layer thickness down to the scale of one millionth of a millimetre”, Ameen explains.
Stability guaranteed
Over the past two years, TNO at Holst Centre and partners have been conducting experiments with sALD in electrolyzers. The researchers applied an ultrathin layer of iridium as catalyst material to a porous titanium support, called porous transport layer. The operation and stability of the innovative methodology has now been proven successful after several tests in the lab. Little to no degradation occurred after the stress tests. In the new PEMWE, the inorganic components (iridium and platinum metal included) are separated from the organic ones (polymer electrolyte) and that makes it easier to define recycling strategies.
High volume manufacturing
“Now, with our broad experience in materials structuring, coating technologies, and the device process integration of a broad variety of thin/thick film manufacturing technologies, we will work on next-generation high-tech electrolyzers to make them affordable and suitable for high volume manufacturing”, Ameen continues.
The breakthrough allows countries in Europe to make plans around scaling up electrolyzers, and it brings more benefits. “From a geopolitical perspective, we are also better off with this technology. This is because we are confident that we have enough iridium in Europe to make the green transition happen, without being dependent on countries we don’t want to be dependent on.”
Many other applications
In addition to electrolyzers, sALD can be applied in even more ways. In combination with a breadth of other thin film deposition technologies, sALD as an innovative production technology has the potential to advance the high-tech industry. Initially, sALD was developed for integration in a new generation of displays for TVs, tablets and smartphones. The technology is also used worldwide in the automotive industry and by manufacturers of solar panels and batteries. And lastly, with regard to hydrogen, the technology can also be extended to fuel-cell manufacturing to produce electricity out of stored hydrogen.
Steps further
TNO at Holst Centre will take follow-up steps with this established proof-point in two directions. Firstly, they will help make the technology applicable for large-scale production in collaboration with sALD startup companies in the Dutch ecosystem, such as SparkNano. The company develops sALD devices for energy, OLED and related applications. Ameen: “There are still a number of details to address, which include finding more suitable and affordable precursors for the sALD process and designing recovery strategies to minimize raw materials spillage during manufacturing.”
Secondly, TNO at Holst Centre will engage in the further integration of the full breadth of thin film manufacturing technologies – including sputtering, electroplating, photolithography and its background on developing thin film electronics on foil – for the realisation of next-generation high-tech electrolysers. Auke Kronemeijer, research manager of the Thin Film Electronics department at TNO in Holst Centre concludes: “Ultimately, the full high-tech manufacturing industry value chain will need to play an important role in enabling large-scale production of electrolyzers with significantly increased performance to make the energy transition a reality. Together, we will make sure that the countries in Europe can apply green hydrogen on a large scale in the future.”
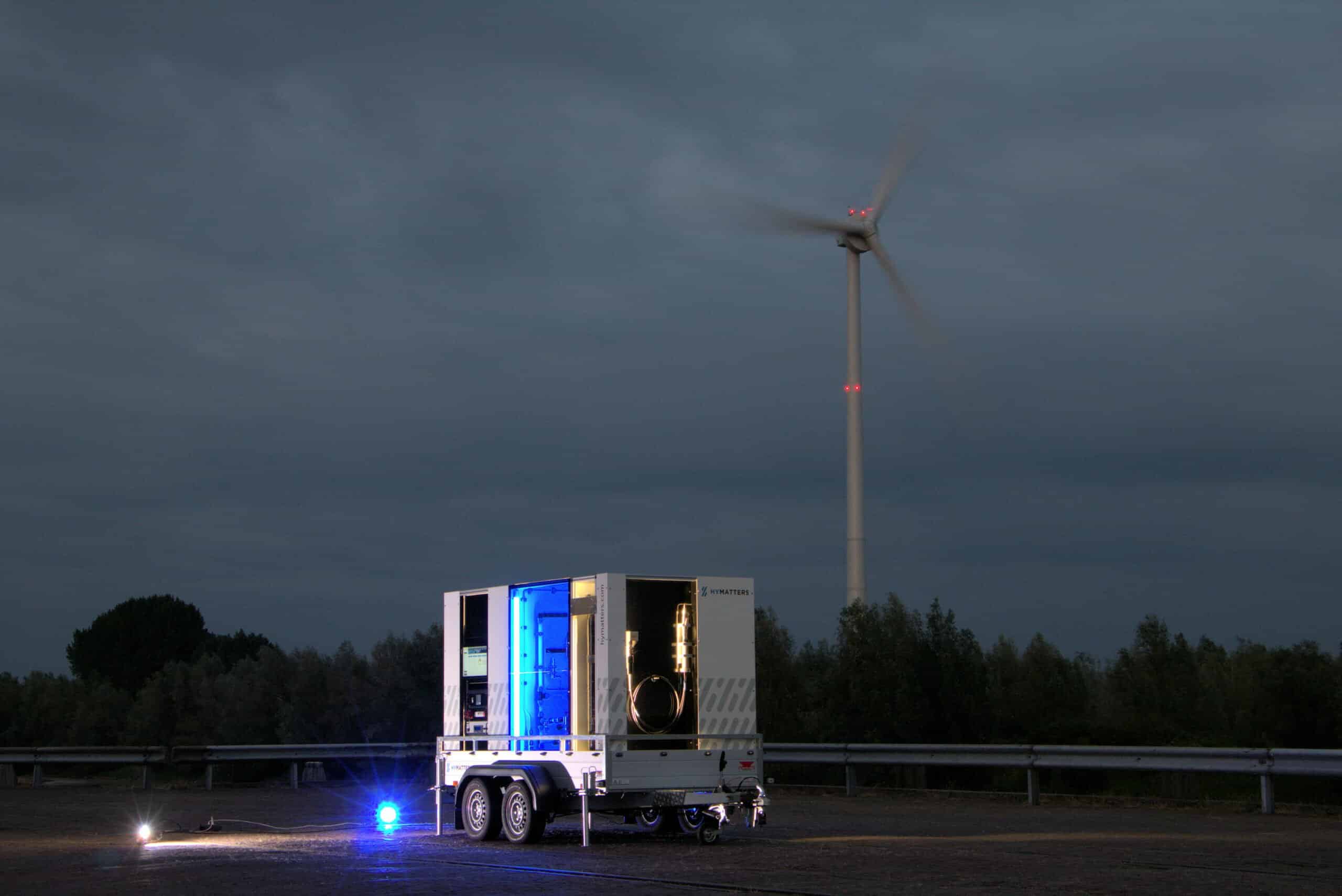