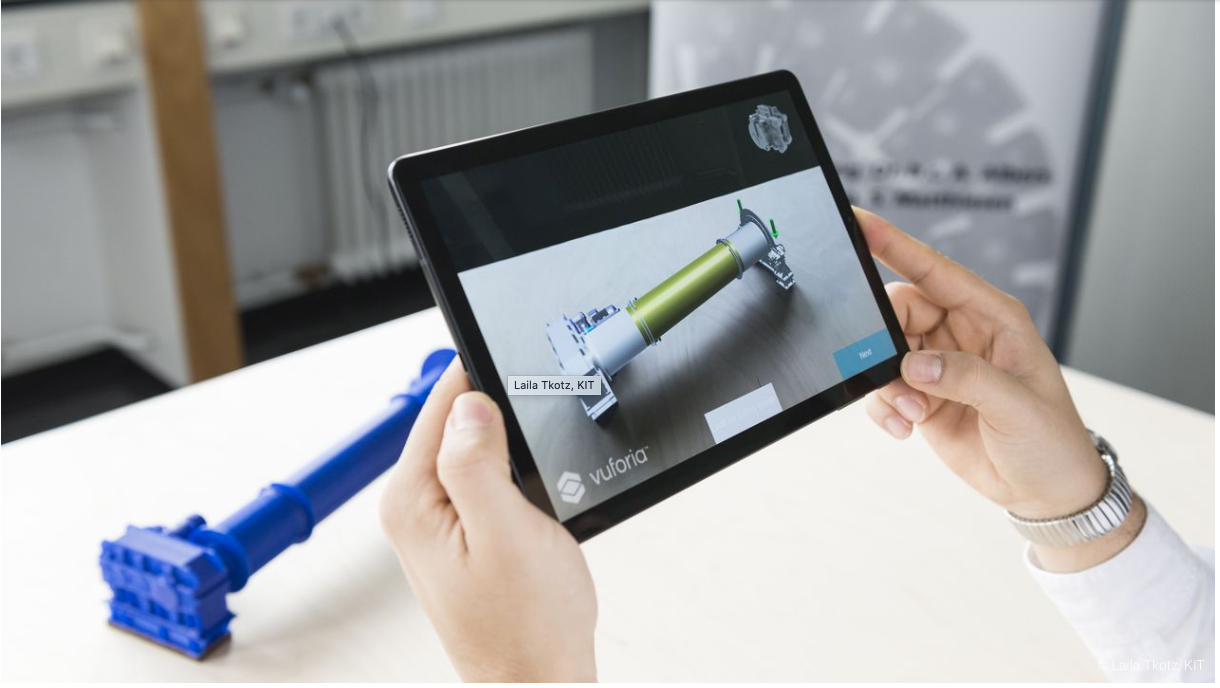
Industrial designers know better than anyone that things can look great on paper. But to check if a product really looks that good in actual practice, or if a machine part really works, you do need a prototype. Every year, manufacturers of cars, appliances or machine parts spend millions on building prototypes. According to scientists at the Karlsruhe Institute of Technology (KIT) in Germany, things can be done differently. With their Extended Reality (XR) techniques, a designer can check at an early stage whether a product is going to meet its specified requirements.
โIn the automotive industry, itโs not uncommon for 10 % of the entire development budget to go into the production of prototypes,โ says Marc Etri, head of the XR Lab at the KIT Institute of Product Development (IPEK). โThat can very easily add up to many millions of euros.โ
Cutting costs
Scientists at the IPEK want to cut down on these costs: with Extended Reality (XR). This works by using computer technologies such as Augmented Reality (AR) and Virtual Reality (VR). That way, you can augment the physical environment with virtual components, or even completely replace them.
โXR technologies make it easier for us to adapt products to the needs of customers and the requirements of the market in all stages of their development. This entails finding product profiles, creating concepts, specifying and realizing them,โ explains Etri. โPhysical-virtual prototypes can save development time and costs. It also allows you to avoid flaws that are often not discovered until the later stages of development.โ
As one example, he shows a realistic three-dimensional model of a road bike that can be customized on a tablet. โI can change the design of wheels, frame or saddle with one click,โ he says. Even such subtleties as the color and level of shine of the seat post or the structure of the upholstery can be changed with just a few clicks on the screen.
โMany engineers are not even aware of what is already possible with AR and VR in practice,โ states Professor Albert Albers, head of IPEK. โGame developers have long since shown us how to do that,โ Etri adds. Often todayโs customer-centric product development efforts still fail due to inconsistent data management and the resultant lack of consistency, Albers says. โWe canโt use 20th century methods to develop 21st century solutions.โ
He goes on to say that engineering can benefit greatly from new technologies and methods, even in the current corona age. โBecause this technique also makes it feasible to work contactlessly in a variety of locations,โ Albers continues. Which is why, in addition to research projects in fundamental research and with companies, the XR-Lab is also used in education.
Also interesting: โ
Ook interessant: โThis is going to be the new way of designing neighborhoodsโ