
“Almost all products we use daily are (partly) made of plastic,” says Eric van Beijsterveldt, account manager at plastics distributor Resinex. Plastic is everywhere, from phone cases to flower boxes and from coffee machines to tools. “The world cannot do without this material.” Demand for the material remains as high as ever, and the needs of companies and consumers are changing. Sustainability and circularity are becoming increasingly important and are the central theme at the Kunststoffenbeurs 2024. Extra attention will also be paid to the anniversary, with an exhibition on the most critical plastic and rubber developments over the past 25 years.
Recycling
Resinex is one of the exhibitors. The company handles the distribution of plastics and rubbers. “We are the link between producers and processors in all kinds of markets such as medical & healthcare and building & construction,” says Van Beijsterveldt. He says recycling is a “hot topic” in the market. “Right now, we are focusing mainly on post-consumer recycling developments. We recycle products that have already been with consumers, such as the plastic parts of a phone.”
It’s a new – and more complicated – line of business because they are not strictly separated streams, as is often the case with waste from industry. Plastic packaging, for example, also contains food scraps. “That makes it more difficult but not impossible.” At the anniversary exhibition, Resinex shows recycled materials to give visitors an idea of the possibilities.
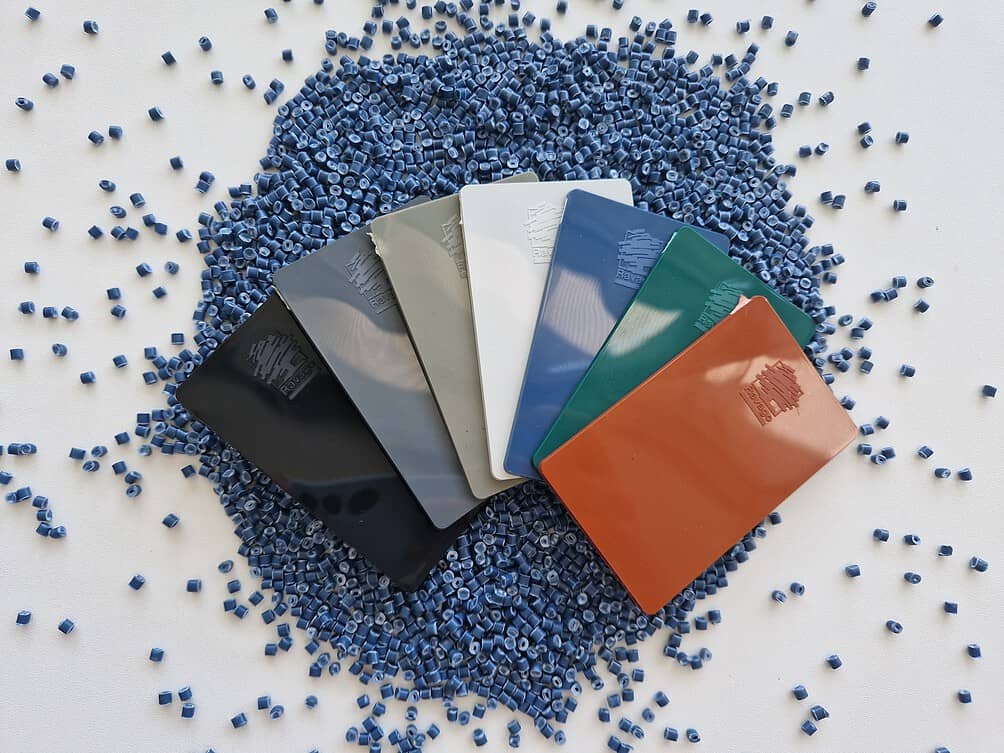
Environmental friendliness is increasingly important
VDL Parree and three other sister companies of VDL show essential developments of the past 25 years during the special exhibition, the Kunststoffenbeurs The company makes diverse products using plastic injection molding and shows the latest and most complex techniques during the fair. “Sustainability is starting to become a big theme now,” states Pieter Melisse, managing director of VDL Parree. This is – he points out – due to increasingly extensive European legislation in this area and changing public opinion. “People want a cheap product, but they also increasingly have demands about the environmental friendliness of products. Then you see that the industry is also changing.” However, it remains a tricky area of tension; reprocessed plastics are currently more expensive than new plastics. Their price is linked to the cost of oil and other chemicals. “We have to set a new balance, which takes time for companies and consumers.”
Meanwhile, VDL Parree continues to grow briskly. “We once started with metal stamping, but we have since transferred that branch to a sister company. As a result, there is now more room for making increasingly complex plastic parts,” Melisse outlines. For example, the company used to make mainly individual car parts, but now, complete door panels are coming out of VDL Parree’s factory. “These are much more complex processes, which require very different knowledge and equipment from us. For example, there are high-quality requirements for the products.”
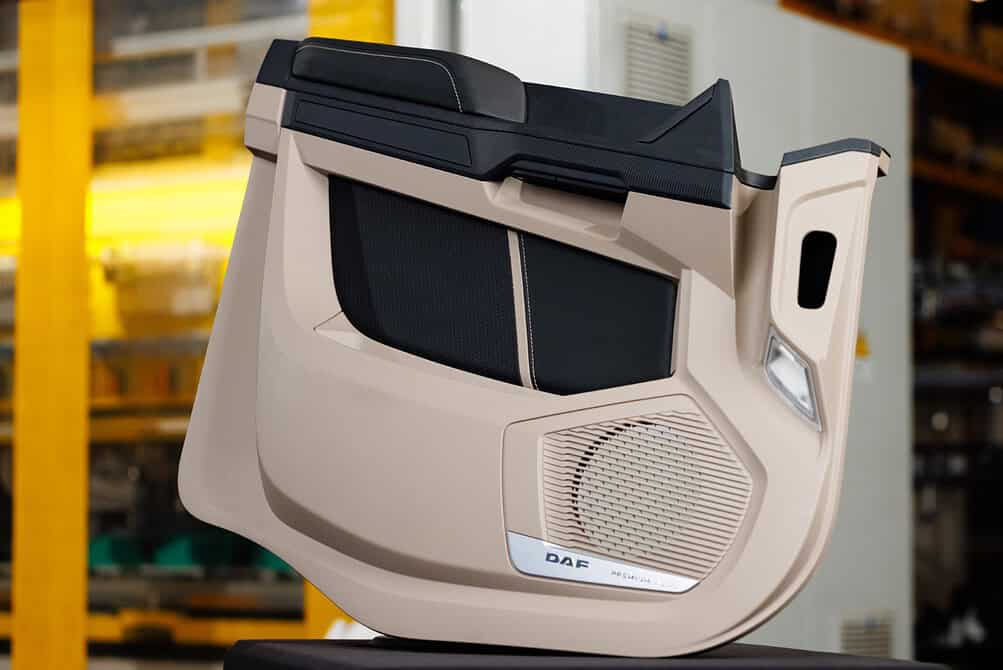
Smart systems on the rise
Tool Temp Benelux will also be at the Kunststoffenbeurs in September. The company supplies tempering and cooling equipment for industry, particularly for companies that make products from plastic. “Plastic is injected into a mold in liquid form, after which it hardens and forms into a product. During this process, the plastic must be cooled so our devices can take the products out,” says Gerd Teeuwen, managing director of Tool Temp Benelux.
More energy efficient
The company is developing intelligent temperature controllers. “We are moving from simple devices to smart, self-learning systems that can quickly and accurately control temperature. This ensures a better end product and considerable energy savings,” Teeuwen says. Tool Temp Belenux will showcase this significant development at the special exhibition 25 Years of Plastics and Rubber. “The outside of the devices has not changed much in recent years. But the controls are completely different with the advent of AI.”
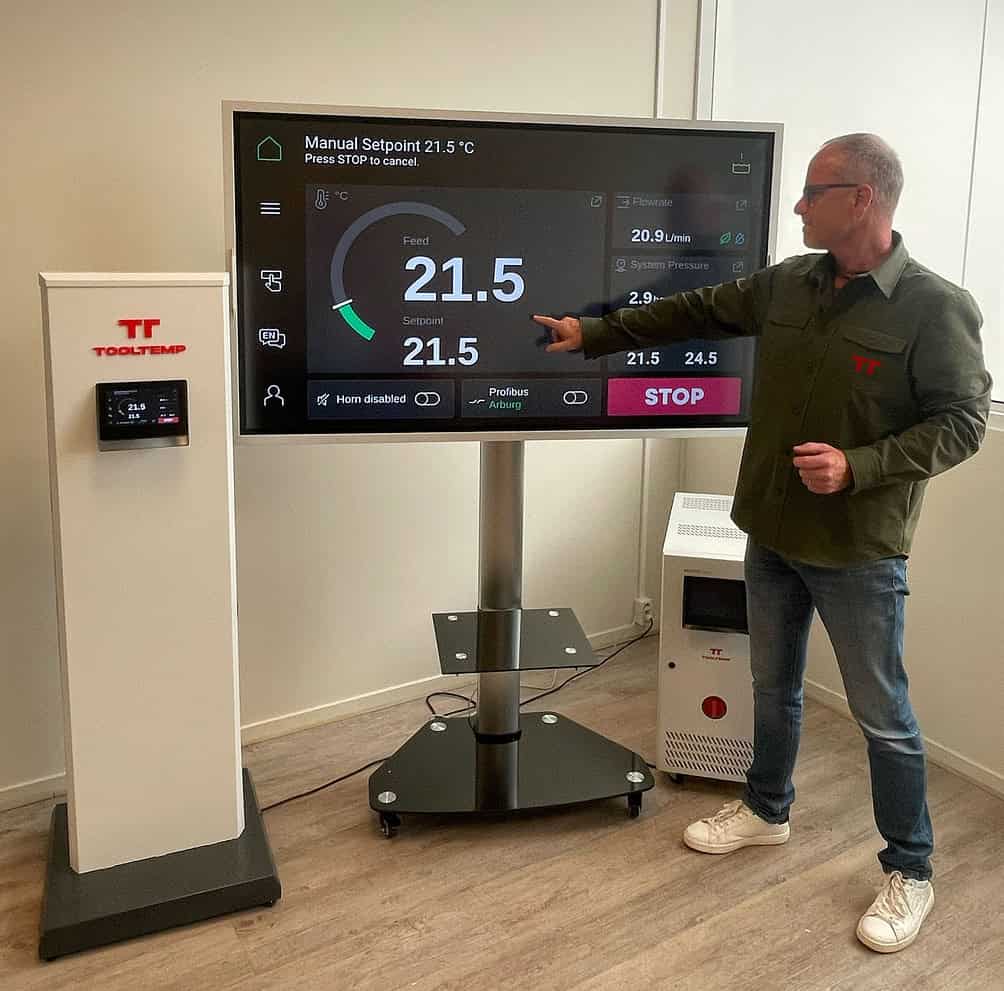
With the implementation of AI, the device gets to know itself. “As a result, the system learns about the process and how to set it up best. This also opens up different possibilities for preventive maintenance. If a piece of hardware is in danger of breaking down, the system signals the operator. This ultimately results in less downtime,” says Teeuwen. He emphasizes that developments are going super fast. “Companies that don’t jump on the AI train now are too late.”
Closing the circle
Van Beijsterveldt (Resinex) says this applies to technological development and sustainability: “The industry’s focus is increasingly on circularity. This is due to a growing number of international regulations in this area and companies’ motivation to contribute to the future. It is also important that consumers feel an urgency to contribute, for example, by recycling plastic properly. In this way, we can close the circle together.”
Would you like to attend the Kunststoffenbeurs on Sept. 18 and 19? You can register here.