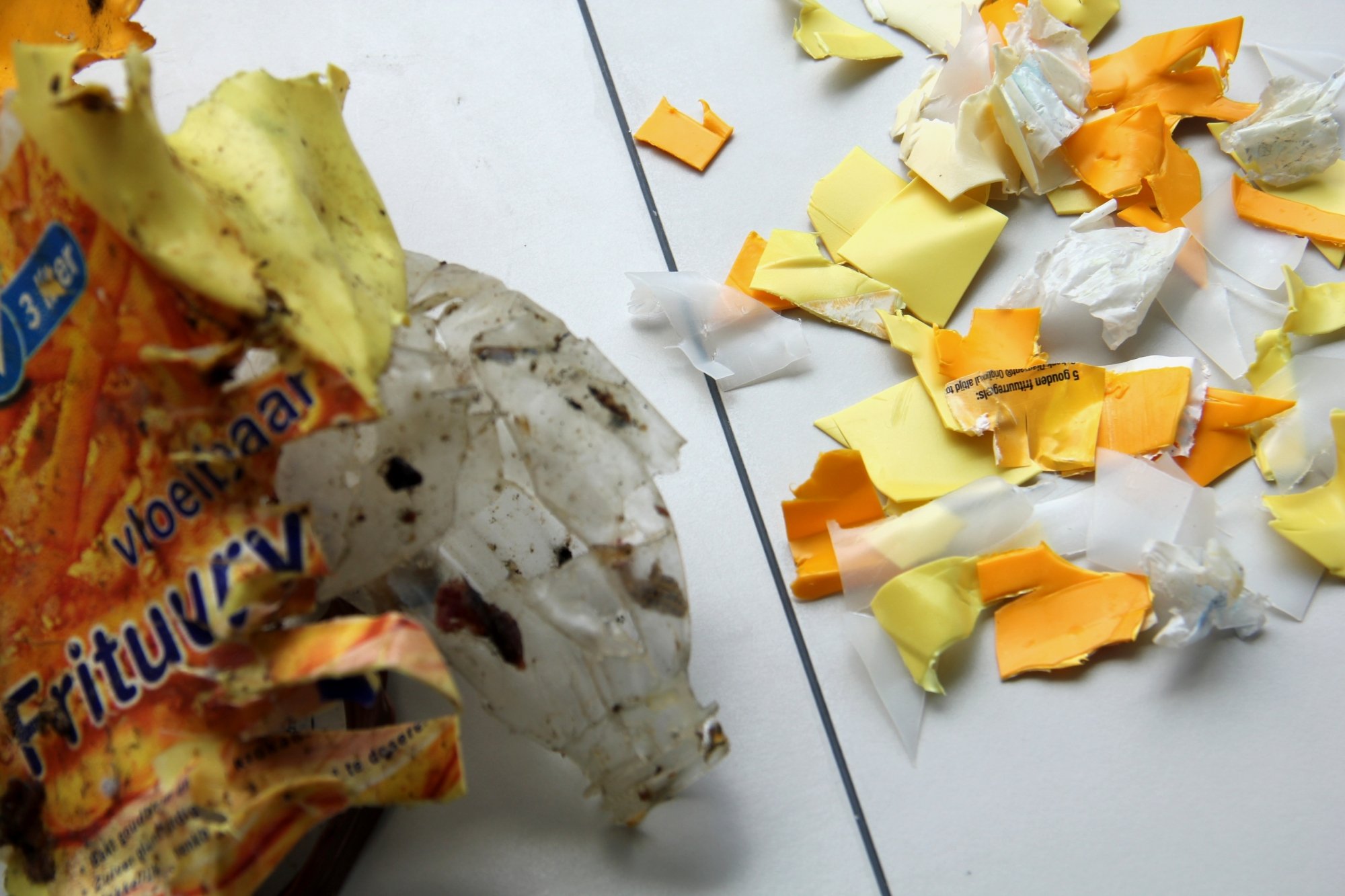
Around the giants of the Eindhoven tech scene – Philips, ASML, NXP – are hundreds of smaller fledgeling companies, honing their ideas, and hoping to be the next big household name in high tech innovation. But what does it take to turn an idea into a success story? Part two of our series about companies in the buildings of Twice: How TUSTI tries to improve the recycling of plastics.
Read all the stories about Twice here
TUSTI is a high-tech recycling company from the Brainport region, specializing in solving recycling issues and in treating difficult waste streams. One of the problematic waste streams of that kind is greasy plastic from the recycling stations dealing with used deep-fryer oil. Vast amounts of greasy jars and boxes made of high-quality, usually food grade plastic is simply being burned because the oily plastic cannot be recycled. Cleaning the stubborn oil residue from the plastic is currently not possible without steam or corrosive and unhealthy chemicals. TUSTI came up with the innovative technology for cleaning the plastic from grease which does not involve either high temperatures or harsh chemicals: plastic is shredded into small pieces and they are washed with the special cleaner, dried, packed into bags – and they are ready to be dispatched to a plastic recycling facility.
TUSTI was founded in 2015 as a collaboration of Stiphout Industries and Eindhoven University of Technology – an alliance of entrepreneurship and research. Today, the company’s inventions have two patents pending: one for the first generation of the cleaning liquids and another one for the second generation – in time the cleaner has become cheaper and lost volatility.
“At the moment we are busy with the recycling of non-greasy post-consumer plastic – almost 5000 tons per year,” tells us Jan Kolijn, TUSTI’s CTO. “TUSTI will start cleaning oily plastic beginning next year. However, our current recycling plant in Montfort is becoming too small for all our needs, so our plan is to build a new facility in a new location with the recycling capacity of 10 000 tons per year – both greasy and non-greasy plastic waste. Brainport Development and the Eindhoven University Innovation Lab helped us to get the funding for our research and guided us to Rabobank for a new loan, which we have recently received. This loan will help us to make the final steps towards building our new factory.”
In addition to the new facility plan, TUSTI is working on turning the cleaning of the greasy plastic into a closed loop process by re-using the cleaning agent. “One of our solvents can be separated from the oil, that is why we are working on the technology enabling us to do so – and we are close to having it!” says Kolijn. “We can separate the solvent and the oil using molecular sieving: the oil molecules are quite big whereas our solvent’s molecules are much smaller. That means that if you have a “sieve” with the holes small enough, you can strain the oil from the cleaning agent.” TUSTI will a start pilot project with the new sieving technology this October.
The laboratory where TUSTI work on their technologies is located in TWICE Catalyst building on the territory of TU/e Campus. “The Catalyst building is one of the few facilities in the Netherlands where it is possible to rent both the laboratory and the office space, and they are close together – that’s convenient, “ says Kolijn. “There are also other recycling companies in Catalyst, with which we are working to develop our technologies. We have recently finished a project with Ioniqa – the goal of the project was to find out if Ioniqa’s chemical recycling technology could help us with the waste streams that are not recyclable in our plant,” says Kolijn. “When you work in the building with the companies in the same industry, it is much easier to find partners for your projects – having coffee together helps!”