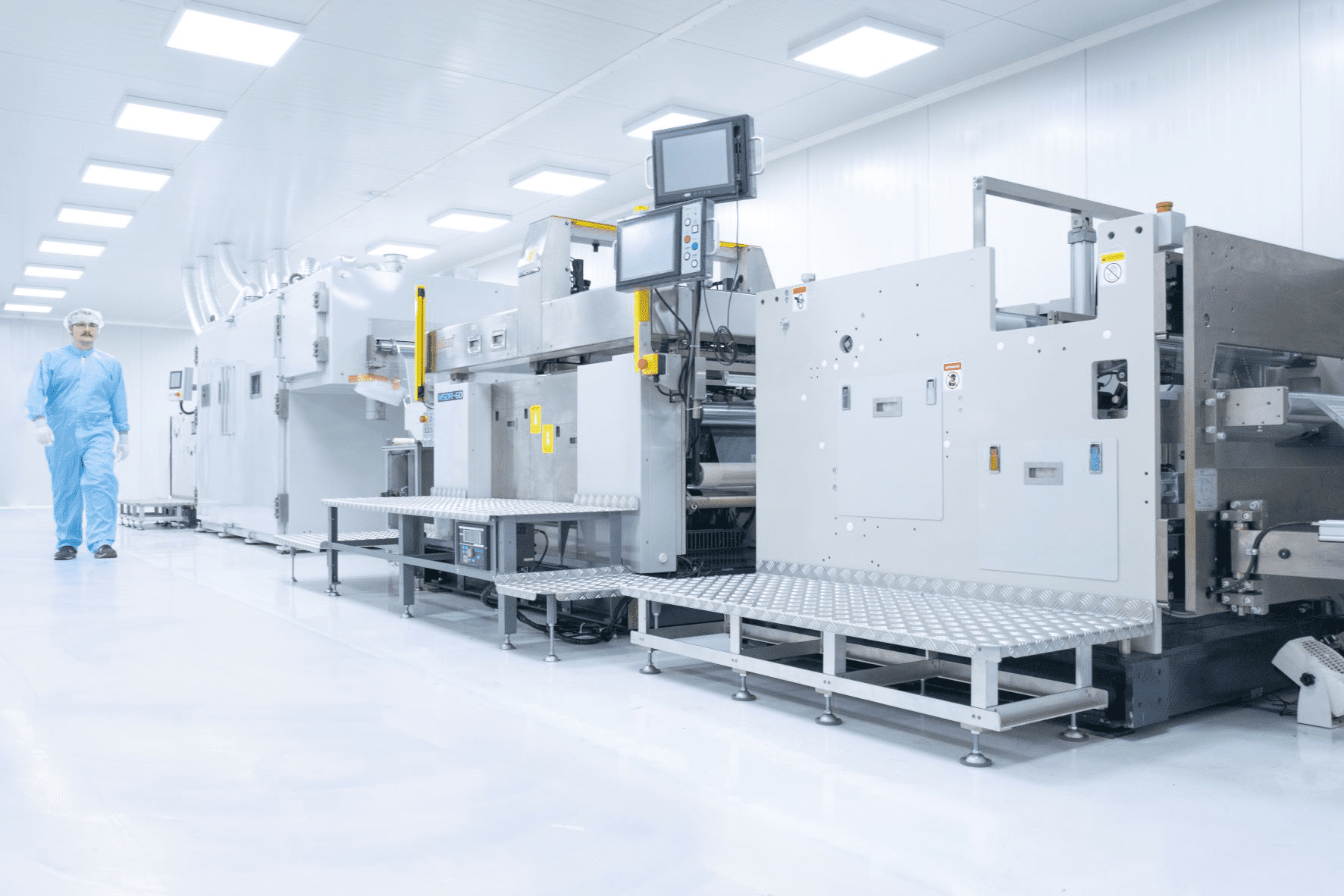
It’s all about medical patches with printed electronics that can be produced “roll-to-roll”. The technology comes from Holst Centre, where TNO researchers conceived it. Scaling up occurs at Tracxon, a stone’s throw from Holst. But for a solid foundation under the idea, mass production is essential. Because the higher the production, the better the product and the more promising the business. This requires customers, and the good thing is that there are plenty of them in Brabant.
Almost forty companies participated in the recently organized working visit by the Brabantse Ontwikkelings Maatschappij (BOM) to Tracxon on the Hastelweg in Eindhoven. All organizations are working on developing wearables, plasters, or textile applications equipped with sensors and electronics. The functions of those applications can be very different, but they always revolve around translating certain body information into valuable data. Heart rate, blood sugar, brain activity, perspiration; everything can be measured. Whereas previously, only complicated (and large) devices were up to measuring, Holst technology allows incorporating the sensors into clothing, plaster, or a bracelet so that the user no longer notices anything.
What is the Patch Factory?
The ‘Patch Factory‘ project is a collaboration between TracXon, Holst Centre, Salvia Bioelectronics, BOM and Elitac Wearables and is funded by Stimulus OPZuid, and co-funded by the European Union and Province of Brabant.The aim of this project is to contribute to accelerating the health transition by creating a complete patch factory. It should help large Brabant medical companies, SMEs and start-ups to realize their health products. Three concrete goals have been defined:
1. Creating an open patch factory for mass printed electronics in Brabant
2. Demonstrating the capabilities of the pilot line on pre-selected use cases;
3. To expand the ecosystem to more Dutch and European parties and generate a sustainable business model.
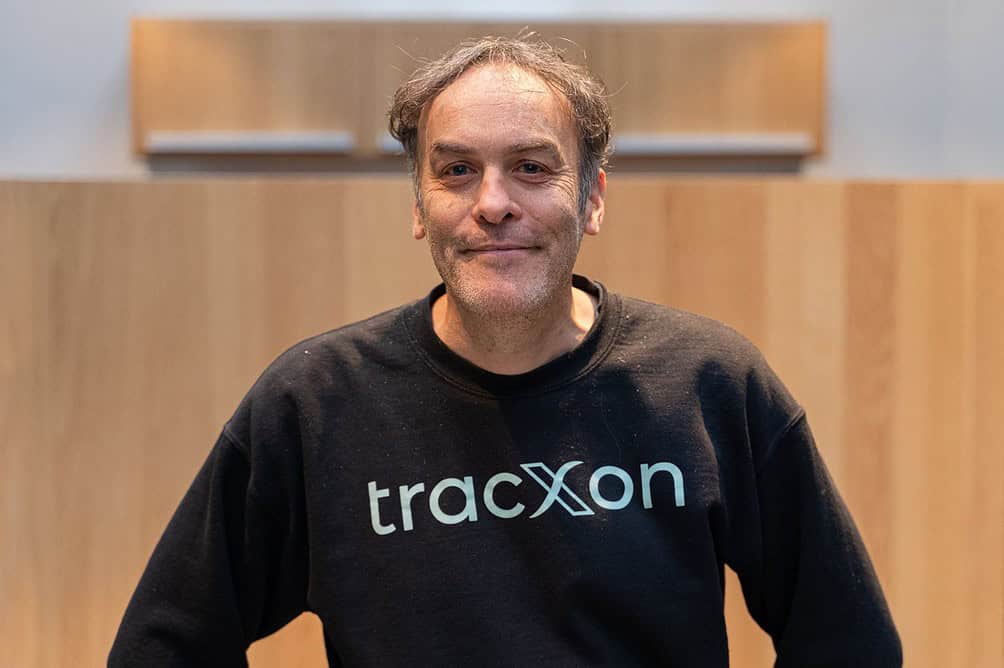
Given the aging population and shortage of healthcare personnel, solutions like this are increasingly important. It allows for accurate remote monitoring, which means patients have to come to the hospital much less often, and doctors can spend their time more efficiently. Where the electronics in wearables used to be the bottleneck, that threshold has now been overcome, says Corné Rentrop of Tracxon. “Those electronics must be able to move with you. It has to feel good and comfortable, and you have to be able to shower with it. Thanks to our printed electronics, this is now possible: the result is fragile, stretchable, washable, and still has all the functions you need for your application.”
Business opportunities
Those 36 companies visiting recently had signed up not only to be updated on the latest technology but certainly also because of the business opportunities. That means they also have a common interest. After all, the more companies that can do business with Tracxon, the faster that full-fledged Patch Factory can get off the ground, and the more there will be a functioning local ecosystem.
“It’s a little chicken and egg,” Rentrop says. “We need to make meters to increase the performance of our process, but making meters requires a lot of customers. Those customers would understandably prefer proof first that we can handle that scale-up. But so for that, we have to make those meters.”
Ria Hein, manager of ecosystem development at BOM, came into the picture to break that impasse. “We can push here and there so that potential cooperation partners can become part of the value chain. As a result, innovations are accelerated, and products find their way to the market faster.”
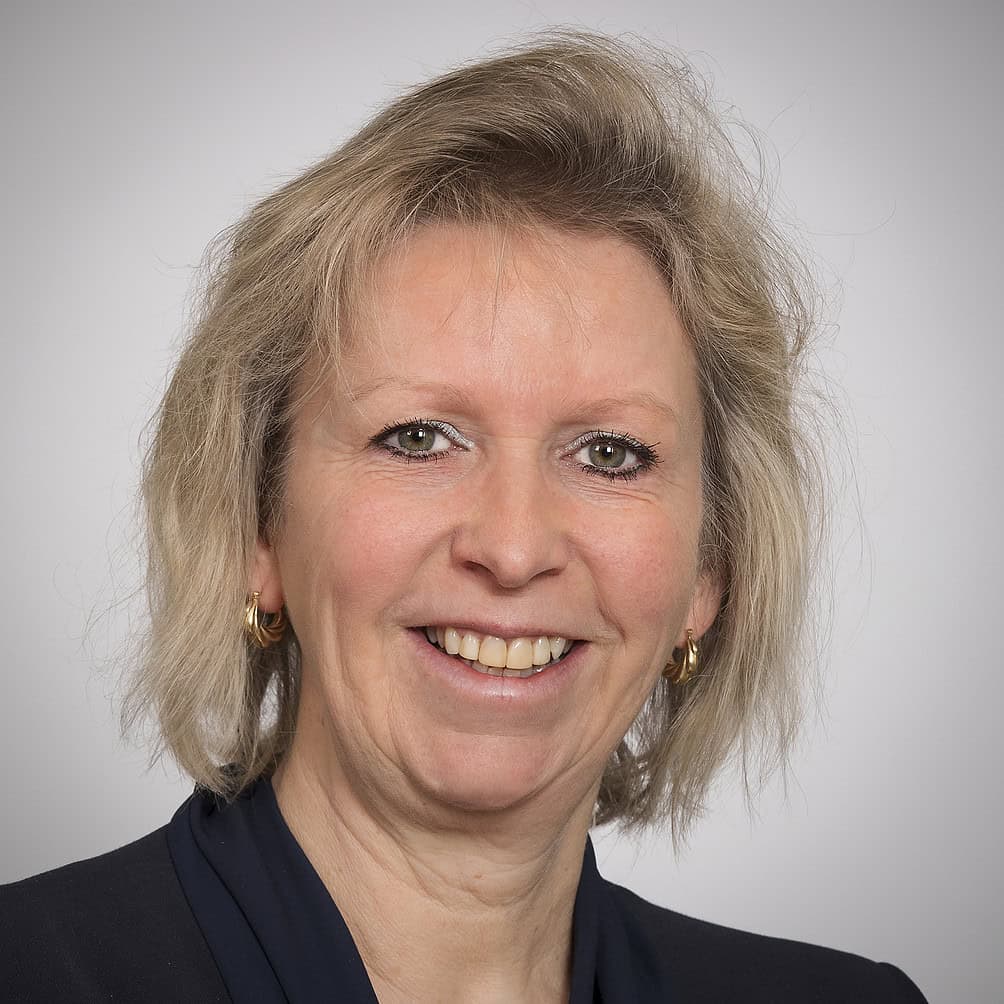
The target group for this is innovative SMEs throughout Brabant. “We want to help these SMEs accelerate toward high-value complex applications. For example, medical patches could be turned to Tracxon. With most potential customers, however, there is still some work to be done before they can use this facility. We need to intensify the network to make the innovative capabilities of the Patch Factory more visible and thus inspire parties to achieve new product development. After that, the move to the Patch Factory is a logical next step.” All stakeholders recognize the importance of this development, both from social goals and for business economic reasons. This is partly why the joint goals are promising, she adds.
Endurance testing
Coen Lauwerijssen, Director of Product Creation & New Business at 2M Engineering in Valkenswaard, confirms this. 2M has been working with Holst for some time but is hard at work looking for a party that, preferably close by, is capable of mass production. “That mass production is essential for two reasons,” says Lauwerijssen. “Only when you run several endurance tests do problems become visible that you can’t see in a lab environment. So, the more that is produced, the faster the quality increases. In addition, higher production results in lower costs.”
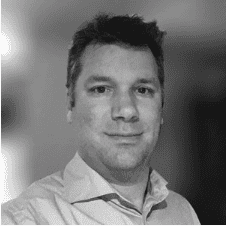
To become truly prosperous, Tracxon needs more than orders from start-ups, Lauwerijssen knows. “For that, corporates also need to step in. If that happens, you also immediately have a boost in confidence in Tracxon’s solutions, which will attract new parties.” Although those large companies have yet to come forward, 2M Engineering is already gearing up for that situation. Lauwerijssen: “We will soon create a separate website on which we will already show the medical patches that we can offer the market through an order at Tracxon. And we are also in talks with cardiologists about their specific wishes. We’re already getting started on that.”
Well-functioning ecosystem
For Ria Hein, it’s an example that makes her happy. “These steps are needed to create that well-functioning ecosystem eventually. This is local for local. Many parties in the region see the importance of this, as was evident during their visit to Tracxon. But now they have to put their money where their mouth is: the more companies take the steps that 2M is already taking, the faster we can continue to grow. As Brabant, we want to be number 1 in Europe in Medtech innovations, and with the patch factory, we are on the right track.”
Lauwerijssen is also hopeful because Tracxon has now succeeded in obtaining the medical ISO certification required for the production of medical devices. “It’s great that Tracxon has already come this far. I would therefore urge all companies working on this technology to apply with concrete projects.”