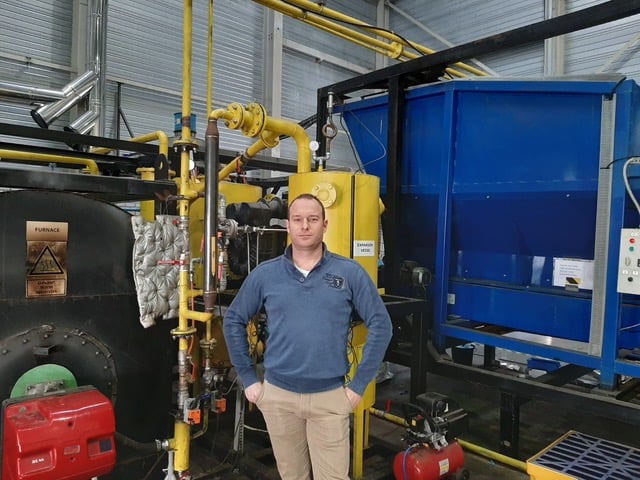
The greening of the process industry is not only a vital but also a complex task. The electrification of the manufacturing processes and the transition to renewable and recyclable raw materials are making other demands on the forms of cooperation, financing structures and policy measures. What opportunities does this transition offer? What obstacles lie ahead? And what contribution can the Groene chemie, nieuwe economie’ (Green Chemistry, New Economy) action agenda make towards overcoming them?
In response to the online summit ‘Green Chemistry, New Economy’ held on February 24, Roger Blokland, founder and managing director of Relement BV, Vincent Toepoel, director/founder of the start-up Waste4Me and Hans Linden, program manager at Electrification give their views.
What does your innovation entail, and how will it change the chemical sector?
Blokland: “Relement, a spin-off from TNO (Netherlands Organisation for Applied Scientific Research, ed.), stems from the Biorizon shared research center, and stands for ‘Renewable Element.’ Aromatics are the building blocks for the chemical industry. Forty percent of chemical materials are made up of aromatics. But they are also a bottleneck for the chemical industry. Because aromatics are not as yet genuinely ‘bio-based‘.
We are changing things and making bio-aromatics from biomass residues. Take, for example, sugar beet pulp and corn cobs that are left over when you remove the kernels. This hemicellulose forms the basis of our bio-aromatics. These are valuable compounds that give materials their firmness, such as paints, insulation materials and special lubricants like those used in industrial ovens.”
Toepoel: “We have backgrounds as a project developer and technology provider in chemical recycling. In addition, we also test the legal, ecological and commercial issues that surround chemical recycling. What else can you do with oil at the end of its service life?”
It’s a matter of defining: Which polluting components are absolutely unacceptable, and which are reusable.” Vincent Toepoel, director-founder of the start-up Waste4Me.
“What parts of that can go back to the refinery? We make life cycle analyses, but also deal with market trends and regulatory issues. We are currently working with about six oil internationals on which oils from waste can be used to fuel industrial crackers. It’s a matter of defining: Which polluting components are absolutely unacceptable, and which are reusable. Take agricultural plastic, for example. Admittedly, it’s usually extremely contaminated and full of sand, soil, plant remains, twine, you name it. But that’s not such a problem. The same goes for coffee packaging, cups and plastic mugs. We can process those just fine, after which they can be sent back to a factory.”
Linden: “Within the electrification program line, set up by Brightsite stemming from a partnership between Sitech Services BV, TNO, the University of Maastricht and Brightlands Chemelot Campus, we are researching the potential for using plasma technology in the chemical industry. This technology is based on producing a plasma using electrical energy which, instead of the current methods based on natural gas combustion, can be used for carrying out certain chemical processes. Such as the production of hydrogen, acetylene and ethylene from methane, without generating any CO2.
Plasma technology in itself is an old technology that was already being used in the German chemical industry back in the 1940s. However, it was never applied on a larger scale after that time as other processes were cheaper to use. That perspective has now changed, because you can save a lot of CO2 emissions with plasma technology. Which, moreover, will be an increasing cost factor for the processes currently in use.”
What phase is your company in?
Blokland: “We do a lot of testing with customers. For the next phase of upscaling in the paint market, we have formed a project consortium with raw material suppliers, paint manufacturers and users in the south of the Netherlands. In the past, we have already run a number of Proof of Concept projects in conjunction with Biorizon.
Our first launch customers come from the paint market, and after that it will be the lubricants’ turn. Initial results are encouraging. Our customers are also very positive. They think our bio-aromatics are even better than fossil products! Why do they think that? For one thing, the paint is harder, but also more UV-stable. Whereas the lubricants last longer.”
Toepoel: “We have now set up a demonstration plant in Moerdijk in collaboration with the Moerdijk Port Authority. The purpose of this is not only for our own use – given the magnitude of the challenge of chemical recycling. Besides, we like to work together with others. We therefore also make our facilities, our laboratories and our separation technology for materials available to other companies that want to make use of them. For example, to convert gas into products.”
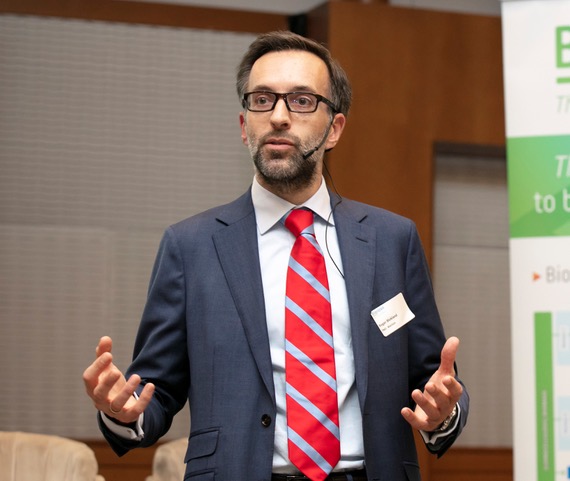
Linden: “In order to further develop plasma technology, steps need to be taken on three levels. On the first level, we focus on the technical-economic feasibility of plasma technology. This should lead to the set-up of a demo plant in 2025.
This is part of a broader program aimed at replacing methane with the electrification of processes. We will study and optimize the process based on plasma technology for hydrogen production from methane. This is used as a raw material for ammonia and the fertilizer production that is associated with it. The carbon present in the methane can be converted by the plasma process into acetylene, ethylene and related hydrocarbons that can be used for the production of plastics. In this respect, we will work in parallel on three generations of plasma technology at different TRL – as in Technology Readiness Level – stages.”
How is the scaling up of your product going? And how does it fare against the fossil market?
Blokland: “We are still working on a limited scale at the moment. But the potential for bio-aromatics is enormous. It involves hundreds of billions of euros. Internationally, as well. We are starting with a ‘specific obtainable market’ that is already good for €2.5 billions! Unfortunately, ‘more expensive’ and ‘more sustainable’ don’t necessarily go together. That’s why we have to get to a scale that will cause the price to drop. Only when sustainable products are priced right and offer a better performance, will companies join in. Which is exactly what Relement is aiming for.”
Toepoel: “We are currently working on a chemical recycling project. Innovation is not something you can do on your own! You have to share each other’s knowledge and facilities. Waste is also such a diverse stream of materials. You will not succeed without establishing a chain! Attempts have been made to do so in recent years, but going solo is a guarantee for failure. Collaboration is really essential if you want to achieve success.”
Collaboration is really essential if you want to achieve success.” Vincent Toepoel, director/founder of the start-up Waste4Me.
“We make a life cycle analysis per flow. And what we see is that oil companies are now also prepared to work with that. Plus, they are asking themselves the question: Which oil from waste products is acceptable for reuse and which isn’t?”
Linden: “We are focusing on 2025 first. By then, we want to have completed a demo plant for the production of 12 kilotons of hydrogen. By 2030 we want to scale this up to 2 megatons. The aim is to demonstrate the results on a small scale first. But also to plot out a timeline for large-scale production. To do this, we are working together with the large chemical companies at Chemelot. The industry also finds the application of plasma technology very interesting as part of their roadmap to meet the 2030 and 2050 climate targets.”
What are you running up against when it comes to forming a chain, funding and policy?
Blokland: “What perhaps bothers us most is the lack of legislation. In contrast to other sectors, the chemical industry does not yet have a legal framework for promoting sustainability. Although this is expected to change now.
Funding, and in particular seed money for the first phase, is also a really tough one. Why? We operate in an industry sector, Deep Tech, that needs a long start-up period. That is not very attractive for capital funds. They prefer to see a return on investment within a few years. There is definitely some interest, but the structure of funding bodies does not always give this room.
“On top of that, the costs are an obstacle. As long as fossil products are cheaper, the chemical industry will not always buy sustainable products. The oil industry has also been so optimized over the years in such a way that start-up companies with sustainable technology can hardly compete against it.”
As long as fossil products are cheaper, the chemical industry will not always buy sustainable products.” Roger Blokland, founder and managing director of Relement BV
Toepoel: “Funding for those young companies that are in the process of scaling up is always difficult. And banks only want to give short-term loans. We don’t talk to them anymore either. We only ever enter into talks with venture capitalists. We’re also talking about substantial amounts of €1 million now and more than €20 million in the next phases. Oil companies want to join in and are looking at things on a grander scale. That starts at hundreds of millions of euros. What you are also missing at this point are investors who really understand the business case and want to inject money into it.
As far as regulations are concerned, the Dutch National Waste Plan 3 that regulates the waste market is extremely well put together. It was actually worked on for more than 30 years. Moreover, it is increasingly being pushed in the direction of waste recycling. What often goes wrong, however, is that the various governmental departments often work at cross purposes. They often don’t know what the other department is busy doing. That is slowing down the process. Even though the push from waste treatment to recycling is well and truly on its way.
What we need is greater coordination. One such example is the ‘end-of-waste status.’ This is the legal status that the government has to apply in order to classify something as actual waste. An enormously murky process, given that there are no guidelines as yet. We do understand that old regulations serve as a basis for new ones. But take those grey plastic garbage bags as an example. They still stink because they still contain biomass. You are not really getting a perfect product. Gaining approval that something is not waste is a real nightmare!”
Linden: “We are working, as I said, with the industry. We have to. You have got to join forces in order to achieve those goals, otherwise there is no point.”.
You have got to join forces in order to achieve those goals, otherwise there is no point.” Hans Linden, electrification program manager at Brightsite.
“However, finding funding for each of those three levels at the same time is still quite difficult. In addition to the contribution from industry in kind, we need funding from government funding bodies, such as the NWO* and the RVO*. This means you have to apply for funding rounds in the form of tenders. Then you have to wait and see whether they are granted.” (*Dutch Research Council and the Netherlands Enterprise Agency respectively).
Then the next challenge will be to leave the ‘Valley of Death’ and get the plants funded. We need European and national funding for that.”
What solutions do you have in store? And to what extent will the Green Chemistry, New Economy Action Agenda be of help?
Blokland: “Legislation that makes becoming sustainable mandatory where sustainability standards are concerned would significantly accelerate the transition. Apart from that, there is the question of financing, i.e., seed money for the first phase. Parties such as Invest-NL are working to increase the availability of seed capital in Deep Tech. Seed money is absolutely crucial for sustainable start-ups in green chemistry.
As to the formation of chains, we are in talks with several companies. For example, bio-refineries as a supplier of raw materials, and paint manufacturers as a buyer. Entrepreneurs in sustainable chemistry can help and stimulate each other a great deal and a network is thereby important.
A very good analysis has been carried out for the Action Agenda, so it will definitely help! I am also very happy that it gives an insight in how huge the scope of green chemistry is.”
Whether you are talking about your cell phone, your keyboard or desktop: there are aromatics in everything. But nobody knows that!”
“What we see is that everyone has good intentions. We all want to move towards a new and more sustainable industry. We can do our bit by building a company that not only converts waste products, but is also capable of supplying better products.”
Toepoel: “We can already do most things. What we really need are cross-sectoral roadmaps. I am pleased that attention is now being paid to this within the Action Agenda. There are currently small waste streams that are suitable for recycling. Only separate recycling takes place outside of Northern and Western Europe. That is really stupid.
For example, if ash is contaminated with metal residues, these must first be extracted. The metal company then needs to cooperate with a chemical recycling company. But also with the packaging industry, among others. You have to think carefully about that too, so that even their products can be recycled more effectively as well. Mechanical recycling is very expensive for all streams. We look at how chemical recycling can be as efficient as much as possible in addition to mechanical recycling.”
Linden: “I think the Action Agenda is going to help complete the picture. As well as make clear what innovations are taking place that will help make the transition to green chemistry happen. But it will also help to map out the funding that will be needed at both a national and European level to get this going. That way you can help companies, large and small, to advance the necessary technology to the next level.”