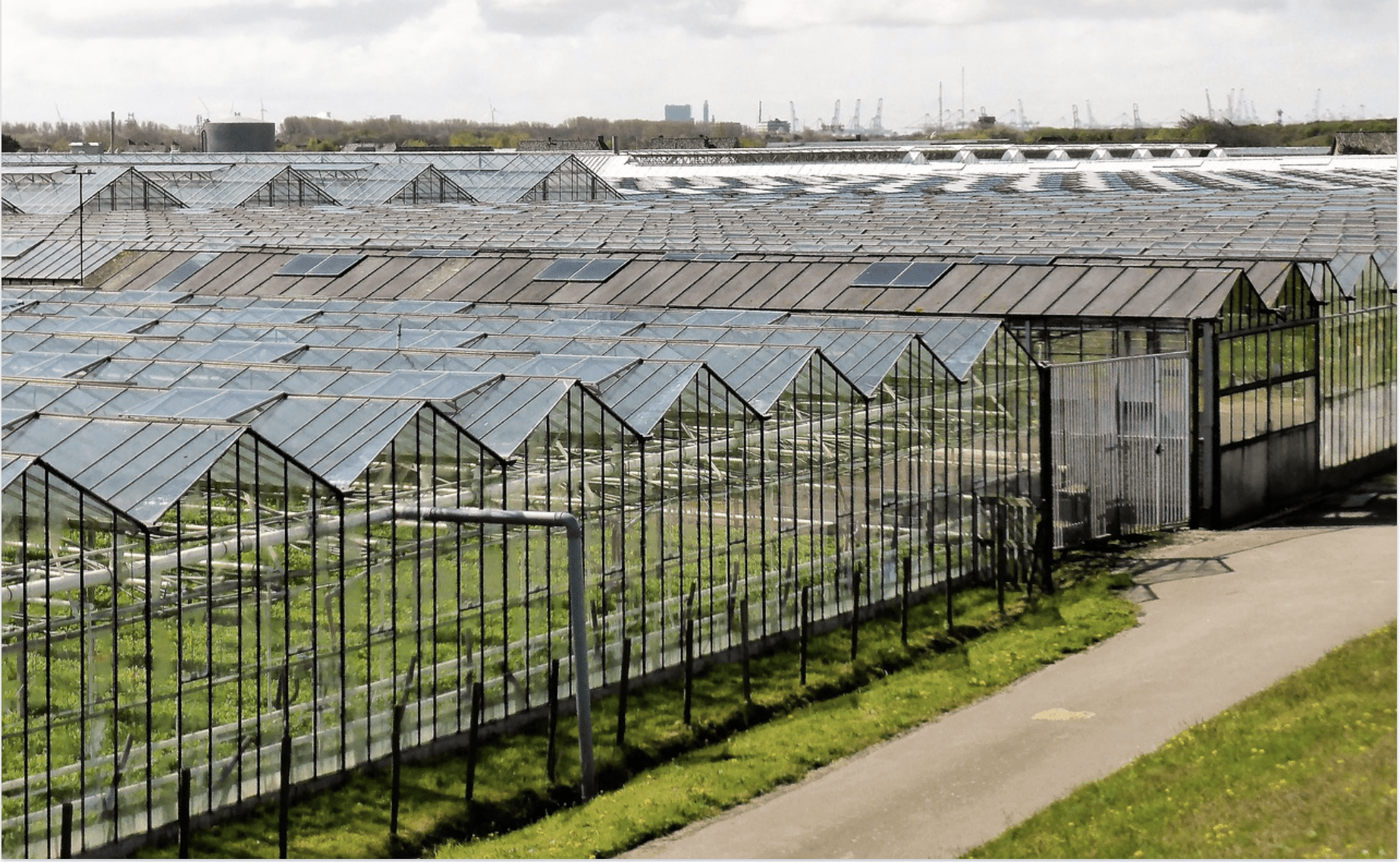
“Growing flowers and tomatoes on gas is coming to an end” was the headline of an article published by the Dutch national newspaper Financieele Dagblad (FD) on March 23. Even more poignant was the headline, “High gas prices force four out of ten greenhouse growers to permanently or temporarily shut down.” What is the deal with energy consumption in greenhouse horticulture and when will we be able to grow in a climate-neutral way?
In addition to labor costs, energy is a major cost item affecting the price of our greenhouse produce. For plants in greenhouses to grow optimally, a sophisticated mix of heat, light and CO2 is needed.
For a large part of the time, this can be done in a natural way in our Dutch climate. Good soil, water, CO2 and enough sunlight that provides the right temperature and light for growth.
Flat glas
However, at certain times of the year or even during the day, there is too much or not enough light and temperatures are too low. From the seventeenth century onwards, work was already being done to regulate the temperature. Growers worked with ‘flat glass’, windows that were placed on low stone walls to let the heat in during the day. The windows were then ;open’ and then closed during the night and on colder days to keep the heat in.
The first systems to store heat for a slightly longer period of time and also able to be used in a greenhouse were the wall-type glasshouses. A thick wall of bricks was built which the windows were placed up against at an angle. The wall absorbed the heat in the greenhouse during the day and slowly released it during the night.
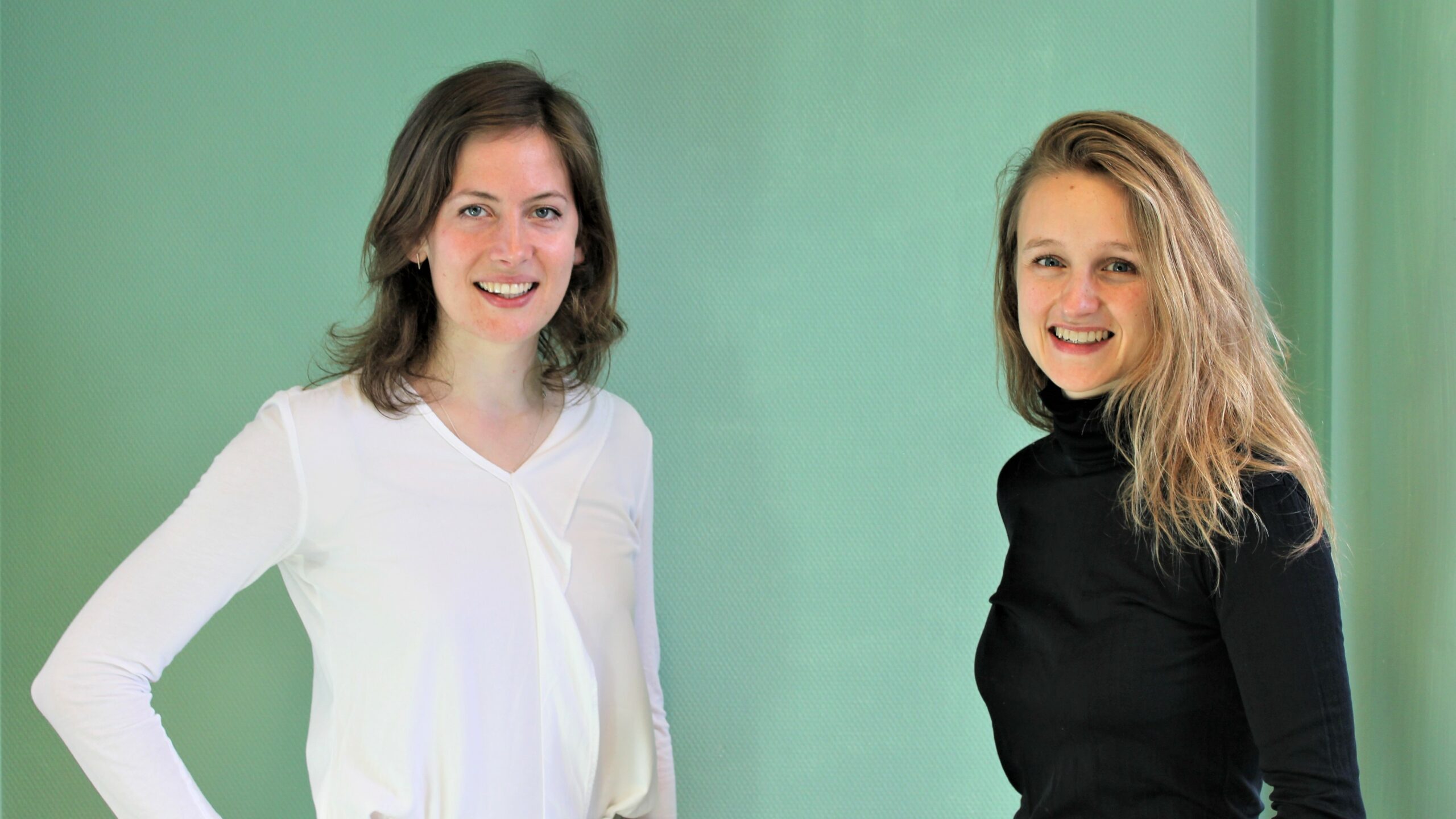
LED
A few hundred years down the road. The Netherlands is still at the forefront of horticulture in greenhouses. Our horticulturists now use high-tech greenhouses for the year-round cultivation of vegetables, flowers and potted plants. In order to do this as efficiently as possible we no longer use just the light and heat of the sun, but we use other sources as a supplement whenever it is too cold, too hot, too dark or too light.
We use lights in those times when there is not enough light. This lighting has since become LED lighting more and more in recent years instead of the old lights that mainly gave off a lot of heat. We have fabric screens to keep out excess heat during the day and the same screens help us keep the heat in at night. We use cooling systems and can bring extra CO2 into greenhouses.
We do this through the use of a (gas-fired) boiler or combined heat and power (CHP) system. The boiler produces heat and we extract CO2 from the flue gases for use in the greenhouse. We not only produce heat and CO2 with a CHP but also electricity for lighting.
Feed-in tariff
Another good thing to know is that greenhouse horticulture feeds much of its electricity back into the grid. They use the heat themselves and the energy that is ‘left over’ can be used by others. When compared to generating electricity in a power plant, where it is not always possible to use the heat that is released, this is a significant step forward in terms of efficiency.
The systems that horticulturalists use are also on stand-by to handle peaks. Since a CHP can be scaled up or down much more easily, they form an important link in what is known as congestion management.
In recent years, all kinds of new solutions have been devised for the storage of energy for longer or shorter periods of time. The heat that is produced when generating electricity can be temporarily stored in a buffer tank when heat is not required in the greenhouse. This means that peaks and troughs can be compensated for during the day.
Heat
This is a good solution to serve as a ‘day buffer’ but it will not fix the difference in ‘free’ heat between summer and winter periods! The greenhouse effect means that heat from the sun can easily filter through to the greenhouse, but not out of it. During summer, the windows have to be opened to dissipate this heat, but of course, a much better solution is to store the surplus heat so that it can be used during the winter.
This is being done on an increasing number of farms by using heat and cold storage. The heat is pumped into the ground in summer and extracted in winter. As early as 2006, grower Maurice van der Hoorn in Ter Aar built the first ‘greenhouse without gas’ to make use of this system.
The use of geothermal energy has also been expanded with wells being sunk into deeper earth layers, for example, to a depth of 2.3 kilometers as part of the Trias project. The warm water from these sources is used to heat greenhouses. This is done via a heat network that around 50 companies will be connected to.
A great solution, but the use of geothermal heat calls for major investment and the fact remains that electricity (for lighting, pumps and cooling) and CO2 will still be needed. The latter can also be supplied, for example, via the so-called OCAP pipeline which can supply the CO2, a waste product from e.g. Shell, to the horticulturalists via a long pipeline.
Green energy
A major concern among horticultural business owners are electricity rates. Due to a government regulation, it has become fiscally very unattractive to purchase green electricity. This means that these entrepreneurs are still choosing to generate their own electricity with a CHP. This therefore means that gas is needed again, even though they could manage to do without it otherwise.
So, a lot is already happening in the horticultural sector in the area of energy efficiency, but the sector is not yet climate-neutral. The overall goal is for the entire sector to be able to do without natural gas by 2040.
Yet there are also companies that believe that this is taking too long. The Koppert Cress company, for example, plans to be energy-neutral as soon as 2025. A greenhouse has been built that costs a million euros more per hectare than a ‘normal’ greenhouse. This is a huge investment, but one that will make it possible to save a substantial amount of energy.
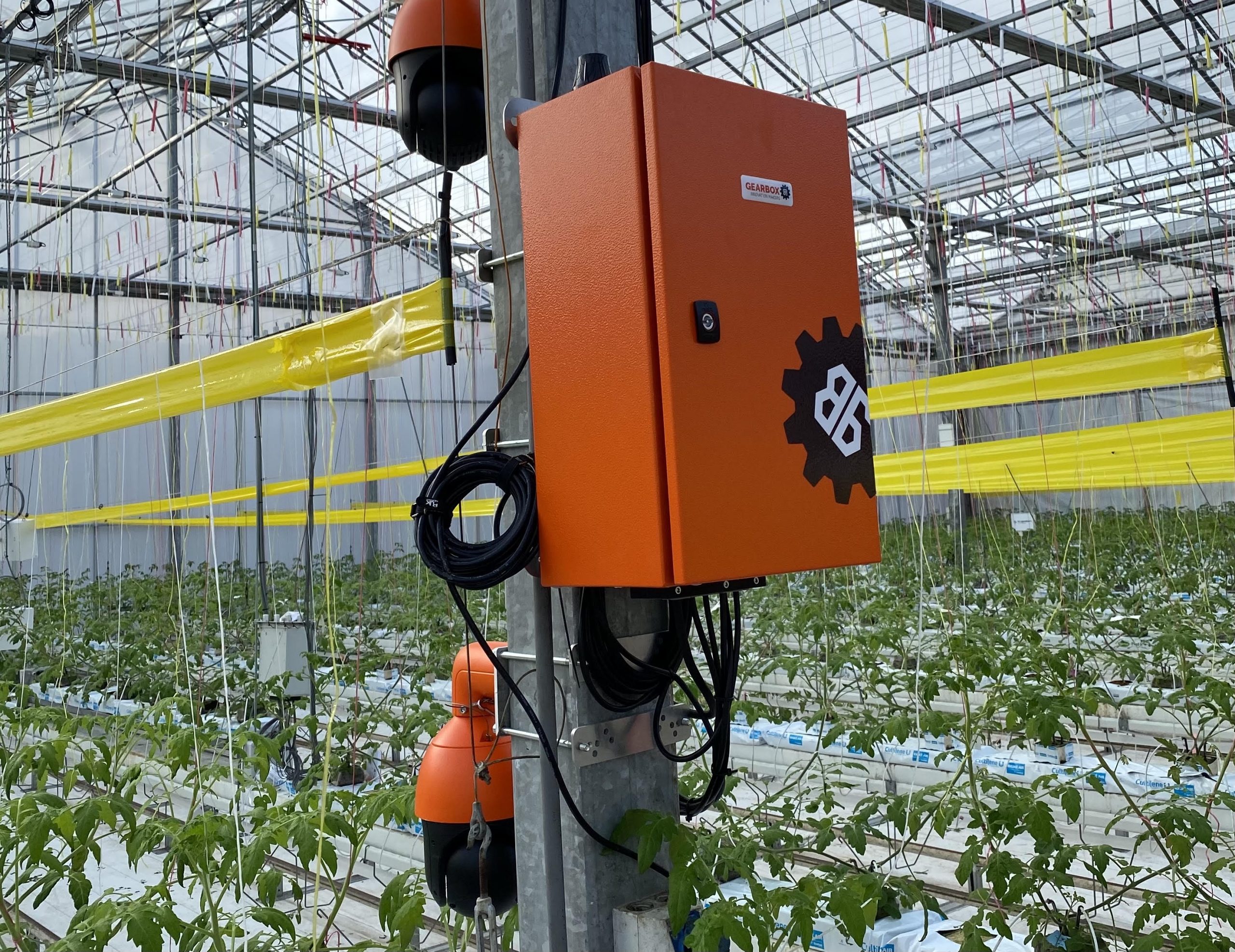
Several innovations are currently being tested at this company as well. One of the other companies involved in this is the Delft-based Physee, which has been working for several years on the development of windows that convert light into electricity. They are developing a coating for greenhouses that converts UV light, which cannot normally be used by the plant for growth, into photosynthetic active radiation (PAR). This means that more light (for growth) can enter the greenhouse. This is ‘free’ light which means that no lamps need to be switched on.
Cooperation
Another innovation that is undergoing testing at Koppert Cress is the thermal battery from Thermeleon. The technology they are developing is similar to that of the walls used in the very first greenhouses to store heat. The system stores heat when it is too hot in the greenhouse and releases it again as it the temperature drops.
All in all, serious consideration is already being given to innovations in the area of energy in greenhouse horticulture. There are a number of developments but they are often too expensive or risky for a grower to undertake on their own. This is where, as is so often the case, cooperation is important! There are probably also innovations outside the sector that would be very well suited to horticulture. I am very keen to find out which companies are developing innovative products which we as the horticultural sector could make use of. Not only to produce in a climate-neutral way as soon as possible, but also to ensure that our horticulturalists will still be able to grow enough healthy and safe food for our region 10 years from now.
About this column:
In a weekly column, alternately written by Eveline van Zeeland, Eugene Franken, Katleen Gabriels, PG Kroeger, Carina Weijma, Bernd Maier-Leppla, Willemijn Brouwer, Maarten van Andel and Colinda de Beer, Innovation Origins tries to figure out what the future will look like. These columnists, sometimes joined by guest bloggers, are all working in their own way to find solutions to the problems of our time. So tomorrow will be good. Here are all the previous articles.