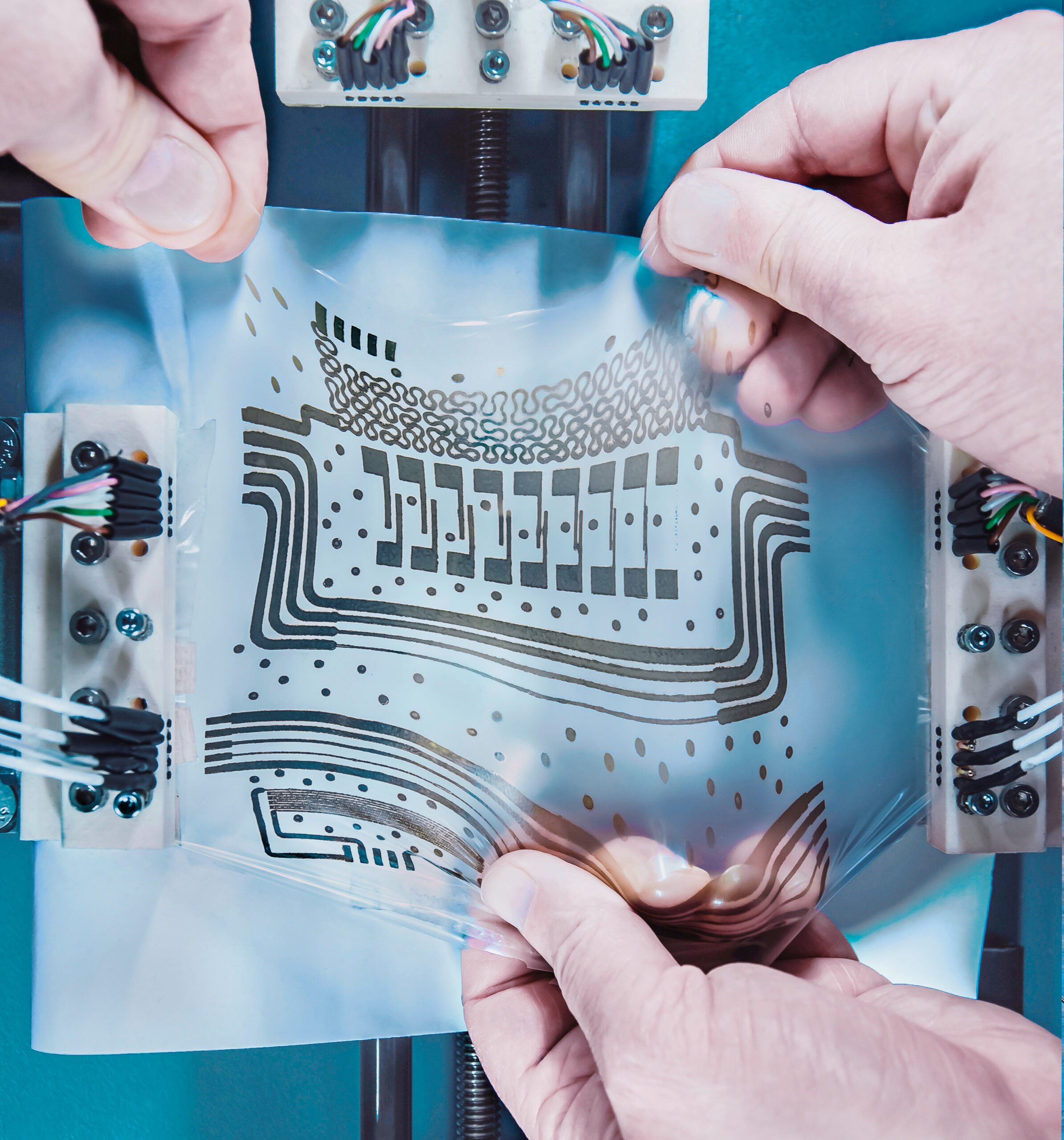
When integrating electronics into soft, movable materials, crush and stretch resistance is important. In elastic plastic films or textiles, the required components must withstand high mechanical stresses. Research in the field of these so-called stretchable electronics or stretchables is in full swing. These will enable technological interaction between the environment and the body. Integrated into textiles or patches, stretchables can be used to record or optimize performance and monitor physical functions. Other areas of application include prostheses and robotic arms.
Ink systems for stretchables
There are two methods of applying electronics such as conductive tracks or sensors to stretchable surfaces: inkjet printing and screen printing. Inkjet printing uses somewhat more fluid ink while screen printing uses paste with a honey-like consistency. As a result, the latter has a higher viscosity. Common technologies for conductive ink and paste systems are based on nano- or microscaled fillers such as silver micro flakes. The filler particles are bonded to polymers and impart conductivity to them. The disadvantage of these fillers? They are very expensive.
Self-reducing ink systems
A promising approach to stretchables has been found in self-reducing ink systems. Here, fillers are not added but are formed in the printing process during the curing phase of the compound. These self-reducing ink systems are more affordable, but cannot yet be implemented commercially because toxic chemicals are involved in their manufacture.
Also of interest: Constant conductivity in stretchable e-textiles (German only)
“The self-reducing ink systems described in the literature to date for the production of stretchable conductive webs contain toxic reducing agents such as sodium borohydride, which are harmful to humans and the environment,” explains Professor Thomas Griesser from the Institute of Chemistry of Plastics at the University of Leoben, Austria. Together with partners from industry and research, he and his team have developed an equivalent ink system that does not require these toxic chemicals.
The self-reducing ink systems described in the literature to date for the production of stretchable conductive tracks contain toxic reducing agents such as sodium borohydride, which are harmful to humans and the environment.
Dr. Thomas Griesser
Silver ink
The researchers achieved this by developing a novel ink system based on the self-reducing silver compound silver formate. The conductive components of the ink consist of silver nanoparticles. These can be produced by self-reducing a silver compound. The formate anion, a salt of formic acid, acts as the reducing agent. In the reduction process, the ink is heated so that the silver compound decomposes to elemental silver.
Polymerization
The ink system also contains monomers that polymerize at elevated temperatures to form an elastomer. This leads to the formation of nanocomposite material. These are silver nanoparticles embedded in an elastomeric matrix that exhibits high conductivity even when stretched.
The elemental silver forms nanostructures that are embedded in a polymer matrix and give the printed ink film its conductivity.
Dr. Thomas Griesser
The reduction of the silver compound and the polymerization of the monomers occur simultaneously. This is triggered by heating the compound to over 100° C in the printing process. The research consortium tested the process in the form of both ink and paste. Both could be applied to stretchable materials in a structured manner by means of printing.
Sensors and conductor paths
Ink systems for sensors and conductive tracks were developed. The challenge was to get electronic functionality for both applications. Griesser comments: “With conductive tracks, you want to have a small change in electrical resistance under a mechanical load. In contrast, the conductivity of sensors should change greatly under strain.”
The sensors, on the other hand, are strain sensors. That is, their function is based on increasing the spacing of silver particles in the plastic matrix and changing the resistance.
Enormous elasticity
Another new feature of the system is the enormous elasticity of the conductors and sensors, which can be as high as 200 percent, explains Griesser. Compared to common stretchable screen printing pastes, the new system proved superior even under cyclic loading. This opens up a wide range of application areas
This new self-reducing ink makes it possible to produce stretchables on elastic films. As such, the ink would be an ideal material for use in items such as the artificial skin on prostheses or robots, Griesser explains. It could also be used in smart clothing to monitor bodily functions.
Sensor patch
In collaboration with Joanneum Research Materials Weiz, Austria Technologie & Systemtechnik AG and the start-up Human Research, the technology has already been used to develop a sensor patch. The ink was screen-printed in a structured manner onto a thin elastic film. The sensor patch is self-adhesive and is applied to the chest, where it enables simultaneous monitoring of heart and breathing activity. But there are also other applications in medicine and sports for such sensor patches.
The advantages of the sensor patch are high wearing comfort and low manufacturing costs. It is also environmentally friendly because it consists largely of biodegradable polyurethane film. The silver in the printed conductors can be easily recycled.
Applications in mining
Together with their colleagues from the Department of Mining Science, the researchers from the University of Leoben have found another field of application: Rock bolts are used in mining to secure cavities in the mountain. These rock bolts consist of long metal rods that act as supports. Under a high rock load, these metal rods can warp. To detect changes in length in time, researchers are now working on sensor foils that can detect them.
Also interesting: New sensors improve mind-controlled prostheses (German only)