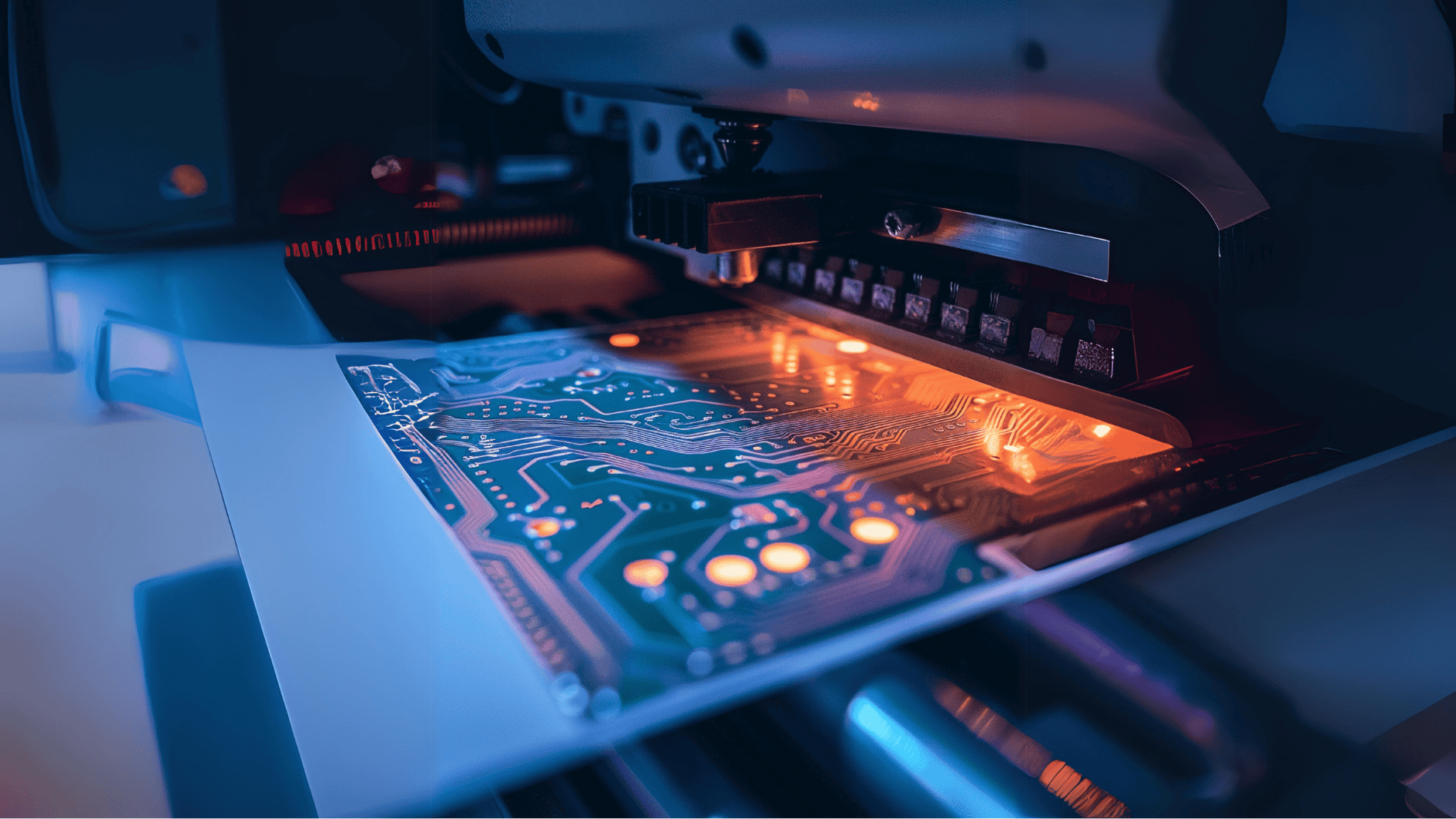
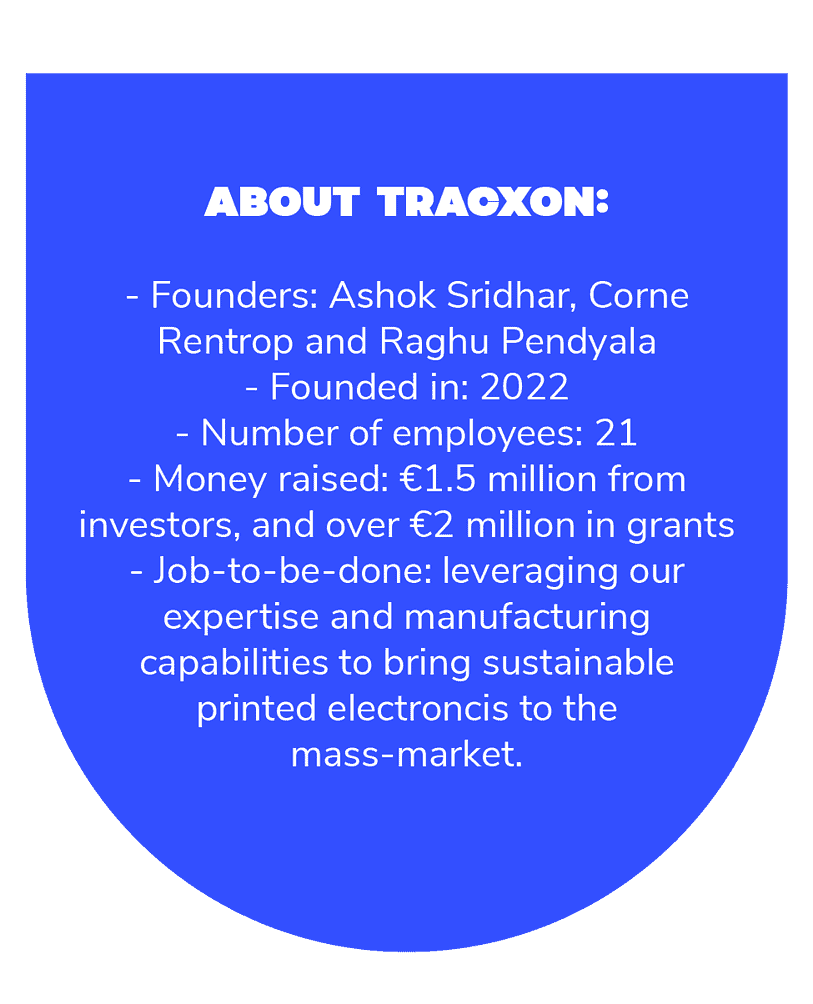
At the heart of most electrical devices are printed circuit boards (PCBs). These thick and sturdy – often green – boards house circuits and can be considered the brains of a remote control, a blender, or a TV screen. Instead of rigid PCBs, more and more devices need thinner and possibly flexible solutions in a factory in Eindhoven; TracXon, a spinoff of the Holst Centre supported by imec and TNO, prints hybrid electronics.
TracXon’s ultimate goal is to replace at least 10% of traditional circuit boards with more sustainable printed electronics technology. This means replacing billions of non-recyclable and rigid printed circuit boards annually with recyclable, printed electronics.
The origins of TracXon
Work on printed electronics has been going on at Holst Centre since 2005. The electronics are produced using additive manufacturing and are completely recyclable.
Says Ashok Sridhar, co-founder and CEO of TracXon: “When the technology was mature enough to go to market, TNO said, ‘Ashok, Corne, and Raghu, why don’t you start a company that can make electronics based on whole center technology?’ The sheer breadth of the technology and its complexity meant that no other outside company could successfully achieve mass production. Taking the initiative into our own hands was the best decision, as this gives the Brainport ecosystem all the ingredients to help TracXon make a huge impact in the electronics industry.”
And so it did. Currently, the startup has customers from eight countries on three continents. It built a production facility—including clean rooms and unique machinery—within three months last year. It achieved two major certifications (ISO 9001 and ISO 13485) within a year of opening the plant.
In our latest magazine – IO Next: Gerard & Anton Awards – you read about the 10 winners of the 10th edition of our own Awards Show. We look back at the 90 winners before them and look ahead to the impact these 100 winners together are making on the world.
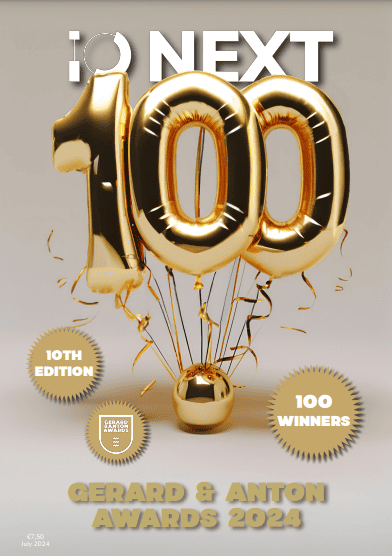
Thinking big
Over the next five years, the company plans to produce millions of IoT sensors for various applications, including wearable patches for healthcare applications. In ten years, millions of cars should drive around with smart user interfaces and glass-integrated functionalities enabled by TracXon’s technology.
“We believe this is going to be big. We intend not to set up a small-scale production but to become the largest company in this market in the next five years. In that time frame, we want to change the industry’s mindset. This technology makes Many applications possible, and we want to be the first,” says Sridhar.
Brainport: building machines is in the DNA, but limited energy supply is a problem
As a trailblazing manufacturing company, TracXon needs highly skilled operators and engineers, as well as unique machines. Brainport Eindhoven, with its talent pool and machine building in its DNA, is the perfect location for TracXon to grow. “We are already discussing with machine builders from this region how to build our future production lines based on our ideas, designs, and patents. But the energy supply is minimal, especially at our location (De Hurk in Eindhoven). It will be tough for us to scale up our production activities if the shortage is not solved soon,” Sridhar concludes.
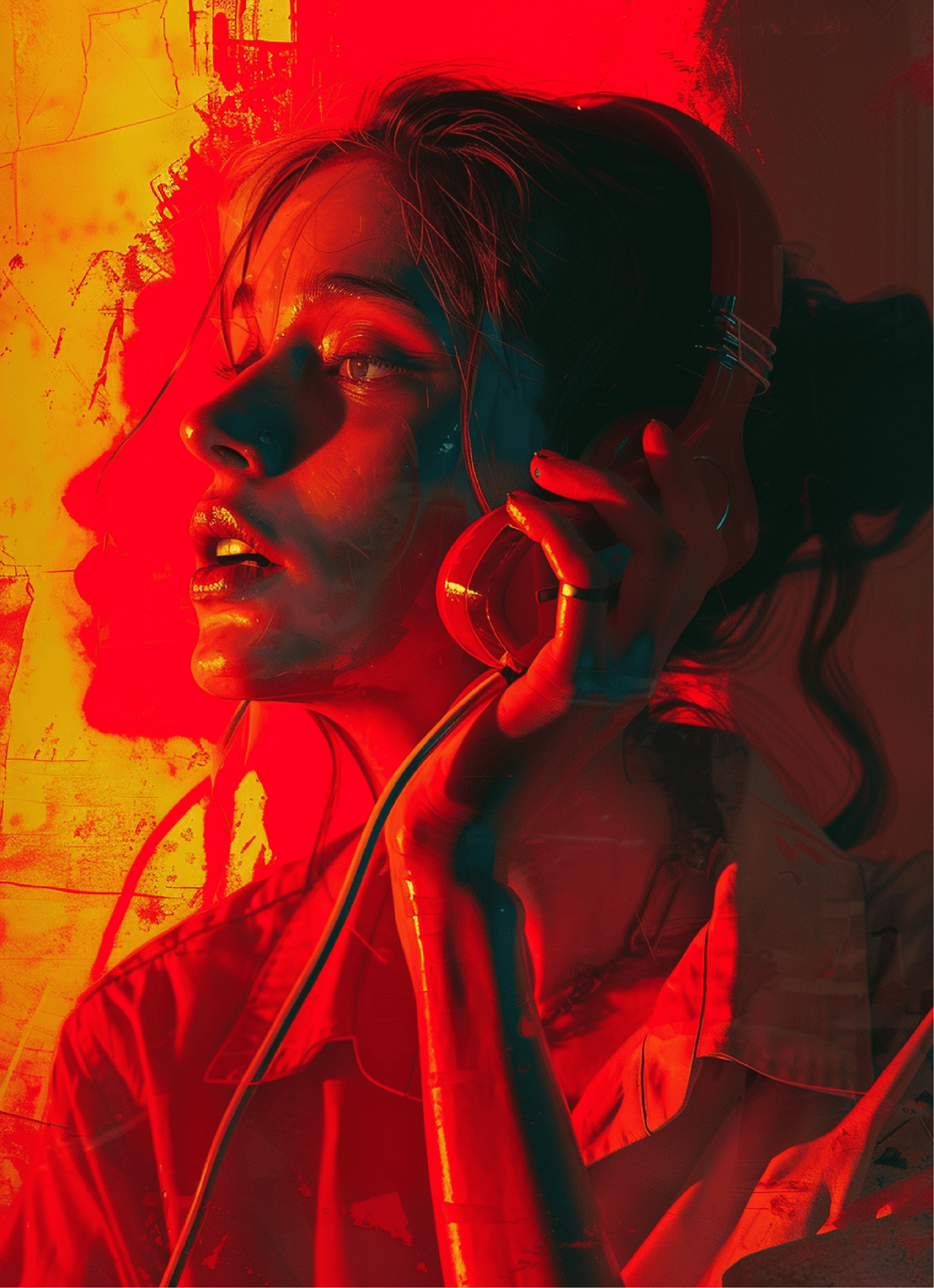
The Gerard & Anton Awards are supported by EY, Rabobank, V.O. Patents & Trademarks, TWICE, Kadans Science Partner, Braventure, Lumo Labs, Gemeente Eindhoven, High Tech Campus, Philips, Goevaers & Znn. B.V. and DeepTechXL.