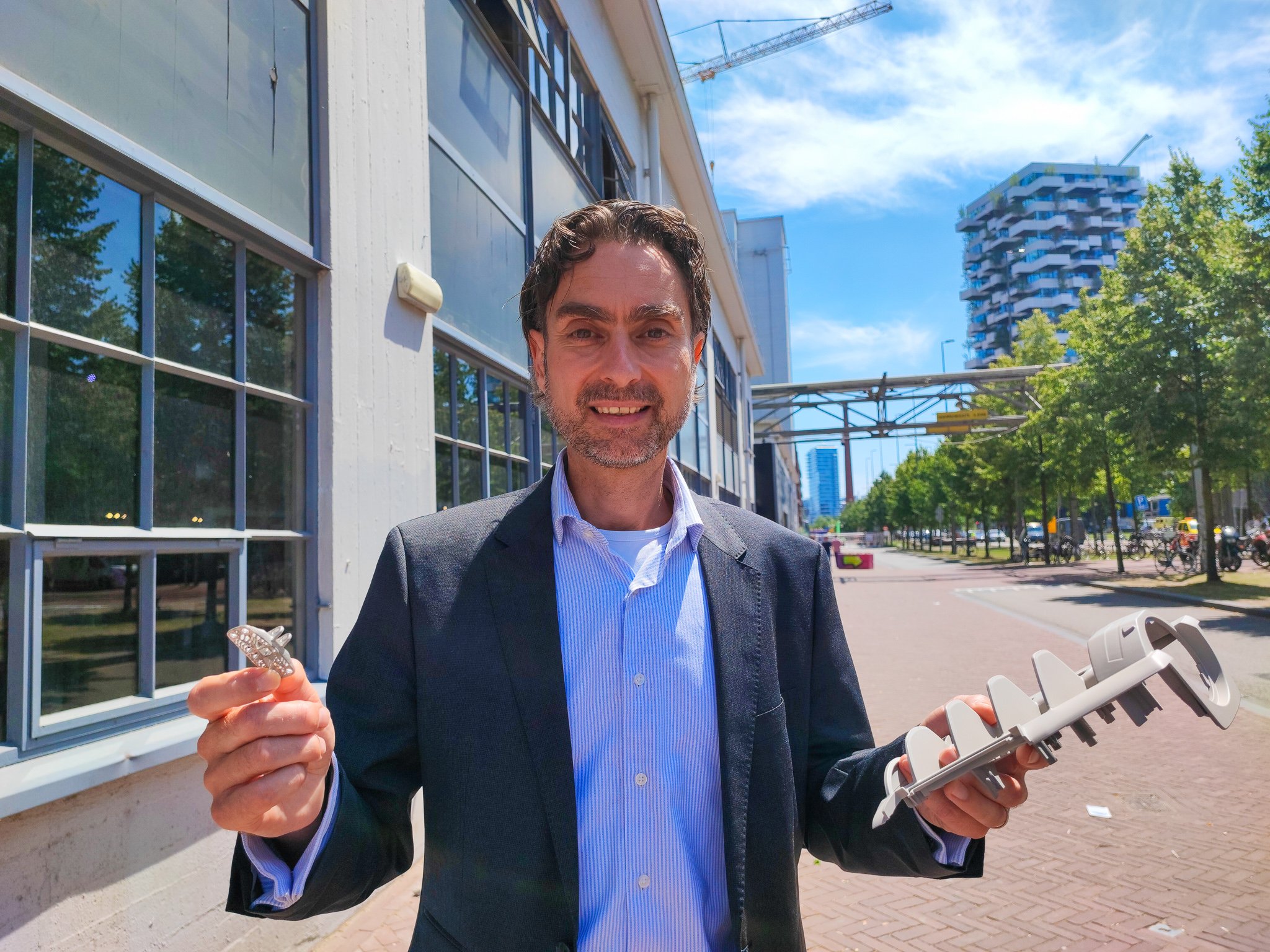
Building a product layer by layer from the computer. In the late 1990s, 3D printing still sounded like science fiction; now it’s a common technology, says Bart Kooijmans, Program Manager of Precision Technologies at Mikrocentrum. “It’s showing up in industrial end products and more and more people have a 3D printer at home.”
Kooijmans was one of the pioneers of the introduction of 3D technology into the industry. As a researcher in Rapid Prototyping at TNO Industrie en Techniek, he was allowed to buy the first 3D printers from around the world in the late 1990s to explore what the technology could bring to the Dutch industry. “We recognized even then that this would be a disruptive technology,” he says.
The art of printing
“Before the days of 3D printing, you started with a lump of material, like steel or plastic. Around that, you then milled away everything and were left with what you wanted. Something was already there. Or you injected material into a mold cavity, for mass manufacturing. With 3D printing, there is nothing yet. It’s a totally reverse process, with less waste and more freedom of form. You can make it into all kinds of shapes that you can’t make with drilling and milling. It’s a technique that doesn’t require any other tools either.”
Kooijmans remembers giving lectures on 3D printing with colleagues at the Eindhoven University of Technology. At the time, students could still choose this as a subject, explains Kooijmans. Back then, Kooijmans was “laughed at a bit” when he made the analogy to printing. “First you wrote a book, with a pen. The art of printing meant that you could multiply that into thousands. Then, with a printer, we could make unique single pieces again. Later again, it was quite normal to have such a printer at home. We painted a picture of how 3D printing would work. People laughed at me, but twenty years later you buy a 3D printer in the toy store for your child.”
Shorter design time
At TNO, Kooijmans and his colleagues brought the first printers to the Netherlands. Like the Stratasys machine from America, the Kira 3D printer from Japan, and the Actua wax printer. An increasingly broad spectrum of technologies and materials emerged. From the Rapid Prototyping demo department set up, especially for this purpose, the applicability to the Dutch industry was tested.
“We looked together with a company at how it could benefit from it,” says Kooijmans. “What was missing at the time was demand. Nobody knew about this technique yet.” A competitive advantage turned out to be the shorter design time. “In no time at all, you could be holding the first prototype.”
In ten years, the initiatives grew into European-subsidized projects on which research institutes from several countries worked together. “That’s how we explored the whole scope,” he says.
Tremendous momentum
We did this in the open industrial domain, says Kooijmans, “But it also happened as ‘best-kept-secret’ behind the closed doors of major stakeholders such as automotive, aerospace and OEMs, who saw in this an opportunity to make major strides in their competitive edge.”
Developments within 3D printing gained tremendous momentum, Kooijmans continues. “With stimulus money, regions and international institutes pitched in as centers of development.” As an example, Kooijmans mentions the Brainport region, with its own gathering place for the entire chain at Brainport Industrie Campus (BIC). “But there are also development centers in Twente, Amsterdam, and Rotterdam. And in Belgium, Flam3D is a leading umbrella initiative.”
The industry has fully developed 3D printing into a production technology with which you can make high-quality products, according to Kooijmans. For the high-tech manufacturing industry, 3D printing with metal offers yet another whole new area of application. “As well as printing with high-tech plastics or biomaterials does”, Kooijmans adds. “We are no longer talking about 3D printing, but about true additive manufacturing of end products. This also involves a whole lot of certification. You have to be able to make a product that you can safely screw into an airplane. Or take a tooth made of technical ceramics: you can’t just stick that in a mouth.”
Remote maintance
Nowadays there is also an issue like Model-Based Definition: how do you work with a 3D file from the computer? “That is separate from 3D printing and actually applies to all manufacturing technologies. In the old days, with a 2D drawing, you also described how smooth the surface should be and what color it had to get. How do you put that information into a digital file so that the entire production chain of suppliers, customers, and the internal employees are on the same page?”
Virtual reality is one step further, Kooijmans continues. “That technology is also getting better and more applicable. Then you don’t even have to produce a 3D prototype anymore but put on a pair of VR glasses and you can walk around in any given environment. That saves another step.” According to Kooijmans, producers are struggling with the question: how do you bring it to the industry. The housing and gaming industries in particular are deploying the glasses. “But you can do much more with them professionally. Remote maintenance, for example: the mechanic doesn’t have to go into the factory. He puts on one of those 3D glasses, the worker goes into the factory with a camera. That way the mechanic can see which screw is loose.”
Trade show
In 2011, Kooijmans made the move to Mikrocentrum, an independent knowledge and networking organization for the high-tech and manufacturing industry. In addition to courses, Kooijmans started the trade show for 3D printing, RapidPro, there. “The technology deserved its own trade fair and congress,” he says. The congress became an annual event. This year it is part of the 3D Production Days taking place this week at the Klokgebouw in Eindhoven.
Fried Vancrean, CEO of Materialise, will open the Production Days. Kooijmans: “Materialise is really a frontrunner within 3D printing. They built the factory of the future years ago. They were the first to set up a next-day service: you send a file and the next day you have it printed out in plastic. Today the company is Nasdaq-listed and has sales of 200 million. The technology scales up so quickly to final production in cars or medical applications it shows what is possible.”
In addition to Rapid Pro, the 3D Production Days will include conferences on Model-Based Definition and Virtual (R)evolution. Those events are also part of 3D Delta Week. Here are the other episodes in this series.
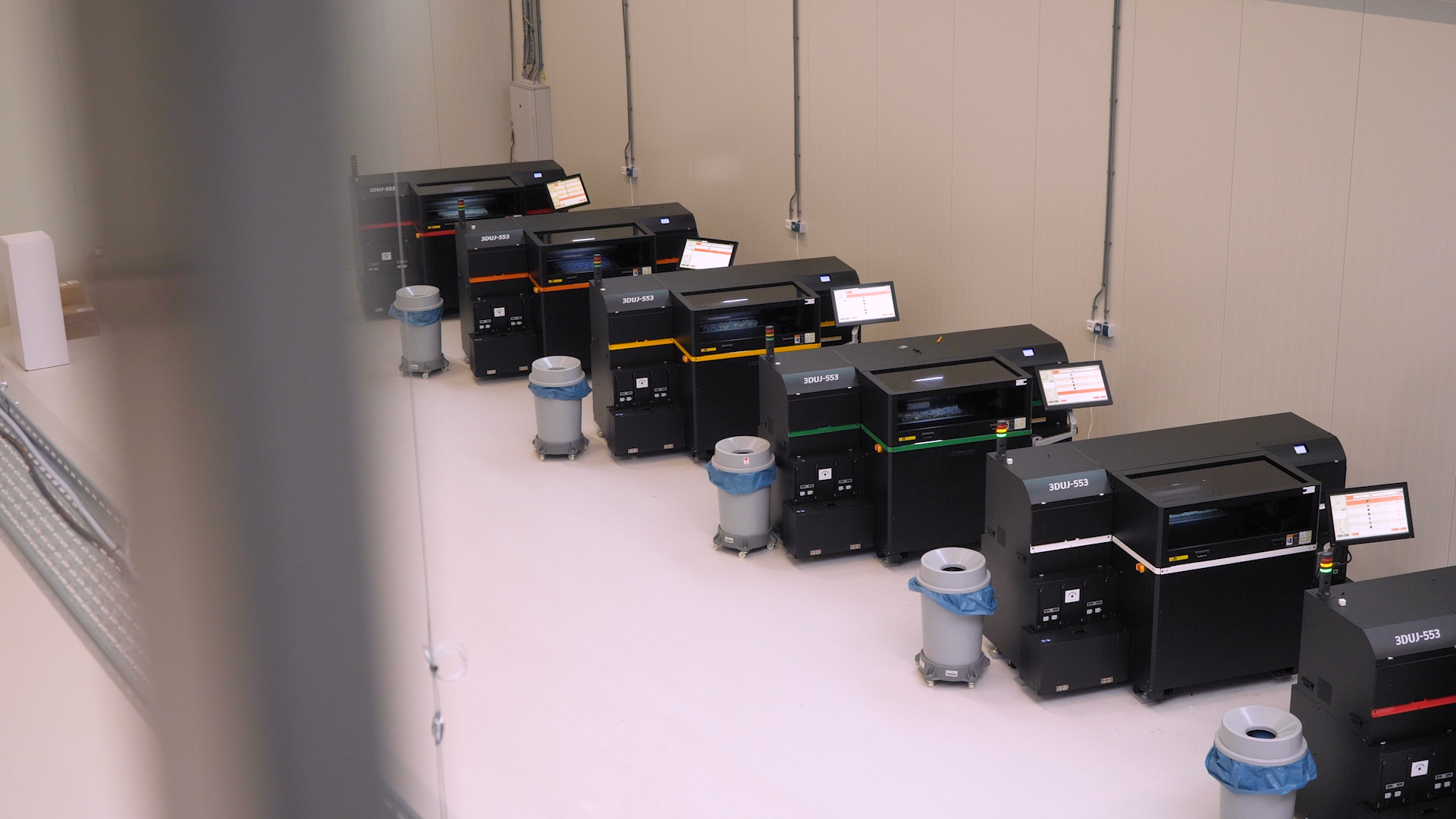