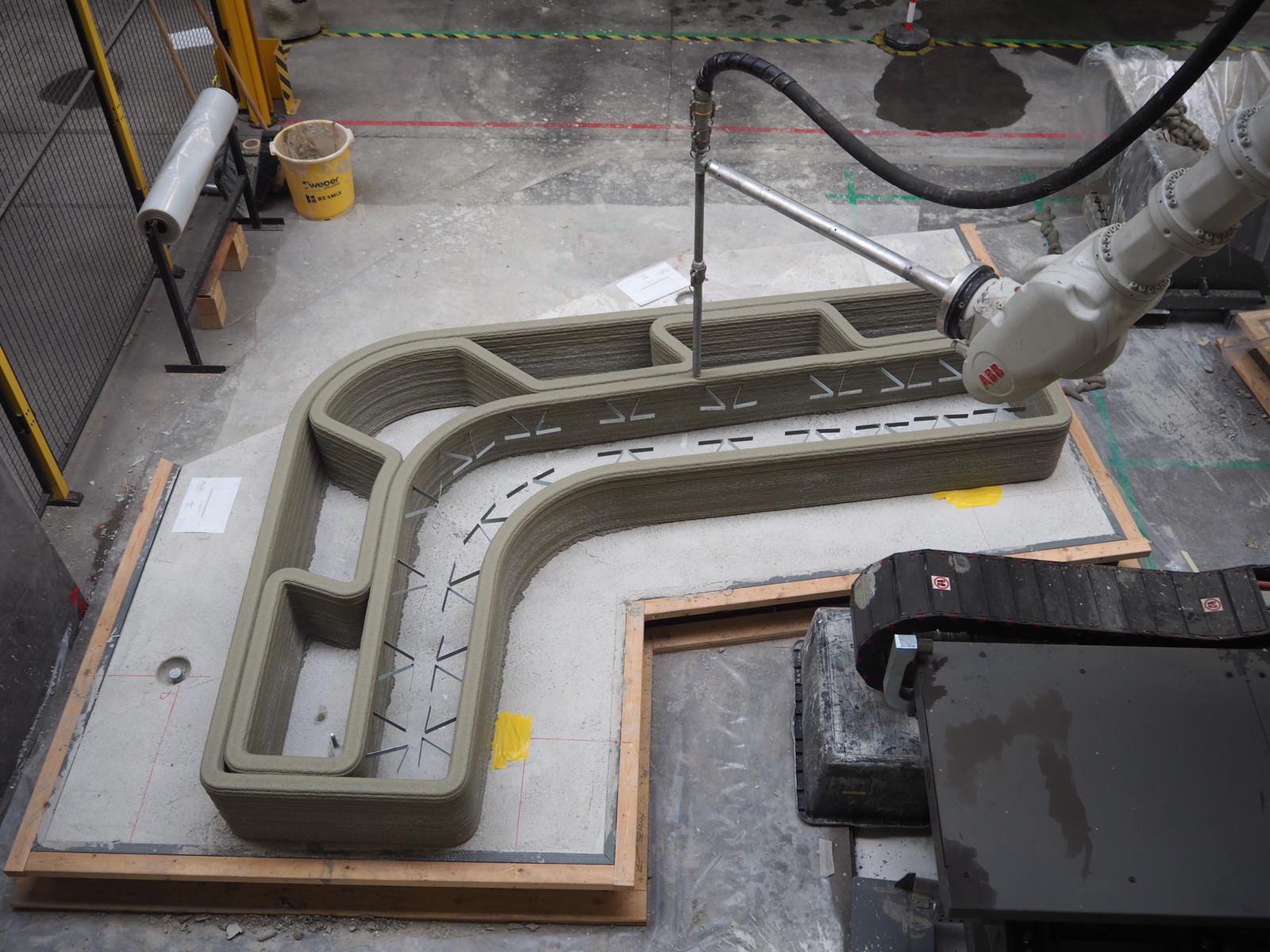
In the 3D Delta Week Brainport Eindhoven shares knowledge about Additive Manufacturing. One of the companies is Weber Beamix which 3D prints with concrete. This is the fourth story in a series on 3D printing and additive manufacturing. Read the rest of the series here.
3D printed bridges, a house, a more than twelve-meter high pigeon tower. These are the concept cars in the world of 3D printing with concrete, says Peter Paul Cornelissen, manager of 3D printing at Weber Beamix. “These cool projects show what is technically possible. With such projects, we are pushing the boundaries of this production technology.”
More sustainable
Weber Beamix produces and supplies, among other things, the mortar from which concrete is made. Mortar is a substance consisting of sand, water, and a binding agent such as lime, plaster, or cement. Cement is the most common. “Using 3D printing with concrete, you need much less material,” says Cornelissen. “Among other things, 3D printing is more sustainable for that reason; it reduces CO2 emissions.” Globally, the cement industry is responsible for about eight percent of man-made CO2 emissions.
“Also, when you look at the operational challenges of companies, 3D printing with concrete offers advantages,” Cornelissen continues. “For example, it leads to shorter delivery times and is potentially an answer to staff shortages. 3D printing has the advantage that you automate and digitize an entire process. You can set it up so that a robot does the work. As a result, you need fewer people for the same work.”
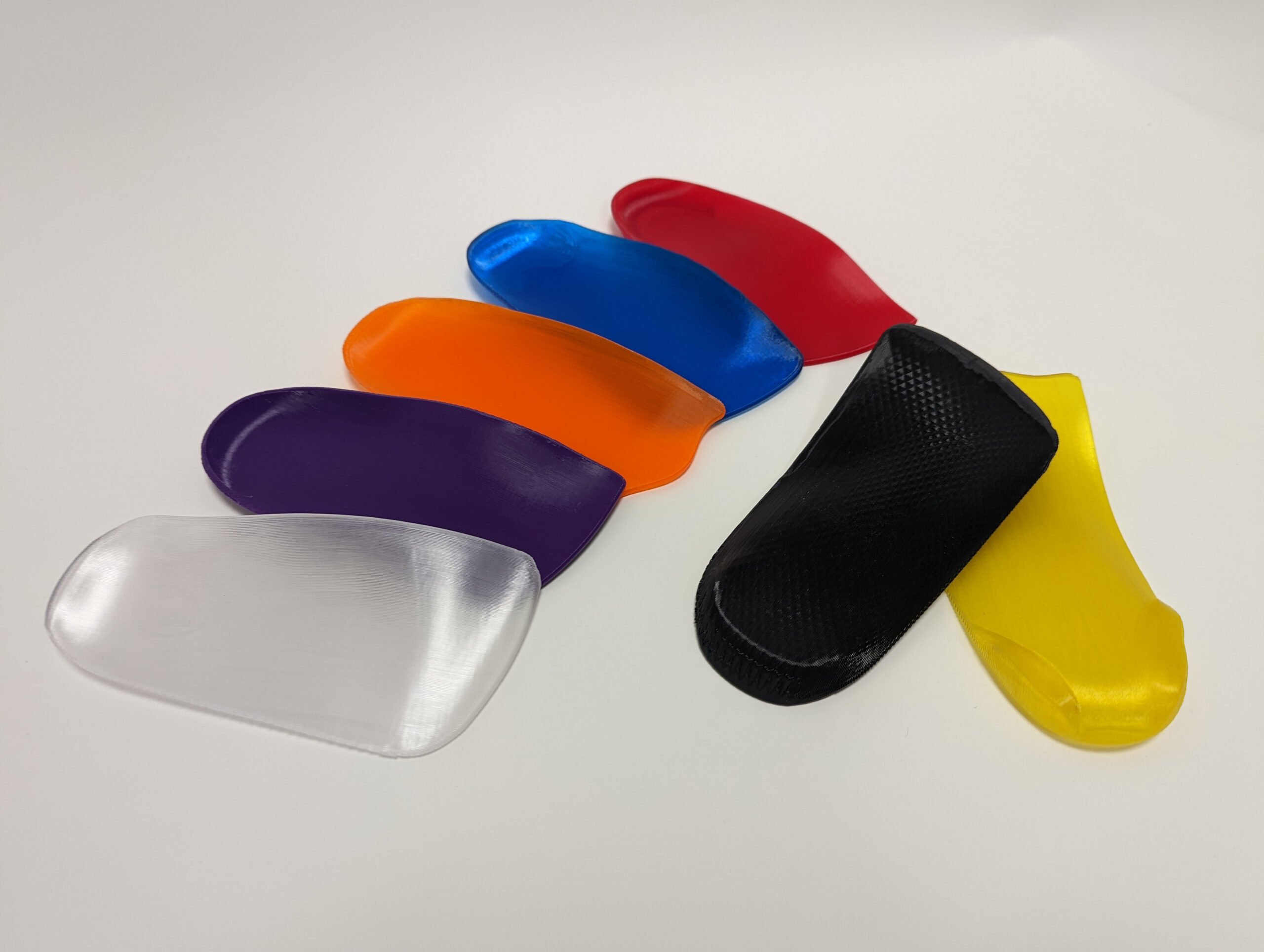
Load-bearing
The company has been experimenting with 3D concrete printing since the beginning of this century. In 2005 already, it printed a concrete wall. The collaboration with professor Theo Salet, from the Eindhoven University of Technology (TU/e), accelerated the development, Cornelissen says. Scientific research led to a technology that was directly applicable to the building sector. The cooperation with TU/e resulted in projects like the first 3D printed bicycle bridge in Gemert and Milestone, the 3D printed house.
Within that collaboration, Weber Beamix concentrated on the development of the 3D process and the mortar. Cornelissen: “Our mortar has a reputation in the construction industry for its good properties.”
The special feature of this mortar is that it is load-bearing, adds Gian Sterken, 3D Sales project manager at Weber Beamix. “No additional reinforcement or concrete is needed to make it structural. We build the load-bearing structure without additional reinforcing steel. For a bridge, we print hollow precast parts, using prestressing.”
Printing beds
Together with BAM-Infra, Weber Beamix set up the first European 3D concrete printing factory in 2019. Since the middle of last year, the mortar company has been one hundred percent owner of the factory. Cornelissen: “BAM works as a contractor, we actually apply the mortar.”
“We print the parts and elements in our factory. This allows us to produce very efficiently and to monitor the quality of the end products.” That saves, according to Cornelissen, an enormous amount of time. “For example, fewer people need to be at the various construction sites because that work has already been done or prepared in the factory. As a result, the lead time on site can also be greatly reduced.”
The plant has two so-called printing beds that can print blocks of about twelve meters long in three meters wide and three meters high blocks. “We don’t do that; we wouldn’t be able to lift that,” Sterken says. “In practice, we go up to about 6.5 thousand kilograms.” For the bicycle bridge in Nijmegen, Weber Beamix printed parts of six thousand kilograms.
Smaller objects
Examples such as a bridge, house, and a tower are nice, according to Sterken, but he believes the gains are mainly in relatively simpler objects. Sterken mentions the talus steps at railroad tracks and dikes. “In the Netherlands, we have an enormous amount of kilometers of dikes and ProRail also manages so many thousand kilometers of embankments. Every kilometer of embankment has a staircase. Each staircase at each embankment has a different size. With 3D concrete printing, you can offer customization very quickly and flexibly.”
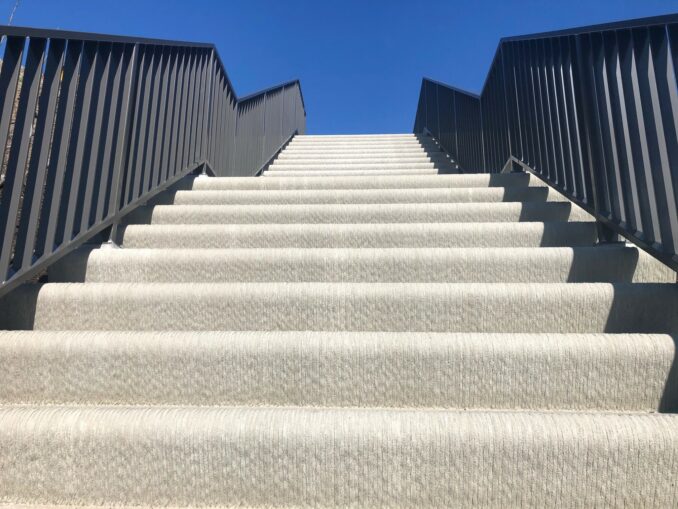
3D concrete printing also means freedom of form. Sterken thinks a good example of this is the round tree box at Driebergen-Zeist Station. “An exterior element like that has to be able to withstand some pressure. With our mortar platform, you can print that quickly, in all shapes and desired strengths.”
Factory abroad
To take the printing process to the next level, Weber Beamix works closely with TU/e. In addition, the company is part of the international Saint Gobain conglomerate. Cornelissen: “In Eindhoven, we are the Global Competence Center for 3D concrete printing within Saint Gobain. In addition to our own R&D department for the development of, among other things, the mortars, we get support from the R&D department in Paris. And in the printing factory, a lot is happening as well. We use all this knowledge to constantly take our mortar platform to a next level.”
Next summer, Weber Beamix will open its first factory abroad. “Where exactly, we can’t announce yet,” says Sterken. “Until two weeks ago there was an extra factory set up in our factory. We have set it up here and adapted it completely. The people who will be working with it have also been trained here.”
Around 3D Delta Week, which was held from June 20 to 24, IO is publishing a series of stories about 3D printing. Read the whole series here.