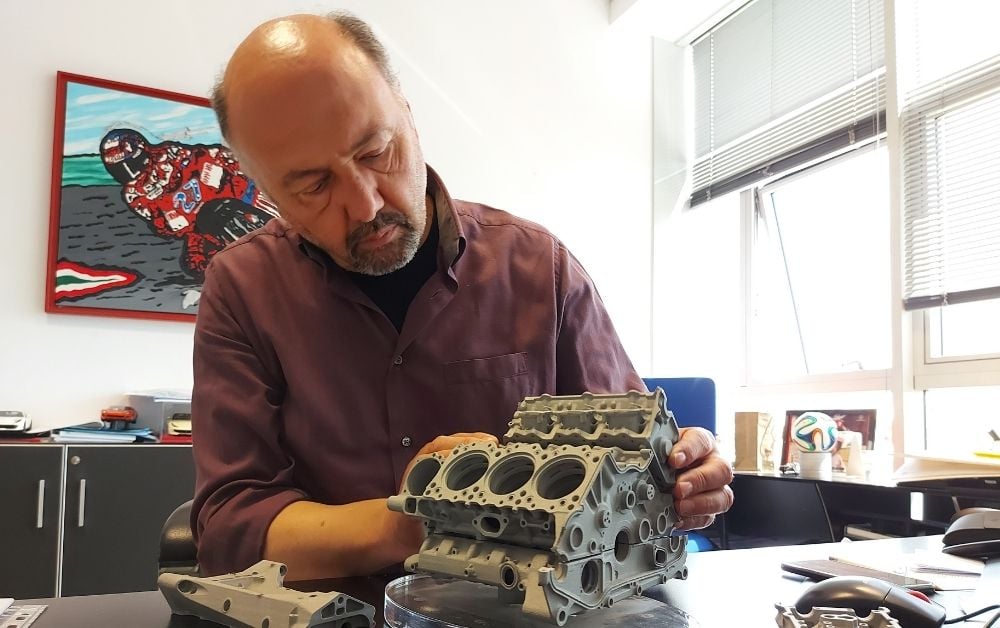
What do Ferrari, Lamborghini, McLaren, Williams, Lotus, Tesla, BMW, Amazon and Maserati have in common? All these companies have (part of) their vehicles made by one and the same supplier.
The supplier in question is completely unknown to the general public thanks in part to the company’s anonymous-sounding name. CPC is the name of the company. This calls to mind click per cost, a term from the online advertising world, rather than the initials of the original founders. CPC from Modena (central Italy) is currently headed by Franco Iorio, an engineer by profession. The company develops everything related to “vehicles in motion,” as Iorio (pronounced “jorio”) puts it during an interview with Innovation Origins at CPC’s headquarters.
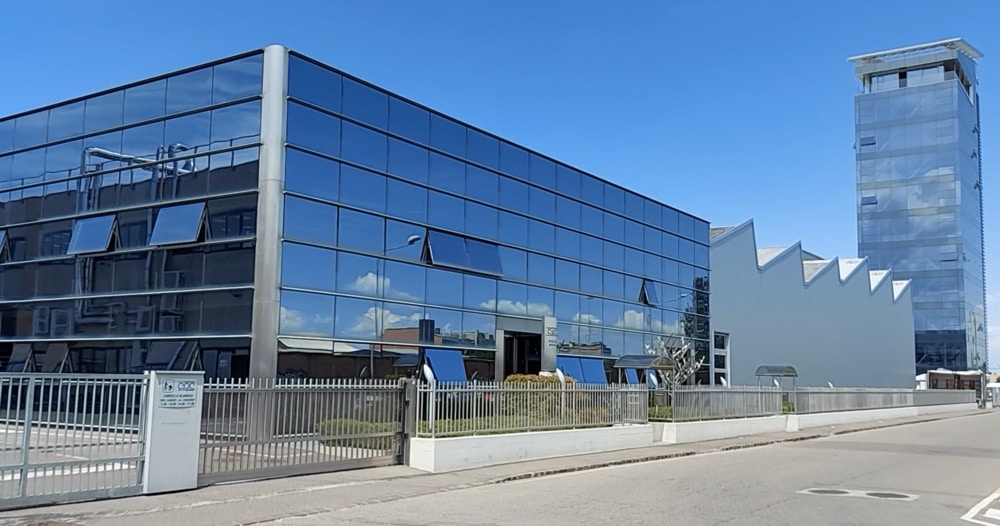
“We are system suppliers and can handle all the manufacturing stages for a customer, from the development of individual components to the manufacture and assembly of the entire vehicle,” says Iorio. That may sound like a sales pitch, but after a company visit to CPC, it is clear that this company really is the beating heart of the Italian Motor Valley.
The Motor Valley is the name given to the area around Modena where most of the world’s supercars (including Ferrari, Lamborghini, Maserati) are designed and manufactured. All makers of supercars come to Iorio as well as providers of new forms of sustainable mobility more and more as well. For instance, the engines of the Lamborghini Aventador and the bodywork of the electric Maserati Mc20 are built there. But some of the elements of the Tesla S also come from Modena.
Composite materials
CPC has traditionally specialized in engines and mechanical parts. For example, the company has developed engines with Ferrari and is still doing that. On Iorio’s desk is a model Ferrari engine which demonstrates the connection with the famous automobile manufacturer. But CPC owes its spectacular growth in recent years to Iorio’s fingerspitzengefūhl. Fifteen years ago, the director-owner invested in the manufacture of composite parts, fiber-reinforced plastics. This relatively new form of material use at the time was gaining popularity in the world of racing.
The advantage of composite materials containing (among other things) carbon fiber is that it makes the chassis much lighter. The weight reduction can be as much as fifty percent compared to steel or aluminum. Despite this, the material is still extremely strong. Also, the torsional stiffness (difference in pressure on the wheels) is substantially lower and the lower center of gravity provides better road holding. Ferrari, Williams, and the other Formula One manufacturers recognized early on that lighter yet robust cars save time on the road and thus success on racetracks.
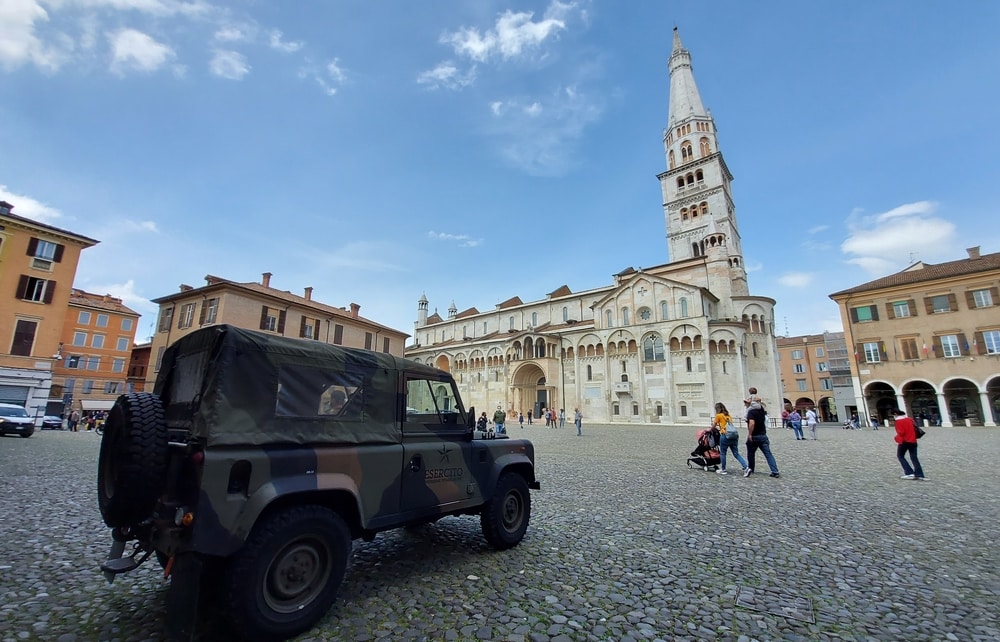
The Italian Motor Valley got in early. For example, the first model that Horacio Pagan brought to market some 20 years ago was built of composite materials, after which this Pagani Zonda was renamed the first hypercar in history: it was a lighter car with even more engine power.
Giampaolo Dallara is another pioneer. Dallara now builds the (composite) chassis for all participants in the Formula E, the electric Formula 1. Not surprisingly, there are plenty of suppliers in Italy, such as Magnabosco, that specialize in the manufacture of autoclaves. An autoclave is a mix of oven and pressure chamber, where composite parts harden under high pressure and temperatures.
The use of composite materials is no longer confined to racing. Parts of motorcycles and aircraft are also manufactured with them. Composite materials have a future, especially in electric mobility. That’s in great demand in the era of the electric car. The lower the weight, the more energy efficient a car is, the less battery capacity is needed. Fiber composite also comes in handy in other modes of transport modes of the future.
It is not for nothing that CPC has been chosen by both Google and Amazon to work on their future vehicles. With Amazon, the Italians are working on the development of the Zoox, an autonomous robot cab, which, among other things, was tested on public roads late last year, as shown here:
Even though CPC is very much focused on innovation for the benefit of new types of mobility, the CEO is still skeptical about the electrification of vehicles. “The electrification of cars is triggering a genuine industrial revolution, in terms of the design of cars as well as the different types of electric motors. But for the time being, it can basically only be used in a hybrid vehicle. Society is not yet ready to switch over to electrical completely. There is simply not enough clean energy out there”.
In any event, Iorio is eager to do his part for a sustainable society. Composite materials do offer a contribution, even if recycling the material is still problematic.
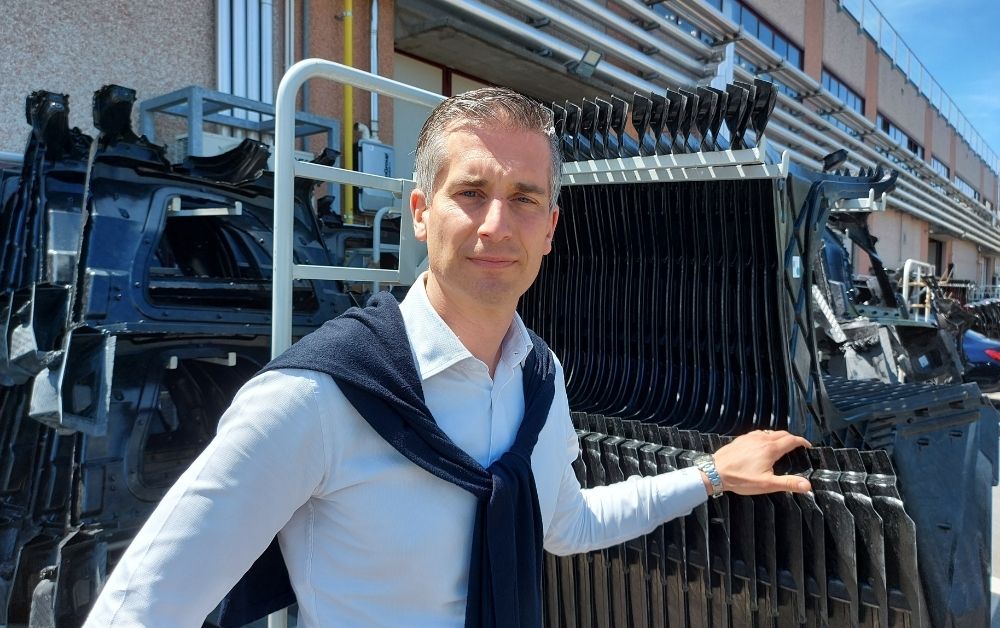
Composite materials also enables large parts, including complex shapes, to be made in one piece, even an almost complete chassis. The fewer parts, the less complicated the vehicle is, which in turn helps to lower costs. “The future of composite materials is joining components of large proportions in carbon fiber, and lightweight,” Thomas Vecchi explains.
He is the second in command at CPC. “The future of the automobile lies in the challenge of reducing the number of components that it is made up of. We aim to glue rather than bolt the few components together, thereby strengthening the structure. We have learned from Formula 1 that this works”.
Producer of carbon fibers
The Italian company has one significant asset. Iorio transferred 44 percent of the company’s shares to Mitsubishi Chemical in 2017. This company is one of the largest producers of long carbon fibers. With Mitsubishi as a partner, CPC will likely never be short of composite raw materials.
Moreover, CPC had invested early on in the industrial manufacturing of carbon composite (normally it involves a lot of manual work). CPC has had the privilege of having put into operation the first European press-compression machine with a capcity of 5 by 3 meters, which is sufficient for making, for example, a whole chassis. The automation has led to a much lower manufacturing time, higher output and lower costs.
Read more about the challenges of the Italian Motor Valley
The Motor Valley has also set the standard for electric motorcycles.