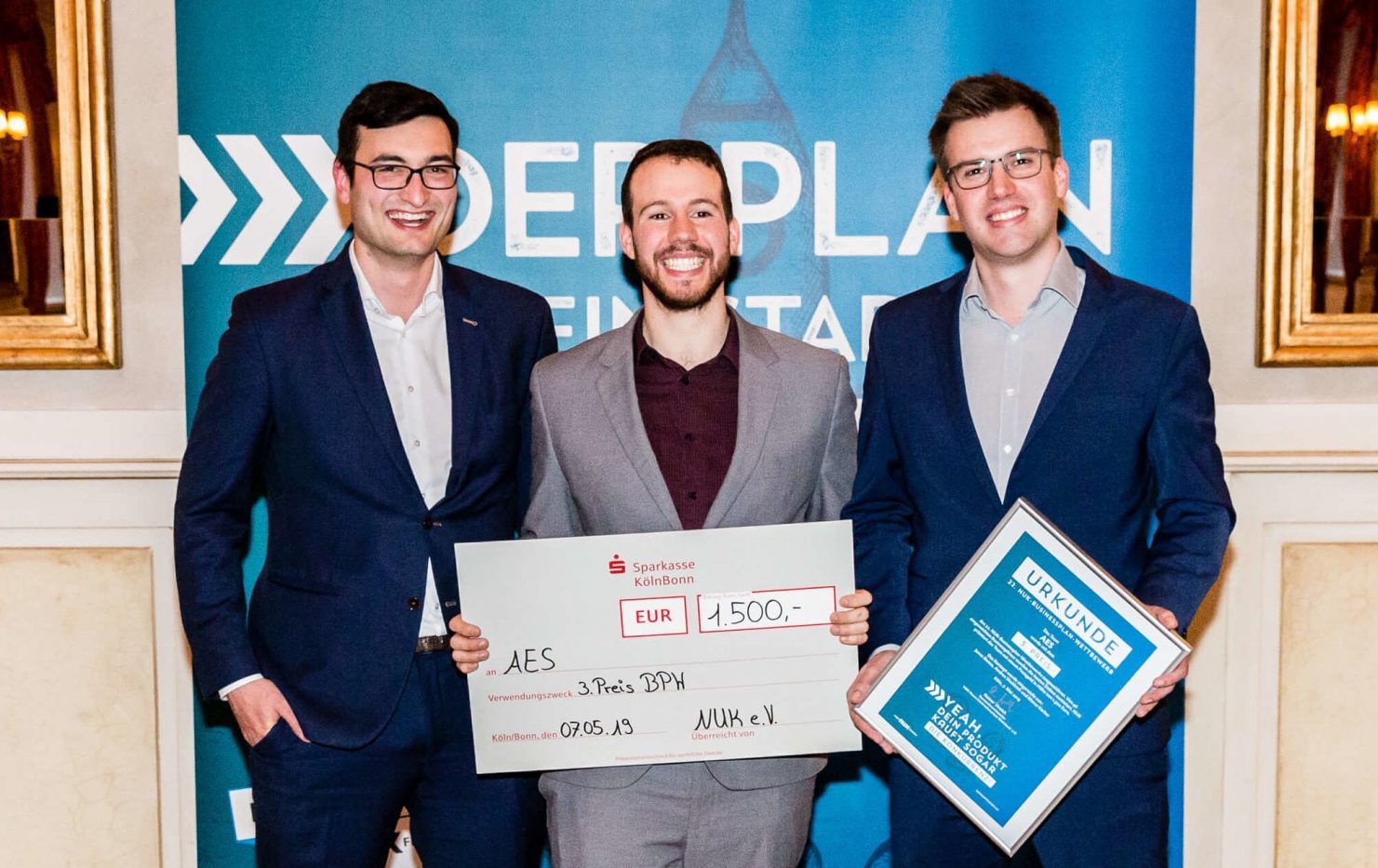
Two major challenges await us in the future. Actually, they have been with us for a long time already. We produce too much waste. While we need more and more energy. The Aachen start-up AES – Autonomous Energy Systems has developed a solution for both problems. But there is also a third point – independence. The systems function in a decentralized manner, so companies can independently generate energy from their waste and save on electricity costs. That sounds pretty good. We talked to Marco Karber, one of the company founders, about how energy can be generated from waste.
How does your plant work exactly?
We are all about generating energy from waste. In our plant, the pyrolysis furnace, mixed waste can be recycled. Our first customer will be a retirement home. This means that in this case hygiene waste, gloves, and incontinence material will be recycled. But also kitchen garbage, i.e., organic and garden waste. The retirement home employee just goes down to the basement with the garbage bag and throws it into the plant. First, the waste is shredded, then the material is fed into the pyrolysis reactor, which we have designed precisely for this purpose. This produces gas that is subsequently burned. The resultant heat is directly used again by the plant for the pyrolysis process. Oil is also produced which is then burned to provide heat and electricity. Both can be used directly by the consumer.
So the consumer also supplies themselves with their own energy when they dispose of their waste?
Yes, they can cover up to 20 % of their own energy requirements. The efficiency of the system is around 60 %. This means that far more energy comes out than goes in. The greatest savings are achieved in waste. Half the amount that usually goes into garbage cans can be eliminated. In larger facilities this saves enormous costs in waste disposal.
Can I put such a system in my basement at home?
Originally, the system was actually intended for private households so they could generate energy from waste. But during the developmental phase, it became clear that operating it successfully would only work with a higher volume. That’s why we turned to retirement homes, hospitals, and hotels. Even larger restaurants could be added. Such facilities have a constant high energy demand. The system is able to run all year round. In the textile industry, too, discarded clothes that aren’t recycled could be salvaged and the oil could be reused.
Do you have any customers yet?
We are not there yet. since the plant is still in the development stage. We’re working closely with our future customers in order to tailor our pilot plant to their needs as much as possible and are also cooperating with the Institute of Textile Technology at RWTH Aachen University in Germany. We are in an incubator program there and are on-site at the institute, so we can use the workshop and laboratory to do analyses.
How did you come up with the idea of producing energy from waste?
My colleague Andres Sheldrick and I studied process engineering together. While getting our master’s degree, we brainstormed and developed ideas from time to time. We thought about possible processes that have not yet been brought into the 21st century and found that many of them were already patented. But we continued to pursue the idea of decentralized waste recycling. We also discovered that there are hardly any decentralized plants that are controlled digitally. First of all, the savings potential was important to us, but being able to make a contribution to sustainability is, of course, even better.
Have there been critical moments so far?
There have been a few. The development phase of obtaining energy from waste is a lengthy process. You always have to make changes in the design, make new parts, and try them out. There are long dry spells before the next success comes along. We started right after graduation. Then, of course, there was a financial problem. We always had to figure out where the money for the next parts would come from. It is risky to start something like that after your studies with no financing. But now we are at a good point and we will soon find an investor who supports us in our final year.
In the beginning we worked in my basement – we couldn’t even stand up straight in it. Later on we were able to use a kind of pavilion with a mentor and since our foundation as a start-up, we have been able to use the workshop at the Institute of Textile Technology. We have only been able to work properly since January.
What challenges do you still see coming?
Once the plant is up and running, the most important thing will be done then. We’ve been busy with the development for a year and a half now and have already overcome a number of hurdles. Finding our place in the market will not be that difficult, we believe, because we have very good sales arguments. The system pays for itself within five years and from then on you begin saving money. We already have declarations of intent from retirement homes; they are very enthusiastic about the idea.
What are the next steps?
It will still take another four to six weeks until the prototype is ready and another six months for the pilot plant. Right now we have to wait for parts that are made in China. We need to find an investor to get us through this past year. Then the pilot plant will be built; we already have a customer for that. That will be done by November. Hopefully in a year’s time we will be able to deliver the first plant.
You can read more articles about start-ups here.
More IO articles on the sustainable reuse of waste here.