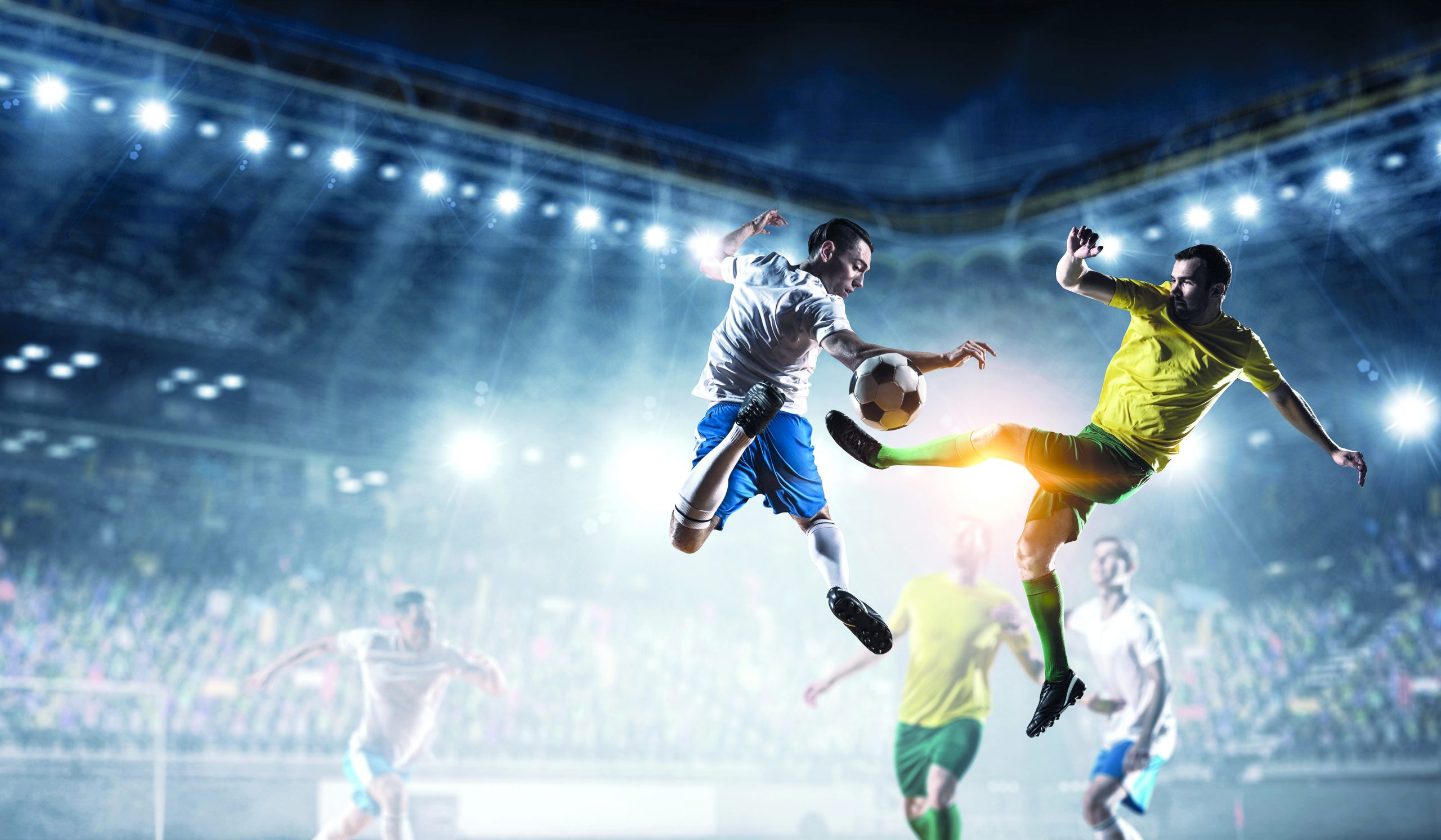
One of the most innovative gems on the Chemelot Campus in the Dutch town of Geleen is perhaps Arlanxeo, a subsidiary of the world’s largest oil company, Saudi Aramco. Which means it is a throwback of the old fossil fuel industry. But at the same time, it is one of the few producers of sustainable rubber that uses far fewer petroleum-based raw materials.
But what exactly is sustainable rubber? -That’s a question for Herman Dikland, a chemical engineer and head of innovation at Arlanxeo. “It’s not the case that this rubber is biodegradable,” says Dikland. “Try to imagine if a rubber car tire was biodegradable, then it would crumble under certain circumstances. Whereas the tire has to last a long time. When we talk about sustainable rubber, we are talking, for example, about synthetic rubber such as EPDM (ethylene propylene diene monomer rubber), whose main raw material, ethylene, is not extracted from naphtha (a product processed from crude oil) but rather from bioethanol.”
Vast fields in Brazil
This bioethanol is produced from sugar cane that is grown on vast fields in Brazil, the largest sugar producing country in the world. “Ethylene is made out of that bioethanol.”
Plant-based rubber produced by Arlanxeo, which bears the brand name Keltan Eco, is more sustainable than synthetic rubber made from petroleum-based raw materials for two reasons, says Dikland. Firstly, Keltan Eco’s CO2 footprint is 85 percent lower than that of comparable conventional synthetic rubbers.
That percentage has been determined by examining the entire production process, from sowing the sugar cane in the ground to the finished product delivered to the customer.
Sugar cane continues to grow after harvesting
Secondly, once the sugar cane has been harvested to make bioethanol, it simply grows again. “In this sense, it is a renewable resource that can regrow within a few months. Whereas fossil fuels take millions of years to develop.”
At the moment, it is not possible to recycle used rubber at a competitive price, Dikland notes. “You cannot melt or dissolve rubber. This means you can create fantastic technological products that can withstand high temperatures. But it is precisely these properties that make them difficult to recycle back into their original raw materials.” This is still too expensive.
But that could change in the future. “You can see right throughout the industry’s value chain that rubber processors want to do just that. If at some point, customers start asking for these products, the industry will start innovating in order to supply them.”
In contrast to polymers, not much research has yet been undertaken into making rubber recyclable, confirms Niels van der Aar, chemical engineer and project manager Sustainability at Arlanxeo. The composition of polymer products is purer than that of rubber products. When it comes to plastic, often more than 99 percent of the same raw material is used. Whereas with rubber, this is often less than half. That makes it more difficult to recycle.
Recycling rubber is difficult and expensive
Dikland points out that a recycling policy for rubber such as the EU is introducing for plastic as of next year is not yet in place. One reason for this may be that polymers are used much more widely in plastic products. About 80 percent of synthetic materials are polymer-based, 10 percent are rubber and 10 percent are synthetic resins.
Consequently, it is still difficult to recycle rubber and offer it as a product at an attractive price. But that is not impossible, according to Dikland. “In the Netherlands, a few million car tires are crushed for recycling each year. The grains are used, for example, to make floors for playgrounds. They can also be integrated into the bitumen that is used to make freeways. And they are used to extract dye for black ink.”
No matter how sustainable we may become as a world, Dikland and Van der Aar both expect that the demand for rubber to remain. We will just be more economical with it. Rubber is a raw material that you don’t usually see. But it is necessary in battery production for separating rechargeable cells. “It’s in your car around windows, in the engine, on your shower head to prevent water from leaking.”
Is chewing gum biodegradable?
And it is even in chewing gum. It would be a godsend for many municipalities if that kind of rubber would become biodegradable. In that case, civil servants no longer need to scrape off the countless white globs off the sidewalk in a cleaning frenzy. And unlike car tires, chewing gum doesn’t have to last more than an hour. But this application is not yet ready either, says Van der Aar, because the technology is not there yet. “Although that might well be possible in the future.”
There will be more sustainable rubber on the market in ten to fifteen years’ time, Dikland expects, because then there will probably be far more demand for it. This means more research will have been done into adapting the raw materials than is currently the case.
On one point, however, a lot of environmental gains can quickly be realized. Namely, by making all EPDM rubber out of ethylene based on bioethanol. This is more likely to happen if there is a tax on CO2 emissions for the manufacture of it. This can be done as far as capacity is concerned,” says Van der Aar. “But as long as it is more expensive than petroleum-based rubber, it won’t happen on such a large scale.”
You can also read the previous articles in this series: ‘‘The Chinese and Americans are knocking on the Dutch town of Geleen’s door to test innovative chem tech’
‘Xilloc: ‘Requests from dozens of hospitals worldwide for 3D-printed implants’