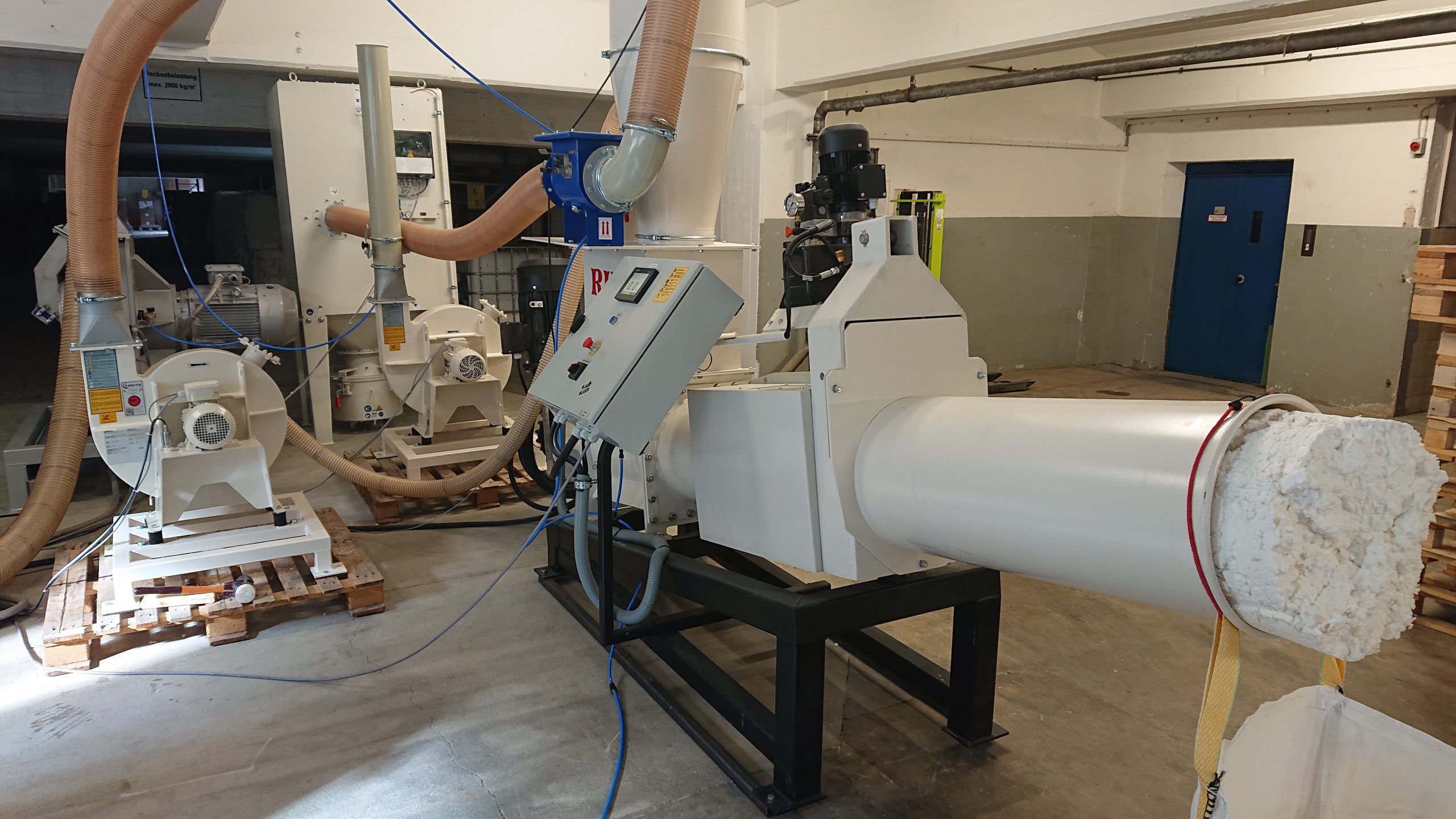
Separating trash โ including paper โ for recycling purposes is common practice in many places. Despite this, recycling paper is not as optimized as it could be. Specialty papers, such as labels, cannot be recycled with the usual water-dissolving process.
Consequently, it ends up in regular trash. To save more paper from going to waste, TBP Future has developed the so-called Dry Pulping technology, allowing specialty papers to be returned to recyclable fibers that can be reused in paper making.
Tons of paper wasted
Based on how much paper is produced each year and how much is being recycled, the team calculated just how much specialty paper ends up in the trash. Another important factor that was considered in this calculation is roughly how much paper never enters this cycle. This can include things such as library books, bank notes, and certain files, for example.
โThis estimate indicates that approximately one million tons of specialty papers go to waste in Germany each year,โ says Dr. Tilo Gailat, one of the CEOs of TBP Future. With dry pulping, a large part of this waste could be avoided.
The machine, a so-called Dry Pulper, works with a four-step process. First, it shreds paper into smaller pieces that the machine can digest. Second, these shreds are broken up into fibers by air whirls within the Dry Pulper. In the third step, the fibers are separated from the air and, in a final step, compressed into a pulp which can be used in paper production once more.
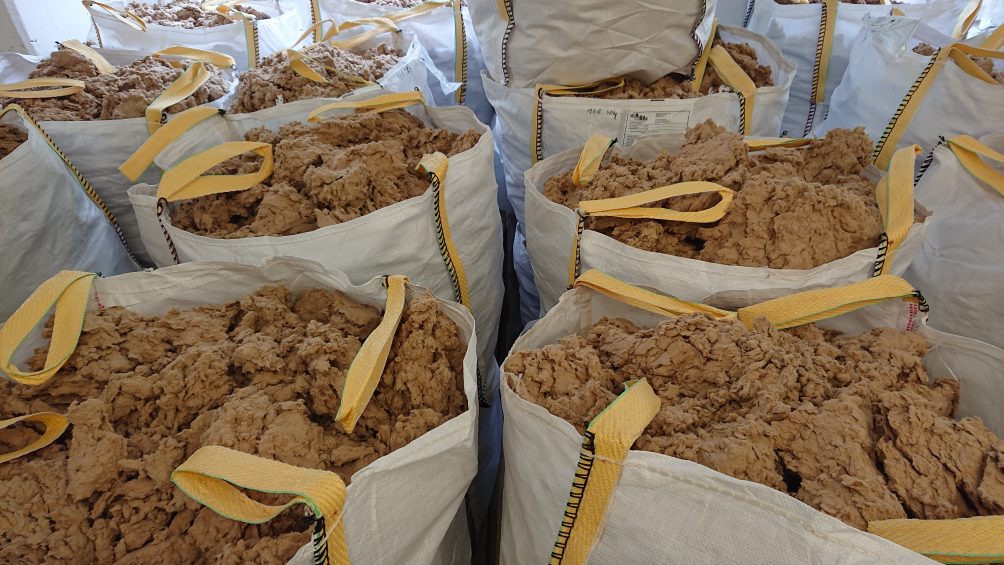
Avoiding water in the process
An important factor of this recycling method is that it doesnโt require large amounts of water used in the regular paper recycling process. Unlike specialty papers, regular paper dissolves into fibers when being mixed with water, creating a pulp that can be transformed into paper again. Specialty papers are often water-repellent, making the normal method ineffective, next to being wasteful.
โWe know that the huge amounts of water used in paper production lead to an enormous amount of energy needed in the process,โ says Dr. Gailat, adding โwe said to ourselves: if we manage to keep water out of this process, weโd save a lot of energy. The longer the process continues without water, the more energy we can save.โ
While thereโs a great environmental benefit of requiring less water, dry pulping isnโt able to replace the recycling process for normal paper fully just yet. While the machine is able to break down normal paper into its fibers as well, using this method is actually using slightly more energy. โThe energy consumption is only favorable for us if water is kept out of other processes, such as the processing of fibers โ or if weโre treating specialty papers,โ explains Dr. Gailat.
Origins in Dresden
TBP Future was originally born out of a research project of the Technical University (TU) Dresden. For this project, dealing with printing ink removal, the team required little shreds of paper. Workers in the lab had to cut up paper with scissors and realized after only a couple of days that it was too labor-intensive and inefficient.
In search of a machine that could take over the task, they discovered a machine that could cut up paper into tiny pieces. While these pieces were too small to be used in the original research project, it inspired the idea of developing a technology that could reduce paper to fibers which could be reused in the paper production process.
In order to develop this technology further, a spin-off, Rethink Paper Making (RPM) was founded in collaboration with the TU Dresden. As the company expanded, RPM and engineering company TBP Group founded TBP Future, with Dr. Tilo Gailat and Matthias Ungerer as CEOs, Thomas Schrinner as project leader, and Professor Harald Groรmann as a consultant.