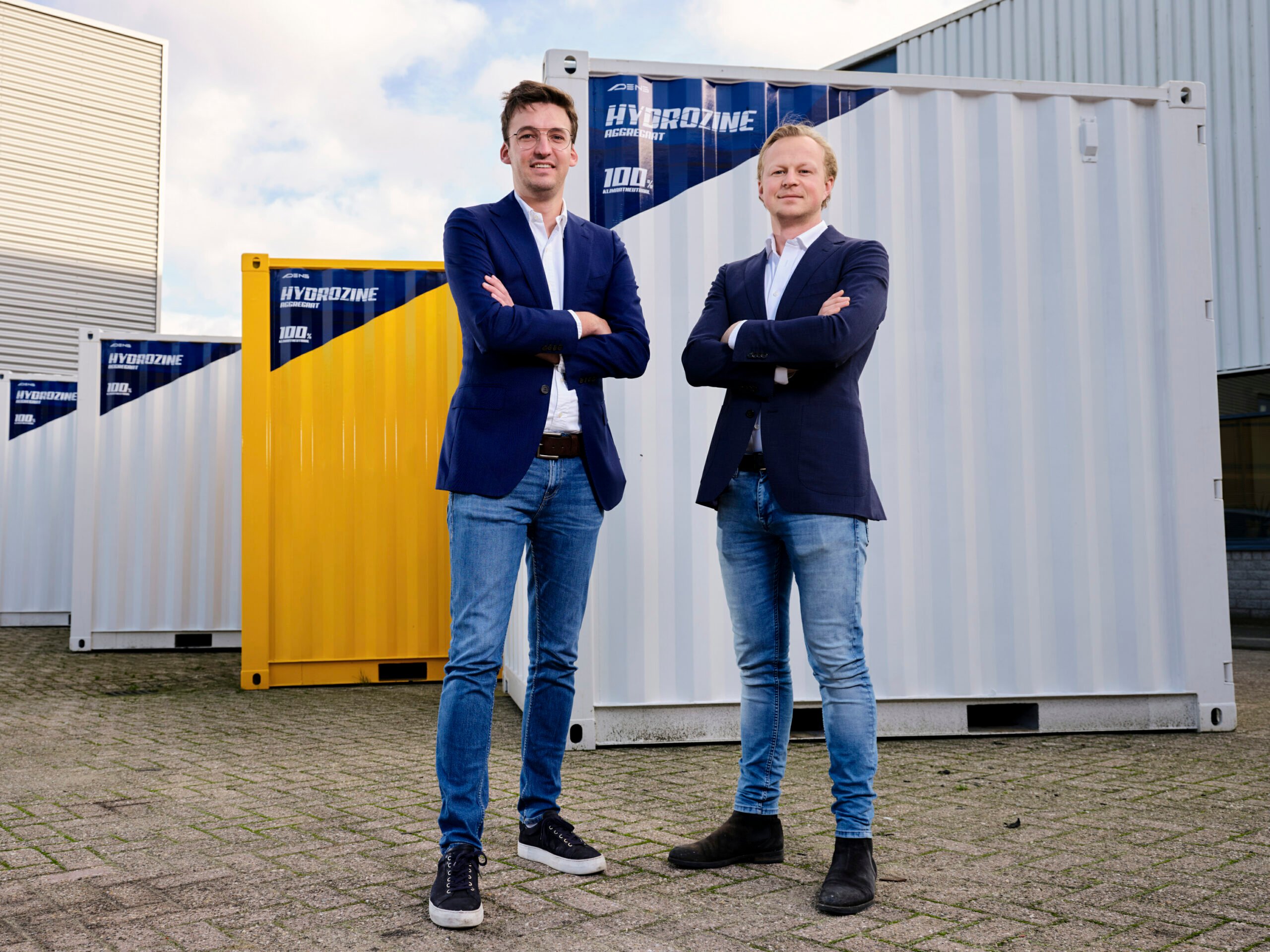
What started as an inspired student project at the Dutch Eindhoven University of Technology (TU/e) is now a fast-growing company. “Looking back, we are quite proud of what we have achieved,” says Max Aerts, CEO of Brabant-based tech company DENS. “Except if you look at where we want to be, we are still dissatisfied. We want to be much further along.”
DENS makes generators that run on formic acid. This makes these generators an alternative to polluting diesel generators used in agriculture, construction and mining, among other fields. In his office at the Automotive Campus Helmond, Aerts talks about how rashly they started as students and how they learned by doing and grew into a production company.
Aerts’ office looks out onto the courtyard where four containers flank the building. They were the first ones sold. The buyers? Real estate, infrastructure, engineering and construction companies Heijmans and TBI who are replacing their diesel generators with DENS generators. They are used to charge the electric vehicles and machines on site. Through rental partners such as F&L Powerrental and FullTank, other companies can also gain experience with the Hydrozine generator.
TU Eindhoven’s start-ups and spin-offs
TU Eindhoven (TU/e) is a breeding ground for new ideas that rely on scientific research. Sometimes these ideas develop into spin-offs and start-ups. This brings scientific research a step closer to society. In collaboration with The Gate and TU/e, Innovation Origins puts the spotlight every month on an innovative company that has emerged from scientific research. This time: DENS.
Inside the container is a tank. In it is about 6000 liters of Hydrozine. “Converted, that’s about 3.5 megawatt hours (MWh) of energy,” Aerts explains. “That’s about enough to power a construction site for a month with average use.”
Investment
There’s a heap of technology incorporated into the system, not just to generate the fuel but also to make it user-friendly. An interface on the side of the container allows the system to be set up and software indicates when a tank needs to be refilled. The owner of FullTank has adapted his tanker truck to carry Hydrozine. Aerts says, “With our information about the contents of the different tanks, he can drive the most efficient route.”
The company is growing rapidly. About 30 people are working on the technology. “Next week, five will be added. And we are still looking for people; we have twelve vacancies.” In addition, five people are involved in purchasing, sales and marketing, among other things. “We hired our first marketing employee last week.”
At the end of last year, the company secured investment from clean-energy conglomerate Koolen Industries and Rabobank. With this, Aerts wants to start real production. If the company grows even more, it will need more space as it is already almost bursting at the seams. It is undergoing a lot of renovation to create more space for future plans. “We now have room, with renovation, to build about 30 units annually, but if we want to go to 100 we really need to move to a bigger building.”
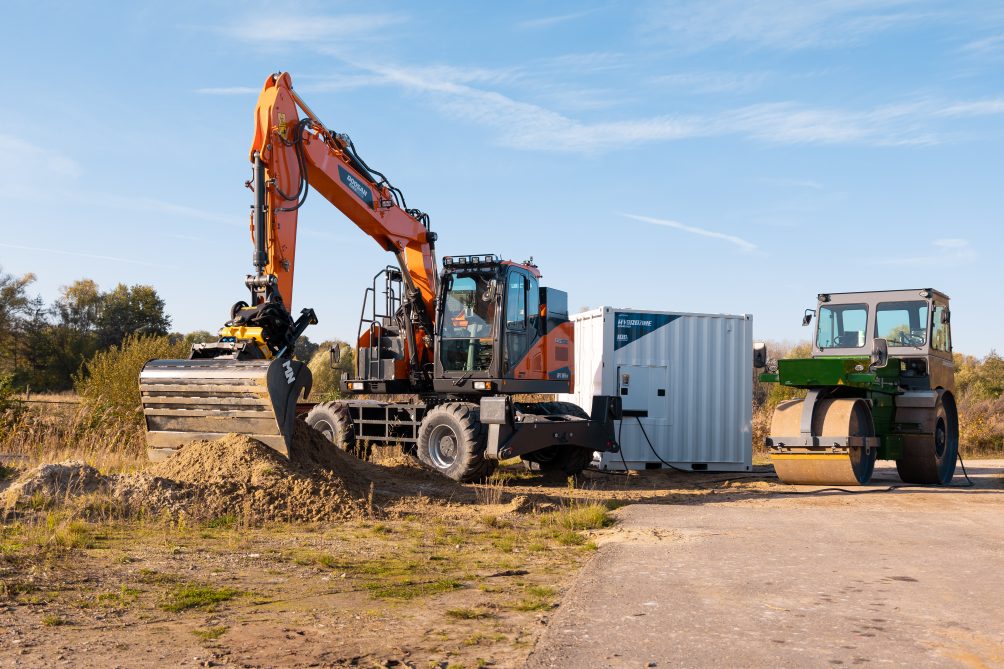
The ASML model
Soon, the non-technical people will move to the main building on the Automotive Campus. Then the building will be purely for construction and development, says Aerts. Because the company wants to continue to develop the prototypes itself, the building also has its own milling machines and lathes. “We develop the prototypes. As soon as they are ready for serial production, we bring in partners for that. We copy the ASML model to a certain extent: we divide the product into modules and place them with partners for assembly. Then we do the final assembly and testing here.”
Aerts would actually have liked to be much further ahead with his company. He would probably approach things differently now than when he started. “But perhaps that open-mindedness with which we started as students was a very good thing. You don’t know yet what limiting factors can be; you don’t see them at all. There don’t seem to be any problems so you just go for it. That is also necessary to be able to take steps.”
Together with four fellow students, Aerts participated in 2015 in TU/e’s Honors program. The team wanted to run a car on formic acid. At the end of the program, a meter-sized model car actually succeeded in doing just that.
Team FAST
During the final presentation in January 2016, the team came into contact with VDL. “They thought we were working on an interesting piece of technology, an easy way to store hydrogen. They asked us whether we wanted to build that in a VDL bus. We answered with a resounding ‘yes.’ Naive as we were, we promised to do it within a year.”
Aerts decided, along with several others, to take a gap year to further develop the technology. “If such a big company as VDL is interested, there must be something to it,” he says. They founded Team FAST. After a year, they planned to return to their studies and a new generation of students would take over. “That was the intention,” says Aerts. But he did not return to the lecture halls after obtaining his bachelor’s degree cum laude. Tijn Swinkels, CTO of DENS, also joined the student team in 2016.
Read more about the student team FAST here
Aerts: “In retrospect, we were very overconfident. We thought we could use all the parts similarly in a moving bus.” That turned out to be a bit of a stretch. “You run into a lot of problems when you go to a scale that is a thousand times larger.” During that time, the students managed to secure funding from the regional development agency, BOM, the Brabants Startup Fund and Rabobank.
Drive
Aerts and Swinkels decided to start a company in 2018: DENS. They wanted to focus mainly on technology and turning driving applications into stationary ones. “That’s technically a little less complicated,” says Swinkels. They made no statements about what would be ready when. “We did learn that: make sure it works and only then go public.” At the time, the nitrogen crisis also “played into the company’s hands to some extent.”
“Then everyone started to go electric like crazy. Electric excavators were popping out of the woodwork. But then you’re in the middle of a field, building something, and then the battery runs out. It’s not easy to find power in a field like that or when you’re building a road or a new housing estate.”
That’s where the DENS system provides a solution. At this moment during the interview, a forklift truck can be seen removing the fuel system from the container. On the face of it, this is a compact system that will soon be used to charge the electric machines of Heijmans, for example. “But it can be even more compact,” Aerts states. “We want to eventually get to the size of an engine block. Our dream is to replace all diesel engines with our engine block. In addition, we will continue to focus on the generators.”
“Our dissatisfaction is our drive to keep going. No matter what we run into, we keep going.”