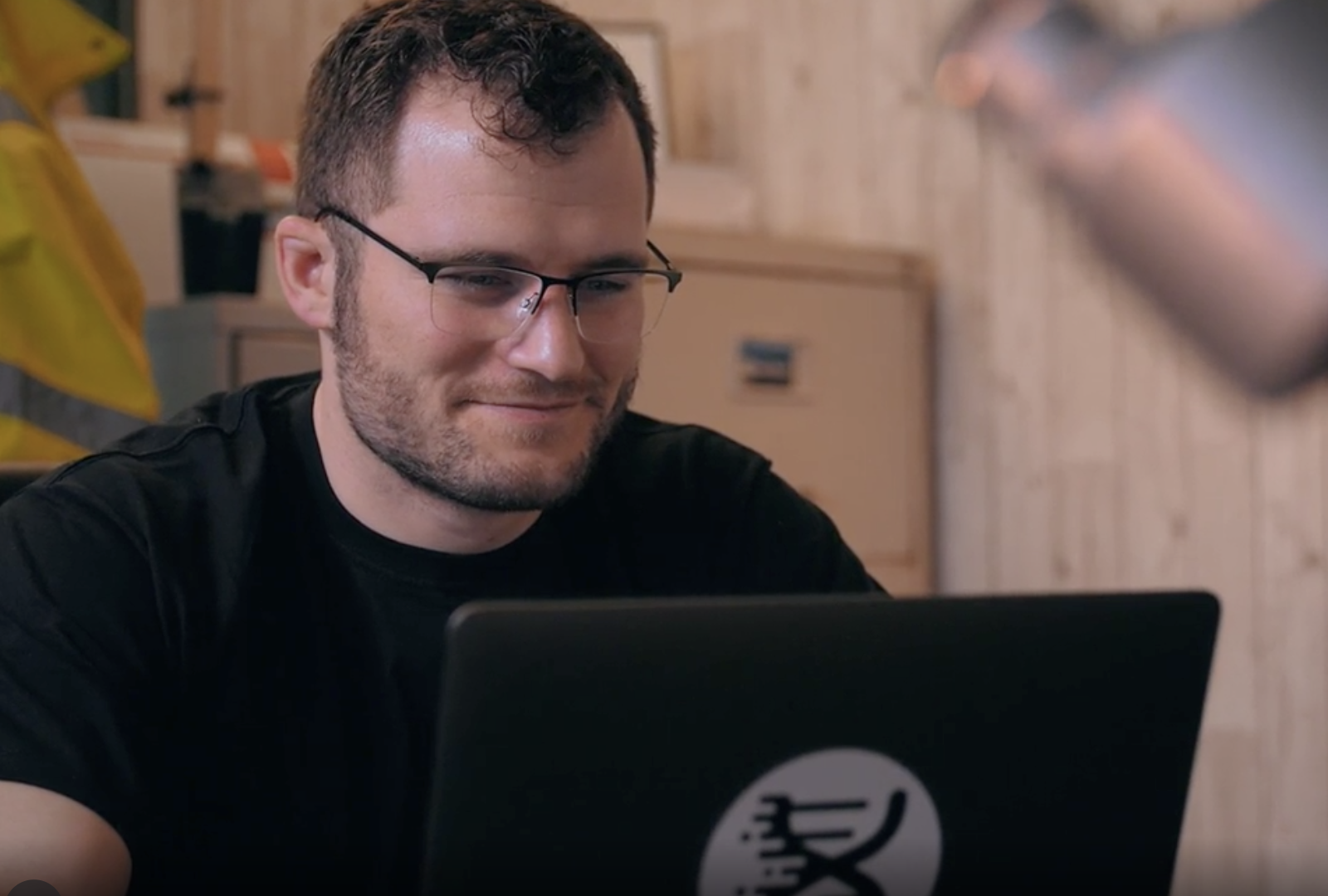
About Deep Branch
- Founders: Peter Rowe, Rob Mansfield, Bart Pander
- Founded in: 2018
- Employees: 18
- Money raised: €2.5 million from the European Union's Horizon 2020 EIC Accelerator program
- Ultimate goal: creating a better way to transform the feed industry, using carbon dioxide
Deep Branch is a biotechnology company focused on carbon recycling. Founded in Nottingham, it is now preparing to build its first plant on the Brightlands Chemelot Campus in Geleen. Deep Branch uses microbes to convert carbon dioxide from industrial emissions into products such as animal feed. The first commercial activities of the start-up are focused on the United Kingdom and the Netherlands.
The British biotech company will build a pilot plant on the campus in Geleen for the production of proteins from CO2 and hydrogen, using micro-organisms. These proteins form the basis for sustainable fish and poultry feed. The construction of the pilot plant involves an investment of over 2.5 million euros, exactly the amount that was received as funding from the European Union’s Horizon 2020 EIC Accelerator program. Deep Branch expects to be able to open the pilot plant in the second quarter of 2021 and subsequently expand the production of proteins at the Chemelot Industrial Park. The additional advantage of this location: an abundance of CO2. CEO and co-founder Peter Rowe explains the background of the choice for Geleen.
What is the idea behind Deep Branch?
“Poultry and farmed fish in Europe are fed with fishmeal and soy, mainly from South America. This is certainly not sustainable because the seas are being emptied of fish and the rainforest is being affected by it. It is bad for biodiversity and the transport of these proteins is also harmful to the environment. We can use CO2, water, hydrogen, and micro-organisms to produce high-quality proteins that are specifically suitable as raw materials for animal feed. Simply, through a process of fermentation. It’s a process that reduces CO2 emissions by more than 90 percent compared to the current sources of protein used.”
Are you focusing on reducing CO2 or making livestock farming sustainable?
“Both. We use CO2 to make animal feed sustainable. The sustainability of livestock farming and wider concerns about reducing CO2 emissions are two of the biggest problems of our time. By 2050, the world’s carbon emissions will have to be zero net to prevent an environmental disaster, but by then, our planet’s population is expected to have increased by a third. As the average consumption of animal products grows, it is thought that livestock production will have to double to meet demand.”
Wouldn’t it be better to reduce meat consumption?
“Of the total emissions per person, about a quarter comes from food and most of these emissions are related to animal products. While we at Deep Branch recognize that the best way to reduce the carbon intensity of food is to reduce meat consumption, we are also pragmatic: we recognize that not everyone sees it this way. We address this problem by developing Proton, our single-cell protein.”
Why did Deep Branch choose the Chemelot Campus?
“We’ve been on a search through the United Kingdom and Europe and have come to the conclusion that we really find everything we need here. This campus with its excellent innovation hub has all the facilities, including infrastructure and permits, a lot of expertise in the field of chemical processes, expert people, and sustainable ambitions. We are happy to join the circular plans for CO2 recycling and sustainable hydrogen use. In January, we will start the construction of the pilot plant with five employees. At least as important is the ability to scale up quickly. The Chemelot Industrial Park has room for a large-scale production facility and sufficient raw materials are available. We can build our own hub here, with our own assets, so there are no constraints by being in someone else’s backyard.”
The technology has been proven in the lab; what do you expect from the pilot plant in Geleen?
“On a smaller scale, we have shown, together with the British energy company Drax, that the technology works. The pilot plant in Geleen is essential for finding the right recipes for ‘Proton’, as our new nutrient has been named. The proteins are used in salmon and chicken feed by BioMar and AB Agri, two European companies for animal feed. Not only is Proton on a large scale much more sustainable than soy and fishmeal, but it also makes a significant contribution to reducing CO2 emissions.”
Are you already thinking of next steps?
“Yes, certainly we are. Proton, our protein-based food ingredient, is just our first product. We have chosen this because of the high market demand. But our technology can be used for many other purposes. That’s why we don’t consider ourselves to be an animal food business, but more as one with very promising platform technology. The question, for now, is what other products we will be able to generate from this platform. Of course, we have our thoughts about that, but before we share them, let’s first try and make Proton a success. Our pilot plant in Geleen is already designed in a flexible way: first, it’s all about protein, but later it may be re-used it for other purposes.”
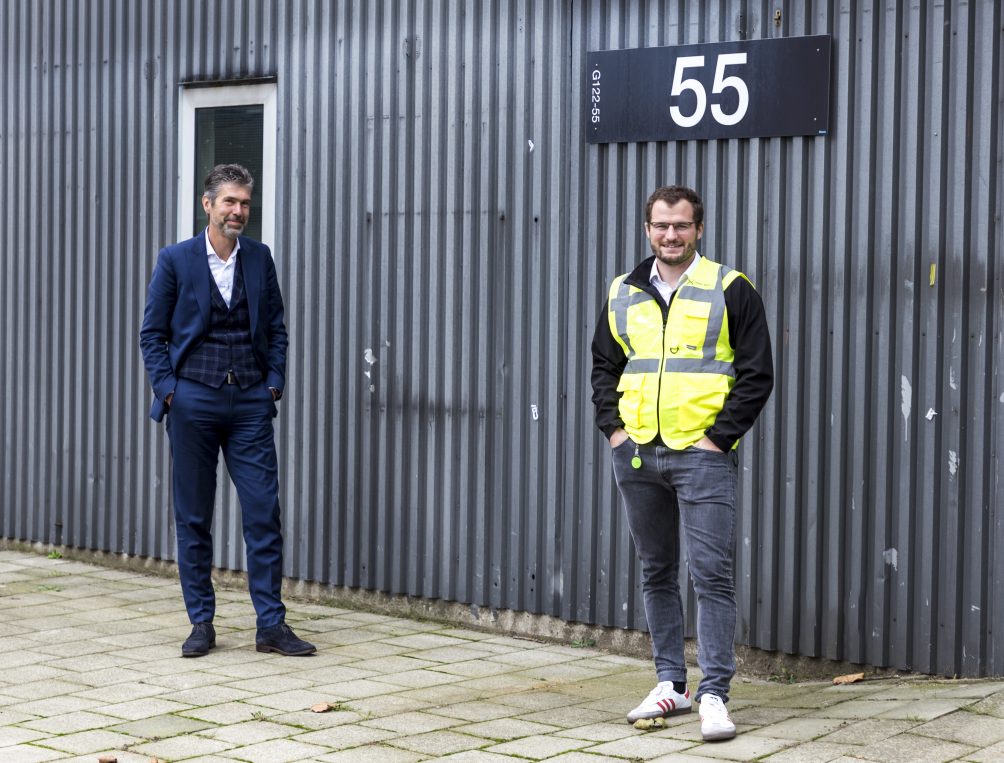