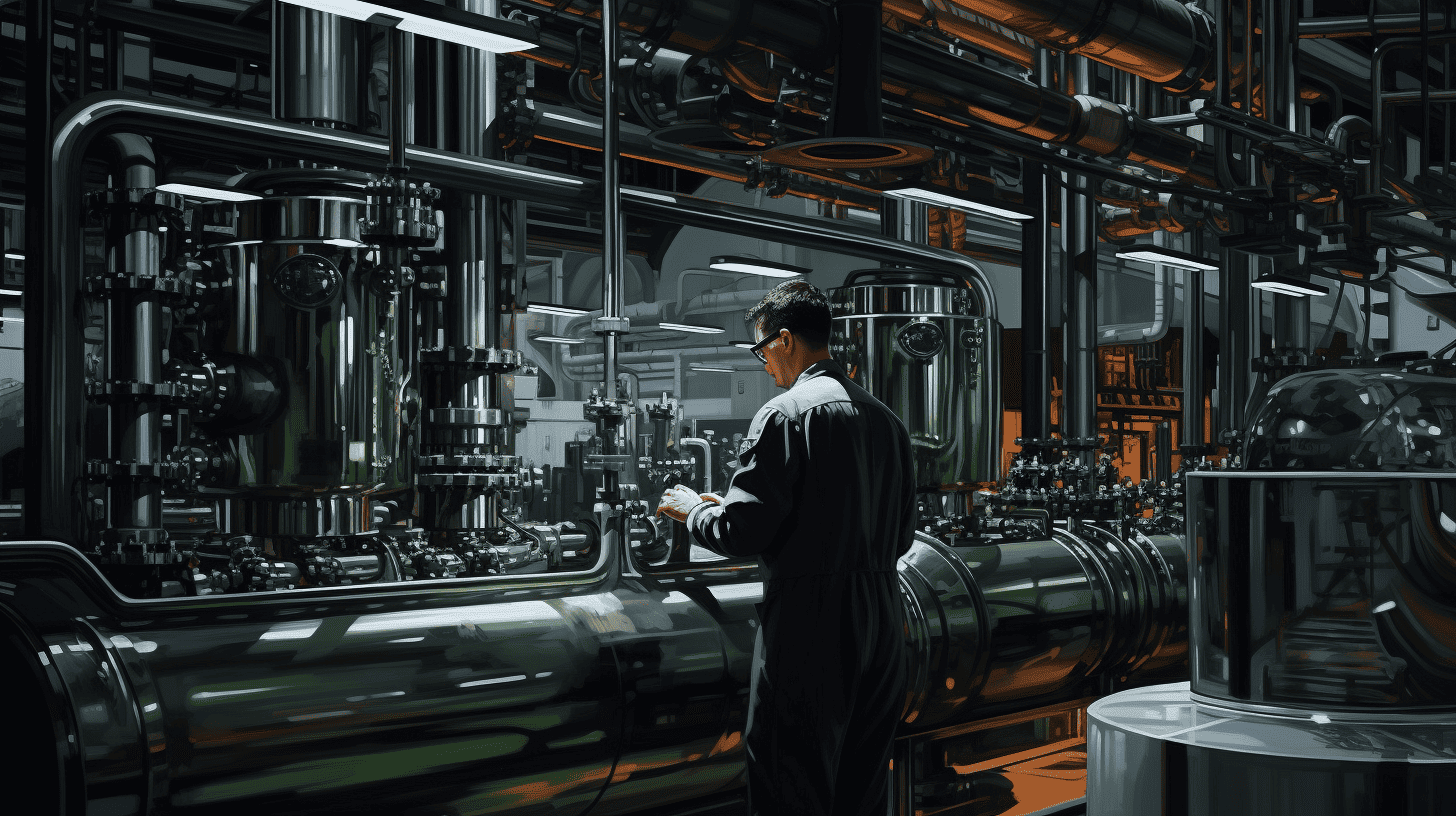
Chips, transistors, and solar panels are all made with silicon. The demand, and thus the production, of this mineral spiked over the past few decades, driven by the increase in the production of solar cells and computing power. Yet, silicon production comes at high environmental costs. Per every kilogram of silicon produced, 7.5 kilograms of CO2 are discharged into the atmosphere.
- Silicon can help us transition to a greener future, but its production is highly polluting.
- In different projects, aluminum and hydrogen reduce the coal used in silicon-making.
- The EU launched its project to improve the resilience of the silicon supply chain.
Nowadays, around eight thousand tons of silicon are produced worldwide. China is by far the world production leader – with approximately six thousand tons. Russia ranks second, with less than ten percent of Chinese supplies – around 580 thousand tons. Norway is the European country producing the most of it.
In the near future, demand for silicon is forecasted to soar further amid the growth of solar power installations and the expansion of computing power driven by AI models. The EU has classified silicon as a critical raw material (CRM) since 2014. Europe’s willingness to decouple from the Asian superpower also applies to silicon, yet the road to self-sufficiency is long – and tortuous. With climate targets looming over, achieving self-sufficiency goals in a green way is the path Europe wants to walk on. Some European projects to decarbonize silicon production exist; how do they plan to reduce the footprint of this industry?
So common, so rare
Although it is the second most common element on the Earth’s crust, pure silicon is hardly ever found in nature. It is primarily found in rocks or sands as silicon dioxide, often combined with oxygen. Quartz – consisting of one silicon atom and two hydrogen ones – is one of the most used rocks for producing pure silicon.
In the traditional smelting process, quartz and carbon are used to get pure silicon. In high-temperature furnaces, the bond between quartz’s silicon atom and the hydrogen ones is dissolved using solid carbon, such as coal or coke. The outputs of this process are pure silicon, carbon monoxide, and carbon dioxide, making silicon production highly pollutant. Norway, Europe’s largest producer of aluminum and silicon, generates ten percent of its emissions from the metal industry. Therefore, new technologies are emerging to decarbonize the process and make green silicon, replacing carbon with green alternatives.
Aluminum scrap to replace coal
The Norwegian University of Science and Technology (NTNU) developed an industrial process that can remove all direct carbon dioxide and nitrogen emissions from the silicon production process. This new method, called SisAl, uses aluminum instead of carbon to break the bonds inside quartz atoms. Thanks to this method, “green silicon production is just around the corner,” told Norwegian SciTech News Maria Wallin, a materials researcher at NTNU.
Whereas the conventional silicon smelting process is endothermic, meaning that it uses energy to reduce the quartz, SisAl is exothermic, as the reaction between quartz and aluminum releases power. “SisAl uses only one-third the energy consumption per tonne of finished silicon,” said Wallin. In addition, SisAl uses nearly all the quartz put in the furnace – the conventional method takes up 85 to 92 percent of it.
Besides, the process can use slag and scrap from the aluminum industry, as well as thin aluminum coming from the food industry. The SisAl process also generates calcium oxide and aluminum oxide as scrap, substances demanded by the steel industry. In a way, the model aims to close the loop and create a circular business model. Wallin also believes that current smelters wouldn’t have to invest large sums of money to complement or replace current production. NTNU got a patent for the SisAl process, and it is building a pilot plant in South Africa to test it further.
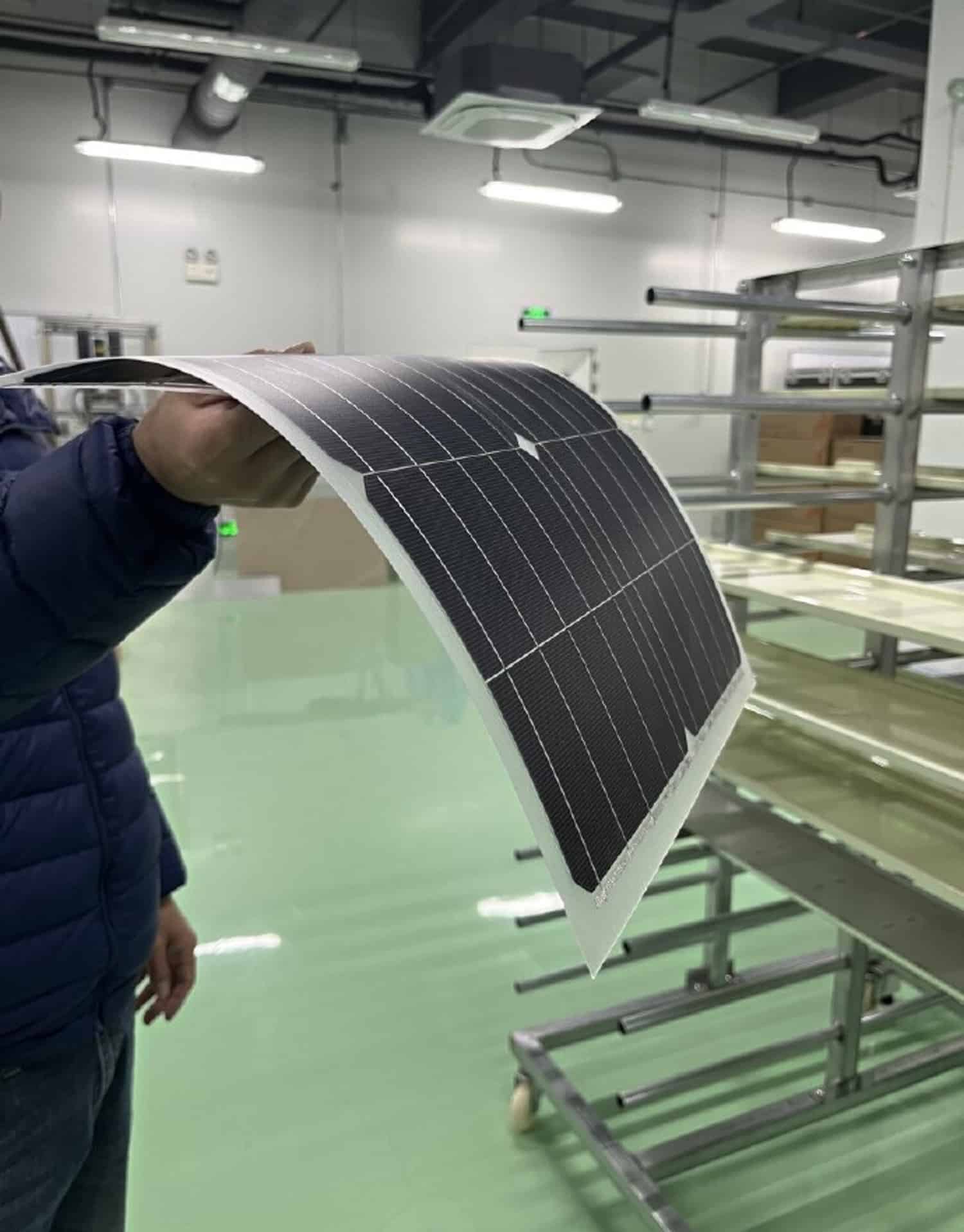
The role of hydrogen
From neighboring Sweden comes another technology. Green14 is building a new reactor to produce green silicon. The facility aims to manufacture silicon in an innovative and environmentally friendly way. The startup’s furnace will use 3000 degrees Celsius hydrogen plasma to convert silicon dioxide into pure silicon. After conducting successful experiments, the company decided to scale up its process, thus building the kiln inside the furnace hall of the KTH Royal Institute of Technology.
Instead of using solid carbon – namely coal or coke – the company plans to employ hydrogen plasma, a state of matter in which hydrogen has been ionized into plasma. Plasma is one of the four fundamental states of matter – the most abundant one – and is characterized by the presence of a portion of charged particles in any combination of ions and electrons. Therefore, hydrogen plasma consists of free electrons and protons that conduct electricity and that can be manipulated by magnetic fields.
The byproduct of the process developed by Green14 is water vapor. Another generated sidestream is silicate, a compound used in electric car batteries. However promising, the process poses relevant challenges, such as safety. “The combination of high temperature and hydrogen gas is always a risk,” said Björn Glaser, project manager at the Swedish startup. The pilot plant will help Green14 refine its technology.

Value chain
In an effort to reduce dependency on external suppliers, the EU launched the RESiLEX project. Part of Horizon Europe – EU’s flagship research fund – the initiative targets to increase the resilience and the sustainability of the entire silicon value chain. Started in mid 2022, RESiLEX covers raw materials extraction and transformation, as well as the optimization and recycling of photovoltaic (PV) modules.
Developing innovative solutions to recover mining wastes is one of the initiatives undertaken by the project, led by Cetaqua – a water research company and one of the members of the consortium comprising 21 European partners. NTNU also joined the program with its aluminum refining initiative. Up until 2026, RESiLEX will have time and funding to dig deeper into the topic.
With different roles, chips, and solar panels will help society transition towards greener standards. As things stand, we are yet to have fully green solar modules and computing units. Still, as research progresses, green silicon might soon be a reality, possibly impacting the geopolitical landscape.