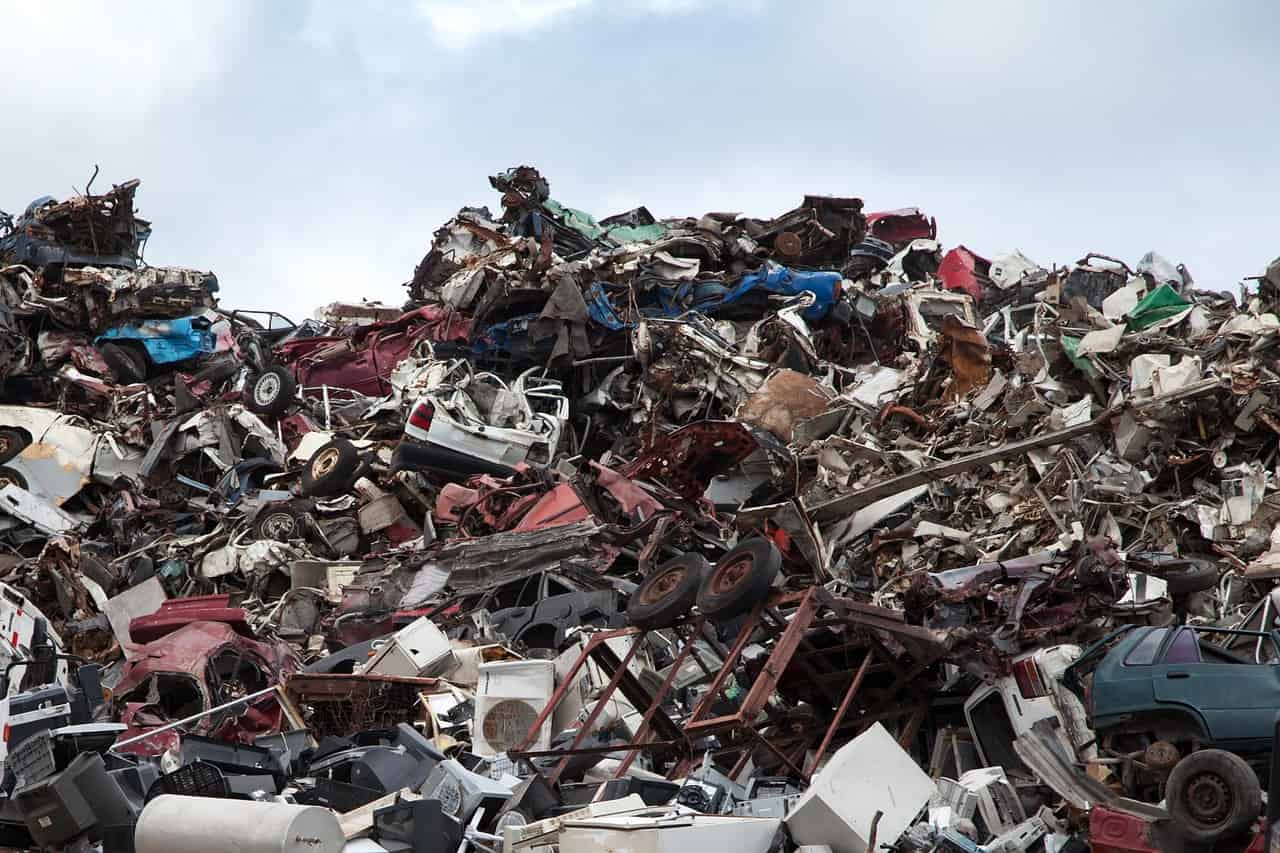
Last week, Tata Steel was all over the news. Activists demonstrated on the plant’s site in Velsen-Noord, demanding greener steel production or the departure of the steel producer. But how do we achieve that?
15 to 33 percent of all steel produced worldwide is lost to corrosion. Steel corrosion costs are estimated at three to four percent of global GDP. Coatings or cathodic protection can reduce corrosion – the deterioration of an object through interaction with its environment. Adding an extra layer of protection to all steel objects would be a simple preservation measure. But it’s more complicated than that. Corrosion – and its prevention – is a complex, electrochemical, and dynamic process.
- Corrosion causes significant economic costs and environmental damage;
- Tata Steel and science are innovating in corrosion protection to make steel more sustainable;
- Alternatives to harmful corrosion inhibitors include: chromium-3, lithium-based inhibitors and machine learning for corrosion prediction and protection.
A star in protecting steel, enemy for man and environment
“Once steel reacts with the humid outside air, an iron (hydr)oxide skin forms. If we do not consider this properly during the production and application, that layer can be full of cracks and defects. Then it offers insufficient protection and cannot prevent the underlying metal from dissolving,” explains Arjan Mol. He is a professor of Corrosion Technology and Electrochemistry at TU Delft.
Chromium-6 (officially: Cr6+) is a star in protecting steel from corrosion. Because six electrons are missing from the two outer shells of the atom, the substance quickly reacts with oxygen, for example. Thus, it forms an anti-corrosion layer when the paint layer is damaged. This “active corrosion inhibitor” is self-healing: when damaged, the chromate dissolves in water, forming a protective layer in the scratch that keeps the underlying metal from corroding. But, the material is environmentally polluting and carcinogenic. According to EU legislation, it should only be used when there is no reasonable alternative and under strict conditions, such as in the inside of airplanes.
Sustainable steel
Our society is built on steel. We make bicycle bridges, pipelines, and cars from it. In 2021, 1.9 billion tons of steel were produced worldwide – an all-time high in global steel production—or the low point because every ton of new steel produced is associated with 1.9 tons of CO2 emissions. At seven percent of global CO2 emissions, it is one of the industries with the most significant carbon dioxide emissions.
Yet we need it because there is no alternative to steel. So there is only one thing to do: make the life cycle of steel greener. In this series, we look at how scientists from TU Delft and industry are making the life cycle of steel – from production to processing, application, and recycling – more sustainable. Today: the role of corrosion technology in making steel more sustainable.
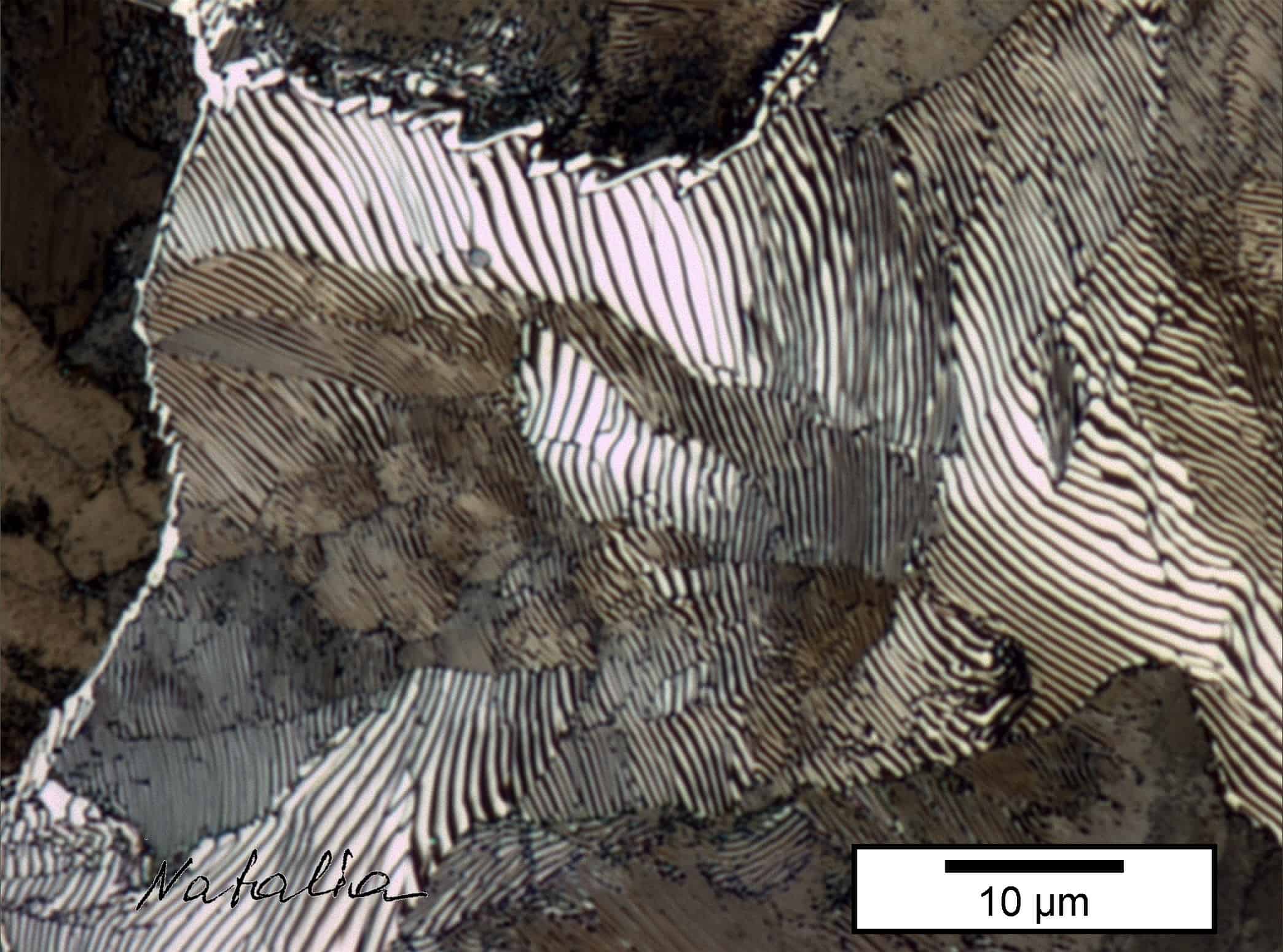
Harmless little brother
So what alternatives are there? Its non-hazardous sibling, chromium-3, is used to produce cans. For a long time, the use of chromium-3 was considered impossible; the protective layer is not as strong. “We have now succeeded; chromium-3 is used as a protective layer in packaging materials, such as cans of drinks,” says Hans van der Weijde, program director of Tata Steel R&D.
The steelmaker was the first in the world to develop a method by which a very simple electrolyte can be used to make a thin chromium coating from a chromium-3 solution. “That’s nice on a small scale in a laboratory, but it’s a different story for a production line of three hundred meters per minute. We want to create a layer about a hundred nanometers thick with the structure of metal oxide. A big challenge, but a very nice one.”
Other elements may also offer a solution. For example, lithium-based corrosion inhibitors are also undoubtedly the subject of industrial-academic research. After the limited dissolution of the metal, this chemistry ensures the formation of a dense, well-protective oxide layer. In this way, Mol turns the enemy (corrosion) into a friend based on the deposition mechanism. “If you take microstructure and chemicals into account, instead of a loose layer, you can create a robust layer. That way, we make corrosion work for us instead of against us.”
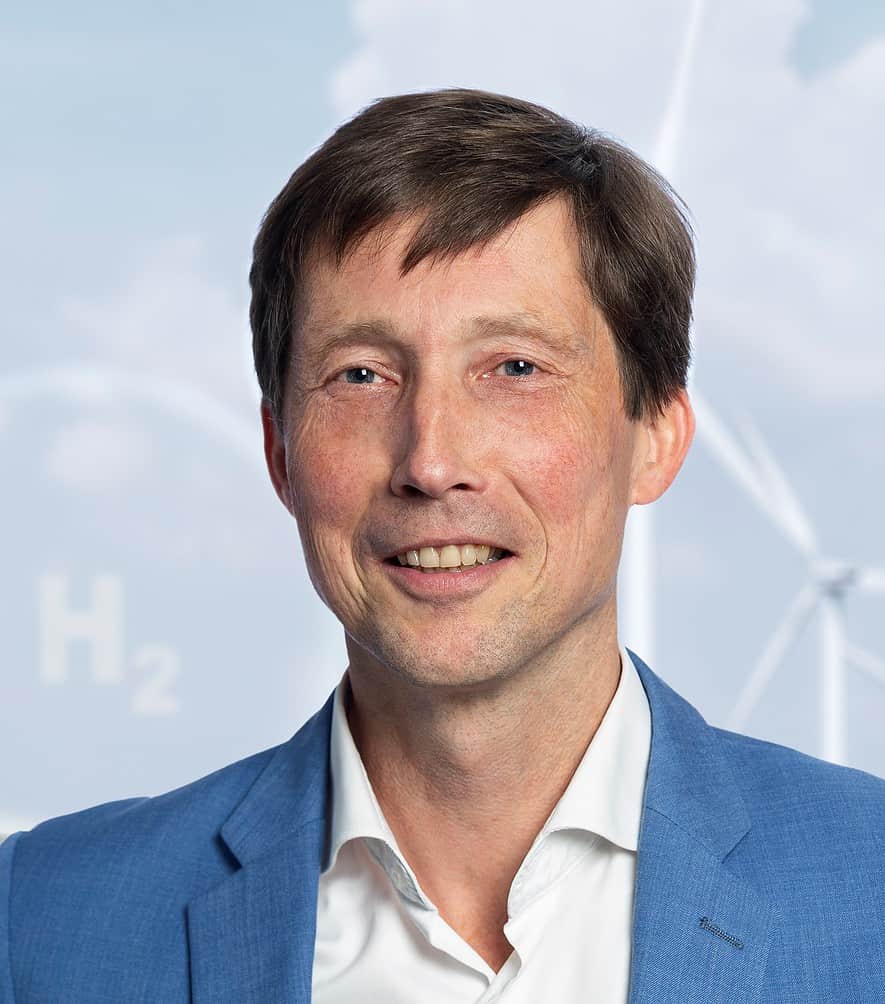
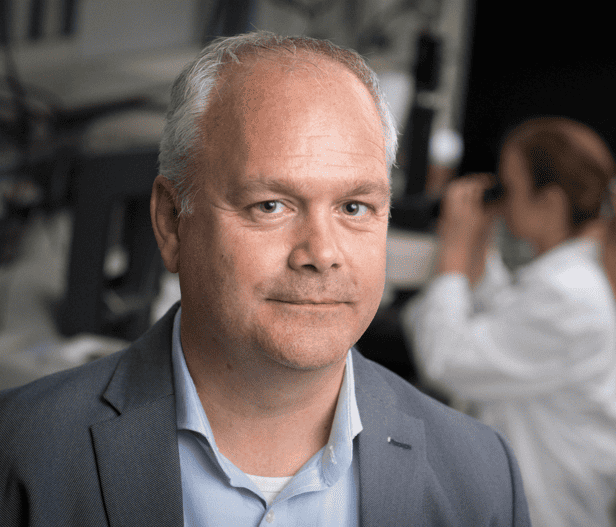
This application has now only been investigated on aluminum alloys for civil aviation. The trouble is that – before the industry has built up experience with practical applications – scientists need help predicting how long such a layer will provide sufficient protection. Mol: “Making predictions is complex, mainly due to the unpredictability of environmental conditions to which objects are exposed. We can link accelerated laboratory testing methods to actual lifetimes, but mechanisms and rates of underlying degradation processes in a laboratory can typically differ from those in practice.”
Lighter structures
According to Van der Weijde, the industry can still take a big sustainability step by making structures lighter. “When I started at Tata Steel, a beverage can still weigh 35 grams; now it’s 20 grams. This trend applies not only to the packaging world but also to the automotive and construction industries. We have eighty to one hundred Ph.D. students working at universities. All that scientific knowledge provides technological development. We work with ever-thinner and, therefore, lighter materials and smarter coatings, which allows us to produce ever more durable, thinner, and lighter steel. You also don’t have to recycle the material you don’t use.”
Machine learning
As Mol looks to the future, he expects a lot from machine learning. “Even if we were to search day and night with thousands of researchers, the options of different combinations of chemicals that could serve as chromium-6 replacement corrosion inhibitors are endless. Using machine learning, we can test how efficient a set of chemicals is in terms of corrosion inhibition, thus identifying promising other chemicals and predicting their effectiveness. We are doing research on this with several partners in a European context. That is now focused on aluminum and aerospace, but we can roll out this approach broadly toward other metal types.”
Machine learning is also going to play a big role in lifetime prediction – a holy grail in corrosion research – of steel, Mol expects. Using machine learning, scientists will shortly be able to predict the condition of a steel bridge or sheet piling in five or ten years, considering different environmental conditions scenarios. One example is the SUBLIME project, where researchers are looking at digital twins of steel objects. “Combined with theoretical modeling, monitoring, censoring, and experiments, this provides a much more realistic prediction,” according to the professor.
Arming ourselves against corrosion is becoming increasingly challenging because of the areas of application.
Arjan Mol
Increasingly challenging application areas
Mol and Van der Weijde’s field of work is getting more challenging. Mol: “Our armoring against corrosion is becoming increasingly challenging because of the areas of application. The energy transition is an excellent example of this. Take the increasing demand for offshore wind energy. The conditions for wind turbines – salt, wind, water – are very corrosive. So are all kinds of electrolysis processes, such as hydrogen production or carbon dioxide conversion, which are essential to the energy transition. Those processes work catalytically very well in relatively aggressive operational conditions, but those same processes also have a lot of effect on the degradation of materials. “
Mol is on a mission: to make his students, whether they end up in research or industry (right they), aware that investments and choices that prevent corrosion may seem more expensive up front but pay off in the end. “Every kilogram of steel produces 1.9 kilograms of CO2 emissions. Let’s make better decisions during the design phase to prevent premature or abundant corrosion in the application. We will earn that back twice over the lifetime of products and structures economically and in terms of ecological impact on our society. The better the steel quality and protective measures, the lighter we can construct in many cases. This way, we reduce costs at the design stage and make transportation applications cheaper and energy costs lower. The industry has to look at the whole lifetime of an application. It’s an integral responsibility of everything and everyone to take better care of our planet.”