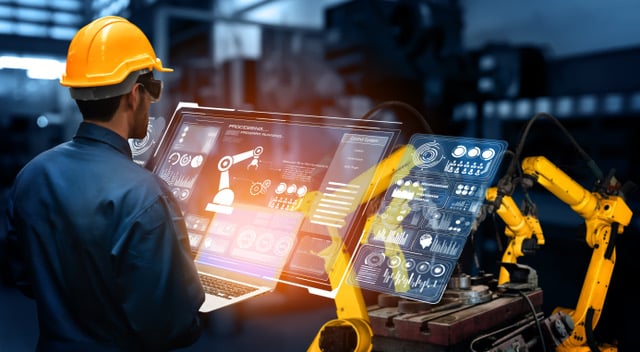
Digitalization has a crucial role to play in order to achieve the transition to a fully circular manufacturing industry by 2050. For this purpose, the Netherlands Organisation for Applied Scientific Research (TNO) has developed a step-by-step plan for companies.
Global warming, energy transition and scarcity of raw materials: A whole tsunami of challenges is looming over companies. “There are a lot of things to be done leading up to 2050. This can be quite overwhelming for entrepreneurs,” says Christa Hooijer, Science Director TNO in the Industry Unit.
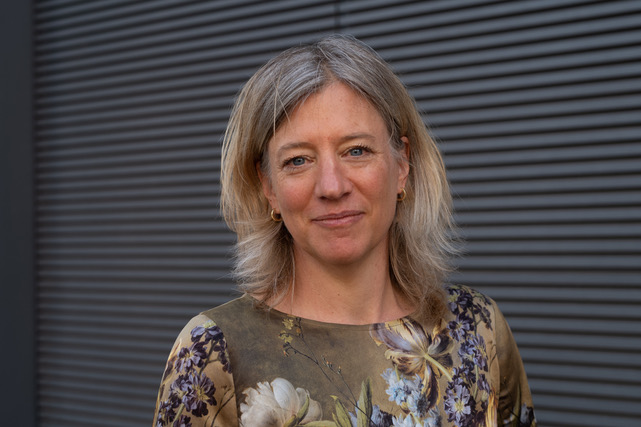
“We have seen in recent months how vulnerable we are as a society. In that sense, the pandemic was also a wake-up call. We have noticed how dependent we are on each other, but how connected we all are as well. This also applies to the manufacturing industry. If a component breaks down somewhere in the chain, the entire production process comes to a standstill. I personally spent months waiting for a washing machine because certain parts could not be delivered due to the pandemic.”
Flexible production
However, this also shows the value of flexible production. Whereby things are better coordinated, and you are more aware of what is going on in the production chain. What you are receiving, what equipment is being used and what the situation is concerning raw materials. In the future, more and more will be manufactured on demand, in small factories and close to the consumer.
Digitalization is imperative to ensure that the supply chain is not interrupted. So, that invariably involves the whole chain. Make sure that others understand you, and prevent production from getting bogged down. This is why in the field labs at TNO we are carrying out tests that use robots at companies, looking at how they can deal with unexpected situations. Robots can take on different tasks, such as retrieving digital data but also communicating with a human operator.
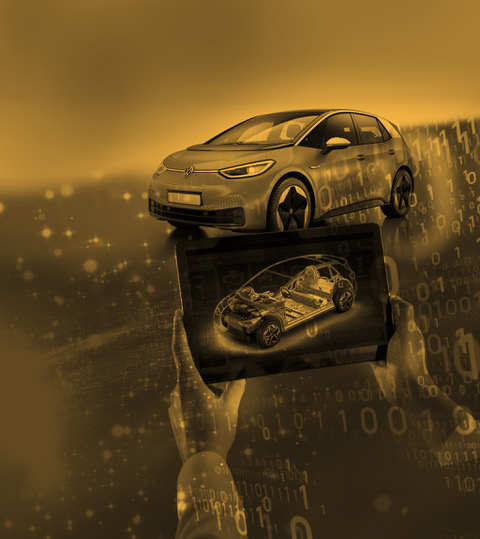
Service economy
As far as raw materials are concerned, it is also a question of: gone is gone. Whole appliances, be they coffee machines or cars that are no longer used, tend to end up on the scrapheap. In the future, you will no longer need to own a coffee machine, it will be about being able to make coffee, and a company will take your machine back when it is worn out. In the meantime, broken parts, monitored by sensors, are replaced. This also applies to other industries, such as the automotive industry, where all of the parts can be replaced again until the vehicle is completely used up.
The idea is that by 2050, everything will be manufactured in a circular way and there will be no new raw materials in the chain. They will be extracted and reused. At present, a lot still ends up in landfills and incinerators.
The intention is to optimize this as much as possible by bringing all raw materials back into the chain. However, this is still something for the future. But if we want to make sure that we do not send the earth to its doom, then we will all have to take these steps.
Step-by-step plan
This also applies to the manufacturing industry. There is a great deal that has to happen and it can sometimes be dispiriting. But what we want to emphasize is: you don’t have to do it all at once, take it one step at a time. We tell companies: you don’t have to take on all the problems of the world. But get moving and make a start!
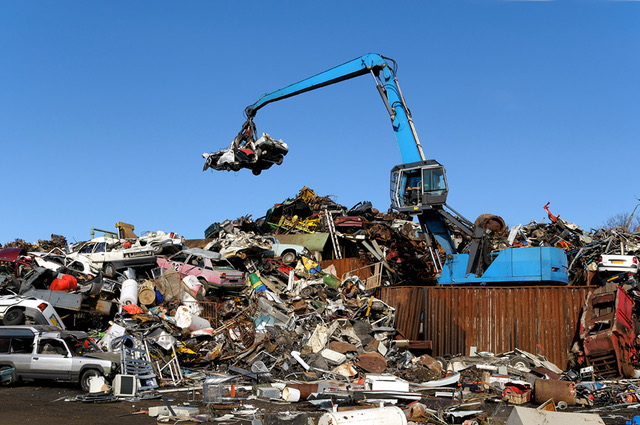
We offer a step by step plan with our white paper Digitalization crucial for circular industry. With this, companies can move towards a more flexible business model, and gain better insight into their suppliers’ materials supply with the help of digitization and data sharing.
Optimistic
I grew up in the 1980s, when we were very concerned about the ozone layer due to acid rain. But by taking the right measures, we managed to keep it in check. I am not saying that with regard to global warming that we can turn the tide. But the sense of urgency is constantly increasing. And I think that by making industry as green as possible, we can at least limit the damage.
For instance, what alternatives can we come up with for the dirty way that we manufacture? That is also what we are researching at TNO. How can we make our industrial processes better, cleaner, safer and cheaper?
Also read via this link other IO articles about the support TNO offers.