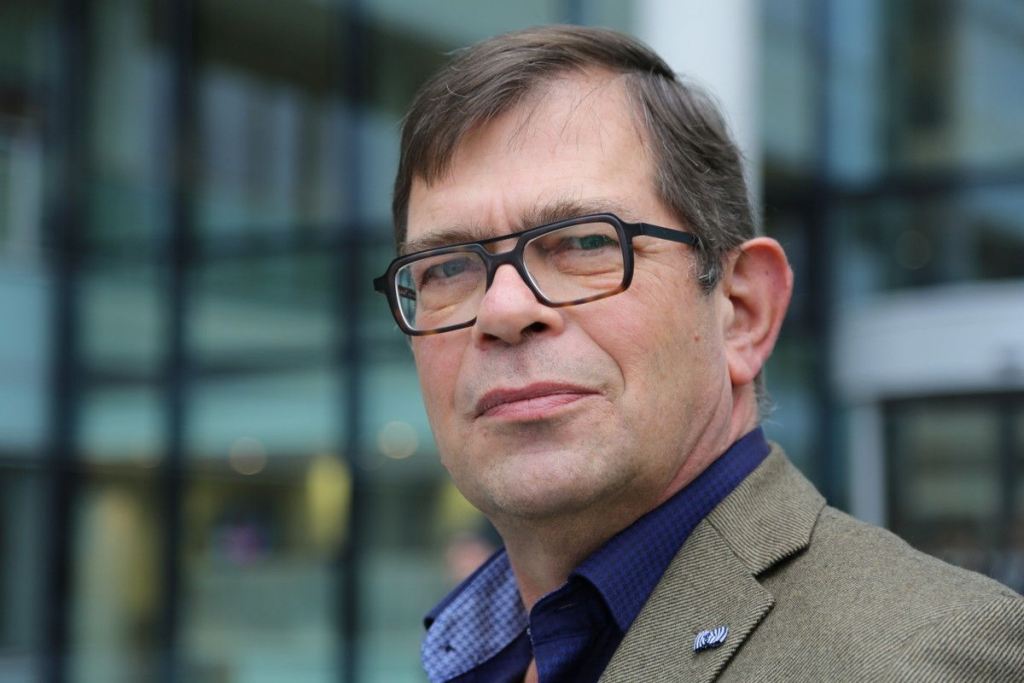
In conversation with Ben van der Zon, Program Manager for International Technology Projects, HighTechNL based on the High Tech Campus Eindhoven. He spoke with Jonathan Marks of PhotonDelta.
“The kind of work we do today at HighTechNL is very different to when we started. We have made a complete ‘pivot’. Until around 3 years ago, the Netherlands Ministry of Economic Affairs offered many national subsidy programmes for Dutch enterprises. They established several sector-specific organisations to manage those funds. For the high-tech industry sector, they had an organisation call Point One, which released calls for projects, evaluated incoming proposals together with external experts, granted proposals and then managed the flow of money.
Point One attracted a lot of interest from large enterprises like Philips, Océ, VDL and ASML as well as SME’s. Gradually, this cluster around the Ministry of Economic Affairs became an industry association. This continued until the Ministry of Economic Affairs ended the national subsidies programme, and only participated in European project funds like Horizon2020.
Understanding Changing Industry Needs
The ending of the subsidy brought about a reorganisation within HighTechNL because its primary reason for existence had gone. But after consulting our 150 members, we discovered there were other sets of needs arising. In 2018, we are now focussed on helping the small medium sized businesses which make up more than 80% of the Dutch (and also European) companies in high tech. Large enterprises have already found their way to funds like Horizon 2020 and in finding innovation partners. They have internal departments working on it. But smaller companies need help in finding partners to apply for cross-border subsidies between the many European regions. And things may change again once the successor to Horizon 2020 is announced.
We have a lot of expertise amongst our partner network. That includes micro-nano electronics in the broadest sense – such as photonics, smart applications and equipment for the production of semiconductors. And the other sector of growth is robotics, where there is a cluster of 300 companies being involved in robotics. We observed that, until recently, much of the robotics development was university led, with often the result that they develop breakthrough technologies for which there is a poor product-market fit. So, we’re turning it around – defining the robotic needs of specific high-tech industries and then reaching out to research organisations to find partners interested in accepting a commission. There are several regional initiatives in various stages of development, but they need to collaborate more closely if they are to scale globally. Although there are much larger Technical Universities in neighbouring countries, the level of expertise in The Netherlands in optics/photonics and precision engineering is acknowledged as world class. But we need to develop more relevant courses that prepare sciences students for a career in Industry 4.0.
Three Main Activities
Today we are a team of 8 people working in Eindhoven, Enschede and Delft focussing on three core activities.
The first is building more human capital. There are many more jobs than available engineers in our high-tech regions. In November 2017, for instance, ASML reported 500 unfilled vacancies. This explains why there is a growing market in technical recruitment companies reaching out to countries like India. That is one route. But we believe we can do more to tap in to the existing wealth of knowledge and experience that you find all over the Netherlands. Initiatives like TalentBox give young professionals an excellent overview of job openings and work experience positions in the Brainport Region. There is a similar successful scheme run by the Materials Innovation Institute in Delft.
Companies have approached us saying that a significant percentage of their workforce will be retiring with 5 years. We are helping them find ways to tap into this huge source of expertise and make sure there is active knowledge transfer. We organise in-company sessions during which we involve people from other companies with domain-sector knowledge. And that has led to several successful outcomes. We are also helping to set up young professional’s work-experience tracks. We make it possible for both alpha- and beta- students to meet and exchange experiences. And we organise study-trips to surrounding countries to help young entrepreneurs discover new markets and partners.
We see that larger enterprises benefit from the innovative, disruptive thinking brought in by these young professionals. That is more difficult for the smaller companies with tighter workforce budgets. But they often benefit from events we organise in which they learn about new best practices from each other.
Trusted Subcontractors
The second role we play is helping small and medium-large enterprise build trusted networks of supply chain companies. With the exponential growth of some technologies, product life cycles are getting shorter and shorter. Companies like ASML and Philips increasingly want to focus on developing their core competencies to keep them ahead of the global competition. They are making more use supply chain companies to solve specific operational challenges. For instance, the large enterprise specifies a problem they are trying to solve with a particular machine. They farm out the solution to trusted partners who have a proven core competence in high-tech engineering solutions. The same holds of course for the small and medium-sized companies. That demands excellent communications between both parties for the success of such technically-complex precision projects.
We see that if you operate in an open collaborative system, then you get access to all kinds of triggers from outside which helps you maintain innovation levels and speed up “time to market” for new products and services. On recent fact-finding missions, we have seen several examples of large high-tech enterprises in Asia who are still very vertically organised, trying to do everything themselves in the way Philips operated 50 years ago. They are trapped in their own manufacturing legacy and find it extremely difficult to innovate from within. But clearly, they are aware of the problem, which explains why Asian companies have been reaching out to companies in the Eindhoven/Enschede area.
In addition to an understanding of human resources, we have a lot of specific domain knowledge, either amongst ourselves or we know where to find it within the membership. That sets us apart from some of the more general innovation bureaus who may understand the process but have little feeling for the technical challenges these SME’s are facing. In the end, smart match-making can be crucial to a small company’s prosperity.
Reaching Out to build Alliances
And our third area of expertise is getting our high-tech ecosystems integrated into other European ecosystems. We were one of the co-founders of an alliance called Silicon Europe in which 12 different European cluster organisations working with innovative electronics & software technologies work together to improve this continent’s competitive edge.
Our ambition is that HighTechNL is one of the main engines that fosters collaboration both at home and abroad. And we would like to play a role in increasing the initiatives in making the public more aware of the opportunities in the beta sciences. Our workforce is changing. Robots are replacing a lot of unskilled, boring and dangerous jobs. But at the same time, there are going to be a lot more opportunities for the highly skilled.”
“Our workforce is changing. Robots are replacing a lot of unskilled, boring and dangerous jobs. But at the same time, there are going to be a lot more opportunities for the highly skilled.”Ben van der Zon,