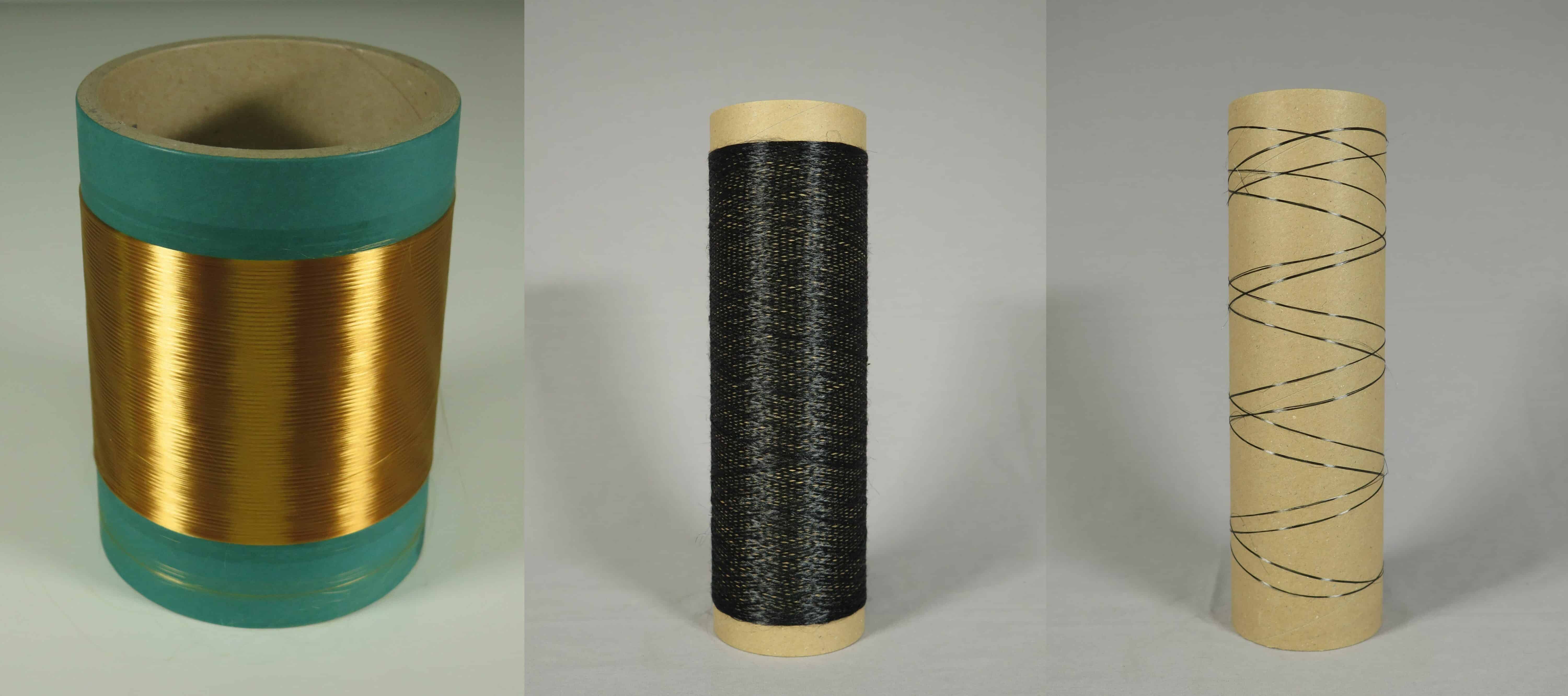
Carbon fiber production is not only costly but also causes a considerable wastage of energy. Researchers at Deutsche Institute für Textil- und Faserforschung (DITF) have developed an innovative production method that uses lignin, a renewable raw material to manufacture carbon fiber. This production technique offers the same quality of carbon fiber while cutting down on cost and energy consumption.
DITF has been successful in the production of carbon from lignin, an organic polymer found abundantly on this planet. Since the production technique does not require the use of any solvent and is made from a renewable raw material, the process is sustainable and cost-saving, said the institute in a press release.
New raw material replaces established process
The carbon fiber production method adopted by industries includes stabilising and carbonising the fiber in high-temperature furnaces for extended periods. As a result, the production cost is high. Also, the removal of toxic by-products during the manufacturing process leads to the wastage of energy and money.
To save energy in the production process, DITF has replaced polyacrylonitrile (PAN), a polymer used by industries in carbon fiber production, with lignin. The process includes a two-step process, where the raw material is firstly converted into a precursor fiber and then into the required carbon fiber. Lignin, which is available in large quantities and is a waste product in paper production, has been mostly overlooked by industry experts during carbon fiber manufacturing.
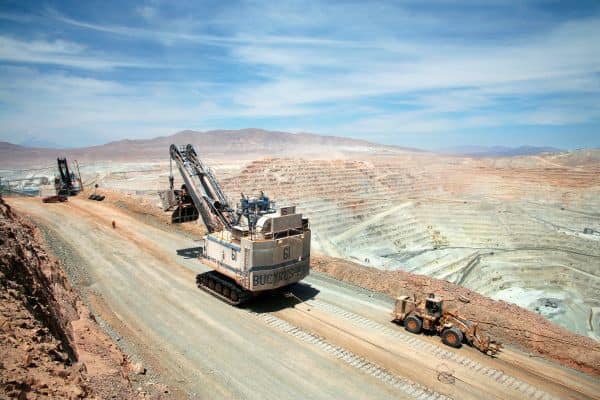
Advanced method of production
Lignin fiber production involves the separation of wood into basic organic components, lignin, and cellulose. What follows is a sulfite digestion process that yields lignosulfonate. Since the production of lignin fiber is based on an aqueous solution of lignin, the lignosulfonate is dissolved in water. The production of lignin fiber from this aqueous solution ensures that no solvent or toxic additives are used in the process.
Substantial technical advantages
Since stabilisation of lignin fiber requires relatively low temperatures compared to PAN fiber, the energy savings shoot up to fifty per cent and provides a competitive edge.
Also, the dry spinning process offers faster speed, which results in higher production of material in a shorter time when compared to PAN fibers. Thus the faster production of carbon fiber proves beneficial without compromising the quality of the lignin precursor fiber.
The use of lignin in carbon fibre production provides overall cost efficiency and improved sustainability over PAN. Hence, the construction and automotive sectors aiming for cost reduction in their production process stand to benefit from this new technique of carbon fiber manufacturing. Not only will these industrial sectors benefit from an economic perspective but also create a sustainable environment.
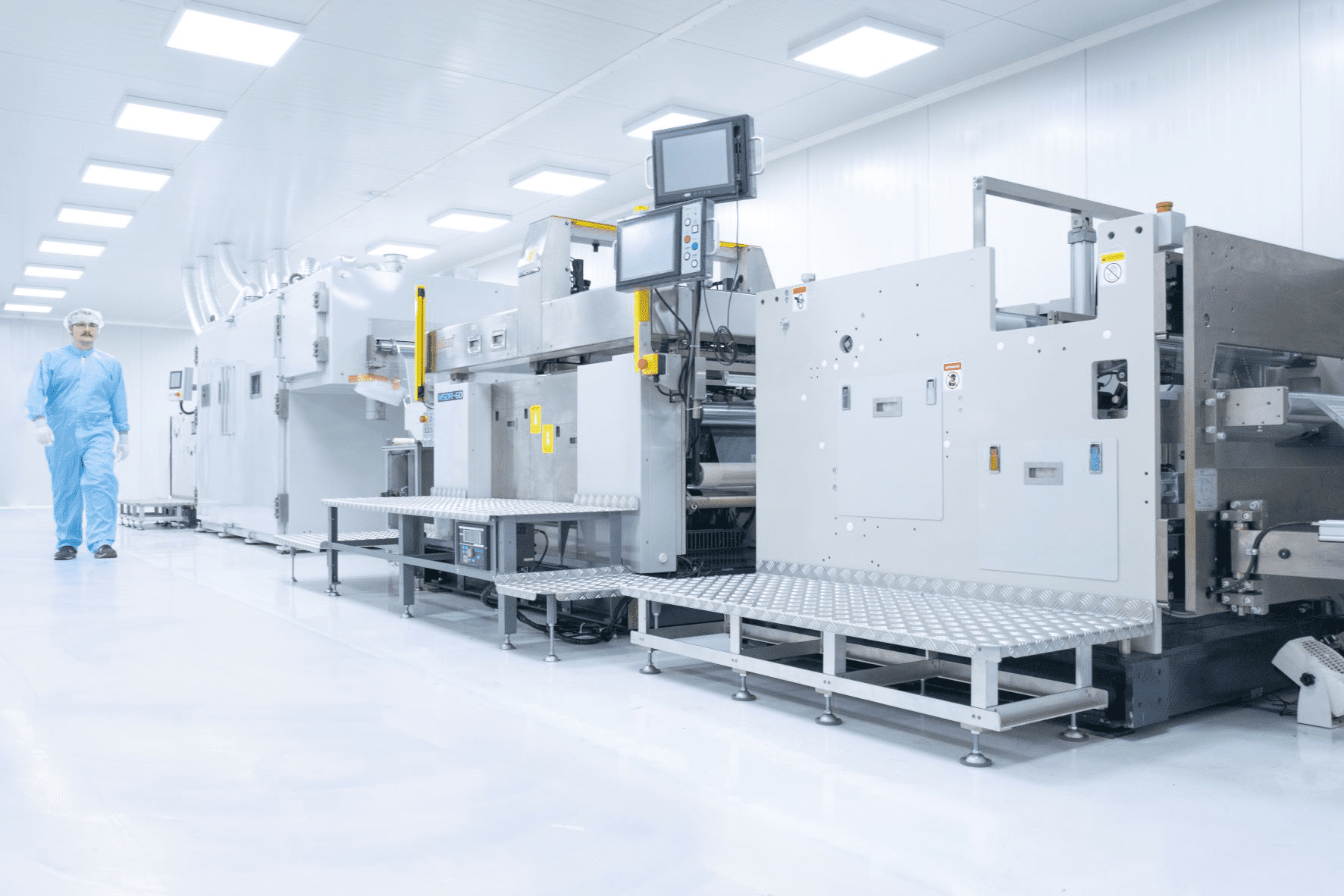