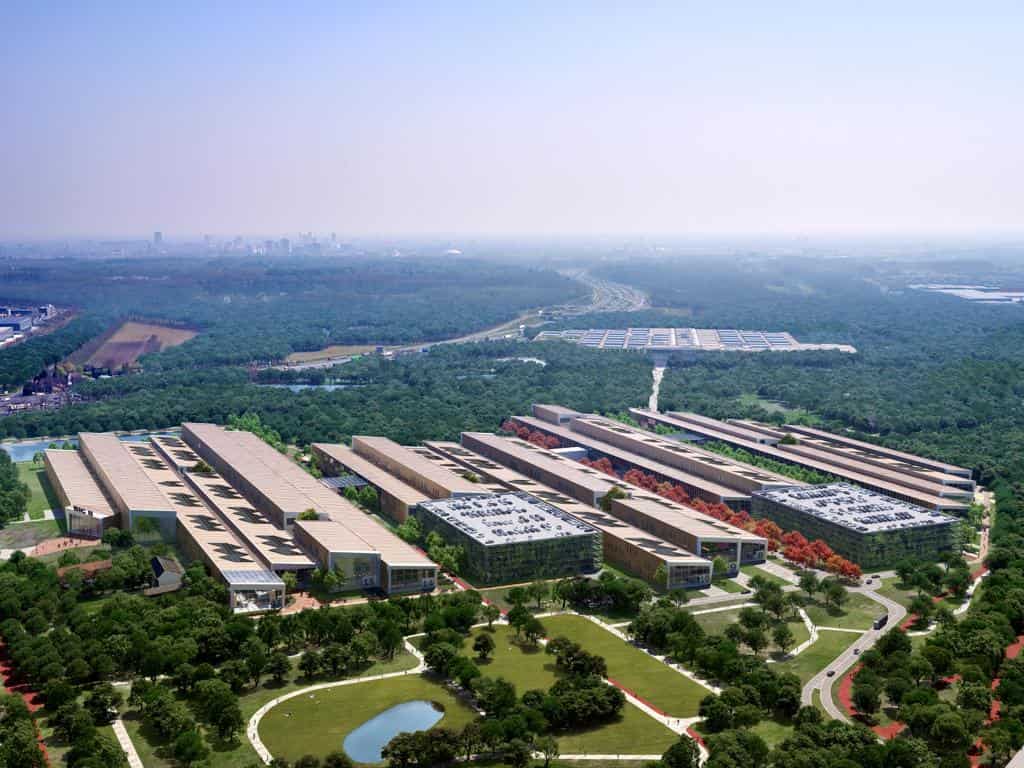
According to the initiators, it is about nothing less than the further development of the manufacturing industry in the Netherlands and thus “securing our prosperity, our autonomy and the living environment for generations to come”. Brainport Industries Campus 1 already makes a major contribution to this. Still, the picture is only genuinely complete with an expansion to complexes 2, 3, 4, and 5 – a plan that spans decades and will eventually cover more than a million square meters. The primary agreement for BIC2 was signed last year, and the preliminary zoning plan will be added this week.
In cooperation with SDK Vastgoed and the Municipality of Eindhoven, Barcode Architects & Van Aken designed the second BIC building as a 17-hectare “factory of the future”: a place with shared facilities where many different companies within the high-tech manufacturing industry can come together and learn from each other, and “where an innovative work environment goes hand in hand with exercise and nature”.
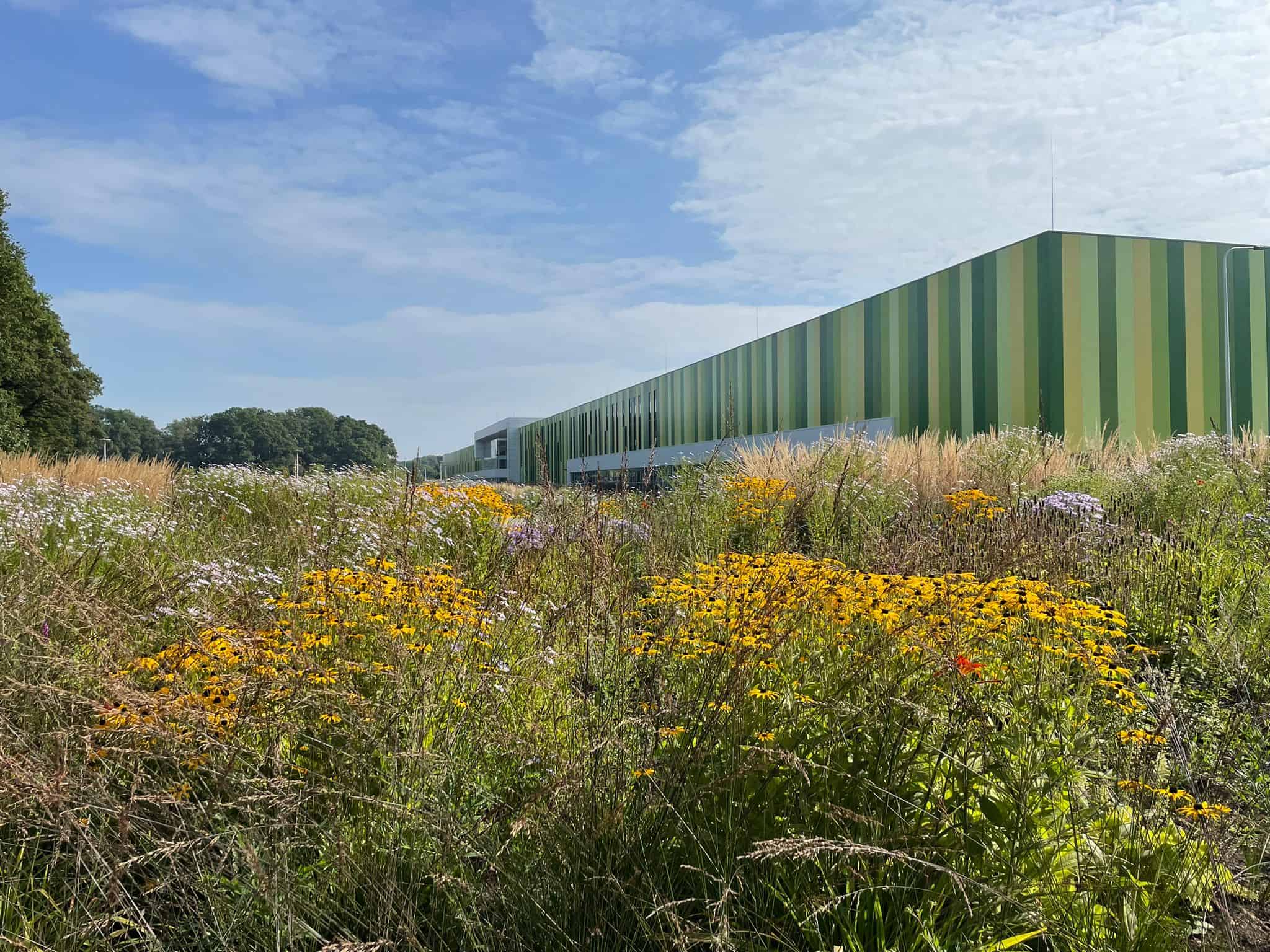
BIC1 currently houses about fifty companies and educational institutions employing altogether about three thousand people and is thus virtually sold out. BIC2, which will be built in three phases starting in 2025, will eventually be twice the size of BIC1: 225,000 square meters versus 100,000. And with BIC2, the ambition is not yet finished: the rough sketches for complexes 3 through 5 are already ready. This is necessary too, say responsible alderman Stijn Steenbakkers (economy) and SDK Vastgoed director Ferdinand Gremmen. The municipality has recently acquired all the essential land to build on.
“What we do here has direct consequences for the position of the Netherlands,” said Steenbakkers. “Our jobs, our prosperity, our autonomy; the companies that will soon establish themselves here play a crucial role in this. Think of battery development and production, photonics, additive manufacturing, and more. BIC1 already plays a prominent role in this, but BIC2 will soon be the place for it. Companies that focus on high complexity, in relatively low volumes but with a gigantic impact.”
For Ferdinand Gremmen, director of SDK Vastgoed (VolkerWessels), the increasingly concrete steps for BIC2 are the ultimate proof of the success of the Brainport Industries Campus’ original “clubhouse” idea. “We have brought the whole chain together since the opening of BIC in 2019. Within the current BIC, we already see how the companies are growing; soon, we will be able to take additional steps in that direction through even better clustering.”
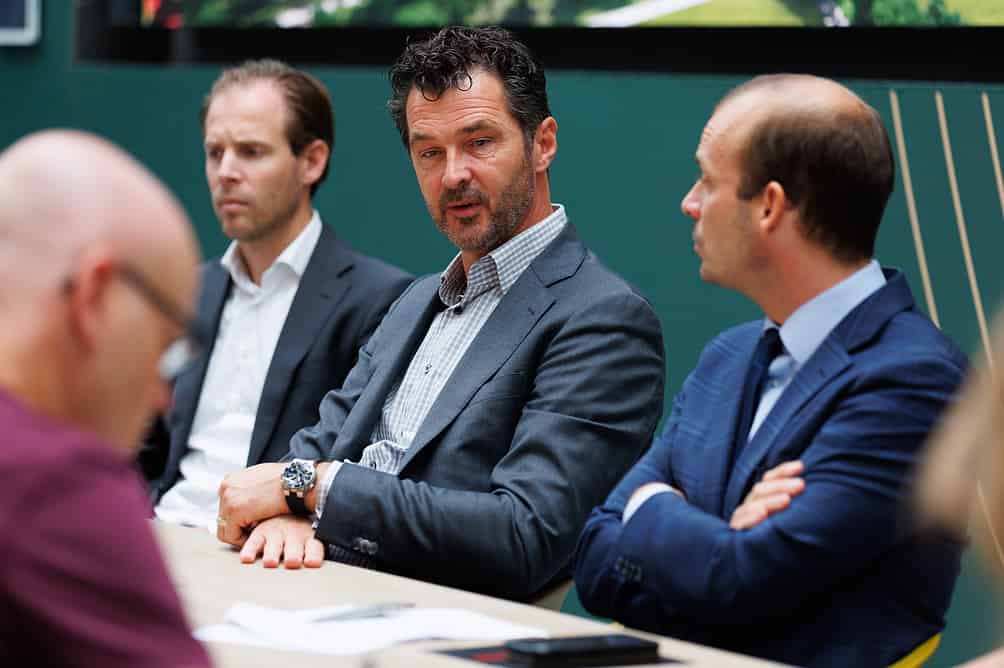
Rent and buy
The companies that are expected to move into BIC2 from 2027 can no longer do so only as tenants but also as owners of part of the complex. “But whether they rent or buy, the condition remains that they need to be part of the chain and the ecosystem,” says Gremmen. “That means open innovation, collaboration, sharing the added value. A campus like ours is more than just a business park.”
According to Gremmen, the cooperation model also has major advantages in terms of efficiency and sustainability. “We calculated that the companies that are now in BIC used to need about 20 megawatts of energy annually; now that they are together, it is 3 to 4 megawatts. Or take the logistical implications: thanks to BIC, there are now only 75 trucks instead of the 450 previously needed. This is mainly due to smart combining: the carrier can now take the packages of several companies with one drive to ASML.”
Regional direction
The expectations for BIC2 and beyond are partly based on the experience that the municipality and developers have already accumulated. Steenbakkers: “We see clear lines of development from TU/e campus, where many initiatives arise in their earliest form, through growth towards R&D and prototyping on the High Tech Campus to real production on BIC. The Automotive Campus in Helmond and the initiatives at Strijp-S and Strijp-T also play their role in this process. That way, we get a realistic impression of the need that will arise for BIC2 in a few years.”
But to keep all that on track, some regional direction is needed, said the alderman. “We really want to make BIC2 the place where the high-tech manufacturing industry can get started. The better that concentration is, the more successful the concept will be. At the same time, we also want to keep space for the other SMEs in the regular business parks. So, see this also as a signal to the region. Of course, we cannot force anyone to locate here and not somewhere else, but good coordination between small and large is essential within the 21 Brainport municipalities, both in the interest of the high-tech manufacturing industry and SMEs.”
Apart from that direction, BIC also has its internal appeal, says Gremmen. “It’s really not just about the price per square meter, but also about things like the access to talent thanks to all those students who are here. Or about the time-to-market that can go down thanks to the campus. Entrepreneurs look at the total cost of ownership, and for that, BIC has all the advantages.”
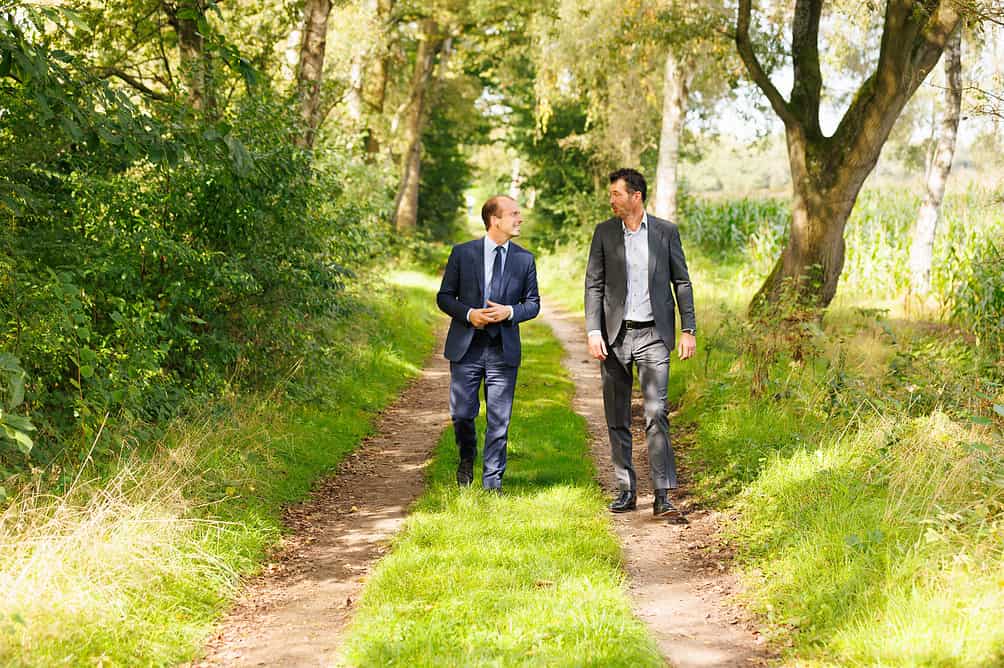
Crossing the campus by bike
From the existing Brainport Industries Campus, it is a 5-minute walk to the intended site for BIC2. Steenbakkers and Gremmen show us what to expect there. “The design is completely adapted to the landscape,” the alderman promises. “Even Eindhoven residents who don’t work here will get their share of it. Cycling to the campus and being able to see through the windows what wonderful solutions are being worked on here. And meanwhile, they can enjoy the green, park-like surroundings. The cornfield behind us will no longer be there, but you can bet that the biodiversity will only increase.”