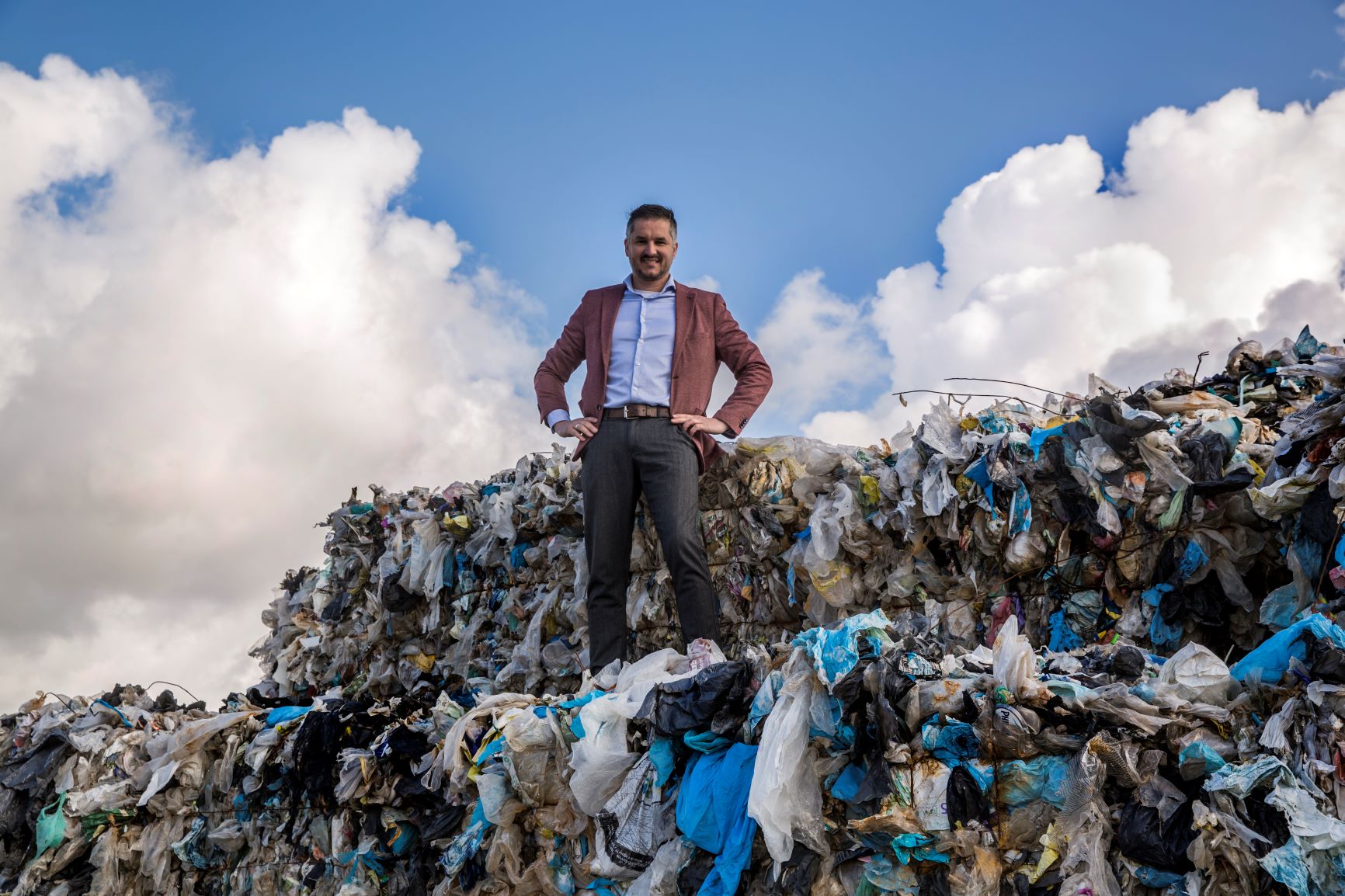
A new, localized plastics recycling plant is opening today in Almere to address one specific problem: mixed plastics. These are the lower grade variety plastics โ such as single-use plastic bags and dirty containers โ that we throw in with the rest of our trash. While higher quality plastics can be recycled easily, about half of all discarded plastics in the Netherlands are mixed plastics and either follow our garbage to the landfill or are incinerated, emitting more and more CO2 into our atmosphere. The plant in Almere is the start โ a test to see if regions can take control of their mixed plastic recycling internally and make products that benefit their communities.
The Arnhem based Save Plastics is behind the project and have built it to test the feasibility of a dedicated mixed plastics recycling plant for a single municipality or region. It will receive mixed plastics from the people of Almere and convert it into several end-products, such as building blocks for houses, cladding, and outdoor tables, among others.
โThe fun part is that it is technology that already exists,โ says Bram Peters, CEO of Save Plastics. โThe equipment is not patented. Itโs not rocket science. Even I can work the machines after one day at the factory.โ
Save Plastics have operated for over thirty years and supply many infrastructure projects with products made out of recycled plastic. In Arnhem, for example, they process plastic litter into plastic walking bridges.
In Almere, they have to build 50,000 houses over the next two years and are interested in using plastic building blocks
Bram Peters โ CEO of Save Plastics
This new plant will serve as a pilot project for a larger concept idea by Peters. If successful, he would scale up this project and begin an ambitious goal of creating dedicated regional plants to recycle mixed plastic โ around the world. These would also function as factories, creating similar products currently being used by his customers.
Save Plastics
โJust to be clear, I am anti-plastic,โ says Peters. โBut every year, the amount of plastic packaging is growing, so the problem will be here for a long time.โ
Peters has been in the plastic recycling world for nearly his entire adult life. His father, Gerard Peters, began Save Plastics in the 1980s, where he recycled agricultural plastic film into raw materials. After graduating with a degree in forestry, Bram took over the business and made headlines when Save Plastics created a lamp post made entirely of recycled plastic. He then transitioned the company away from creating raw materials and into outdoor products: Plastic scaffolding, plastic sheeting, and plastic picnic tables, to name a few.
Peters even lives in a house that is literally made of recycled plastic. โThe first plastic waste house from Holland,โ he jokes.
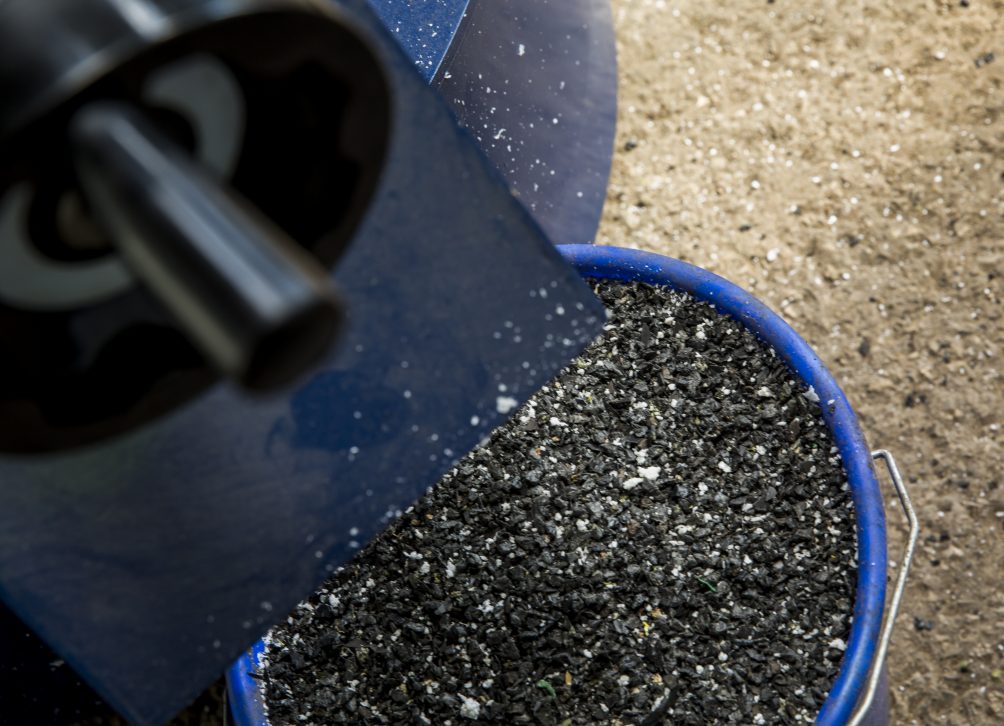
This is one of his ideas that has not achieved the same public acceptance that his other products have. He envisions building communities out of building blocks and cladding made entirely of recycled mixed plastics. An idea that has so far been a tough sell.
Plastic communities
โThere is not a soul in holland (or perhaps the whole world) who says, โI want to live in a plastic house,โโ says Peters.
The current recycling plant he uses, at Hahn Plastics in Germany, wants nothing to do with the idea either. โThey think weโre nuts,โ Peters explains.
Despite this, he believes in the idea to build recycled plastic communities enough to branch-off from the Germany-based large plant and into smaller, local ones. The plant in Almere will kickstart this vision.
โIn Almere, they have to build 50,000 houses over the next two years and are interested in using plastic building blocks,โ says Peters.
Localized recycling plants
If the idea for plastic communities does not garner enough support, the plant will still be able to supply useful products while taking care of mixed plastic recycling in a sustainable way. Using the environmental cost indicator โ a way of equating the impact of material production in terms of its environmental footprint โ the production of one kilogram of his recycled plastic product costs .05. This is a fraction of what it costs for new plastics or even sustainable tropical wood production.
They use intrusion molding and can create a mold for any products region might need. The plant itself is also inexpensive โ this pilot plant only costs about 100,000 euros to build. This means that it can be scaled and replicated in less developed countries as well.
โFor instance, we are now doing business in Fiji,โ explains Peters. โIf they wanted to have this factory, we would fly operators over there and give them instructions for a week โ certify them โ and then they can operate them there.โ
โI really think that innovation should come from small companies with help from big companies and government,โ says Peters. โIn the end, it should all come from local people.โ
Read here about an app that predicts where plastic will collect on beaches.