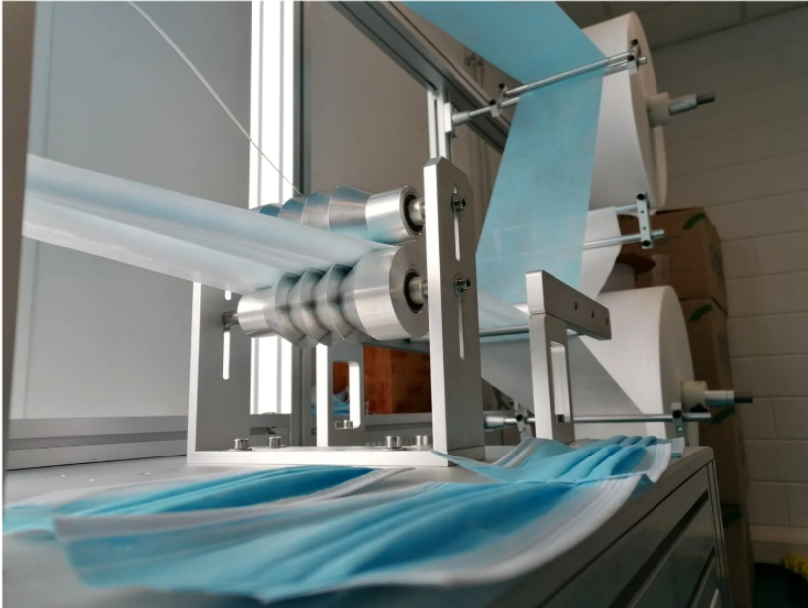
It should have presented a splendid business opportunity for textile screen printer Eco Textieldruk: the purchase of a machine that produces more than a hundred medical face masks per minute. Given the high number of infections, increasing production in the Netherlands is a matter of urgency. Yet, the sales of the Groningen-based company have been at a standstill for months due to fierce competition from countries such as China, Russia or Brazil. After all, medical masks are manufactured there at ridiculously low prices. According to founder Jos van der Mijl, it is high time that the Netherlands started looking beyond the price tag. “Let’s produce safe face masks on our own soil and build a complete recycling system around that.”
The decision to produce face masks was quickly made for the family business, where Van der Mijl’s own daughter and two sons also work. “We made the decision when we heard that panic was breaking out among healthcare institutions in the Netherlands because there was not enough capacity for face masks,” says Van der Mijl. ” In order to buy the right machines, we had one of our manufacturers in China with whom we had been doing business for years very quickly get a machine ready that we had flown to the Netherlands.” The company focuses on so-called type IIR -certified mouth masks, which guarantee protection. The support from the Province of Groningen through a grant for the machine was the deciding factor. “We thought it was going to be a great success.”
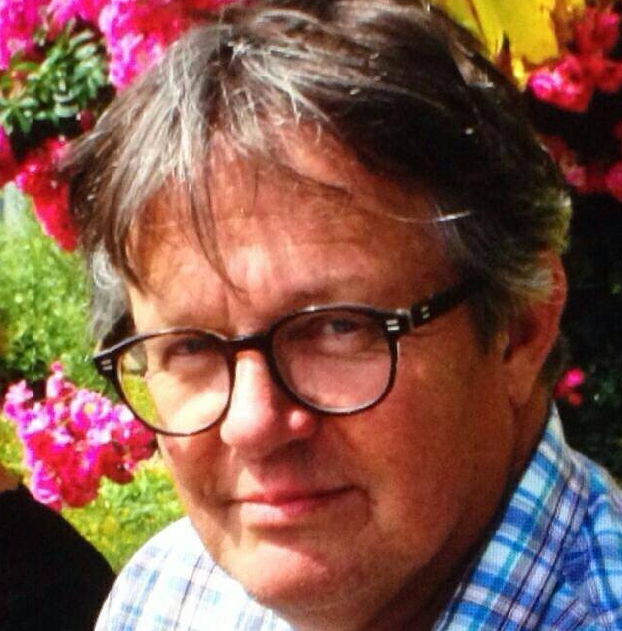
But nothing could be further from the truth. EcoTextile Printing no longer sells any face masks and the brand new machine has been idle for months. The problem? The competition from countries such as China and Eastern Europe, where the government and healthcare institutions buy the masks in bulk. The advantages are obvious. “The raw materials used to produce the masks in these countries are up to 30 times cheaper than the more expensive but safe filter material that is used in the Netherlands,” Van der Mijl explains. There are many disadvantages to this kind of mass purchasing from abroad. Apart from the fact that shipping the masks generates enormous amounts of CO2 emissions, many of the imported masks are unsafe.
Unsafe masks
Due to the skyrocketing increase in the number of infections during the spring of 2020, hospitals and healthcare institutions were under pressure to import a huge quantity of medical masks into the Netherlands as quickly as possible. But a study by TU Delft showed that most of the medical masks, randomly surveyed among more than 400 suppliers, were unsafe.
According to Van der Mijl, the masks are easier to inspect if they come from the Netherlands. “In practice, many masks that are certified do not meet the requirements at all. As a result, a huge number of masks had to be rejected and are now in storage waiting for buyers. If we have the masks produced in the Netherlands, it is much easier to carry out tests, see how the production process takes place and ensure that the masks are guaranteed to be safer.”
Millions of face masks are also purchased in huge stocks from abroad, such as Lithuania. These are in danger of becoming out of date. This leads to bizarre situations. The Dutch Ministry of Health, Welfare and Sport sells the masks at extremely low prices to foreign buyers. And these buyers then bring the masks back onto the Dutch market. “These unsafe face masks then end up in our healthcare system after all. That simply should not be the intention. When the face masks are produced domestically, the lines of communication between buyers and producers can be kept short. When a surplus threatens to occur, the producer is quickly able to switch gears.”
Reusing face masks
The sight of face masks littered around parks and neighbourhoods is a familiar one. Face masks are a source of pollution and are seen as the new litter. If most of the medical masks were produced in the Netherlands, it would be possible to come up with a well-functioning, nationally organised recycling process, as Van der Mijl sees it. “Currently, masks are changed about four times a day in healthcare institutions. Healthcare institutions handle used masks properly and they don’t end up in parks, nevertheless, the fact remains that they eventually end up in landfill. This can be done in a smarter way. We can set up an ecological system whereby manufacturers of face masks charge an environmental fee for retrieving the masks. And we at EcoTextile Printing would definitely be willing to work on this.”
Subsidy for face masks
Safer, Dutch face masks that can be reused: it is a clear goal. But how are we going to accomplish this in the Netherlands? “My idea would be to give healthcare institutions that buy face masks a subsidy on those masks if they can prove that they have bought a Dutch mask,” says Van der Mijl. And as for recycling: “What if we gave healthcare institutions bins where they could dump the used masks? We can then collect them and recycle them. Then we’ve come full circle.”
It is not a complicated plan, but government parties have to step up and make it happen. “Maybe in five years’ time, we will be in the middle of the next pandemic. Then we’ll be overwhelmed by panic again and we’ll have to make decisions quickly as a country. Right now we have the opportunity to responsibly set up a circular system for face masks. Let’s seize that opportunity.” Meanwhile, Van der Mijl is endeavouring to approach various government parties and get them enthusiastic about the plan.
Innovative and Sustainable SME Groningen
Entrepreneurs in small and medium-sized enterprises (SMEs) often have their hands full with matters relating to the start-up and expansion of their business. They have very little time and capacity to figure out how to become more sustainable or to innovate. Entrepreneurs in Groningen are supported in this process by the provincial Innovative and Sustainable SME subsidy scheme. The company Eco Textieldruk has received a grant for an investment in a machine for manufacturing face masks. The machine is capable of producing around 125 face masks per minute.
Positive change
The setbacks over the past year, however, have not deterred the family business from further growth. In fact, this past period has also brought some positive developments. “We have hired three new staff members who we can now give new work in our print shop. This has made a huge improvement to the entire organisation. We have also started to work in a much cleaner and streamlined way. The staff no longer have to look at printed orders, for example; we now have computer systems everywhere to process them.”
Van der Mijl still hopes to be able to continue manufacturing face masks in the future. “But we’ll just keep on doing the other work we’re good at: printing on clothing and designing the machines for that.”
Read other stories about Groningen via this link.