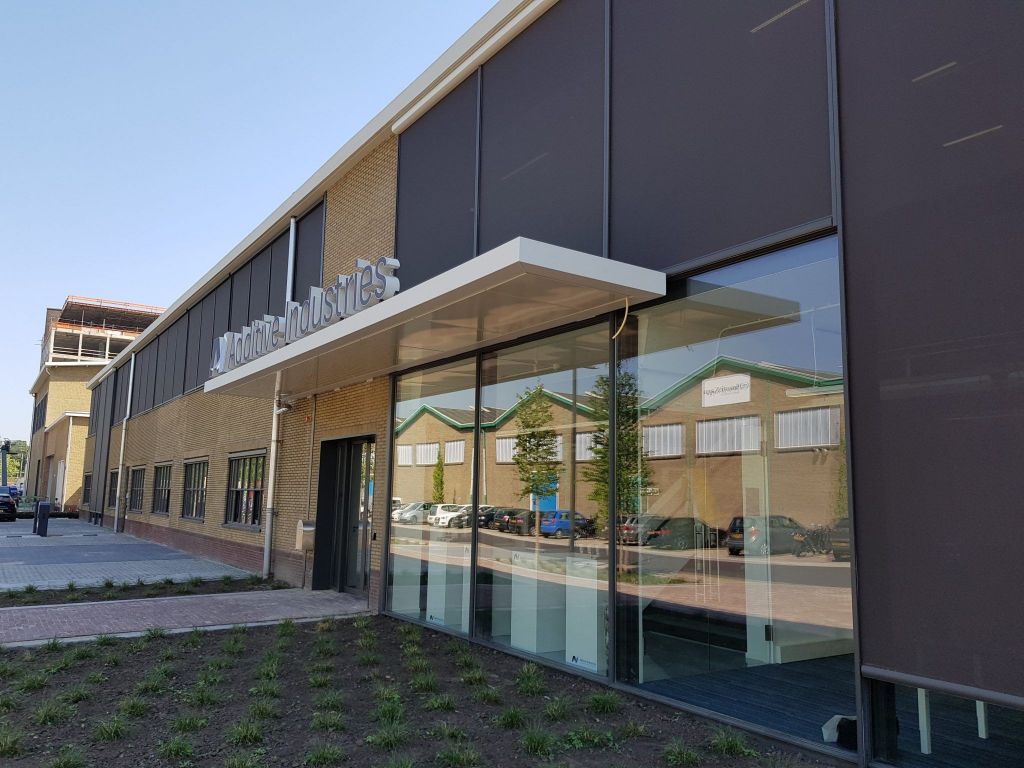
6 designs from 6 countries on 4 continents have reached the finals of the Additive Manufacturing Challenge 2019. They were selected from a group of 129 contestants, both professionals and students. The organiser of the Challenge, Additive Industries, wants to ignite creativity in redesigns of products, using additive manufacturing. “The redesigns submitted from all over the world and across different fields like automotive, aerospace, medical, tooling, and high tech, demonstrated how product designs can be improved when the freedom of additive manufacturing is applied”, says Daan Kersten, CEO of Additive Industries. “This year again we saw a major focus on the elimination of conventional manufacturing difficulties, minimization of assembly and lowering logistical costs. There are also interesting potential business cases within both categories.”
Professional
This year, in the professional category, Carbon Performance Limited (the UK) shows how the hyper-performance suspension upright, one of the most critical load-bearing components of the sports car, can get a 30% weight reduction, in contrast to any conventional upright, by using topology optimisation. Another professional, K3D from the Netherlands, improved the performance of the old design of the cutting dough knife (food tech), which is attached to a robot, by optimising it for additive manufacturing. Besides solving such problems as the stickiness of the dough during the cutting process and uneven depth of each cut, K3D also manages to save up to 90% of the weight & reduce the production price by using the redesigned additive manufactured dough knife. The third finalist of the professional category, Mr Kartheek Raghu, from the Indian company Wipro3D, redesigned the conventional design of a Cold Finger thermal trap for a sublimation process. The cold trap is a device that condenses all vapours, except the permanent gases into a liquid or solid. The redesign contains a fine lattice structure that holds cryogenic temperature for longer and therefore improves performance.
Students
The finalists from the student category had interesting redesigns this year as well. Two students from Nanyang Technological University (Singapore), with their “Brake Caliper” (automotive application) optimised the part design for the challenge and managed to reduce the weight by 2.61kg, which is a 35% weight reduction of the overall part. Abraham Mathew from the McMaster University (Canada) introduced his Topography Optimized Cubesat Propellant Tank (space industry) to improve the stiffness of thin-walled parts by modifying surface features without increasing wall thickness and consequently mass. The third finalist in the student category, Obasogie Okpamen from the Landmark University (Nigeria) achieved the mass and material reduction in his version of the “Twin Spark Connecting Rod” through topology optimization.

The designs are (from left to right, first top row then bottom):
“Hyper-performance suspension upright” from Revannth Narmatha Murugesan, Carbon Performance Limited (United Kingdom, professional category)
“Cutting dough knife” from Jaap Bulsink, K3D (The Netherlands, professional category)
“Cold Finger” from Kartheek Raghu, Wipro3D (India, professional category)
“Brake Caliper” from Nanyang Technological University team (Singapore, student category)
“Cubesat Propellant Tank” from Abraham Mathew, the McMaster University (Canada, student category)
“Twin Spark Connecting Rod” from Obasogie Okpamen, the Landmark University (Nigeria, student category)
Pictures: (c) Additive Industries