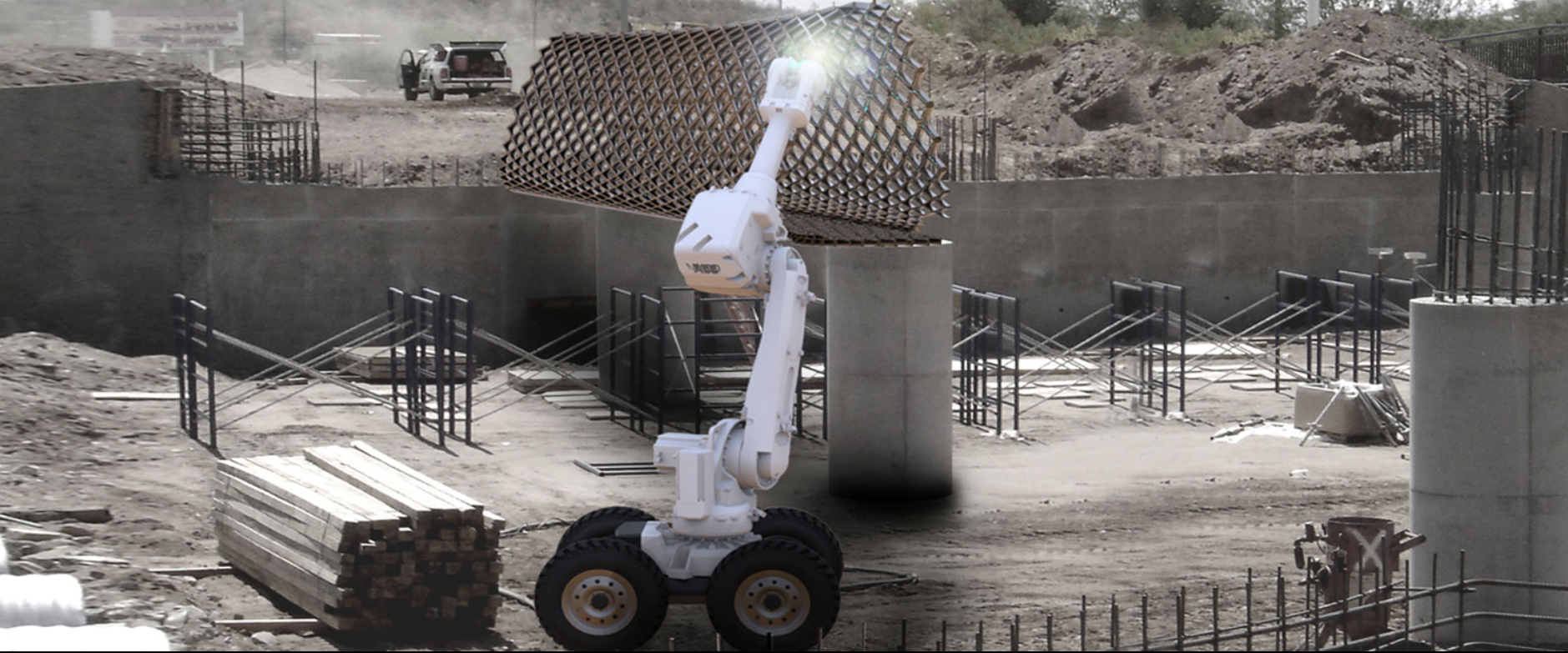
The use of 3D printers has been more than hype for a long time. In the automotive and aerospace industries and for medical applications, it is a widely used means of production. Often these are high-quality products with high added value, such as prostheses or car parts. Last summer, the first 3D-printed bridge weighing 6,000 kilos was opened in Amsterdam. Is this project, the first of its kind worldwide, a harbinger of large-scale deployment of 3D printers for the construction industry?
If it were up to Gijs van der Velden, founder and CEO of MX3D, it would be. MX3D launched the bridge project as a dot on the horizon. The goal was to provide visible proof that it really can be done: print a safe, large, high-quality object. โWhen we started in 2015, it was totally unclear whether the construction industry would be able to do anything with it. Everywhere we tried to market our technology and vision, we were laughed at because we were doing something where people only saw the problems, not the possibilities.โ
Increasing interest from the construction industry
But that has now changed. Since the bridge opened, more and more companies are knocking on MX3Dโs door with increasingly interesting questions. Still, printing a complete bridge is not something that can be repeated. โFor the complex construction parts where a steel structure comes together, a robot is very handy, but the rectilinear, large parts you can build faster and more easily with standard pipes.โ This is also how Van der Velden envisions the future: the 3D printer is not going to replace all current techniques in construction, but rather complement them.
The startup provides a software package that transforms welding robots, often already present at construction companies, into a 3D printer. At least that was the initial idea. Van der Velden says: โWe found out in the process that companies have a much greater need for the total package: a new robot with our software in it. So now we also offer a complete turnkey robot printer.โ
One of the biggest challenges in deploying 3D technology in the construction industry is the material, says van der Velden. โWhen we started, everyone in the industry thought that based on their experiences with welding, a 3D-printed structure could never match the quality of welding technology.โ Five years and a lot of research later, MX3D can truly guarantee that the materials are of excellent quality.
Rob Wolfs, assistant professor at the Faculty of Architecture at Eindhoven University of Technology, agrees. โI see more and more entities daring to invest in printing and robotization. They see more and more that it really is a realistic option. The bridge in Amsterdam is a good example of that.โ
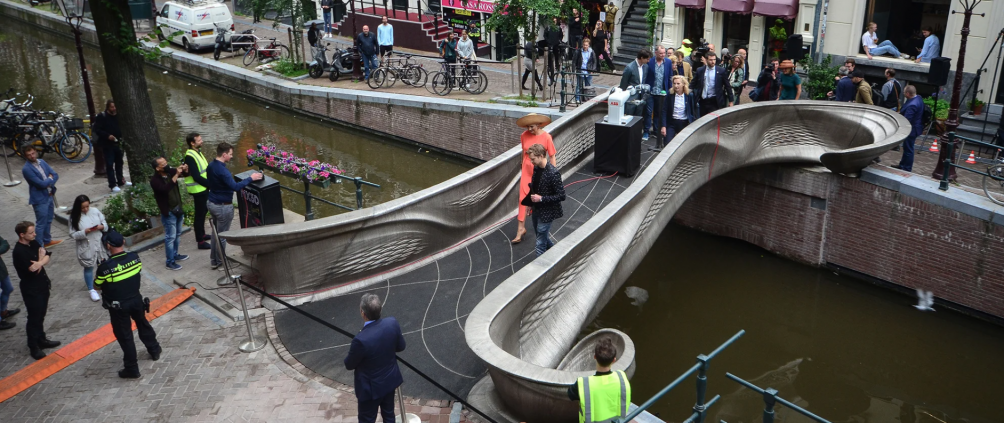
Housing shortage and sustainability
According to Wolfs, the construction sector faces two major challenges: the housing shortage and building more sustainably. โOn the one hand, we need to build more, but it must also be done more sustainably. The beauty of 3D printing is that it can be at least part of the answer to both issues.โ
3D printing is not necessarily more sustainable, but a 3D printer does use significantly less energy than, say, a milling machine, van der Velden explains. โAnd radically less material is needed. Stainless steel has a hefty footprint, but the moment we can produce with a 3D printer with 20 to 30 percent less material, you bring that footprint down enormously.โ Van der Velden sees another question that 3D printing can answer. โWelders are very hard to find these days, 3D printing could be a way to still be able to meet that demand.โ
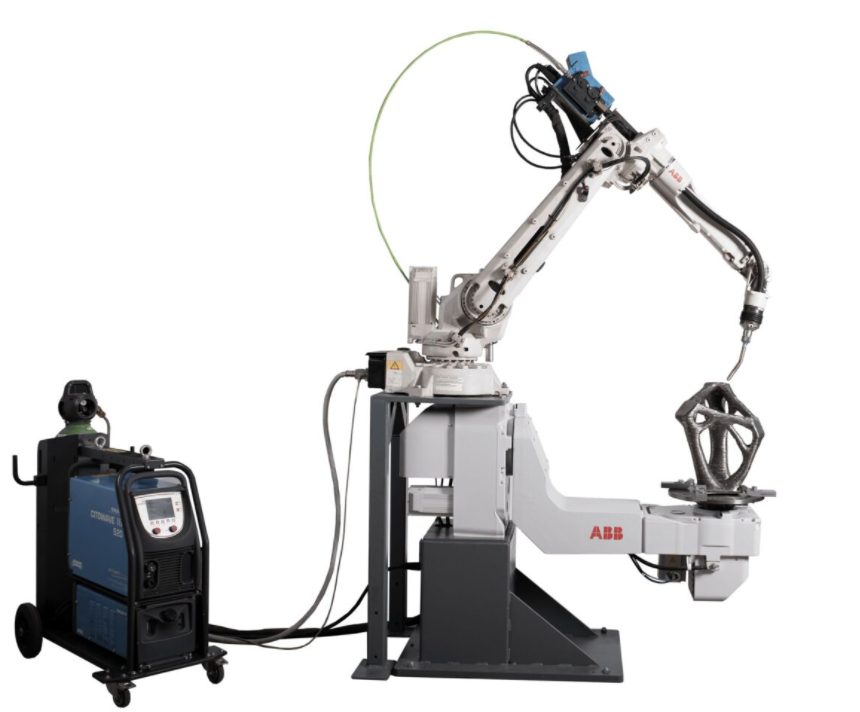
FDM printing
There are different 3D printing techniques: powder bed printing, welding printing or concrete printing, for example. At MX3D, they focus on Fused Deposit Modeling (FDM) printing. A wire passes through the head of the printer and an object is printed layer by layer. The big advantage of this technique is that large volumes can be printed relatively easily. Van der Velden explains: โWe use industrial robots. If you put them on an elevation, you can handle a very large construction volume.โ
One 3D robot from MX3D prints between 1.5 and four kilos of steel per hour. โSo if you produce an object of 6,000 kilos, itโs not printed within two days. People sometimes expect a complete skyscraper to roll out of the printer within a week, haha.โ Printing a skyscraper or a complete bridge is not the ambition, โbut if a new bridge with a special shape has to be built, 3D printing is definitely a godsend.โ
Challenges
The big question remains: Will 3D printing conquer the construction industry or not? Wolfs sees many exciting projects coming up in which 3D printing is fully deployed. Good news, but for the time being these are individual projects. โBefore the technology can enter the construction sector on a large scale, there are three issues we need to resolve. First, the material must become more durable and functional. The materials we print with are still fairly standard.โ As an example, Wolfs mentions concrete that also has a direct insulating effect or has properties enabling it to conduct electricity or repair itself. โThatโs when it becomes really interesting.โ
The second challenge is combining printing with the use of traditional steel bars and nets. โConcrete always interacts with steel. Steel nets and rods absorb the tensile force, otherwise the concrete cracks.โ
The third and final issue, Wolfs says, is how to design with the new techniques. โHow are we going to design buildings and bridges to make maximum use of the technology and work as efficiently as possible? All the safety rules and standards regarding these issues are still being developed.โ
Steel hub as a new milestone
Van der Velden sees that the industry is seeing more and more opportunities to integrate 3D printing into their business. โWe have developed a steel junction in collaboration with a Japanese company that is widely used for bridge construction. Its material properties are currently being certified by Lloyds Register.โ The certification is a new milestone for 3D printing in the construction industry: it ensures that a new project can be carried out faster, cheaper and more easily without the need for further research.
Wolfs also looks positively to the future. โWhen I started researching, it was about putting layers of concrete on top of each other and waiting to see what would happen. Now, five years later, people are already printing all over the world with that technique. Weโve gone from printing layer by layer to a complete house in a short period of time. I find that scaling up to be hopeful and impressive.โ Thatโs also what makes the interaction between 3D printing and the construction industry so interesting, Wolfs says. โA complex task, but through collaboration of industry, government and science, the technology can truly be an answer to the sustainability issue and the housing shortage. I am convinced of that.โ
Read more about 3D printing: Automation in 3D printing post production is key to success