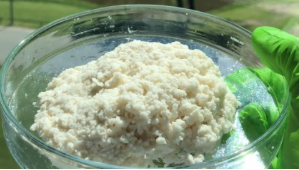
Water shortages are one of the major problems facing the world in the coming decades. Desalination of seawater can offer a solution. But the process is expensive and often unstable. This is partly due to the membranes that are used in the process. However, researchers at the University of Twente (TU Twente) in the Netherlands have invented a new plastic, called salonlast. This enables them to make very stable membranes, which at least solves that problem.
An ion exchange membrane is used in electrodialysis for the desalination of seawater or brackish water. This allows the ions from aqueous salt to pass through, but blocks the water itself. These membranes are expensive and not stable in environments with very high or very low pH levels. But the membrane the TU researchers are making with their new plastic is stable.
Mozarella ball
“When mixing certain positively and negatively charged polymers in water, we were already able to make a poly-electrolyte complex (PEC) that can best be described as a mozzarella-like ball of plastic,” says Prof. Dr. Wiebe de Vos in a TU Twente press release about the invention. “The main problem, though, was still getting this complex easily processed into a usable membrane,” adds Ameya Krishna B.
The researchers eventually chose a technique that uses a heat press. The material is put into a mold and placed inside a heat press. At first, the press closes without any extra pressure and heats up to a temperature of eighty degrees Celsius. After about twenty minutes, when the material has reached this temperature, the pressure increases to two hundred bar. This is comparable to the pressure of roughly two kilometers under water and takes approximately five minutes. After that, the material cools down to twenty-five degrees Celsius.
Fuel cells
“The whole process takes about an hour, much less than other techniques that are used where the process can take up to several days,” Saskia Lindhoud explains. The end product is a transparent, high-density film. The membrane is firm and flexible and extremely dense down to a nanometer scale. In addition, the process is fully scalable as well with excellent control over the size, thickness and structure of the membrane.
The membrane can be used in many ways. Its stability factor at very high and low pH values makes it suitable for fuel cells. Also, the relatively simple production process does not depend on organic solvents, and the material repairs itself in saltwater.
UT researchers , Dr. Saskia Lindhoud and Prof. Dr. Wiebe de Vos (TNW faculty / MESA+) published their work in the scientific journal Journal of Colloid and Interface Science. The article is open access and can be read online here.