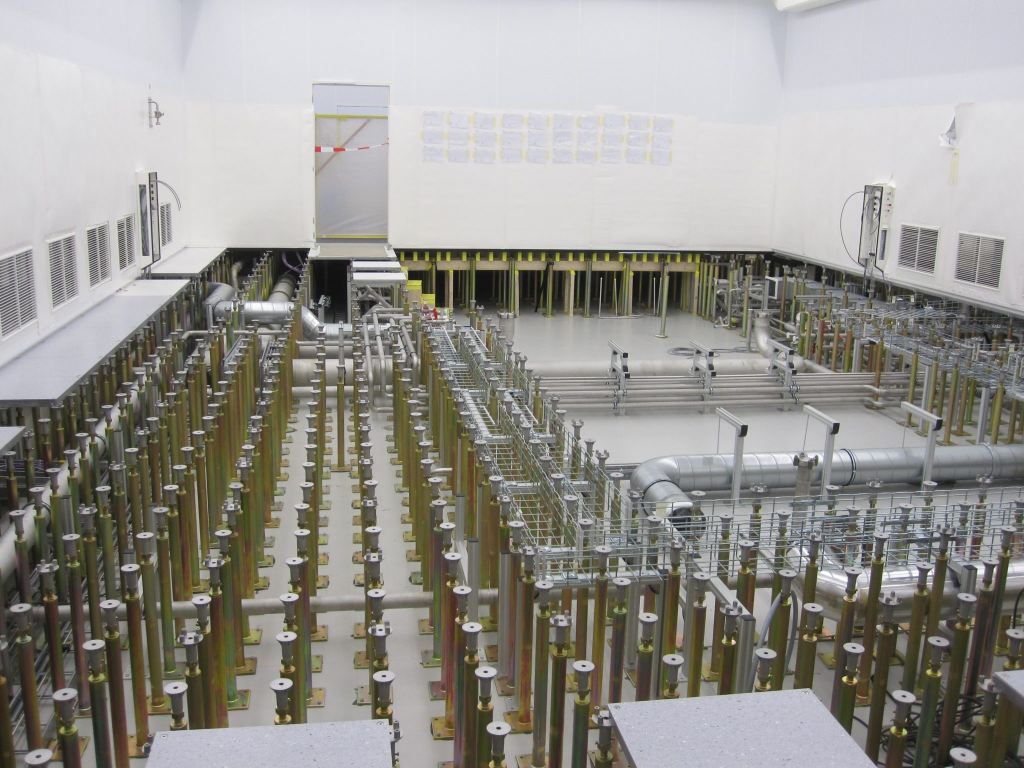
De Veldhovense chipmachinefabrikant ASML is inmiddels zo groot (14.000 werknemers wereldwijd, een jaaromzet van bijna 6 miljard in 2014) dat iedereen wel door heeft dat daar iets bijzonders gebeurt. Maar wat precies? Je moet zowel ingenieur als bedrijfskundige zijn om dat goed te kunnen doorgronden. En dan nog zal een deel van het verhaal altijd verborgen blijven achter de muren van toren 8 op bedrijventerrein De Run.
Die toren is overigens niet de plek waar het “echte” werk gebeurt. Nee, het hart van de organisatie klopt waar onderzoek en uitvoering – als kamer en boezem van het menselijk hart – bij elkaar komen. In ASML-termen: where lab meets fab. In en boven de cleanrooms zijn laboratorium en fabriek één geheel. Geen buitenstaander die er, normaal gesproken, binnen komt, zo zuinig zijn ze erop. Dat is deels om de concurrentie niet slimmer te maken dan strikt noodzakelijk, maar zeker ook om de 100% stofvrije processen daarbinnen niet te verstoren.
Toch, heel soms, maakt het bedrijf precies op die plek ruimte voor een select groepje bezoekers. Niet dat daarmee alle geheimen worden prijsgegeven (integendeel eerder: elk zichtbaar detail roept voor een bezoeker meer vragen op dan dat het antwoorden geeft) maar het geeft wel een indruk van de – letterlijk – duizelingwekkende ontwikkelingen waar ASML nu vorm aan geeft. e52 mocht mee en zag hoe in die stofvrije omgeving draadje voor draadje, schroefje voor schroefje en datadeel na datadeel de modernste chipsmachines worden neergezet. Het zijn letterlijk de machines van de toekomst want zelfs tijdens de bouw gaat de ontwikkeling nog door.
Rondgeleid worden in de nieuwste cleanroom (5H, die in juni officieel open ging) betekent je conformeren aan de regels van het bedrijf – en van de wetenschap. En dus stappen zeven journalisten met hun vier begeleiders in full bunnysuits. Zonder camera of notitieboekje, want dat is de regel.
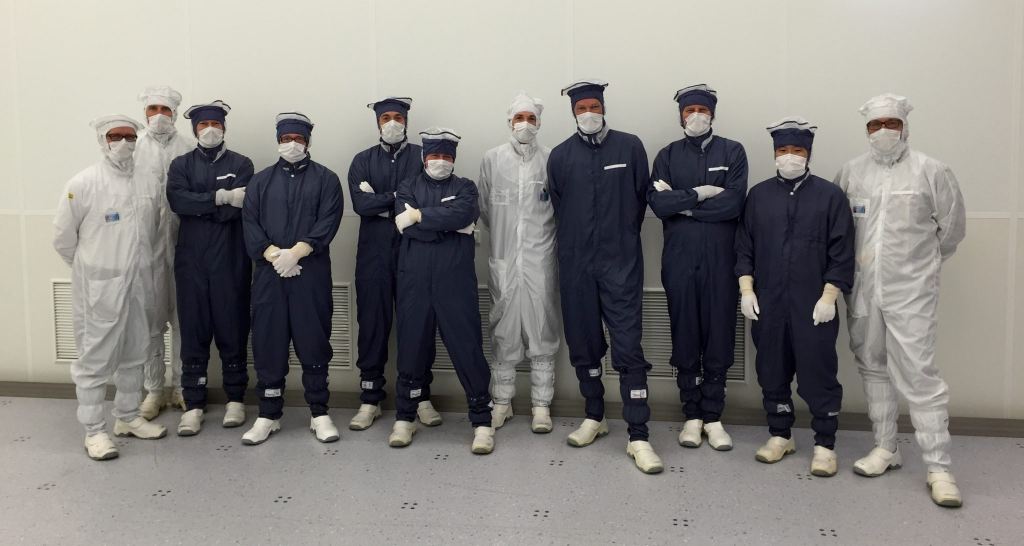
Het belangrijkste idee achter het labfab is, zo zegt vp facility management Marc Peels, “onze strategie van het zo dicht mogelijk bij elkaar brengen van lab en fab, onderzoek en productie.” Hij vertelt hoe in bijna 30 jaar tijd niet alleen de omvang van de machines enorm is gegroeid (de PAS2500 uit 1987 woog 2500 kilo en paste in een bezemkast, de NXE uit 2015 weegt bijna 100.000 kilo en gaat maar net in een Boeing 747), ook de cleanliness groeide mee. Waar medewerkers aanvankelijk aan een haarnetje en stofjas voldoende hadden, komen ze nu niet meer binnen zonder volledige lichaamsbedekking.
Hoe geheim alles ook is voor passanten, ASML eist van haar leveranciers onvoorwaardelijk, wederzijds vertrouwen in het hele proces van onderhandelen, proces bepalen en bouwen. Peels: “We hebben daar een formule voor bedacht: vertrouwen is kundigheid x samenwerking x flexibiliteit gedeeld door eigenbelang. Wie echt wil vertrouwen, moet eigenbelang kunnen uitschakelen. Wij eisen dan ook van onze partners en leveranciers dat ze niet alleen willen snappen hoe het werkt, maar ook dat ze samenwerken en flexibel zijn.”
Hoe snel alles ook verandert, aan enige planning ontkomt ook ASML niet. “Maar het verschil is wel dat bij ons de verschillende stadia in de planning gelijktijdig lopen in plaats van na elkaar. Zo kun je een traditionele bouwcyclus, normaal al gauw zo’n 5 à 7 jaar, flink inkorten. Wij moeten – samen met onze bouwpartners, dat maakt het extra ingewikkeld – niet alleen parallel plannen, maar ook nog eens constant open staan voor tussentijdse aanpassingen. Tijdens de bouw van onze huidige fabriek zijn er 35 scope changes geweest, gewoon vanwege innovaties en voortschrijdende techniek.”
Voordat de machines zelf een plek konden krijgen, moesten ASML en haar zeven bouwpartners ervoor zorgen dat deze in alle omstandigheden trillingsvrij zouden kunnen opereren. Want zelfs de kleinste afwijking zou het chipfabricageproces kunnen verstoren. En dus werden er 1500 palen de grond in geheid, bij elkaar zo’n 25 kilometer in lengte. Daarboven kwam een 3 miljoen kilo wegend stalen netwerk met 15.000 kuub beton, hetgeen dan weer is afgewerkt met een verhoogde vloer op zo’n 20.000 palen.
Maar niet alleen het fundament staat stevig, datzelfde kan gezegd worden van de bovenbouw, waar voor een Eiffeltoren aan staal is verwerkt: er moeten tenslotte de nodige kantoren op gebouwd kunnen worden.
Voor een bedrijf dat zegt het levende bewijs van de Wet van Moore te zijn (elke twee jaar verdubbelt het aantal transistoren op een chip), klinkt het wat vreemd maar Peels zegt er zeker van te zijn dat dat wat er nu staat de komende twintig jaar mee kan. Stap voor stap is ASML nu bezig met de inrichting. Wandelend door de nieuwste cleanrooms zien we de verschillende stadia in de assemblage van de machines. Sommige nog niet verder dan de grove structuren van de basismachine, andere al toe aan de afstelling en finetuning. Per machine is een paar weken nodig voor de bouw, maar zo’n anderhalf jaar voor de afstelling.
De enorme processen (tijd en geld) die daarmee gepaard gaan roepen de vraag op waarom ASML überhaupt de machines eerst in de eigen fabriek opbouwt. Ze zijn tenslotte allemaal bedoeld om uiteindelijk ergens op de wereld bij een klant uit te komen. Peels: “Twee hoofdredenen: tijdens de bouw zijn we de machine nog volop aan het doorontwikkelen, en daar willen we die klant optimaal van laten meeprofiteren, maar ook de finale afstemming is zo tijdrovend dat het niet alleen onhandig maar ook nog eens extra kostbaar zou zijn als we dat bij de klant zouden doen. Kort gezegd: hier in eigen huis kunnen we lab en fab bij elkaar brengen.”
De nieuwe fabrieken zijn helemaal ingericht om de nieuwste generatie chipsmachines te bouwen. Het gaat dan om de derde generatie NXE-machine, gebaseerd op EUV lithografie, ultraviolet licht. Daarmee kunnen de chips nog gedetailleerder worden “gevuld”. Volgens product manager Rudy Peeters zit er een groot voordeel aan deze machines: “Ze zorgen ervoor dat het lithografieproces in minder stappen kan worden doorlopen en dus goedkoper wordt.”
Helemaal uitontwikkeld zijn ze echter niet, zegt Peeters. “Ons doel voor dit en volgend jaar is om de stabiliteit en de beschikbaarheid van deze machines verder op te voeren en daarvoor moeten er nog grote en kleine verbeteringen plaatsvinden. Het mooie is trouwens dat we dat gewoon bij en samen met de klant doen. Wie zo’n machine heeft aangeschaft (ook de oudere generaties trouwens) weet dat hij ook alle verbeteringen geïnstalleerd kan krijgen.”
Wat geldt voor de machines, geldt trouwens ook voor de cleanroom in Veldhoven. Marc Peels: “Aan het einde van de bouw bleef er een lijst over van 35 verbeterpunten. Dan denk je misschien: zo, 35, da’s best veel. Maar als je je bedenkt dat voor een nieuwbouwhuis gemiddeld zo’n 100 verbeterpunten overblijven, denk ik dat we hier een geweldige prestatie hebben neergezet.”
Alle illustraties (c) ASML.