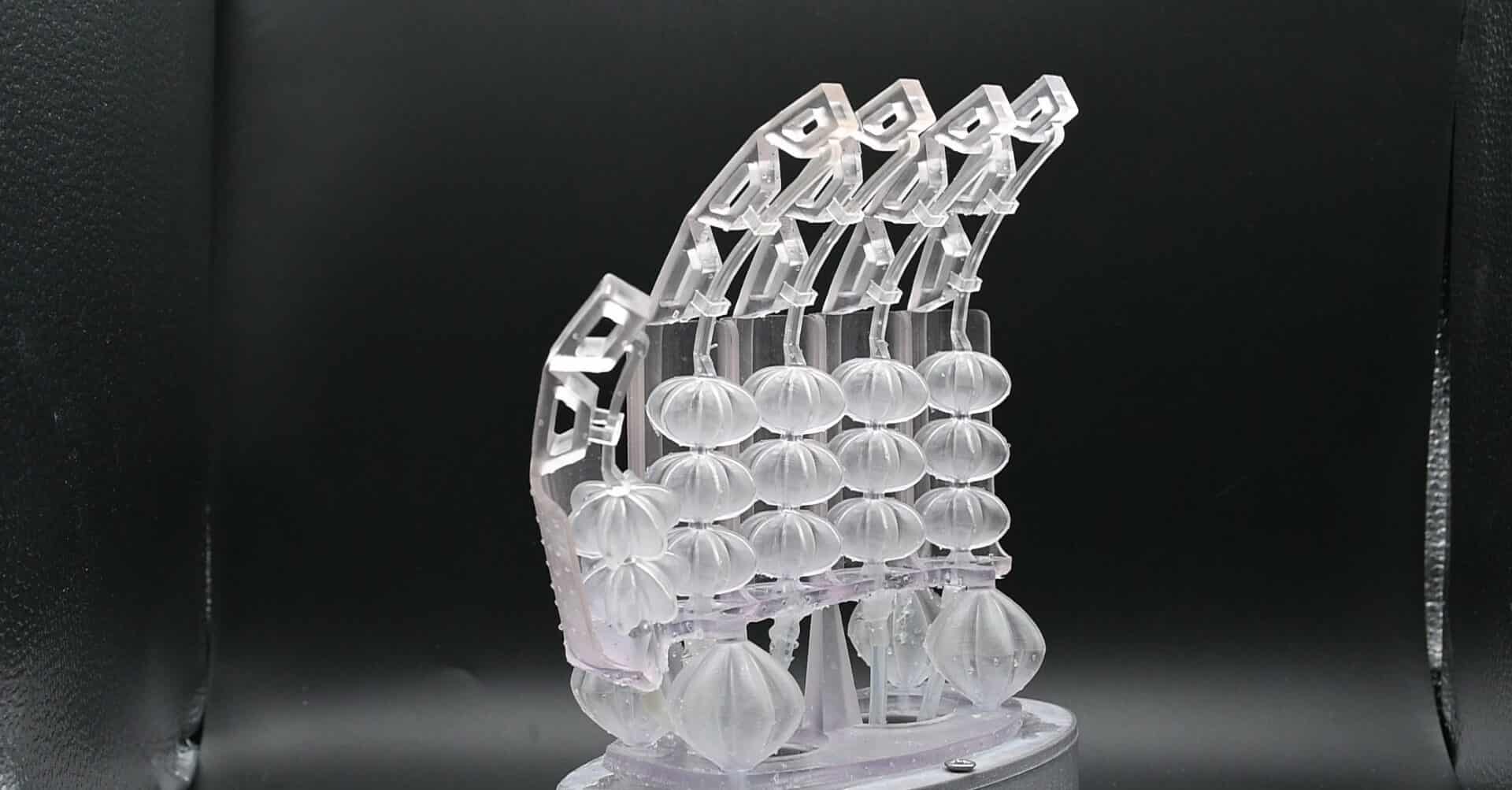
Laugh, walk, or type an e-mail, your muscles help you perform all of these and countless other actions. The human body’s tissue skillfulness has been hardly replicated artificially – because of its complexity. A cohort of researchers developed a way to design artificial muscles that resemble biological ones more accurately.
Scientists from the Italian Insitute of Technology – IIT – created 3D-printed spindle-like structures that can extend and contract at will. As a demonstration of their findings, they designed a pneumatic hand.
GRACEs – GeometRy-based Actuators able to Contract and Elongate – can lift up to 1000 times their weight. Fundamentally – depending on the movement and on the use the muscle has to perform – makers can choose what and how many GRACEs they want to use via a mathematical model.
“State-of-art artificial muscles are good, the problem is assembling and customizing them. The device we created offers a high degree of flexibility since contraction and extension can be personalized. In addition to that, GRACEs also allow the muscle to stretch out,” told Innovation Origins Corrado De Pascali. He’s the lead author of the study and a P.h.D. at the IIT.
Flexibility for complexity
A pneumatic artificial muscle – PAM, also called air muscle – uses air to mimic human movements. In a nutshell, they convert air energy into motion. Standard air muscles – the first one invented by McKibben in the 1950s – consist of an inflatable inner tube inside a braided mesh, with clamps at each end. When the tube is inflated, it expands, pushing the mesh accordingly. This sleeve contracts in proportion to the degree its diameter are forced to expand, pulling the clamps. That’s defined as the contractive force of the air muscle.
Pneumatic muscles are lightweight and provide a copy of biological muscles, being used in all those settings needing safety or entailing human interaction. The IIT team’s approach differs from McKibbens’s foundational one. The spindle-like actuators come in different forms favoring the replication of muscle complexity. A combination of different GRACEs is responsible for both finger and wrist movement in the demo hand presented.
Copying nature’s structures
GRACE design is a remake of a previous version of the actuators. Moving a step closer to nature, the IIT team introduced pleats in their muscles. This detail is already featured in some of the readaptations of McKibben’s concept – for easing mesh fiber placement. In the case of the novel design, they are pivotal to the muscle’s functioning.
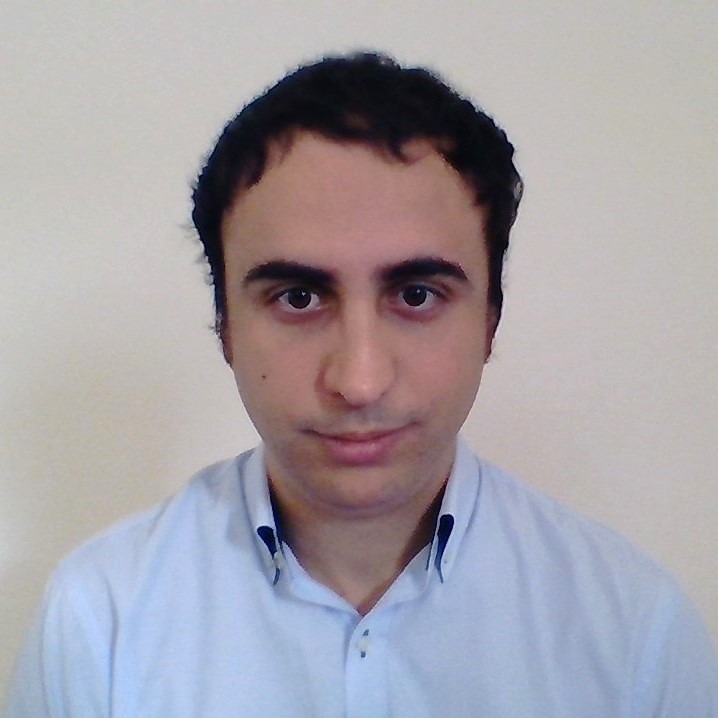
Corrado De Pascali
P.h.D student at IIT
He’s the first author of the study on pneumatic muscles.
Without pleats, the pneumatic muscle would inflate as a balloon. However, this wouldn’t provide effective functioning of the PAM, as it would extend. Pleats make sure that the air muscle contracts, generating a force. When deflating the muscle, pleats push the two ends away. Despite not copying the same dynamics as biological counterparts, for getting closer to the human body, copying small details can make a difference – as in the case of the hand Italian scientists presented.
Print pneumatic muscles as you like
To prove the method’s adaptability, the IIT team used a commercial 3D printer to produce the hand – in a single printing process. Three artificial muscles compose every finger. When inflated, they pull the tendons so that they open and close. Every finger has an autonomous pneumatic line, meaning each one can be deactivated separately. Four bigger GRACEs – two on each side – compose the wrist, allowing all hand rotations.
Printing materials don’t affect the actuators’ functioning – the design is scalable. “Choosing a filament over another changes the forces a GRACE can execute. A stiffer material can sustain higher pressures than a softer one, so it can lift higher loads to over 1000 times its weight.” elaborates De Pascali.
The most undersized samples produced are as heavy as 0.1 grams. Using the IIT method means spending more time on the design phase – mainly to study thoroughly the best way to print the muscle. As per the researcher, it’s all about learning how to use it. “Eventually, it’s not that different than playing with a LEGO box.”
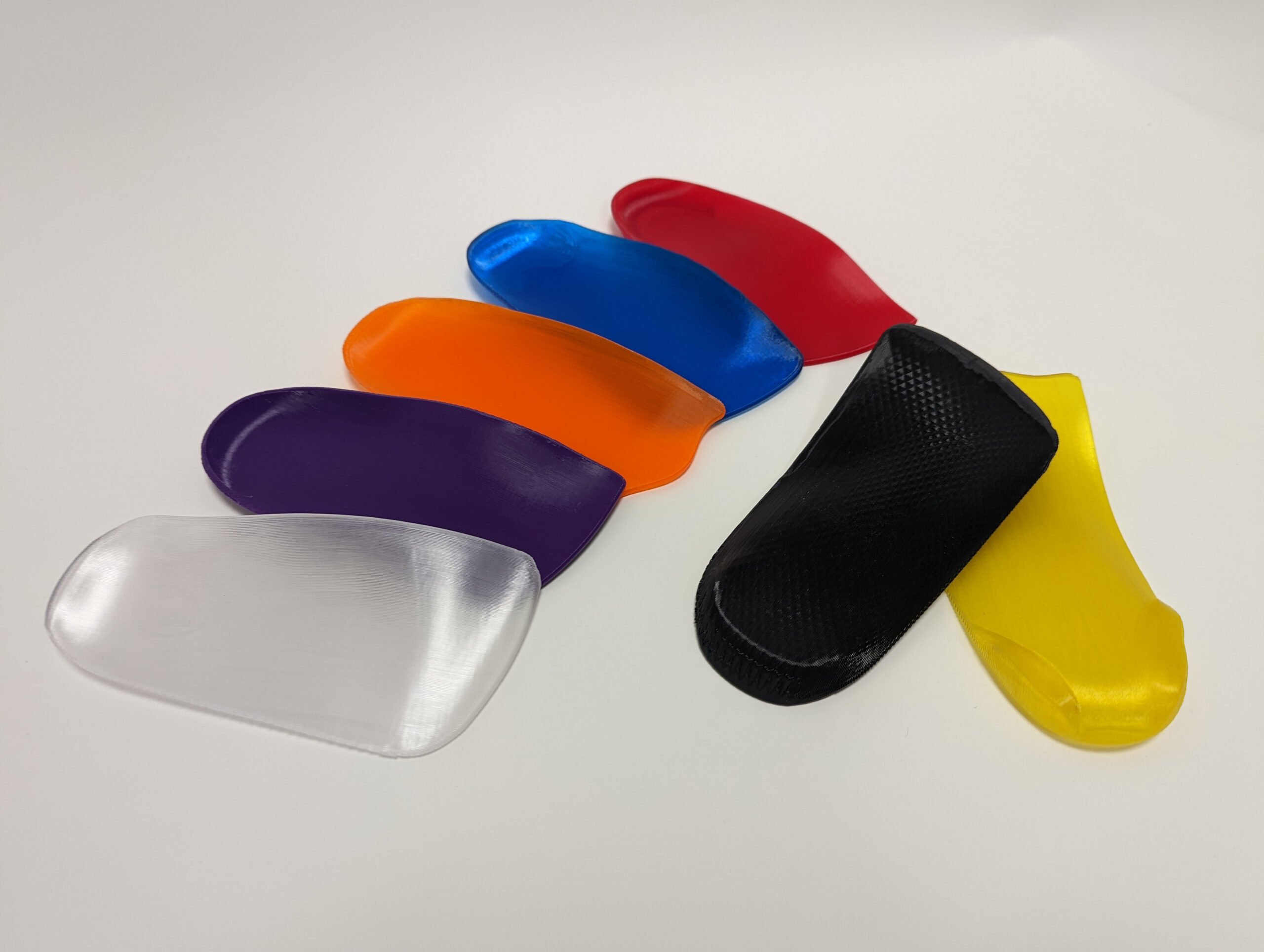
Ready to flex
McKibben-based concepts require assembling the tube and the mesh. Per contra, 3D-printing allows to have an – almost – ready-to-use muscle. According to De Pascali, such an aspect is particularly relevant.
“Joining the different components entails several problems. For instance, there’s the need for crafting an additional element to hold the tube and the mesh together as well as making sure that there are no holes. 3D printing allows doing that in the design phase. When printing is done, it’s all about polishing the excess material and sealing the pipes to the structure.”
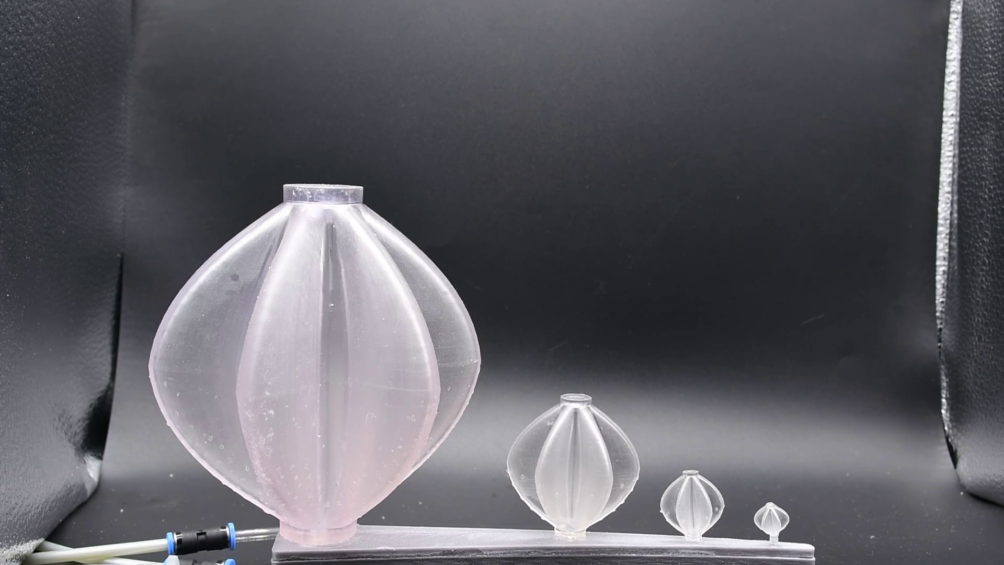
More to come
GRACEs target industry applications. In all those settings where loads as fragile as an egg have to be moved, or where electric arms can’t be used, PAMs come in handy. But there’s more in the IIT’s researchers’ minds.

“As part of a bigger EU-funded project – coordinated by Lucia Beccai – we are working on a robotic arm inspired by the elephant’s trunk. It will be made of thousands of GRACEs, all printed in one go,” says De Pascali.
In the meanwhile, the researcher printed other muscles resembling parallel and fusiform ones – respectively, such as the one in the thighs and in the biceps. Intended to offer freedom of modeling, IIT actuators aim to reshape pneumatic muscles up to the point of being integrated into human bodies.