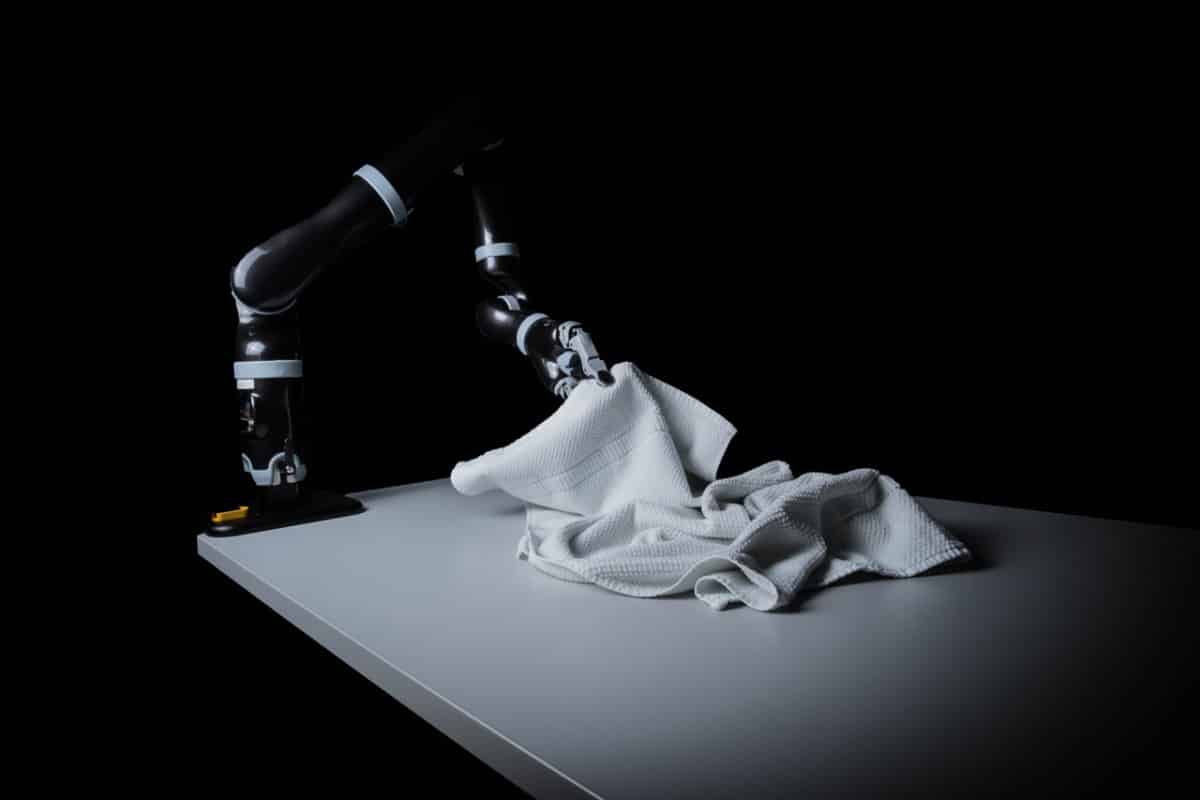
T-shirts leggen een lange reis af. Voordat ze in de winkel te koop worden aangeboden, reizen ze eerst van katoenplantages in de VS naar weverijen en ververijen in India. Vervolgens worden ze in Bangladesh genaaid. Ze belanden uiteindelijk na een reis van zo’n 40.000 km in de havens van Hamburg of Rotterdam. Afgezien van de productie komen er vooral tijdens het transport grote hoeveelheden broeikasgassen vrij. Lokale productie is echter nog steeds niet mogelijk in verband met de kosten. Dat kan in de toekomst veranderen. Want de pas opgerichte sewts – de naam is een samentrekking van het Engelse suit en to sew – wil textielproductie terughalen naar Duitsland. De productie wordt niet door mensen gedaan, maar volledig door robots. De drie oprichters Alexander Bley, Tim Doerks en Till Rickert presenteerden onlangs op de Tech Check in München een prototype voor de volautomatische verwerking van textiel als onderdeel van een industriële textielwasserij.

We spraken met Alexander Bley over de oprichting van sewts en de visie van het bedrijf.
Hoe kwamen jullie op het idee om de start-up op te richten?
Het idee was een geleidelijk proces. Twee van onze oprichters, Tim en ik, hebben tijdens de studie uitvoerig onderzoek gedaan naar vezelcomposieten. Centraal stond hierbij de lichtgewicht structuur van koolstof vliegtuigvleugels. Voor de productie hiervan worden de technische textielmaterialen, zoals koolstofweefsel, op elkaar worden gestapeld en vervolgens met hars geïnfiltreerd. Het doel van de studie was het automatiseren van de verwerking van deze materialen, die onstabiel van vorm zijn. Het was daarna de uitdaging om te voorspellen hoe dergelijke zachte materialen zich zouden gedragen in deze opstelling.
Tijdens de ontwikkelingsfase vroegen we ons af in welke industrieën zo’n oplossing van pas zou kunnen komen. Zo kwamen we bij de textielproductie. Vooral omdat we er alle drie van overtuigd zijn dat de reis die kleding vandaag de dag aflegt allesbehalve duurzaam is. Net als de productieprocessen: van verven tot naaien, alles wordt gedaan tegen zeer lage prijzen. Korte productieroutes zouden niet alleen interessant zijn in termen van emissiereductie, maar op de lange termijn zouden ze ook het opleidingsniveau in landen als Bangladesh kunnen verhogen door het wegvallen van laagopgeleid werk. Een soortgelijke situatie hebben we in Duitsland al meegemaakt door de productieomschakeling in de jaren vijftig van de vorige eeuw.
Hoe zien jullie de specifieke toepassingsmogelijkheden?
In de eerste plaats zien we de toepassingsmogelijkheden in algemene naaiprocessen, bijvoorbeeld van kleding, maar ook van stoelbekledingen voor auto’s of vliegtuigen. Op dit moment richten we ons echter op industriële wasserijtechnologie. Want nu staat er nog altijd een persoon aan de machine die het textiel sorteert op categorie en het vervolgens in de automatische strijkmachines plaatst. Onze ontwikkeling zou een kosteneffectieve, volledig automatische industriële wasserij mogelijk maken.
Wat maakt jullie product bijzonder ten opzichte van andere producten?
Eigenlijk wordt er al gewerkt aan de ontwikkeling van iets dergelijks. Een Amerikaanse start-up heeft zich bijvoorbeeld gespecialiseerd in het naaien van vloermatten en kussens. Maar de Amerikanen werken met een zogenaamd Cartesiaans portaalsysteem, dat wil zeggen, hun robots rijden op rails. Daarom kunnen ze alleen worden gebruikt voor hun specifieke toepassingsgebied.
Onze robot is daarentegen flexibel omdat hij producten van elkaar kan onderscheiden. We hebben daarvoor van tevoren verschillende textielsoorten gescand en geclassificeerd. Dit betekent dat onze robot dankzij AI kleur, oppervlak, materiaal en het product zelf herkent. Het kan bijvoorbeeld een servet van een kussen onderscheiden. Hij kent ook de materiaaleigenschappen en de buigstijfheid. Daarnaast hebben we punten uitgerekend aan de hand waarvan het textiel zonder rimpels kan worden verwerkt. Dankzij al deze achtergrondinformatie kan onze ontwikkeling met een veel grotere productvariabiliteit werken.
Wat was de grootste hindernis die jullie aanvankelijk moesten overwinnen?
Ik zou bijna zeggen dat de grootste hindernis was om de stap naar zelfstandig ondernemerschap te zetten. We hadden tenslotte allemaal een doctoraat kunnen krijgen. En tot kort voor de realisatie wisten we nog niet of we een beurs zouden krijgen.
Was er een moment dat jullie overwogen om het op te geven?
Nee, gelukkig niet. Maar we hadden onszelf ook een einddoel gesteld: ons privé-geld zou genoeg zijn geweest – zelfs zonder inkomen – voor ongeveer zes maanden. Als het na die tijd niet had gewerkt, hadden we het opgegeven. Gelukkig was dit niet het geval.
Wat was voor jullie het beste moment met betrekking tot de stichting, waar waren jullie trots op?
Er waren eigenlijk twee grote momenten. Een daarvan was toen we bij de notaris zaten en de akte van oprichting ondertekenden. We hadden een jaar aan onze robot gewerkt – maar dat was in een universitaire omgeving. En plotseling waren we ondernemers.
Het andere moment was half juli. Toen gingen we voor het eerst met ons prototype naar buiten tijdens de Tech Check van de Zukunftsrat der Bayerischen Wirtschaft zonder bang te zijn dat ons idee gestolen zou worden. We hadden namelijk al een internationaal octrooi aangevraagd. Het evenement was voor ons een bevestiging van het innovatieve karakter van onze ontwikkeling.
Wat kunnen we de komende jaren verwachten, met andere woorden: wat kunnen we de komende jaren van jullie verwachten?
Op dit moment richten we ons op de volautomatische wasserij. Dit betekent dat we werken aan de mogelijkheid voor onze robots om handdoeken en lakens in de wasberg te herkennen en ze zonder vouwen in een strijkmachine te plaatsen. Onze belangrijkste zorg hierbij is het vergroten van onze competentie op het gebied van volautomatische textielverwerking. We willen wat dat betreft eerst geloofwaardigheid creëren, voordat we de volgende stap zetten naar volautomatische kledingproductie. Ons doel is om de productieketen van industriële wasserijen voor 100% te automatiseren. De eerste producten zullen hier in november 2020 beschikbaar zijn. Onze volgende stap is dan rond 2023. Binnen deze termijn willen we het eerste volledig automatisch in München geproduceerde T-shirt op de markt brengen.
Wat motiveert jullie dagelijks?
De gedachte dat we over 20 tot 30 jaar terug kunnen kijken op ons eigen leven en er trots op kunnen zijn dat we de wereld een kleine stap verder hebben gebracht op het gebied van duurzaamheid. Kortom, het is de moeite waard om zelf een positieve impact te hebben gecreëerd.
Wat is jullie visie: waar zien jullie het bedrijf over 5 jaar en wat is jullie uiteindelijke doel?
Op de lange termijn is het onze bedoeling om in korte tijd en op regionaal niveau op maat gemaakte kledingstukken te produceren – onafhankelijk van maten als S of L. Dat wil zeggen, onze visie is dat de klant zijn eigen lichaam en maten opneemt door middel van bijvoorbeeld een foto op een mobiele telefoon en doorstuurt naar onze robot. De robot produceert vervolgens een individueel kledingstuk.
“Onze visie is de realisatie van volledig automatisch geproduceerd textiel op maat – om uiteindelijk de wereld duurzamer te maken.”