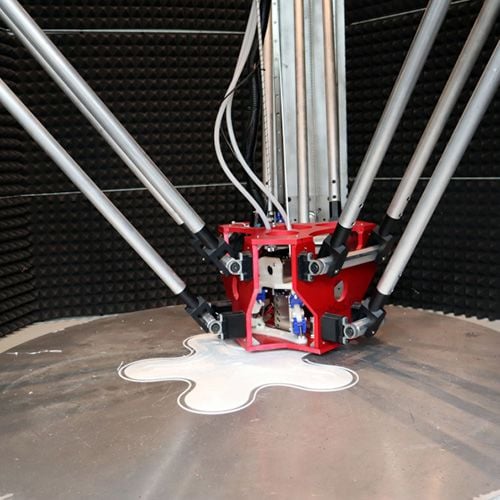
Het bouwen van efficiënte, kosteneffectieve en snelle prototypes wordt mogelijk met ‘s werelds grootste industriële delta 3D-printer. De vier meter hoge machine is ontwikkeld door de onderzoeksgroep van professor Yilmaz Uygun van de Jacobs Universiteit Bremen, meldt de universiteit in een persbericht.
In industrieën als de machine- en installatiebouw zijn regelmatig unieke onderdelen nodig, wat een uitdaging vormt voor deze industrieën; enerzijds zijn de onderdelen complex van structuur maar anderzijds zijn ze slechts in kleine hoeveelheden nodig. Conventionele fabricageprocessen zijn vaak niet geschikt voor de productie van dergelijke onderdelen. Het is vaak te duur, soms zelfs onmogelijk, om deze noodzakelijke onderdelen te produceren.
Binnen no-time ontworpen
Hier komt het project van professor Yilmaz Uygun en zijn team van de Jacobs Universiteit Bremen om de hoek kijken. Met steun van de Kieserling Foundation heeft het onderzoeksteam onder leiding van Serkan Özkan in zeer korte tijd ‘s werelds grootste industrieel bruikbare delta 3D-printer ontwikkeld. De printer maakt het mogelijk om op efficiënte wijze complexe onderdelen te produceren voor prototypes die zich nog in de testfase bevinden. Dit betekent dat hun ontwerp flexibel en economisch kan worden aangepast aan de testresultaten en indien nodig kan worden vernieuwd.
Reusachtige onderdelen
De 3D printer heeft een hoogte van ruim vier meter. Het printgebied heeft een radius van 1.5 meter en een printhoogte van 2.5 meter. De printerkop zweeft boven de drukplaat, bevestigd aan drie armen die een driehoek (delta) vormen. De printerkop kan door de armen in elke richting worden bewogen. Het printgebied dat hierdoor ontstaat, maakt het printen van uitzonderlijk grote onderdelen mogelijk.
De geprinte onderdelen worden momenteel gebruikt in verticale windturbines als onderdeel van een universiteitsproject. En er staan nog meer projecten op de planning. De printsnelheid ligt momenteel rond de 5 kg per uur, afhankelijk van de complexiteit van de gewenste afdruk.
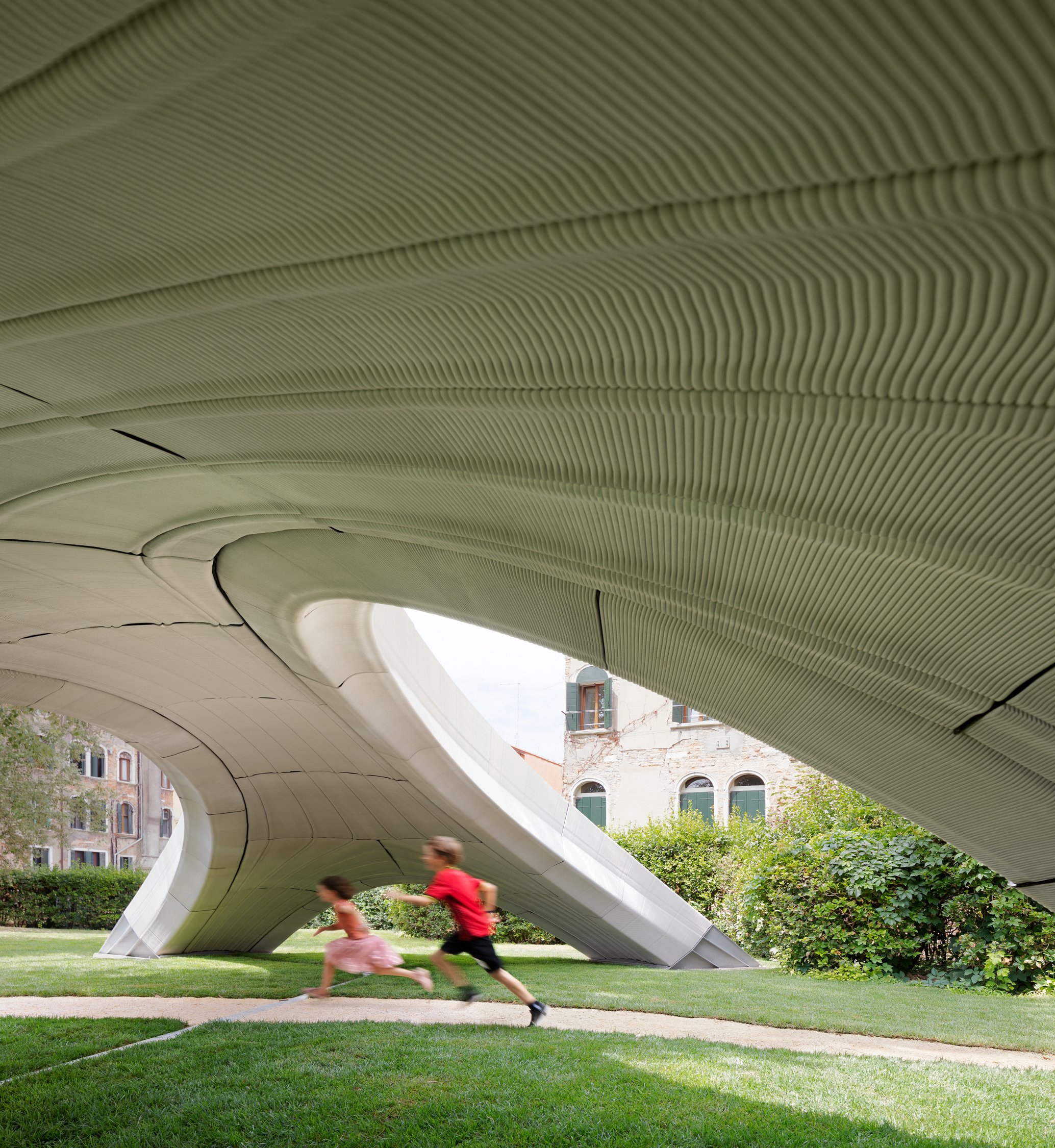
Pellets
Het printmateriaal bestaat uit conventionele kunststoffen zoals PLA, PET of ABS. Hier ziet Uygun in de toekomst veel potentie in. Overtollig materiaal zou kunnen worden versnipperd en als pellets worden gerecycled: “We ontwikkelen momenteel een pellet-extruder om pellets te kunnen produceren. Dit vermindert de koolstofvoetafdruk radicaal. Bovendien kunnen we de kosten verlagen, de toeleveringsketen veiligstellen en zorgen voor meer onafhankelijkheid van specifieke leveranciers en regio’s,” legde de hoogleraar uit.
Camerasysteem
Uygun en zijn team richten zich daarnaast op de verdere ontwikkeling van de kwaliteit tijdens het drukproces. Zo werken ze aan een camerasysteem dat het drukproces visueel bewaakt. Op de lange termijn moet “Honeycomb”, zoals de 3D-printer wordt genoemd, zichzelf corrigeren bij afwijkingen. “Ons doel is om Honeycomb direct in productie te nemen. We hebben verschillende ideeën om het printen te versnellen zonder dat dit ten koste gaat van de kwaliteit.” Het team onderzoekt het gelijktijdige gebruik van meerdere printkoppen met spuitopeningen van verschillende grootte die werken met verschillende snelheden. “Als dit lukt, zou het systeem direct kunnen worden gebruikt”, aldus Uygun.
Geselecteerd voor jou!
Innovation Origins is het Europese platform voor innovatienieuws. Naast de vele berichten van onze eigen redactie in 15 Europese landen, selecteren wij voor jou de belangrijkste persberichten van betrouwbare bronnen. Zo blijf je op de hoogte van alles wat er gebeurt in de wereld van innovatie. Ben jij of ken jij een organisatie die niet in onze lijst met geselecteerde bronnen mag ontbreken? Meld je dan bij onze redactie.