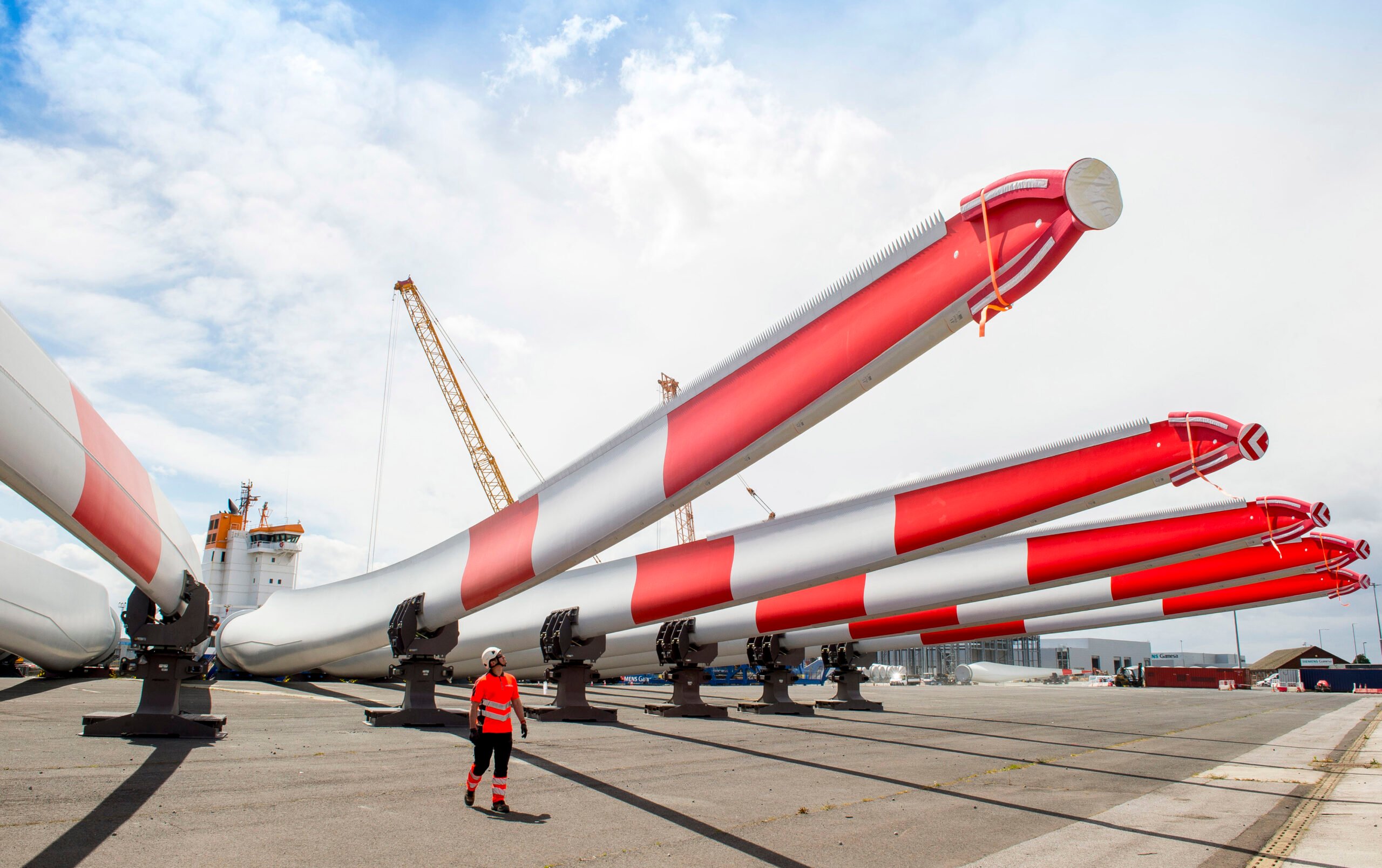
Een werkelijk duurzame samenleving gaat hand in hand met de circulariteit van materialen en energie. Als de elektriciteit die we gebruiken om onze autoโs aan te drijven afkomstig is van fossiele bronnen, is er nog steeds een belangrijk milieueffect. Hetzelfde geldt voor windturbines. Ze produceren wellicht tientallen jaren lang schone energie. Maar wat is het nut als hun volumineuze wieken als de molens zijn afgedankt op de vuilnisbelt belanden? Ondanks een lage koolstofuitstoot voor aan het net geleverde stroom- ongeveer 6 gram CO2-equivalent per kWh- vormen oude turbines een extra afvalbron. Een nieuwe kunsthars voor het binden van de componenten die worden gebruikt om rotorbladen te bouwen, effent de weg om deze volledig recyclebaar te maken.
Windbladen worden gemaakt van glas- en koolstofvezel. Die vezels worden laag voor laag over een kernmateriaal van hout of PET-gespannen en verhard met een epoxyhars. Dit wordt vezelversterkt composiet (FRP) genoemd. Door de kunsthars worden alle lagen en materialen onlosmakelijk aan elkaar gelijmd. Dat nu maakt het zo complex om uiteindelijk het materiaal voor hergebruik te scheiden wanneer de turbine het einde van zijn cyclus heeft bereikt.
Siemens Gamesa heeft een nieuwe kunsthars ontwikkeld die het gemakkelijker maakt de materialen te scheiden. Zonder dat de prestaties van de rotorbladen daarbij moeten inboeten. De eerste recyclebare bladen draaien al in het offshore windmolenpark van Kaskasi, Duitsland, dat wordt geรซxploiteerd door het energiebedrijf RWE.
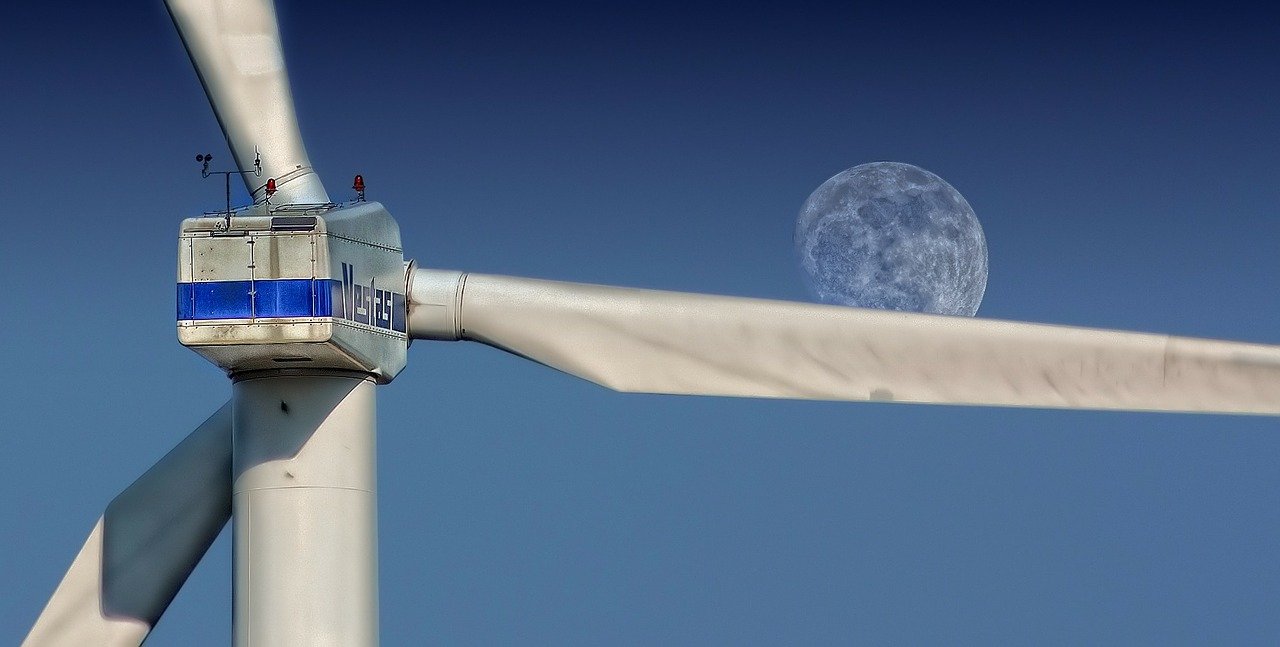
Steeds meer afval
Het recyclen van windbladen is een lastige zaak. Hoewel er creatieve oplossingen bestaan โ Siemens Gamesa hergebruikt er enkele als fietsenstalling โ belanden de meeste op de stortplaats. Andere onderdelen van windturbines kunnen daarentegen wel worden gerecycled. De toren is gemaakt van staal, dat talloze malen kan worden hergebruikt. Volgens een onderzoek van de Universiteit van Cambridge genereren windturbines als er geen goede oplossing gevonden wordt, tegen 2050 43 miljoen ton afval. Bovendien verbieden steeds meer landen het storten van afval. In Oostenrijk, Finland, Duitsland en Nederland is dat al het geval.
Zelfde eigenschappen
De nieuwe rotorbladen verschillen niet veel van de oude modellen. โEr was niet veel herontwerp nodig. De nieuwe kunsthars heeft dezelfde eigenschappen als de lijmstof die we gebruiken voor conventionele bladen. Bovendien blijven de productieprocessen en de levensduur van de bladen hetzelfdeโ, vertelt Harald Stecher, een blade materials engineer bij Siemens Gamesa.
Rotorbladen hebben een relatief eenvoudige structuur en weinig onderdelen. De zogenaamde ligger is het binnenste gedeelte. Deze is gemaakt van glasvezel en koolstof, met een harscoating. Twee schalen โ ook van glasvezel โ bedekken de liggers. De schalen en liggers worden vervolgens samengevoegd en gaan door een oven om ze samen te voegen tot รฉรฉn structuur.
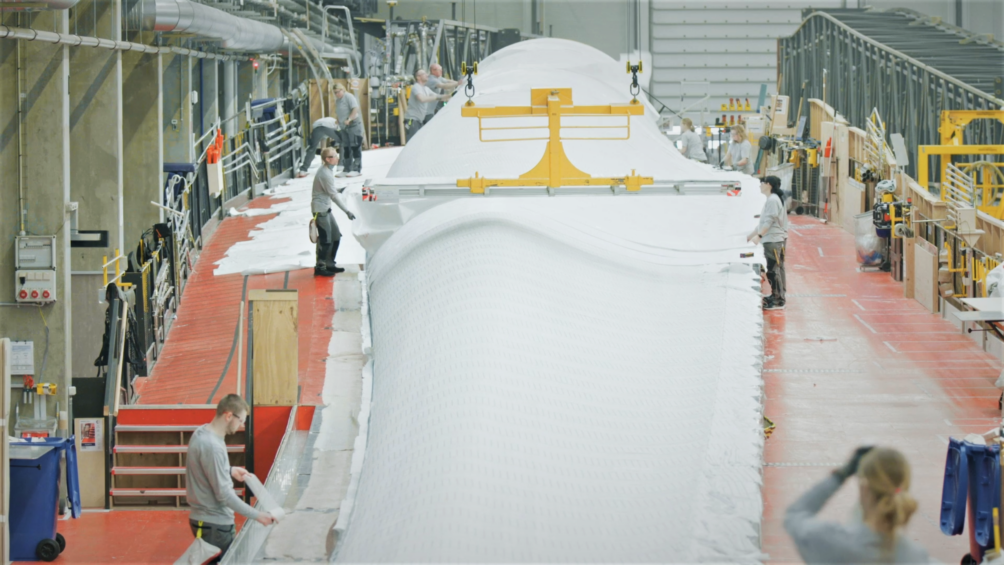
Deze procedure geldt voor alle soorten windbladen tot 110 meter lang. Siemens Gamesa-prototypes van recyclebare bladen zullen binnenkort oplopen tot 108 meter. Ze zijn geschikt voor zowel onshore als offshore windparken. Aangezien ze vergelijkbaar zijn met de conventionele bladen, blijven ook de onderhoudsprocedures voor de recycleerbare bladen dezelfde. Deze werkzaamheden hebben voornamelijk betrekking op het controleren op scheuren in de structuur en vereisen geen extra handelingen bij de recycleerbare bladen.
โIn potentie is het concept plug and play, maar we begrijpen nog lang niet het potentieel van het materiaal. We zullen het proces verder onderzoeken, we moeten nog spelen met temperaturen en infusietijden. Misschien zijn er nog andere voordelen waarvan we ons nog niet bewust zijn,โ voegt de ingenieur eraan toe.
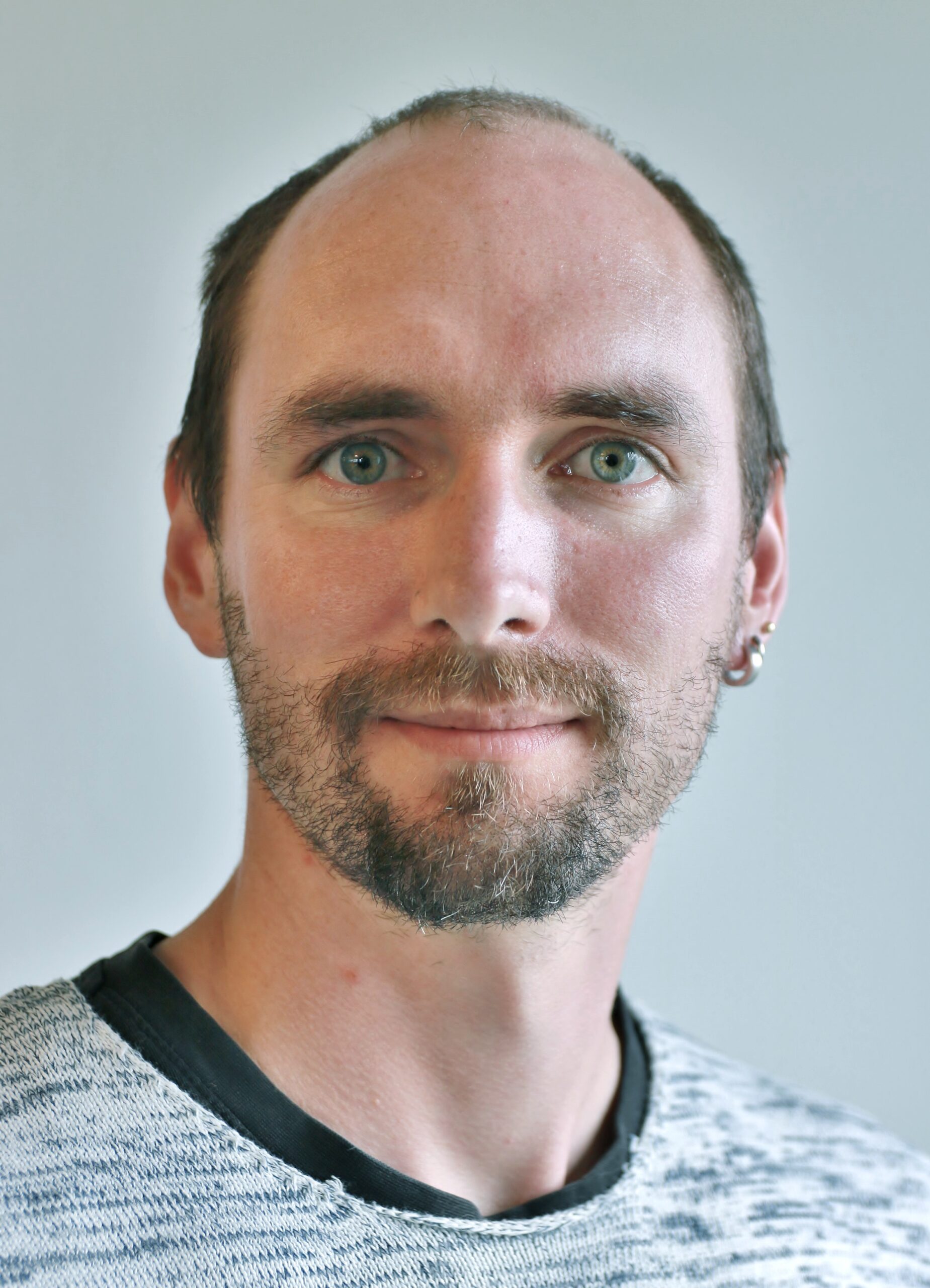
Harald Stecher
Ingenieur rotorbladmaterialen bij Siemens Gamesa
Verantwoordelijk voor de gebruikte kunstharsen.
Chemische reactie
Het verschil zit hem in de chemie van de hars. De chemische verbindingen kunnen gemakkelijker worden afbroken. Wanneer het tijd is om een windturbine te ontmantelen, wordt het blad eerst in stukken gesneden. Deze worden gedurende enkele uren ondergedompeld in verdund azijnzuur bij een temperatuur van tot 90ยฐC. In een geventileerde ruimte lost vervolgens de epoxyverbinding op en scheiden zich daardoor de materialen. Zo worden de vezels teruggewonnen.
Vervolgens wordt de resulterende oplossing gefilterd om ook de lijmstof terug te winnen. Dat kan gebeuren door verdamping of via neutralisatie. De stijfheid en sterkte zijn bijna gelijk aan die van het oorspronkelijke materiaal. Daarom moet het worden hergebruikt voor minder veeleisende toepassingen dan die van een windrotor. Bijvoorbeeld in de automobielsector.
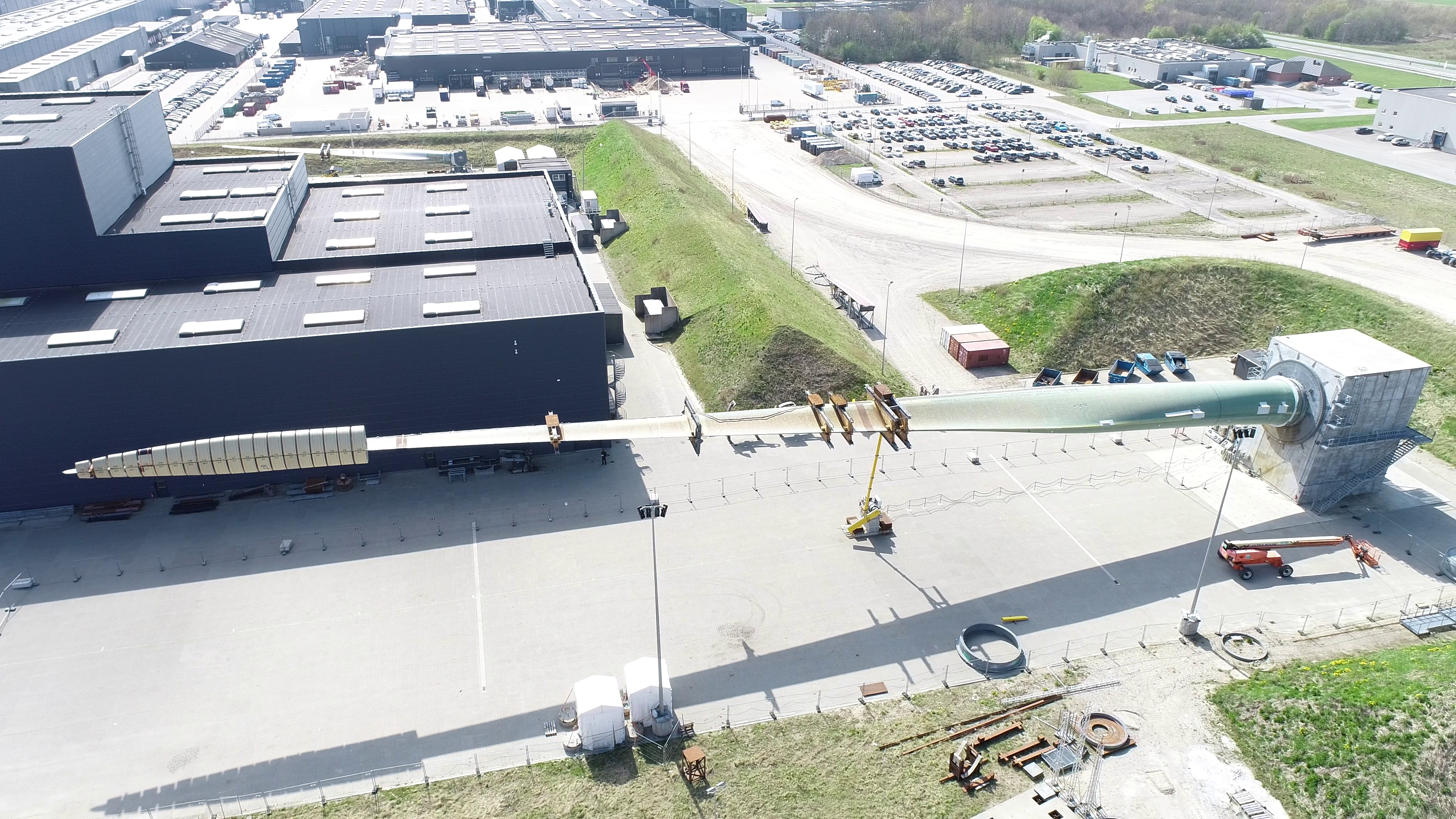
Volledig circulaire windturbines
Momenteel bevindt de technologie zich in de proeffase. Siemens Gamesa wil in 2040 100 procent recyclebare windturbines gaan produceren. Nu het probleem van het recyclen van de wieken is opgelost, is de gondel aan de beurt. Dat is de kast waarin de kritieke onderdelen van de turbine zijn ondergebracht, zoals de aandrijving, de generator en de tandwielen. Deze gondel is ook gemaakt van vezelcomposieten met een soortgelijke harscoating.
De kennis die bij het ontwerp van de recyclebare rotorbladen is opgedaan, komt dan van pas. Ook al is er nog veel onderzoek nodig omdat de onderdelen duurzaam en veilig moeten zijn. โWe hebben het hoofdprobleem opgelost. Er zijn echter nog kleinere dingen om rekening mee te houden, zoals turbinemagneten en andere kleine onderdelen die we moeten aanpakken om een volledig recyclebaar blad te krijgen,โ vat Stecher samen.