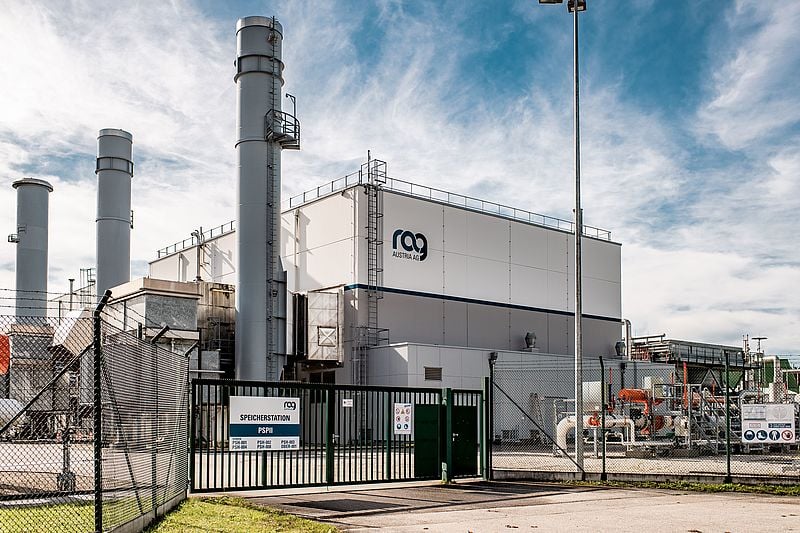
At the Montanuniversität Leoben ( the University of Leoben, one of the three Austrian Universities of Technology and specialized in mining, metallurgy, and materials, ed.) researchers are pursuing a unique approach in the production of hydrogen. Natural gas is broken down into hydrogen and carbon – without any emissions. The Austrian university has a long tradition in the field of metallurgy. By extracting carbon, it is making a scarce material available that enables revolutionary sustainable technologies in agriculture, the construction industry, and high tech.
The basis for the two-track approach to hydrogen production lies in the use of various pyrolysis processes developed at the Montanuniversität Leoben. The researchers work with a high-temperature bath of liquid metals that have a certain catalytic effect. Since solid carbon is produced as a by-product during this process, the hydrogen that is produced is free of emissions (CO2-free).
Also of interest: How CO2 from atmospheric air is converted into a high-tech raw material
Professor Dr. Peter Moser, who is coordinating the project within the framework of the Resources Innovation Center (RIC) Leoben, is expecting significant increases in demand for emission-free hydrogen over the next few decades. He regards pyrolysis as an interim solution until renewable electricity generation is fully established. He also wants to bring it up to an industrial scale together with Austrian industrial partners.
Our technology should be ready for use by 2030 at the latest and cut CO2 output by about a quarter. This means that we can bridge the gap between now and 2050. By that time, there should already be new technologies for renewable energies in place.” Professor Dr. Peter Moser.
CO2 baggage
The oldest process for producing hydrogen is steam reforming, whereby natural gas (CH4) is made to react with hot water during several stages. The reaction produces hydrogen and carbon dioxide (CO2). One problem with this technique is, however, that it generates CO2 emissions that are harmful to the environment.
Another technique used to produce hydrogen is electrolysis, which involves splitting electricity with water. Electrolysis is simple and environmentally friendly. Plus, it works solely with electricity from renewable sources, such as wind turbines or photovoltaics. However, its electricity consumption is high and renewable energies are only available to a limited extent, Moser goes on to explain. “Hydrogen production via electrolysis requires 180,000 kilojoules of energy per kilogram of hydrogen. In contrast, splitting natural gas requires only 45,000 kilojoules of energy per kilogram of hydrogen. Our process is, therefore, four times more efficient in terms of energy than electrolysis. This has a knock-on effect on the CO2 footprint.”
Everything we do comes with CO2 baggage. A hydrogen-powered car may drive around directly emitting low amounts of CO2, but both the production of that car and the hydrogen itself generate CO2 emissions. Even if the hydrogen is derived from electrolysis.” Professor Dr. Peter Moser.
Life cycle analysis
The project partners in the cooperation will also conduct a life cycle analysis in conjunction with the scaling of pyrolysis. From the boreholes for the extraction of natural gas to the transport of the natural gas via pipelines to pyrolysis. And last but not least, including the transfer of the hydrogen to consumers. In this way, they aim to make the overall picture of the CO2 footprint transparent and comparable with the impact of all other alternative production methods.
Initial estimates show that the hydrogen from pyrolysis is loaded with only about five kilograms of CO2 per kilogram. Whereas that from electrolysis using the current electricity mix in Europe is loaded with 30 kilograms of CO2 per kg of hydrogen. Moser: “If someday enough renewable energy sources are available, the hydrogen from electrolysis and from pyrolysis will then have roughly the same CO2 footprint. We, therefore, see our pyrolysis as a complementary technology that is capable of providing the industrial sector with the large quantities of hydrogen it needs.”
Pyrolysis
Pyrolysis has been recognized and researched for a long time but has not yet been advanced to the point where it could be industrially viable. Further pyrolysis-based research projects for hydrogen production are underway in Germany and the Netherlands. Nevertheless, Moser points out that the two-track production of carbon and hydrogen is rarely explored. Hydrogen that can be produced without emissions and solid carbon is considered a valuable raw material. The small quantities that are currently available come from graphite deposits and from the processing of plastics and other industrial processes.
When we split natural gas during pyrolysis, one part hydrogen and three parts of carbon are produced. If we were to target just hydrogen, as other consortiums are doing, that would put us at a disadvantage. Fortunately, our approach is advantageous for us, given that we are focusing on carbon production.” Professor Dr. Peter Moser.
In this pyrolysis process, the researchers from Montanuniversität are working with a large chamber filled with high-temperature liquid metal. As soon as they pass natural gas through it, the gas breaks down into carbon and hydrogen – into an extremely pure form. At present, this metal liquid is composed of nickel and copper. In the future, they plan to use gallium as a means to lower the temperature. Moser: “This will have a positive effect on the ecological balance sheet.”
Transitional solution
The main drawback of the process is the fact that it is reliant on natural gas, a non-renewable source. Moser is aware of this and argues that even with the increased use of natural gas, natural gas reserves would still last another 300 years or so. The extraction of hydrogen and carbon from natural gas is also a viable option that has a very low environmental impact. A further argument in favor of natural gas is that existing pipelines can be exploited. There is no need to build a new distribution network to transport natural gas to local energy companies and then on to consumers. The pyrolysis facility, which converts natural gas into hydrogen, would be installed at energy companies, thereby keeping any investment within reasonable limits. According to Moser, suchh a facility is relatively modest both in terms of size and cost.
He also sees a compelling argument in the two-fold advantages of the method, which eliminates emissions from the process and produces carbon at the same time. Moser: “Carbon is a very stable material that does not oxidize back into solid carbon matter and can, therefore, be used for sustainable approaches in the construction industry and agriculture. Collaborations with the University of Natural Resources and Life Sciences in Vienna, Austria, are already underway.
Industrial scale
In cooperation with research partners from the industrial sector, information for the design of the pyrolysis process on an industrial scale will now be compiled through a pilot plant. Apart from that, the aim is to test which metals can be used for the production of carbon and hydrogen. Alongside the scalability of the process, the focus is geared towards technically, economically, and ecologically sound options for recovering carbon. A life cycle analysis will be performed both for methane pyrolysis and the potential uses of carbon.
The project leader in this area of research is Robert Obenaus-Emler. Industry and project coordinator is RAG Austria, the largest gas storage and energy conservation company in Austria. The industrial partners are:
Also of interest: Energy from waste, simply produce it in your own basement