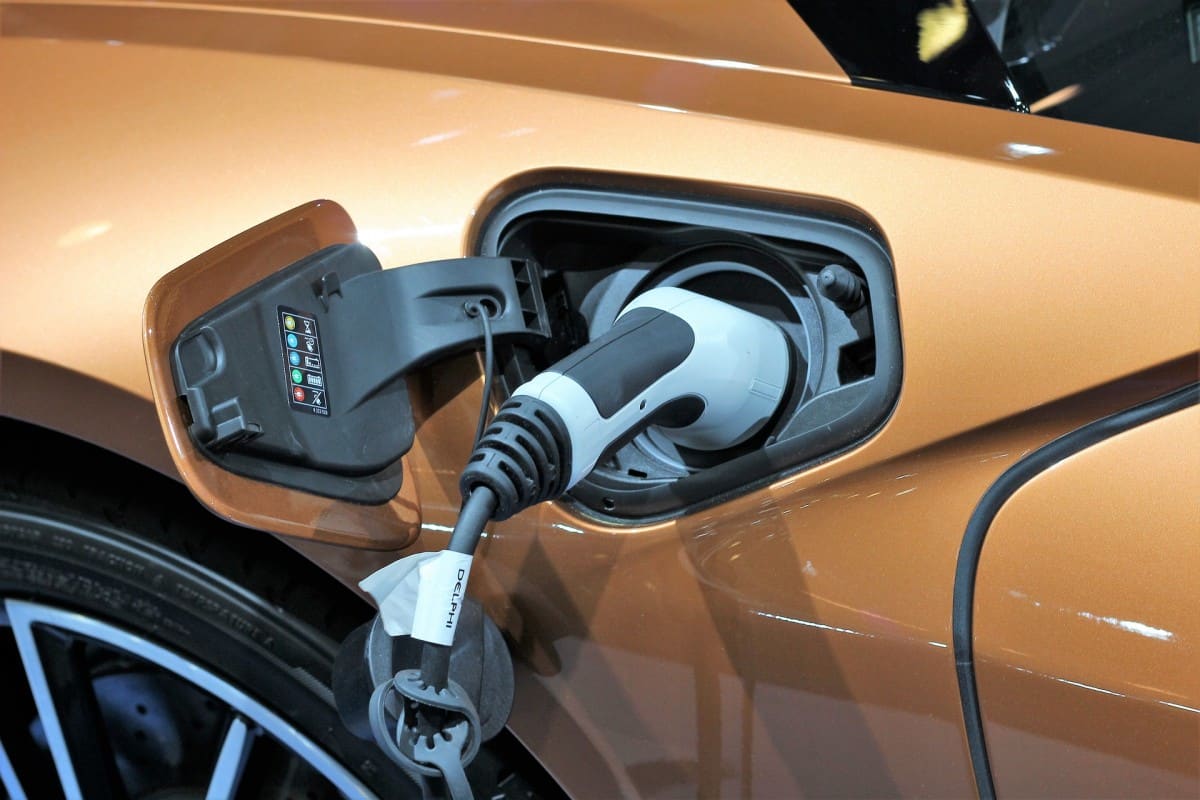
Electric cars are good for the environment. This is certainly a fitting statement โ especially if the electricity for the vehicles is not generated from coal-fired power plants. But what about electricity storage systems, the batteries, of the cars? There is still plenty of room to improve, in terms of production, performance and durability. Researchers at the Fraunhofer Institute for Material and Beam Technology IWS in Dresden have now found a way to tackle precisely these weak points in electric mobility.
So far, the major automobile manufacturers have purchased the cells for the batteries in Asia for several reasons. Asian technology companies have decades of experience in the mass production of battery cells, and a great deal of energy is consumed in production. And this is very expensive in Germany.
To avoid this in the future, the Dresden engineers have developed a better and also more cost-effective production process that saves energy costs and also makes toxic solvents superfluous in this process step: they coat the electrodes of the energy storage cells with a dry film instead of liquid chemicals.
โOur transfer process for dry coating aims to noticeably reduce the process costs in electrode coatingโ, emphasizes Dr. Benjamin Schumm, project manager at the Fraunhofer IWS. โThis enables manufacturers to dispense with toxic and expensive solvents and save energy costs during drying. In addition, our technology also makes it possible to use electrode materials that can hardly or not at all be processed wet-chemically.โ

For future batteries with higher energy density, however, exactly these materials will be needed. โFor all these reasons, we believe that our technology can help to make internationally competitive battery cell production in Germany and Europe possible.โ
End of the Classic Wet Chemistry?
In the production of cells, battery electrodes have until now mostly been coated using a complex wet-chemical process. The active materials, which will later release the stored energy, were first mixed with special additives to form a paste. Since not only expensive but also toxic organic solvents are added here, expensive precautions for occupational safety and reprocessing are necessary to protect factory workers and the environment. After the paste has been applied to thin metal foils, a very electricity-intensive drying process takes place. Dozens of meters of heating facilities dry the coated foils before they can be further processed.
These environmentally harmful and expensive steps are eliminated in the dry coating process because the active material is mixed with binding polymers. This dry mixture is processed by rollers into an electrode film about 100 micrometers thick. The film is then applied to an aluminium foil to form the battery electrode.
โIn this way, we can also process materials for new battery generations in which classical processes failโ, estimates Benjamin Schumm. โThese would include, for example, energy storage devices that use sulfur as an active material or so-called solid-state batteries that use ion-conducting solids instead of flammable liquid electrolytes.โ
โThese batteries will be able to store more energy in the same volume as todayโs lithium-ion batteriesโ, says the Fraunhofer IWS scientist with a view towards the future. โHowever, these solid electrolytes can lose their function in contact with solvents. A solvent-free coating process is therefore much more suitable for producing these storage media.โ
According to their own statements, the Dresden researchers have already achieved a milestone in the manufacture of solid-state batteries: they made it possible to โmanufacture electrodes using dry film processes with extremely low binder contents.โ

Pilot Plant in Finland
Together with industrial partners, the scientists now want to refine the processes and thus help them to achieve a breakthrough. In the โDryProTexโ project funded by the German Federal Ministry of Education and Research (BMBF), they are jointly developing the dry transfer process for electrode coating. In this project, material, process and plant developments are being promoted that will โenable process design for dry electrode production on an industrial scaleโ. โBenjamin Schumm is convinced that the process has the potential to replace conventional processes for paste-based electrode production in the long term.
In a pilot plant in Espoo, Finland, dry electrode production has already begun. โThe demand for our technology is high, also in Germanyโ, Schumm reports. Electrode films on a laboratory scale can already be coated continuously at several meters per minute, thus demonstrating the potential for scaling up to production scale.
On November 18 and 19, 2019, the Fraunhofer IWS in Dresden will host the โCarbon Electrode Materialsโ and the โLithium-Metal-Anodes: Processing and Integration in Next-Generation Batteriesโ to inform about the โBattery of the Futureโ.
Also interesting:
Experts Reveal: Electric Car Study by Hans-Werner Sinn is Nonsense
German Startup Chargery Offers Mobile Charging for Electric Cars