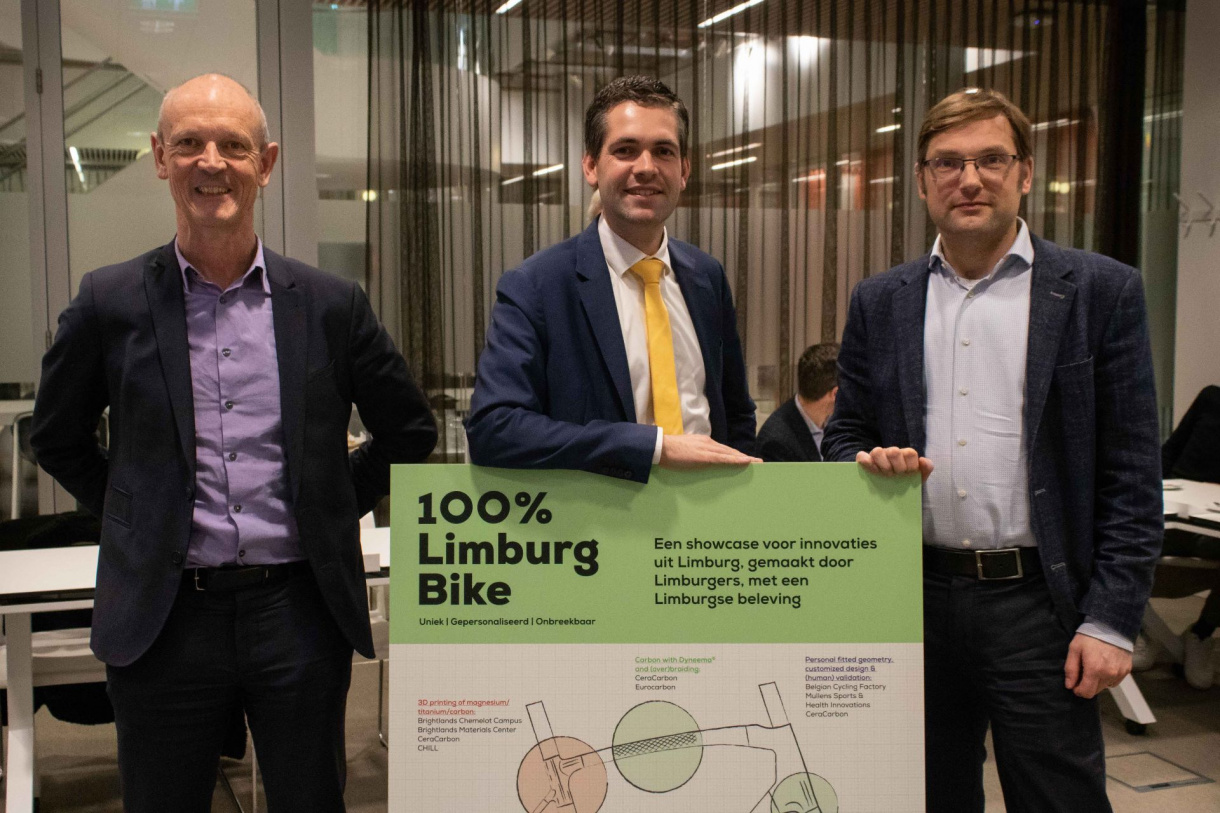
A consortium of SMEs from the Dutch province of Limburg and companies at Brightlands Chemelot Campus is developing an unbreakable lightweight road bike, which is made one-by-one, entirely to the wishes of the individual user. The first prototype is scheduled to be ready in about half a year. But how much a cyclist will have to pay for this Limburg innovation product is still unclear: that will only be determined after the construction of the prototype.
Although it has all the characteristics of a bicycle as there are many of them in hundreds of variations all over the world, the inventors of the 100% Limburg Bike still like to call their product “typically Limburg”. That’s because, they say, it was conceived from a local market need but above all uses the innovative knowledge and skills present in Limburg. The consortium (consisting of CeraCarbon, Mullens Sports & Health Innovations, Belgian Cycling Factory, Eurocarbon, Kembit, Brightlands Materials Center and Chemelot Innovation and Learning Labs) is not yet officially a start-up, but that could just be the case. We spoke with the man who, for the time being, prefers to call himself project leader rather than CEO, Menno Smeelen. “This will soon be a very special bike that meets the requirements of the UCI and all ISO standards. And we’re bringing it to the market from Limburg.”
How did you come up with the idea for the Limburg Bike?
At Brightlands Chemelot Campus, we were looking for a way to enable knowledge institutes to collaborate with manufacturing companies in the field of innovation, thereby strengthening the regional economy. In addition, a certain need has been identified in the market when it comes to special racing bicycles. Figures show an increase in the number of sportive cyclists. Sport is an important means to work on your health. On top of that, Limburg has a warm heart for cycling, which is, of course, a bonus. From that perspective, we have thought about an innovative racing bike as a product and as a showcase.”

What’s so innovative about this bike?
This has to do with, among other things, the materials and special 3D printing technologies. CeraCarbon, one of our Brightlands start-ups, will soon play a central role in the production, which is derived from the exact measurements of the cyclist on each racing bike. Precision work, because that’s what determines the dimensions of the frame. The materials used are titanium, sealed magnesium and carbon fibre. A combination of carbon and Dyneema fibres ensures optimum strength and stiffness, making the front fork absolutely unbreakable. Another special feature is that the frame and joints are glued together. To this end, a sustainable biobased glue is still being developed. The development of thermoplastic resin will ensure that the carbon becomes recyclable. These are techniques that are also relevant in the aircraft and automotive industries, so it is possible that our innovations will soon find their way into these sectors. Special braiding technology ensures the right density and direction of fibres. All this makes the road bike safe. We are very proud of this. And there’s something else special about this road bike that increases safety: sensing.
Sensing?
Our sensing system checks the forces to which the bicycle is subjected. When you bump into something on such a lightweight bike, it is not always possible to tell from the outside whether something has been damaged. Sensing also detects invisible damage. This can prevent a lot of misery. The fibre sensing is actually a development in which the carbon fibres themselves are given a sensoring function. You can then measure, as it were, the resistance and thus also whether there is damage to resin or carbon fibres. This sensing functionality is developed by the Brightlands Materials Center and the translation of the data into a working application is done by Kembit.
But because of the materials you use you claim that the bike is unbreakable anyway, so how useful is it to add a sensor to prove that?
The Dyneema fibres do indeed prevent the frame or fork from breaking, which greatly increases safety. For example, if you remember the crash of Dylan Groenewegen last year in the Tour de France, that wouldn’t have happened with our material. However, the carbon and resin can still be damaged without visible signs, which reduces the performance of the material and requires a bike change or repair, even if you can safely finish your ride. This sensing function can tell you this. The bike is also a showcase for innovations, and the sensing function itself can also be seen separately, so it can be used more widely in combination with carbon. In the case of invisible damage that can result in breakage, the user can be warned whether or not it is safe to cycle on. But I mainly see the spin-off to automotive and aviation, that is the real growth market for this application.
What’s your goal with the 100% Limburg Bike?
We want the prototype to be ready in six months. Then we can also say more about the price a user will have to pay for the bike. Ultimately the bicycle should also become a symbol for Limburg as a region of innovation and cycling.
Read more stories of start-ups from Europe here.