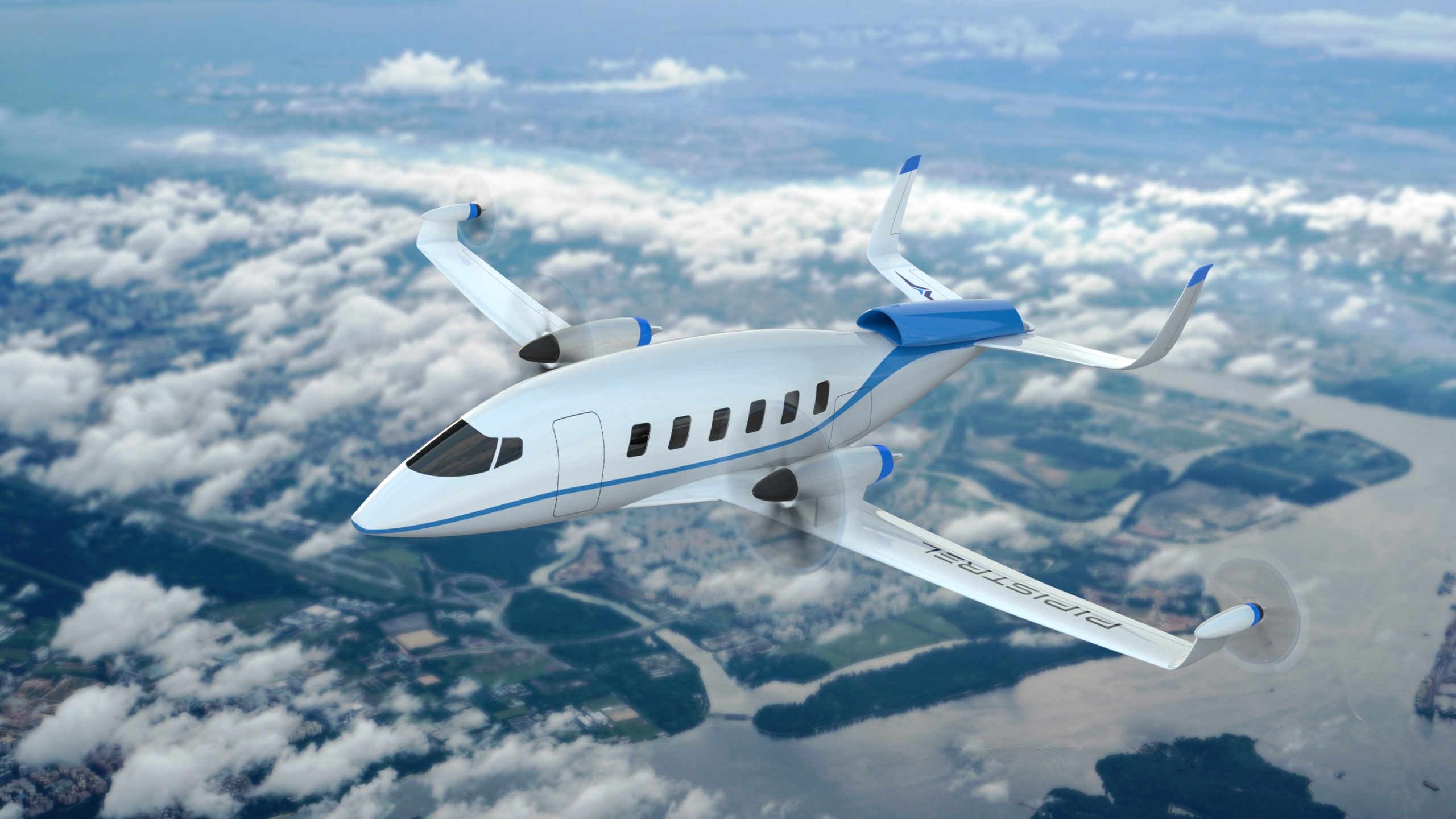
Aviation is the fastest growing transport sector and experts expect this trend to continue post-pandemic. According to the International Energy Agency (IEA), aviation already contributes around 2.5 percent of global CO2 emissions to man-made climate change. If the EU’s Clean Aviation Roadmap is to be adhered to, there is an urgent need for action. It foresees that the first hybrid-electric aircraft should take to the skies in 2035.
Electrification of aviation
As in the automotive industry, the aviation industry wants to switch to renewable energies. Electric propulsion solutions are the most promising. The solid-state battery is seen as the ideal battery solution in both sectors. While the first cars with solid-state batteries are expected to appear as early as 2025, research in aviation is still in its infancy. This is due, among other things, to the disproportionately higher requirements for energy density and system reliability.
Also of interest: Tomorrow is good: Super batteries could cover a range of more than 1000 kilometers
“The electrification of aircraft began with secondary systems such as de-icing or actuator systems,” explains Dr. Helmut Kühnelt, a researcher at the Center for Low-Emission Transport at the AIT Austrian Institute of Technology. He points to the Boeing Dreamliner 787 launched in 2011, where bleed air systems as well as pneumatic and hydraulic systems were electrified for the first time. “But now we’re talking about the electrification of the powertrain, and that’s where development is still pretty much at the beginning,” the researcher says.
Battery hybrid solutions
At AIT, problems are approached in a holistic manner. Research is currently being carried out in three European projects which are advancing the electrification of aviation: IMOTHEP, ORCHESTRA and SOLIFLY. The focus is on battery-hybrid solutions aimed at the regional aircraft segment for around 50 passengers. Once aviation-grade battery cell technologies are available, this would be the fastest solution to implement on the market, explains Kühnelt.
He himself heads the SOLIFLY project, which aims to develop the structural battery for aviation applications. The structural battery comprises components that have both mechanical and energy storage properties. As such, it has the potential to reduce weight and can increase the overall system efficiency of aircraft. It will probably not be possible to use this new type of energy storage system for the powertrain, explains Kühnelt. But in the electric aircraft of the future, he says, there will likely be not just one energy storage solution, but a hybrid system drawing on different energy sources.
Structural battery
The project tackles the issue of the battery concept and structural integration. It will also lead to a first-time demonstration of the novel system in an aerospace-relevant component. The SOLIFLY team can initially draw exclusively on academic fundamentals since the investigation of targeted aerospace applications is a first, says Kühnelt. Actual expectations for the structural battery will also be incorporated via industry partners.
The researchers are building on existing approaches to develop two different battery concepts and compare their performance. Both concepts are based on semi-solid-state batteries in which the electrolyte consists of an open-pore polymer matrix and an ionic liquid. The latter is a non-flammable salt that is safer than conventional liquid electrolytes. The electrolyte must be optimized. Current active materials with high energy density are used for both the cathode and the anode.
In one of the two battery concepts, active material for coating carbon fibers will be used. As an anode, carbon fibers could also serve as a current conductor and structure if uncoated. This is also the circumstance to which the unconventional choice of semi-solid-state battery is owed, Kühnelt says. In the implementation, carbon fibers are used as structural current conductors on the anode and cathode sides. The coatings are then used for energy storage. In the second battery concept, the material will be formed into thin battery cells and then integrated into the structure in the carbon composite.
The integration problem
When integrating the battery concepts, it is important to avoid premature damage. Concepts for connecting the structural element and energy storage device are developed and subsequently optimized with computer models. “The two battery concepts have different degrees of integration, but might also be suitable for different applications,” Kühnelt explains.
The energy-storing component is exposed to high static and dynamic loads in the application which can damage the battery. In addition, different zones of the component are exposed to different types of loads. The researchers are therefore investigating which areas of the component are best suited for integration with energy storage devices.
Energy must be supplied to and discharged from the cell integrated in the structure. This requires electrical conductors. These will probably not be cables, but electrically conductive strips. Kühnelt says: “Here, too, one challenge is to integrate the electrical conductors into the structure in such a way that no premature damage occurs.”
Industrialization
The components in which the structural battery can be implemented must also be researched. Relevant applications will be identified together with industrial partners. The researchers are initially concentrating on the interior, meaning that factors relating to the outer skin, such as foreign object impact and lightning protection, are no longer relevant. However, the structural battery should in any case be located close to the device to be powered in order to minimize electrical connections.
The technical research goal will be achieved when the developed technology can be integrated into a demonstrator, its structural and electrical performance characterized, and is comparable to a conventional panel. The demonstrator in this case is a stiffened panel that represents a standard component and has a size of 40 by 80 centimeters.
In addition, the researchers will determine whether the production processes can actually be industrialized and what it would take to industrialize the structural battery. To this end, a technology roadmap and a technology readiness level scale-up strategy will be created.
Bridge technology
Initially, the project will pursue a semi-solid-state approach. However, after further technology development steps, it should be possible to integrate solid-state batteries in the future. Unlike conventional lithium-ion batteries, solid-state battery technology does not require liquid electrolytes.
High-performance batteries that can be integrated into commercial aircraft must first be developed first, although the energy densities required by the powertrain are not yet available, either. But it will take much longer before the structural battery is researched, says Kühnelt. At the same time, aircraft construction must also be reconsidered, as the AIT researchers are doing in the IMOTHEP project, for example. The researcher hopes that the two development strands can be brought together by 2030. If that happens, then the EU’s ambitious Clean Aviation Roadmap can be met and the first hybrid-electric aircraft can take off in 2035.
About the project
The project name SOLIFLY is short for Semi-Solid-state LI-ion Batteries FunctionallyLY Integrated in Composite Structures for Next Generation Hybrid Electric Airliners. The AIT researchers are conducting research in collaboration with the aeronautics research centers in ONERA, France; CIRA, Italy; the University of Vienna, Austria; the University of Naples, Italy; and the mid-sized company CUSTOMCELLS Itzehoe, Germany.
Also of interest: Aviation industry to European Commission: ‘money is needed to develop zero-emission aircraft’