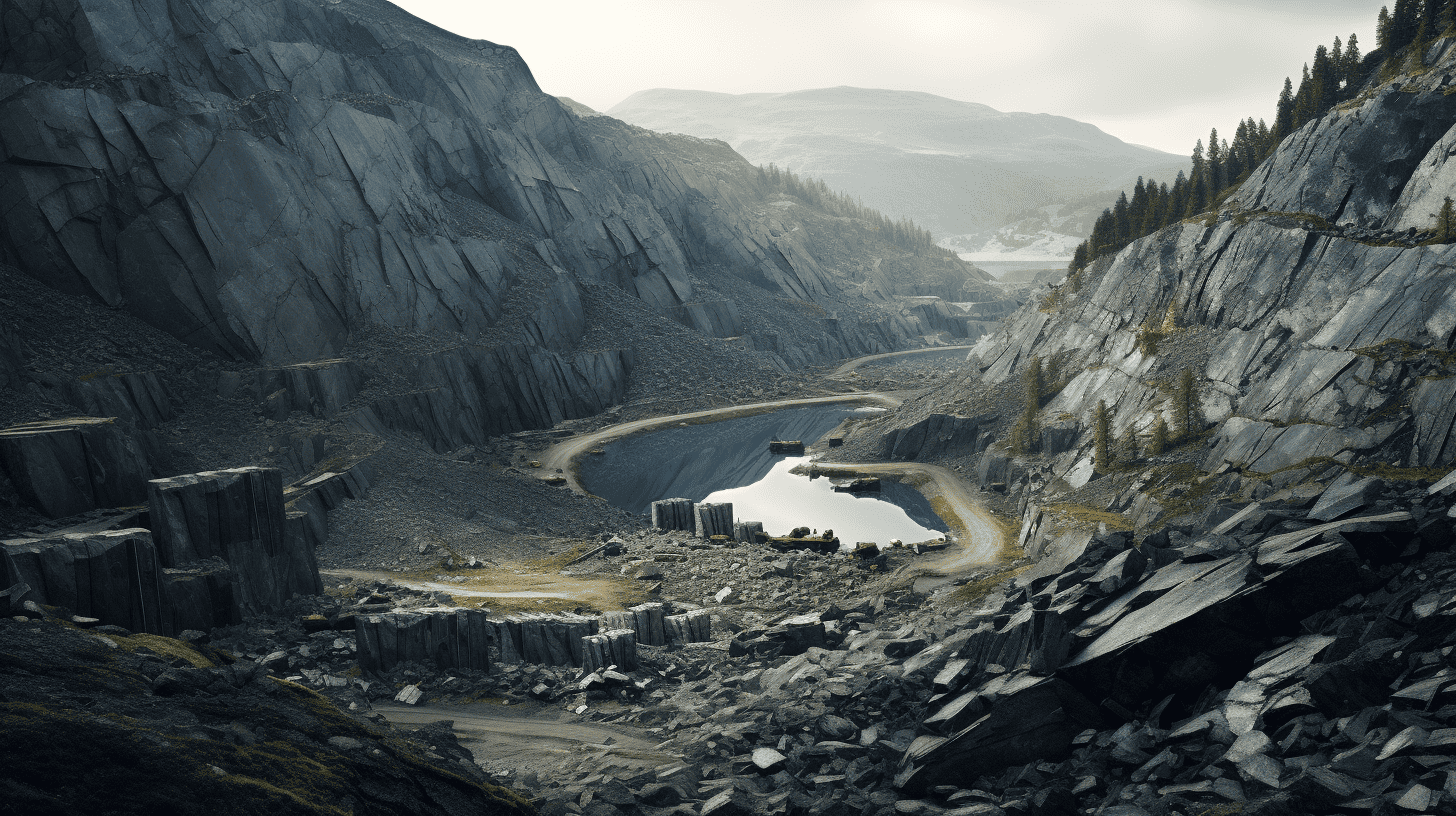
Permanent magnets, also known as supermagnets, are essential in manufacturing a wide range of state-of-the-art products, including electric cars and wind turbines. To create these magnets, crucial in the energy transition, several ‘rare earth elements’ (REE) are needed. Much of this nowadays comes from China, which hinders Europe’s desire to become strategically autonomous in the energy transition. The Fen Carbonatite Complex, near the Norwegian village of Ulefoss and created 580 million years ago when carbonate-rich magma formed a volcanic feeder pipe, might be part of the answer the continent has been looking for.
- Rare earth elements are needed for a wide range of modern products, from wind turbines to smartphones and electric cars.
- To reach strategic autonomy, Europe needs to build a supply chain for rare earth elements.
- The Fen deposit in Norway can potentially serve generations with the rare earth elements the world needs for a more sustainable future.
The Fen deposit can potentially serve generations with the REEs the world needs for a more sustainable future. Being located in Europe, Rare Earths Norway (REN) aims to help achieve the EU’s ambition of reducing CO2 emissions with 55% by 2025 and becoming climate-neutral by 2050. The Fen deposit is said to be at least 30 times as big as the one recently found in Sweden, which already claimed it could make Europe fully independent from China.
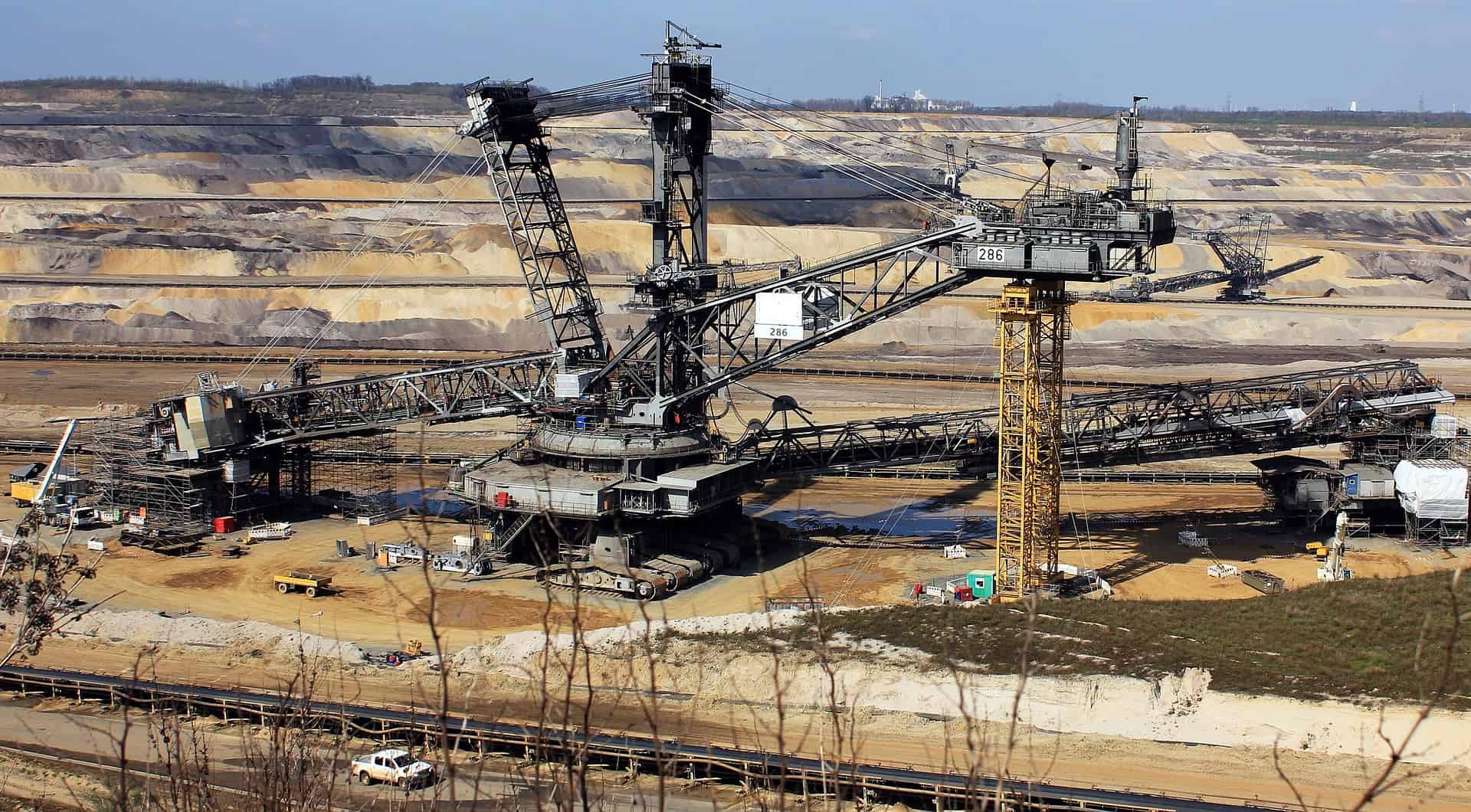
REN, established in 2016 to develop the Fen Complex, promises to dig up the raw materials in a sustainable way. “In developing the deposit, we commit to using production methods that minimize adverse environmental impacts and climate footprint in compliance with statutory obligations and society’s expectations of responsible industrial players”, the company website states.
REN will produce a mixed rare-earth concentrate that can be processed for use in various applications and industries, with permanent magnets using neodymium and praseodymium being the most important end market. These magnets are vital components in most modern high-tech products, including electric cars and wind turbines. The REEs help make the magnets lighter and more powerful.
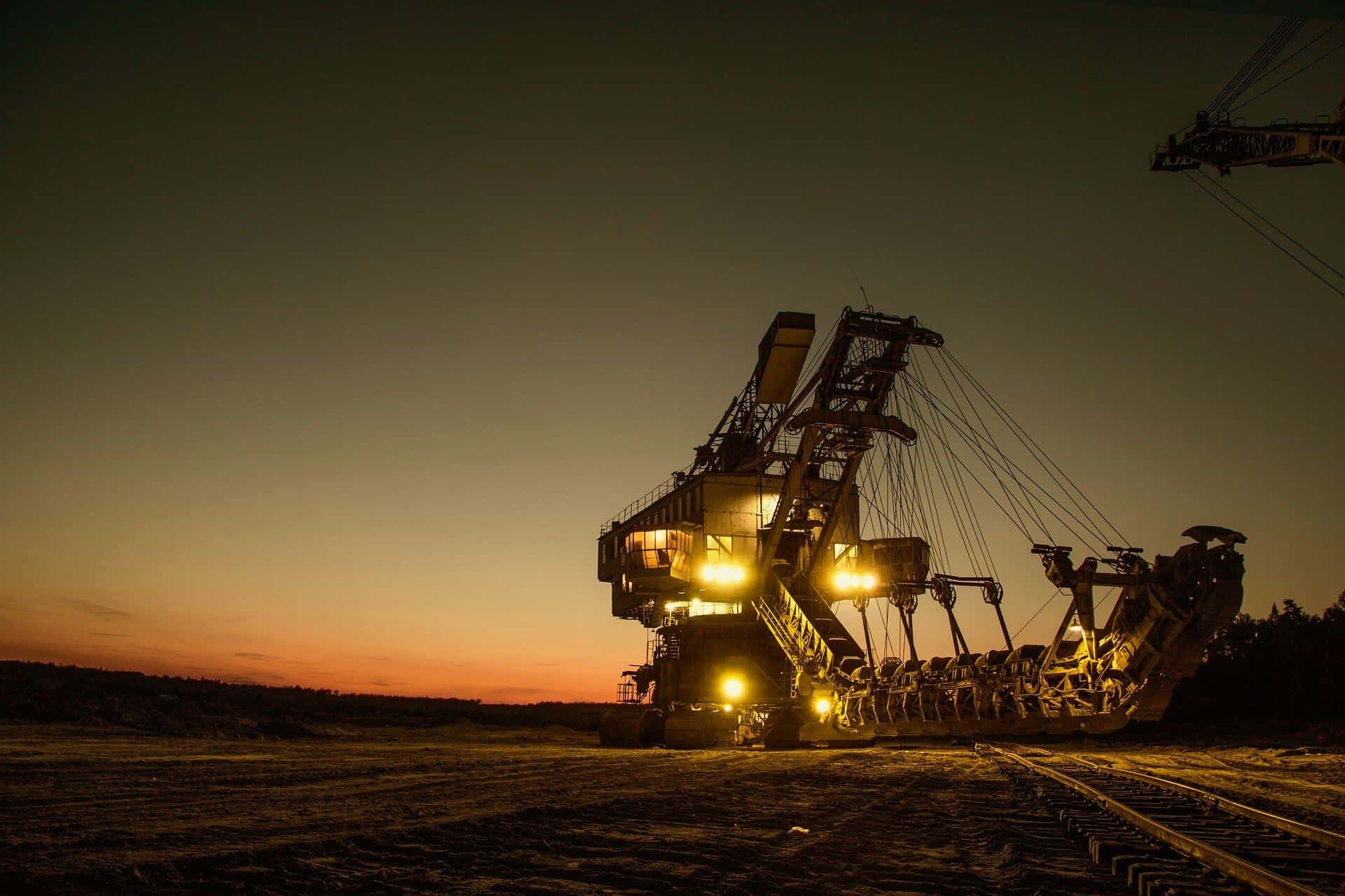
From mining to magnet
The process from mine to magnet consists of six stages, the first three of which REN will manage. The company is in discussions with other industrial players to set up a complete value chain to serve the European industry with permanent magnets. The six stages:
1. Mining
Carbonatite ore from the Fen deposit will be extracted from an underground mine, crushed, and transported to the processing facility.
2. Beneficiation (mineral processing)
Through milling and flotation, minerals with rare earths are separated from other minerals to produce a mineral concentrate for further processing.
3. Hydrometallurgy
The mineral concentrate is dissolved in a chemical process, and the rare earth elements are precipitated as a mixed rare earths concentrate.
4. Separation
The mixed rare earth concentrate, containing up to 17 rare earth elements, undergoes a complex process to separate and purify the various rare earth elements as oxides.
5. Metal production
The oxides are transformed to metals through an electrolytic process and mixed with iron metal to form alloys.
6. Magnet production
The REE alloys are processed and shaped through heat treatment or moulding and then magnetized. These magnets are used in a wide range of applications, from consumer electronics to electric cars and wind turbines.
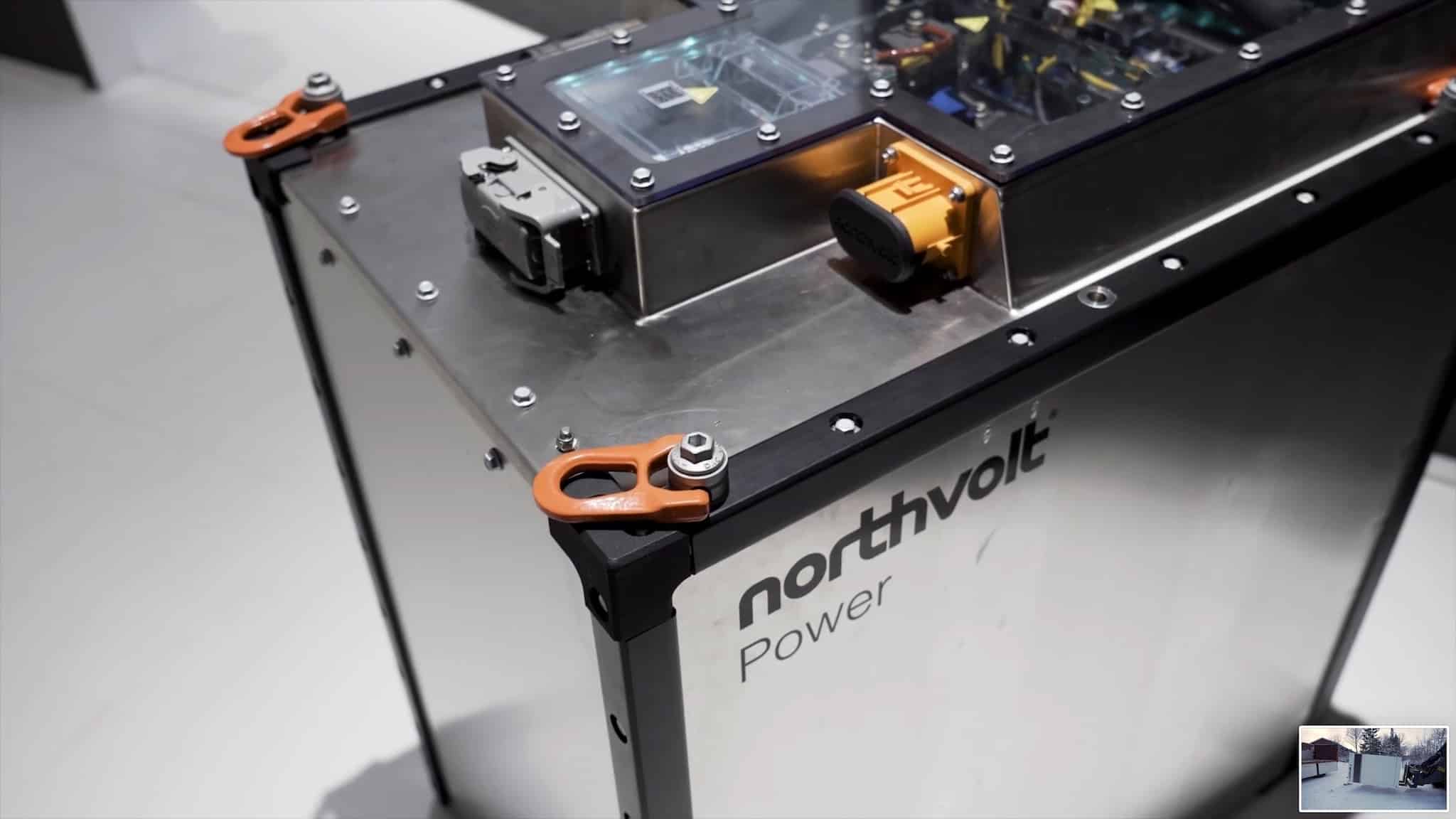
Volcanic feeder
The Fen Carbonatite Complex is what remains of the volcanic feeder pipe of a 580-million-year-old volcano with carbonate-rich magma – known as carbonatite. Over millions of years, the volcano has been eroded and can no longer be seen above ground. The circular feature of the volcanic pipe is approximately 2 km in diameter. It contains several types of carbonatite rock with varying mineralogy and geochemistry.
The part of the Fen Carbonatite Complex consisting of FDC covers an area of approximately 1.4 km2 and has been drilled to a depth of 1000 meters. Building on information from the county council’s geological adviser and Geological Survey of Norway, an exploration target of 1.4 – 3.3 billion tonnes has been set. Neodymium and praseodymium, important constituents in permanent magnets, account for 15 – 25% of the REE found at Fen.
Rare earths
Rare Earth Elements (REE) are a group of 17 metallic elements consisting of the 15 lanthanoids in the periodic table, in addition to yttrium and scandium. Based on their atomic masses, REEs are often classified as light rare earth elements (LREE) or heavy rare earth elements (HREE).
Their special physical and chemical properties make them key in manufacturing most high-tech products – including smartphones, hard drives, medical devices, defense applications, and renewable energy technology.
The rare earth elements neodymium (Nd), praseodymium (Pr), and dysprosium (Dy) are needed to produce high-strength permanent magnets used in electric traction motors and wind turbines.
Rare earths are found abundantly in nature, but they rarely occur in economically viable amounts and are difficult to process.
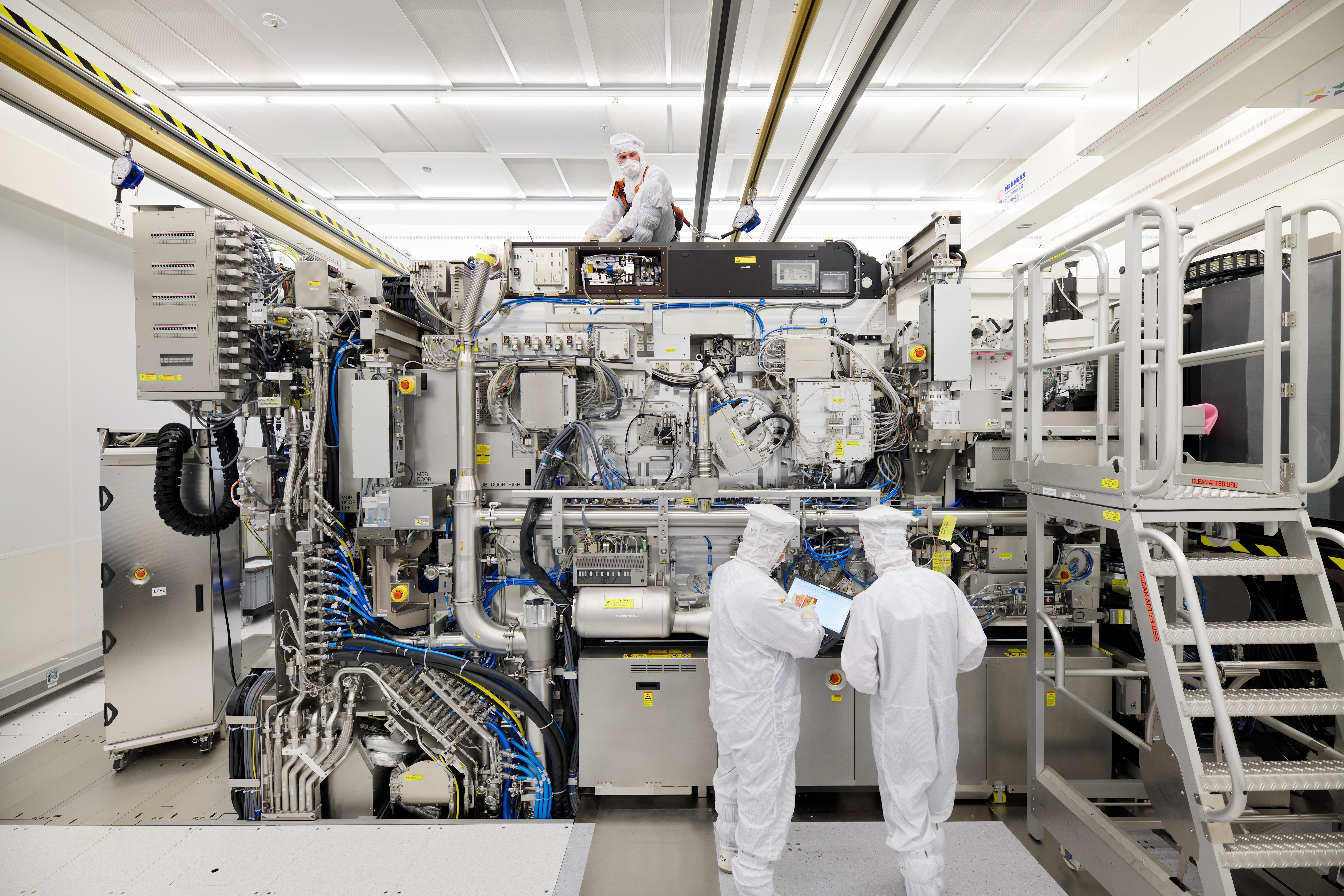
REE and The Green Transition
The European Green Deal can only be achieved with Rare Earth Elements. Europe is currently entirely reliant on REE imports. In assessing critical raw materials, the European Commission has defined REE as the commodity with the highest supply risk.
The ongoing transition towards a green and digital economy is expected to dramatically increase the need for a sustainable supply of rare earth elements. The European Commission expects the demand for REE used in permanent magnets to increase tenfold by 2050. This will require a significant ramp-up of new sourcing and improved recycling.
In 2020, the European Commission launched an action plan for critical raw materials and created the European Raw Materials Alliance (ERMA), focusing “on the most pressing needs, which is to increase EU resilience in the rare earths and magnets value chain, as this is vital to most EU industrial ecosystems”.
Source: Rare Earths Norway