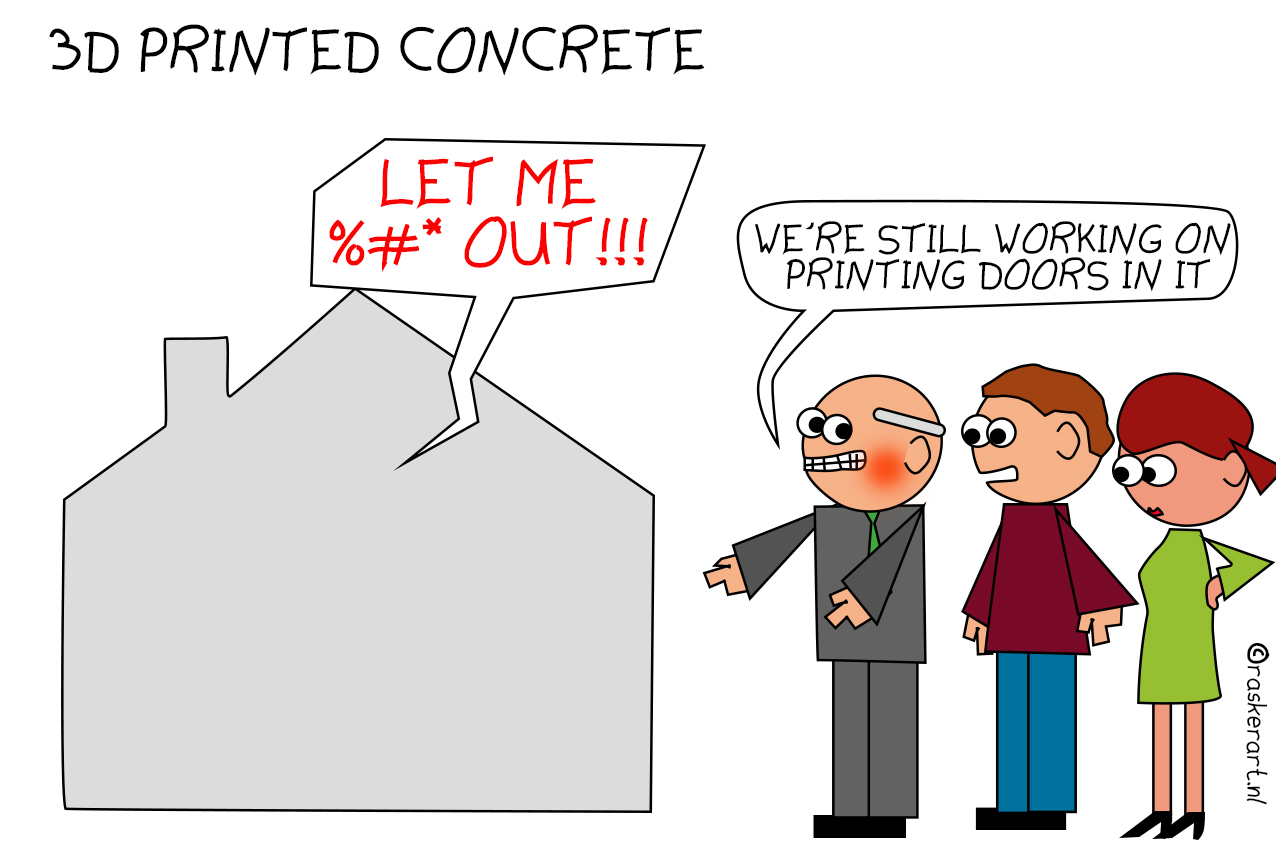
Whereas in other sectors it is becoming increasingly more common for parts or products to roll out of a 3D printer, the construction industry is still lagging behind in this. But that is about to change. For example, in 2017, the Dutch town of Gemert in Brabant had the world premiere with a 3D printed bicycle bridge. Then in 2019, Europe’s first commercial meeting center (the Vergaderfabriek) was also churned out of a 3D printer in Teuge in the Dutch province of Gelderland. Developments in this technology are not standing still either.
For example, last week we wrote that the Dutch city of Nijmegen will 3D-print the world’s longest bicycle bridge. And in the nearby city of Eindhoven, the first 3D printed concrete house now has tenants. Is building with 3D printers a hype that will blow over? Or will we see this more often? Is this going to be the future?
If it were up to Theo Salet, Professor of Concrete Structures at Eindhoven University of Technology (TU/e, and affiliated with the Milestone project that is responsible for the printed house), it certainly will be. “We not only digitalize the design this way, but also the construction itself. It will lead to more sustainable housing because you need less material. We know that the CO2 emissions from concrete are relatively high. If printing technology develops further, I can see walls getting thinner and even more savings being made. Moreover, as an architect you have much more freedom. That’s because you can print concrete in all kinds of shapes.”
More advantages
There are even more advantages to 3D-printed concrete, the professor goes on to say. The printer does the hard work so construction workers have less heavy lifting to do. Plus, the construction itself is faster because the preprinted concrete blocks only need to be joined together. Salet: “You can also print all kinds of features in the wall. For instance, cutouts for water pipes and electricity. But insulation materials as well, or a layer to improve the acoustics.”
All of these integral functions and other facets of 3D printing are being investigated by Salet in the 3D Concrete Printing research group. This is the same group that is collaborating on the Milestone project. So now the first house of this project has been completed. The project partners (TU/e, Van Wijnen, Saint-Gobain Weber Beamix, Vesteda, Municipality of Eindhoven and Witteveen+Bos) expect the delivery of the last four houses to go more quickly. Erwin Kersten, Manager South at Van Wijnen, explains: “We are building a house from different components, which has never been done before. In fact, you’re always working on prototypes and improving them. It takes time to adapt the printing process since the house has to meet strict Dutch building requirements.”
Salet adds: “This has taught us even more. We know much better about what works and what doesn’t. We are also going to make a few more adjustments so that we can speed up the process. We’re not just learning a lot. There’s still four more houses to go. The fact that we can immediately use this knowledge to further develop the project is a gift to me. Not only should it all go faster, but the other houses are also supposed to have several floors or an extra floor. That’s another step in the development of this technology.”
Printing on site
At present, the separate parts are printed in the specially-equipped 3D printing room (also a premiere back in 2019). As soon as the walls have hardened, they are transported to the construction site by truck. Ultimately, the aim is also to print on site, as CEO Bas Huysmans says. “It is not sustainable to 3D print in a large factory and then load everything onto trucks. Over time, everything will be printed on site. I can already see it: A truck delivers the printer. Then an architect can plug in his USB stick that has the building design, as it were. The printer then does the work, so when they come back the next day, the second floor is finished. Although we haven’t got that far yet with the second and third houses. But we can still dream.”
Unlike the Eindhoven Milestone project, the construction of the Vergaderfabriek in Teuge did use on-site printing, says Hugo Jager of Revelating. He worked with the Vergaderfabriek to digitalize things. “This printing was carried out by Berry Hendriks of CyBe Construction. It is important that concrete hardens under the right conditions after printing. Those conditions must be stable. To achieve this, a large tent was erected around the construction site in Teuge.”
Prefab vs printing on site
Personally, he thinks that in the future, this method will be mainly used for unique projects. The prefab method, whereby you make the parts in a factory, is more suitable for scalable projects. To illustrate this point, Jager cites a 3D printing project in Den Helder in the north of The Netherlands. Here, 154 apartment houses will get new facades and balconies straight from a 3D printer. Construction company Bruil has set up a 3D printing factory in Veenendaal for this purpose.
“3D printing can have its advantages. You always have to take the construction and load capacity into account. Traditional concrete has much more mass, while printed concrete is hollow inside. You easily save about 40 to 50 percent in materials, not only in terms of CO2 emissions but also in weight. Moreover, it is very difficult to get traditional concrete made into unique shapes. Especially if you only use a mold once, then that’s very expensive. A 3D printer is much more suitable for this purpose and you don’t need a mold. But the technology is really still in its infancy. There is plenty of research and experimentation going on. In this respect, scaling up and delivering consistent quality often poses a challenge.”
Will house become cheaper?
Jager says that it is not surprising that the adoption of new technology in the construction sector is slow to take off. “The construction and real estate sectors are highly fragmented with all the various municipalities, hundreds of builders and other parties to contend with. So, it is not surprising that the adoption of innovation is not going very fast. Another factor is that there is enough demand and the market is willing to pay for housing. Consequently, companies do not see the need for digitalization as yet. But I am curious about what will happen if several large construction companies start building homes directly from factories. What consequences will that have? Will houses become cheaper? Maybe other builders will also join in with this industrialization process if there is any pricing pressure.”