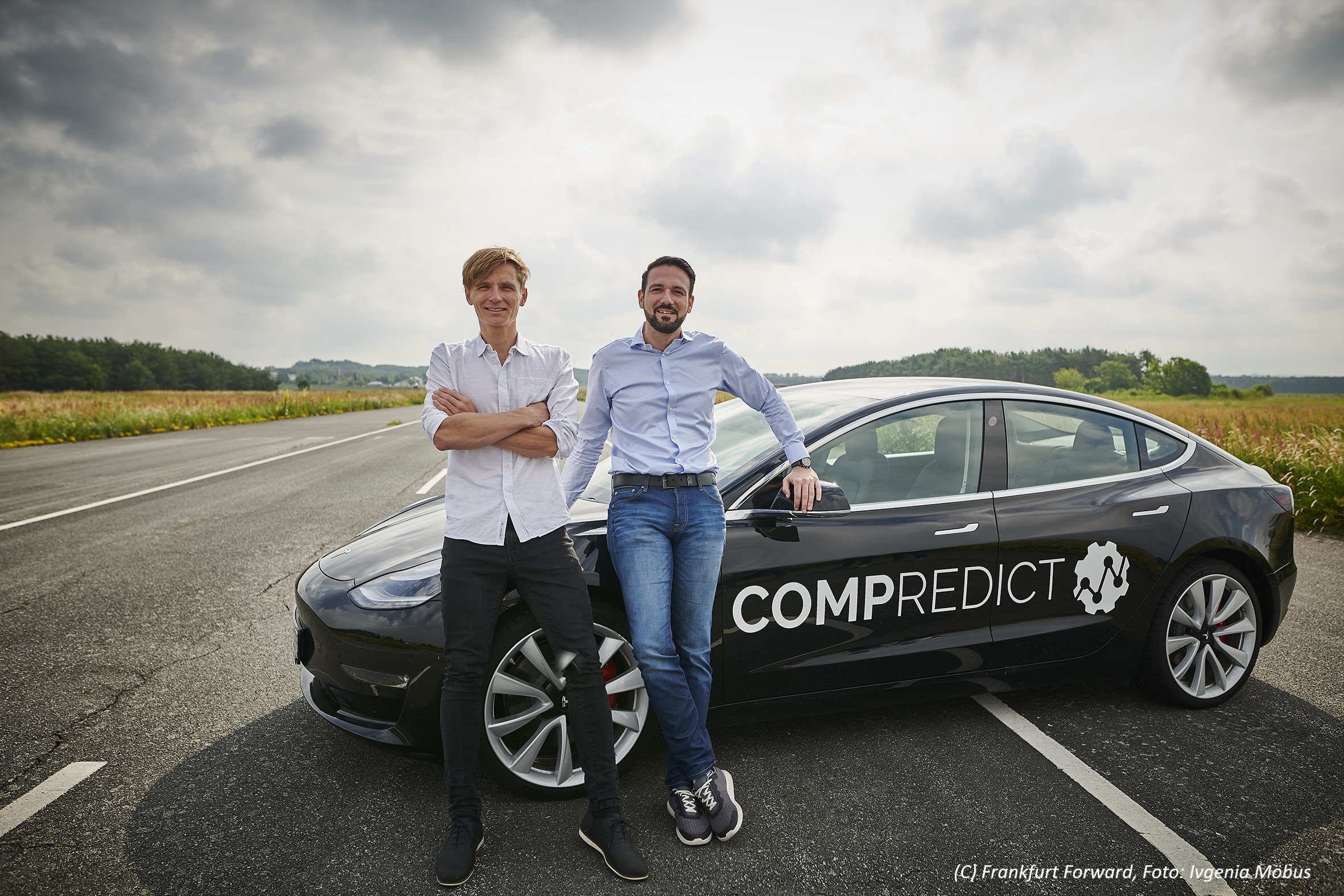
A modern car produces a vast stream of information, from the thousands of data points in the vehicle. A German company has developed a system to collect all that data and to reuse it to generate new information, helping cars manufacturers to develop more efficient components. The system does so via what is known as a cloud-to-cloud connection, without any physical device on the vehicle.
COMPREDICT is the start-up behind the software. It was founded in 2016 within the Technische Universität Darmstadt by Dr. Ing. Rafael Fietzek and Dr. Ing. Stéphane Foulard. The firm provides its system to other companies – including car manufacturers, telematics companies and fleet operators.
Virtual sensors can measure the dynamic behaviour of components such as batteries, brakes, and powertrains. They offer insights on how vehicles are used and how they perform, which enables predictive maintenance and improved components design.
Considering the enormous amount of information coming out from today’s cars, the system needs to know what data to choose from. “We designed an entire machine learning infrastructure, gathering all the data that cars collect. The Artificial Intelligence (AI) is trained to get the right information, and it does so by selecting the right features out of more than 20,000 different data points in the car”, explains Fietzek.
The system tracks components’ lifespan to check how they perform in real-life use and how to design more sustainable devices. This way, a devices’ ecological footprint can be reduced, as waste is minimised as well as any replacements costs. In this respect, the system improves failure prediction which enables companies to predict maintenance times more precisely.
COMPREDICT’s system is suitable for different kinds of applications on vehicles. It can be integrated into existing telematics solutions, showing users real-time data from the vehicle.
Detecting overload
One of the system’s applications is capable of detecting vehicle overloads. It calculates masses in relation to the various forces and acceleration. “Developing an algorithm was complicated, as it needs to work well for different types of vehicles. But the system can be made to scale, and it gives precise results”, says Fietzek.
In the event of an overload, the fleet manager gets an alert. In addition to that, algorithms can determine whether the overload affects the vehicle’s dynamic behaviour, detecting any safety-relevant impacts.
Calculating mass also means that a more reliable prediction of EV’s battery range is possible. In combination with other factors – driving style, external conditions, and battery health status – vehicle weight helps to forecast how long batteries are going to last. Since the loaded mass constantly changes – particularly when it comes to delivering goods by trucks – tracking it down precisely is hard, as current measurements are based on the previous usage. By using the sensors’ real-time detection system, mass detection is possible.
Designing more efficient cars
Measuring wheel force is key for car designing as it assesses metal fatigue and component loads. COMPREDICT’s virtual sensors enable the monitoring suspensions, car body, and driveshaft, giving engineers relevant information on how vehicles perform.
According to Fietzek, virtual sensors provide a better picture of how car parts work. “Nowadays, a lot of components are over-designed because car manufacturers and suppliers don’t know how they are used in practice. Some people break too often because engineers underestimated a certain kind of torque.”
The sensors can both measure the engine and the wheel speed, as well as torque and acceleration. They can optimally correlate the values that the hardware sensors give them, and they can be made to scale for different types of vehicles.
In comparison with other systems, virtual sensors are more reliable. In fact, speed bumps and bad calibration will not invalidate the data. This means that the data is more precise under all real-life conditions.
Tracking batteries’ status
Monitoring the battery’s health is another task virtual sensors can fulfil. “We can get live data from the car on the battery’s current state. The system can predict battery life and provides engineers with information on how to develop better batteries in the future”, Fietzek adds.
The system measures the voltage in the first ten seconds after starting the engine. Then the sensors analyze the voltage curve over time, detecting autonomously the battery status.
Also interesting: Franco-German partnership in battery production is taking shape more and more
Virtual sensors everywhere
Over 50.000 vehicles are now connected to COMPREDICT’s platform. “Our goal is to reach more than a million vehicles in two or three years”, says Fietzek. Automotive is the focus of the company, but its co-founder suggests how this kind of technology could also be used in many other fields of applications.
“Standard sensors are in every appliance, in all mechatronic systems. With the use of virtual sensors, data helps to measure more things that this hardware sensors can’t measure”, adds Fietzek. The technology developed by the Darmstadt-based company could be reproduced in all devices that feature hardware sensors.
Despite a focus on the automotive sector, Fietzek’s start-up is broadening its sights, aiming to become a major sensor company. “We are starting a pilot project to use virtual sensors in household applications too”, says Fietzek. Ovens and fridges in our houses also have hardware sensors. Therefore, in the future they could tell you when your roast is done.
In the photo: Dr.-Ing. Rafael Fietzek and Dr.-Ing. Stéphane Foulard