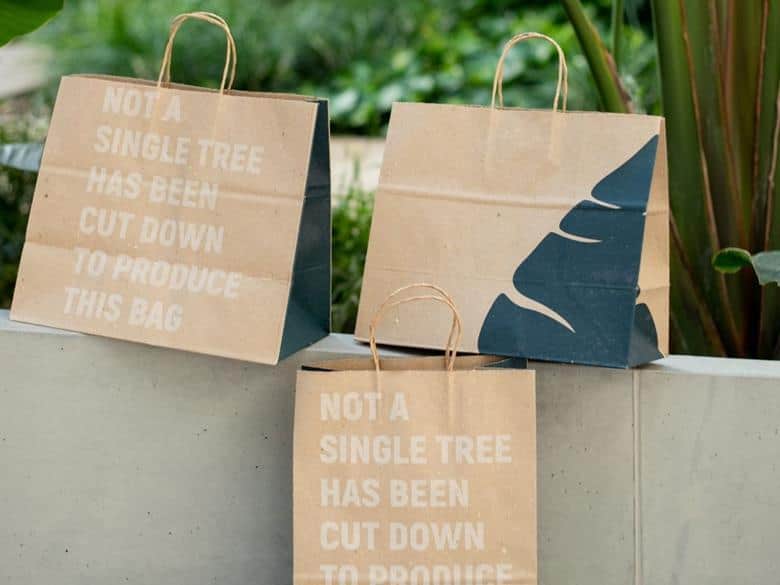
About Releaf Bag
- Founders: Valentyn Frechka and Alexander Sobolenko
- Founded in: 2019
- Employees: 9
- Money raised: 2,85 million euro
- Ultimate goal: Change the packaging industry for good by offering companies a sustainable alternative to paper.
Every year, more than 7.3 million hectares of forest are cut down for paper production. That’s twenty soccer fields every minute. Growing up in a forested area, Ukrainian Valentyn Frechka is worried. He was only 16 when he started looking for an alternative to cellulose – paper’s main raw material. He tries grass and straw, but the results were disappointing.
While hiking in the Carpathians, a high mountain range in central Europe, the penny dropped. “It suddenly occurred to me: why don’t I try it with leaves?” More than five years later, there is Releaf Bag. Compared to the production of traditional paper packaging, the start-up uses 15 times less water and saves 78 percent CO2 emissions.
In this episode of Start-up of the Day, Frechka talks about the mission and ambitions he has with Releaf Bags.
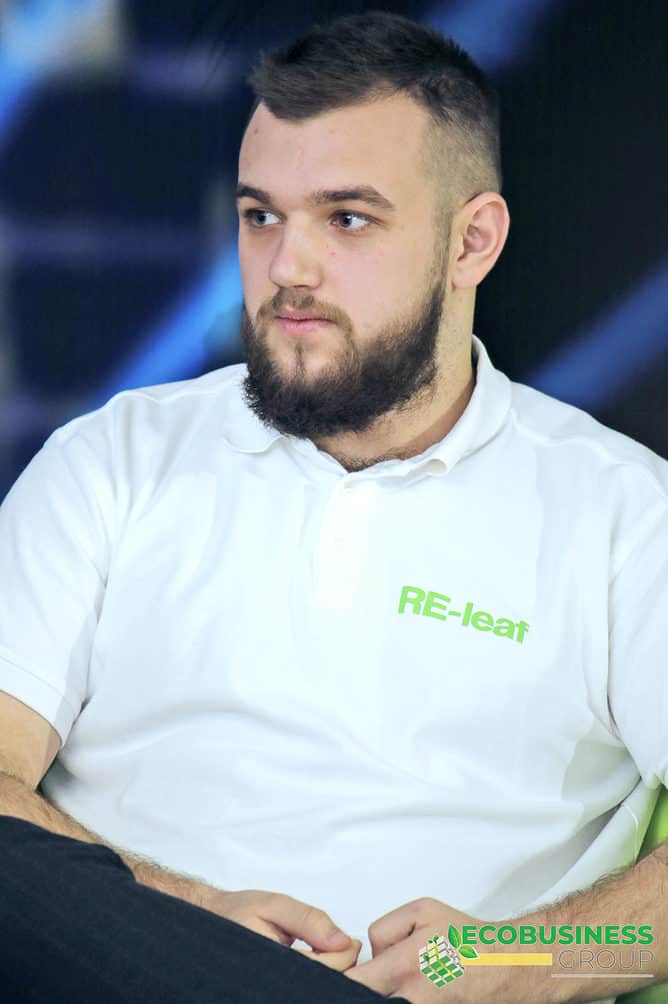
Why leaves?
“Leaves are considered biological waste in cities. To keep the streets clean and prevent nitrogen from being released into the air, the municipality removes them. Often they are burned. This harms the atmosphere by releasing carbon monoxide and other harmful gases.
We see leaves as a source of cellulose, the raw material of paper. This “waste” is an affordable raw material available in large quantities and throughout the year. The pulp from leaves is an alternative to wood pulp, from which paper is normally made.
Thus, with a residual product, we prevent the destruction of forests; no tree has to suffer for our packaging. Moreover, we also use much less water and our carbon emissions are also much lower compared to traditional paper production. Our packaging has a degradation cycle of 30 days, compared to up to 270 days for traditional paper.”
What does the process from leaves to paper look like?
“It starts with collecting leaves from residential areas, city parks and from sidewalks and from other industries where there are leftovers that include cellulose. People often think that we use leaves from forests and then criticize that you have to leave them out, because otherwise you disrupt the ecosystem. But we only use leaves cleared by cities.
Then we clean them, lay them out to dry and grind it into pellets. This way we can store the raw materials throughout the year and the production cycle is stable. This granulate is processed into a special fiber that forms the basis of our paper. To this we add filler and then the paper is pressed and rolled by a machine. Finally, we make blank paper bags from it.”
The idea came about while hiking in the mountains. What happened next?
“At the beginning of 2018, I had before it a high quality package as a final result. With that prototype, I actually started entering every competition imaginable to get funding and develop the prototype further. I won several awards, and in the fall of 2018 I was invited to work in the innovation department of Zhytomyr Cardboard, a large cardboard factory. Here I got the opportunity to refine my technology, and when co-founder Alexander Sobolenko got involved, Releaf was born.”
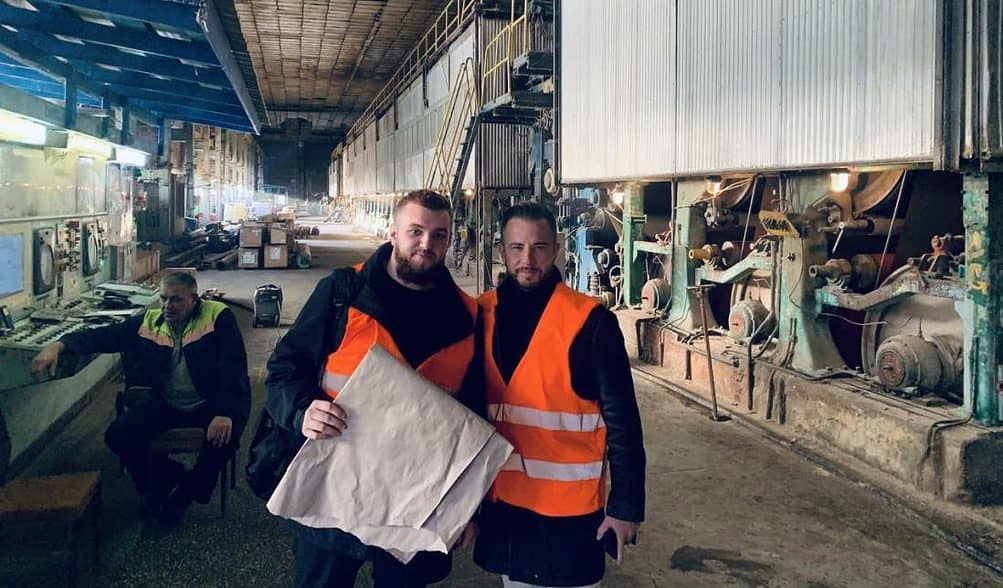
What is your biggest challenge?
“I don’t have one answer to that, there are several. Protecting our technology, is a challenge, but also scaling up and everything that comes with it. We now have a plant in Ukraine, but conditions there are very uncertain right now. I myself am now in France, but we haven’t yet decided where we want to set up our first factory. The system for start-ups here is quite complicated.”
Where are you now and where do you want to be in five years?
“In 2021 we started our first industrial production and got the first support from the World Wildlife Fund and Canopy Planet. Last year we started selling our packaging in Europe and submitted a proposal to the EIC Accelerator 2022 program. The total cost of the pilot production line is 3.5 million euros, of which the EU is subsidizing 2.5 million. In addition, we have commitment that they want to invest in further scaling up in the coming years. In the next five years we want to set up two new production lines. We are in the starting blocks, I can’t wait.”
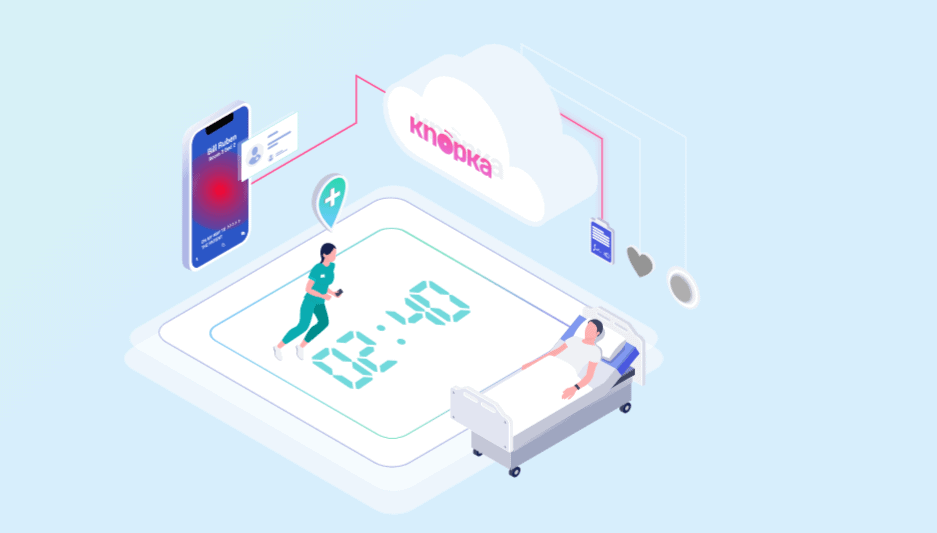