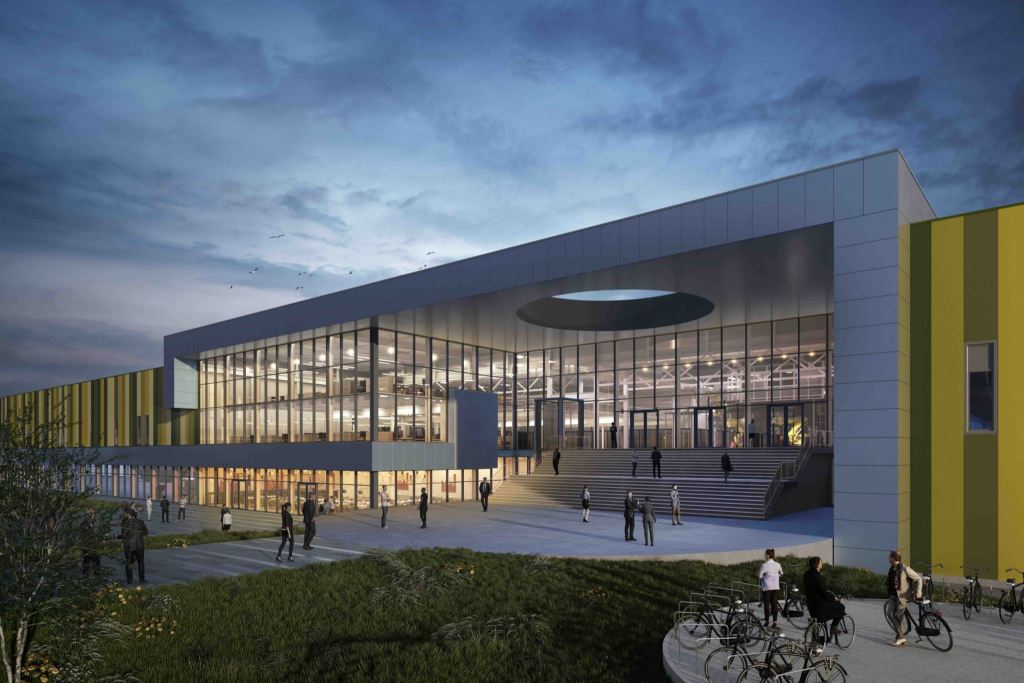
[et_pb_section bb_built=”1″][et_pb_row][et_pb_column type=”4_4″][et_pb_text _builder_version=”3.12.2″]
“Here everything comes together”, Michel Weeda is in the middle of an enthusiastic story about the innovation programme ‘Factory of the Future’ which he set up at the Brainport Industries Campus with the Brabant Development Company (BOM). “New ways of 3D printing, for example, are not only developed and tested here, but also implemented within the company.” For this, residents of BIC -but also companies from outside the campus- make use of the technical facilities and work together with educational institutions to train talent as well. The programme consists of seven different components, each of which will have its own place in the Atrium on the campus.
[/et_pb_text][et_pb_testimonial _builder_version=”3.12.2″ author=”Michel Weeda” job_title=”Programmanager” company_name=”Brabantse Ontwikkelings Maatschappij” quote_icon_background_color=”#f5f5f5″]
“It is unique in the world that education, innovation and production operate so closely together.
[/et_pb_testimonial][et_pb_text _builder_version=”3.12.2″]
Implementing new production methods
Weeda is program manager at the BOM, together with Brainport Industries and the province of North Brabant he set up this innovation program. The program is built around different trends in the industry. Participating parties – more than 70 companies and 6 knowledge institutes – work together to develop new production methods and implement them, they train talent and share knowledge among each other. Trends include robotization and automation: “This comes together in the Fieldlab Flexible Manufacturing. Here, for example, they work on smart, flexible robots that can be used in logistics. Or they develop a quickly adaptable production process that is able to make different products with variable characteristics rather than one fixed component. That is very diverse. That requires smart machines and controlling”, Weeda explains.
[/et_pb_text][et_pb_image _builder_version=”3.12.2″ src=”https://media.innovationorigins.com/2018/11/Wiel-Smart-Industry-2018-1180px.png” /][et_pb_text _builder_version=”3.12.2″]
In each field lab (see framework), participating parties can experiment; students learn to operate machines and products roll out of the factory further in the process. Everything under one roof. Weeda: “It is unique in the world that training, innovation and production operate so closely next to each other. This allows us to reduce the time to the market, which is necessary because the pace in the market is extremely high.”
[/et_pb_text][/et_pb_column][/et_pb_row][et_pb_row][et_pb_column type=”1_2″][et_pb_text _builder_version=”3.12.2″]
History lesson
To explain the origins of these programs, Weeda takes a step back in time: “When Philips pulled the plug from the Centre for Manufacturing Technology (CFT, Applied Technologies) in 2010, the desire soon grew to develop this existing knowledge into a kind of universal language for the entire supply chain.” At CFT, Philips developed process techniques for companies such as ASML and other large companies. When Philips stopped using this centre, concern arose that knowledge would be lost. “You can imagine how valuable this knowledge is, not only production methods but also an incredible amount of system knowledge lay with Philips. Of course, this was not allowed to disappear. Brainport Industries was born with this idea of spreading knowledge to suppliers”, Weeda looks back.
Nowadays, machines are becoming increasingly complicated, factories more flexible and data even more important. This makes it necessary to set up projects together and share knowledge more. By setting up collaborations around different themes and critically examining whether a party adds value to a project, the BOM contributes to the program. Weeda: “In the past, the supply chain was a classic client-supplier collaboration. Now you can see that suppliers are involved in the design process at an earlier stage. That is the first result of closer cooperation and mutual trust. But also because of available data; there is more data that can be shared to enable faster innovation. As a BOM, we have a broad network. We support various parties and identify trends in the industry and determine with partners how we can respond to them, trends such as data and photonics. We bring parties together around different developments.”
[/et_pb_text][/et_pb_column][et_pb_column type=”1_2″][et_pb_text _builder_version=”3.12.2″ border_color_all=”#b7b7b7″ animation_style=”fold” background_color=”rgba(214,214,214,0.44)” custom_padding_last_edited=”on|” saved_tabs=”all” custom_css_main_element=”padding:2%;”]
Factory of the Future” innovation programme
The innovation program at the BIC consists of seven different field labs. Each project is designed around different industry trends and cooperates with different companies and knowledge institutions. Within the projects the participants share knowledge and facilities, in this way they want to reduce the time to market and implement new technologies faster within the industry. A total of 70 companies including 6 knowledge institutes are connected to the innovation programme, the facilities are currently being realised on the Brainport Industries Campus. Research, courses, experiments or other events are being set up around these themes:
Fieldlab Flexible Manufacturing – robotisation and automation
Fieldlab The Smart Connected Supplier Network – smart data exchange
Fieldlab Multimaterials 3D – additive manufacturing & applications (plastics)
AddFab – 3D metal printing – additive manufacturing & applications (metal)
Fieldlab High Tech Software Cluster – virtual prototyping & design, model based software and data analytics & services.
Teclab & Brainport Industries College – innovative education in the ecosystem of the high-tech manufacturing industry
Fieldlab Advanced Manufacturing Logistics – production logistics.
[/et_pb_text][/et_pb_column][/et_pb_row][et_pb_row][et_pb_column type=”4_4″][et_pb_image _builder_version=”3.12.2″ src=”https://media.innovationorigins.com/2018/11/Michel-Weeda-compact-1.jpg” /][et_pb_text _builder_version=”3.12.2″]
Lifelong learning
Despite the separate programmes and various trends, some things overlap: “Some developments have clear interfaces with each other, which in turn leads to new things. In drawing up the programmes, we try to take account of this link and overlap. We should not want to narrow this down too much; that can slow down innovation. For example, today it is already normal for companies like ASML and suppliers to develop prototypes using AR or VR. Data and digitalisation ensure that you can experiment virtually to improve it in reality. In addition to digital development, VR is an ideal tool for education and courses.”
In the fieldlab education, Teclab and Summa work closely with the business community, Weeda explains: “They work demand-driven. Students get to know what is expected of them in practice. But it is broader than just training new talent because current employees also have to keep up with the future. Here we aim to do justice to the motto of lifelong learning by also offering or developing various courses”, Weeda explains.
On 22 November Brainport Industries will organise a kick-off event in cooperation with all participants in the innovation programme. The exact content of the programmes will be announced here.
[/et_pb_text][/et_pb_column][/et_pb_row][/et_pb_section]