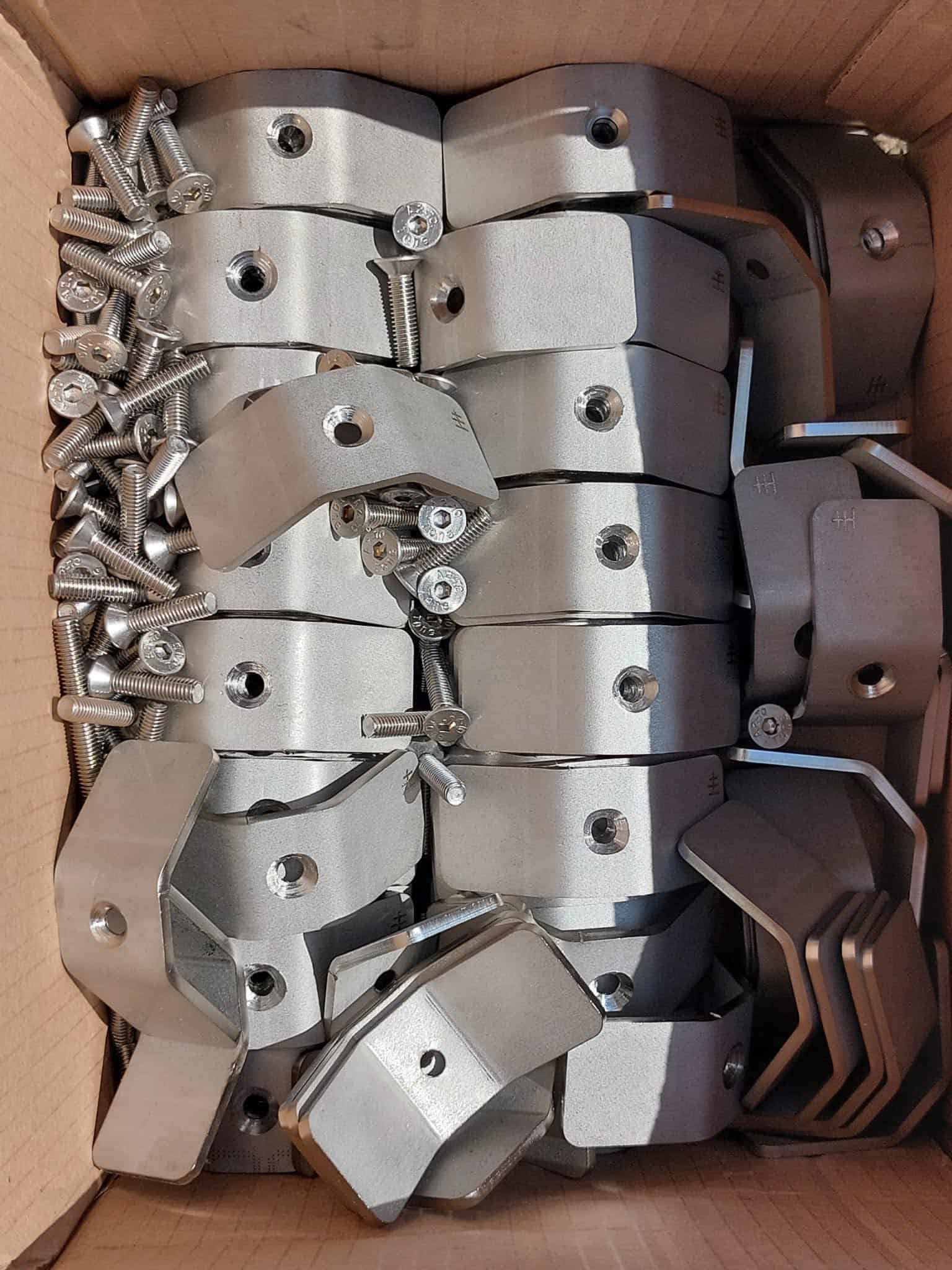
About Hitch
- Founders: Esther Laga
- Founded in: 2020
- Employees: 1 + interns, students and freelancers.
- Money raised: 5000 euros Future Generations Foundation, 5000 euros KU Leuven, 30,000 euros from the city of Ghent, 100,000 euros Vlaio.
- Ultimate goal: HITCH is a joining system that allows all kinds of sheet material to be easily fastened together.
Start-up Hitch designs dismountable and reusable furniture. In this way, the company wants to counterbalance disposable culture. Interior designer Esther Laga founded the company after a somewhat out-of-control school assignment. In this episode of Start-up of the day: Hitch from Gentbrugge.
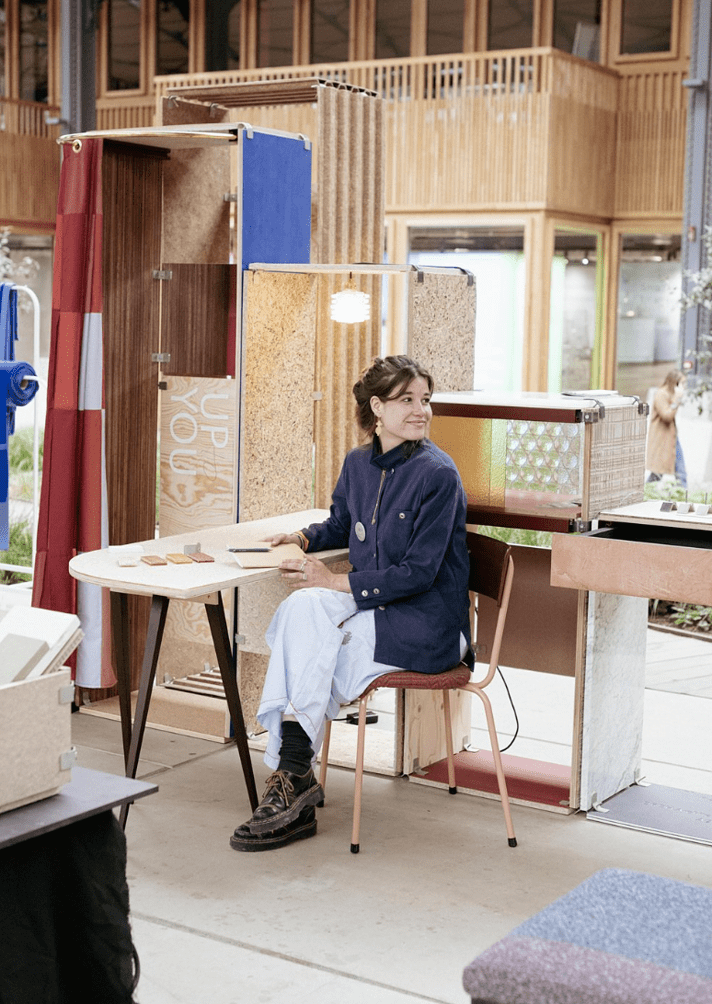
Who are you?
“I am a young designer, passionate about design, but equally passionate about its influence on climate issues. I did my master’s of interior architecture at Sint Lucas in Ghent after studying at KASK. Frustration with the current disposable mentality led me to develop a more sustainable and modular concept. It is high time to take another look at our utensils. It is no longer justifiable to purchase products with a short lifespan, that cannot be used multifunctionally. Products must be able to evolve and change during the life of the consumer so that they can last for decades and remain relevant.”
What is the problem with the current range of furniture?
“We choose our furniture based on our current needs, which means it has a very short lifespan. Moreover, the option to easily disassemble and reassemble products is often very limited or almost not feasible. Circular initiatives are fortunately on the rise but are often quite expensive and inaccessible to the wider public. Consequently, they still too often revert to impersonal, lower-quality pieces of furniture with which they do not really have a connection, which they quickly abandon. The result is an ever-growing heap of waste. We see an urgent need for a sustainable, circular solution accessible to a wider audience. As a student entrepreneur, I had the opportunity to experiment with this and gain knowledge outside the traditional school framework. Thanks to the various awards, I was able to get the first prototypes on point and research sustainable materials and the principles of the circular economy.”
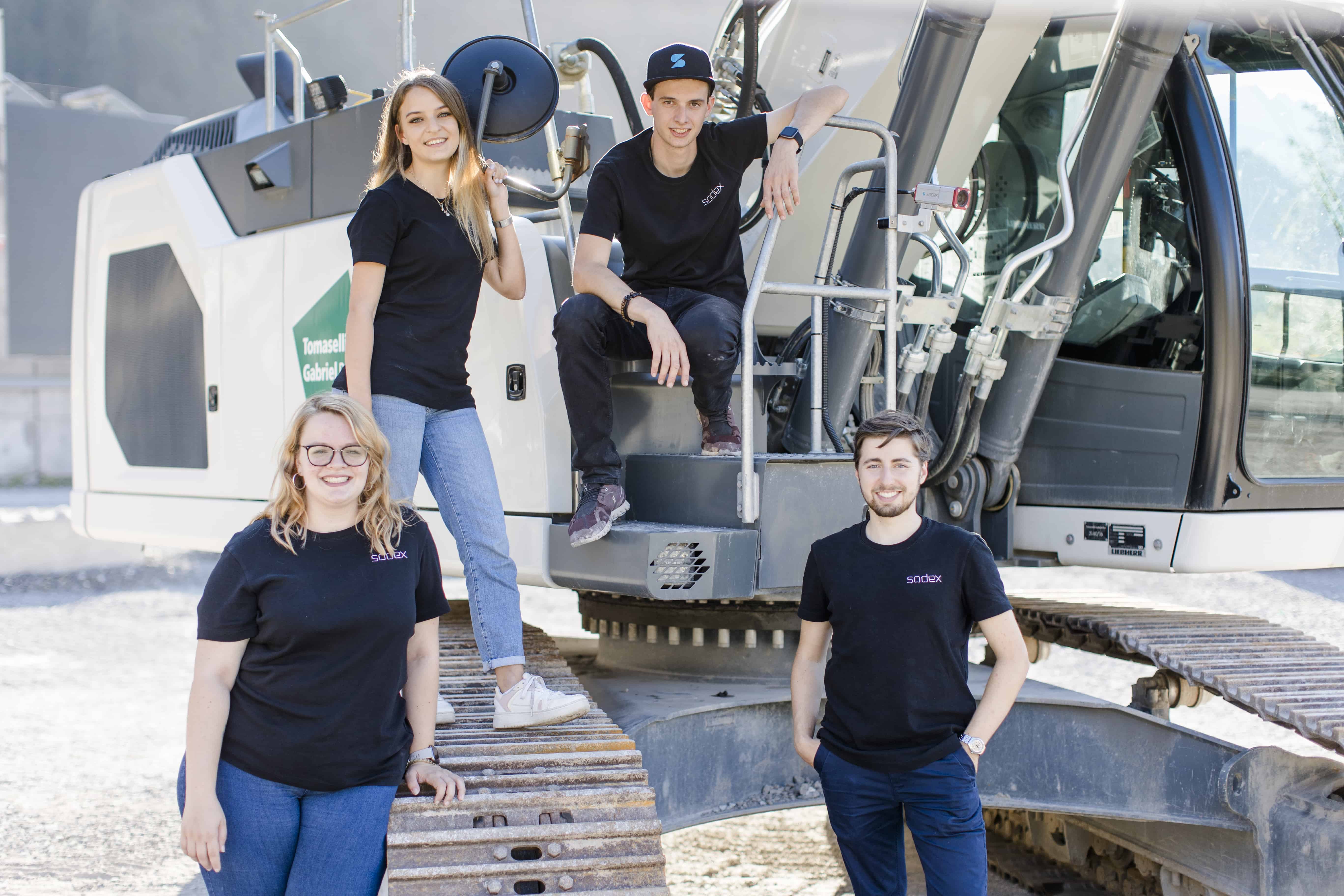
What did you develop?
“We develop reusable furniture that you can rent or buy. Pop-up stores, for example, can come to us. We will find suitable materials for it. We deliver and install everything ourselves. After the customer has used the furniture for a certain period of time, say one month, we disassemble everything and reuse the materials for a new project. The use takes precedence over possession.”
How exactly does that system of reusable setups work?
“We have developed steel connectors, Hitchtools. A kind of handy clamp with which all kinds of thicknesses of sheet material are easily transformed into temporary setups. Think of walls, shelves, and desks, both for home and in offices or stores. Our furniture can also be made very personal and unique. We think with our customers around the ideal choice of materials, color combinations, and customizable setups.”
What is the goal?
“Using our Hitchtools, we want to drastically lower the threshold to DIY. Assembling and disassembling furniture becomes child’s play. The sheet material is tightened between the Hitchtools, and then countless creations can be made. The great advantage is that the constructions, such as shelving systems, can be easily taken apart. You can have entire interiors custom-made, without any waste involved.”
Which materials do you use?
“The connectors are made of steel which makes them very strong and will last a lifetime. We focus mainly on recovered materials but also always keep our eyes open for renewable and other innovative materials. In addition, we like to work with bespoke companies to process these materials in order to also include the social economy in our sustainable story.”
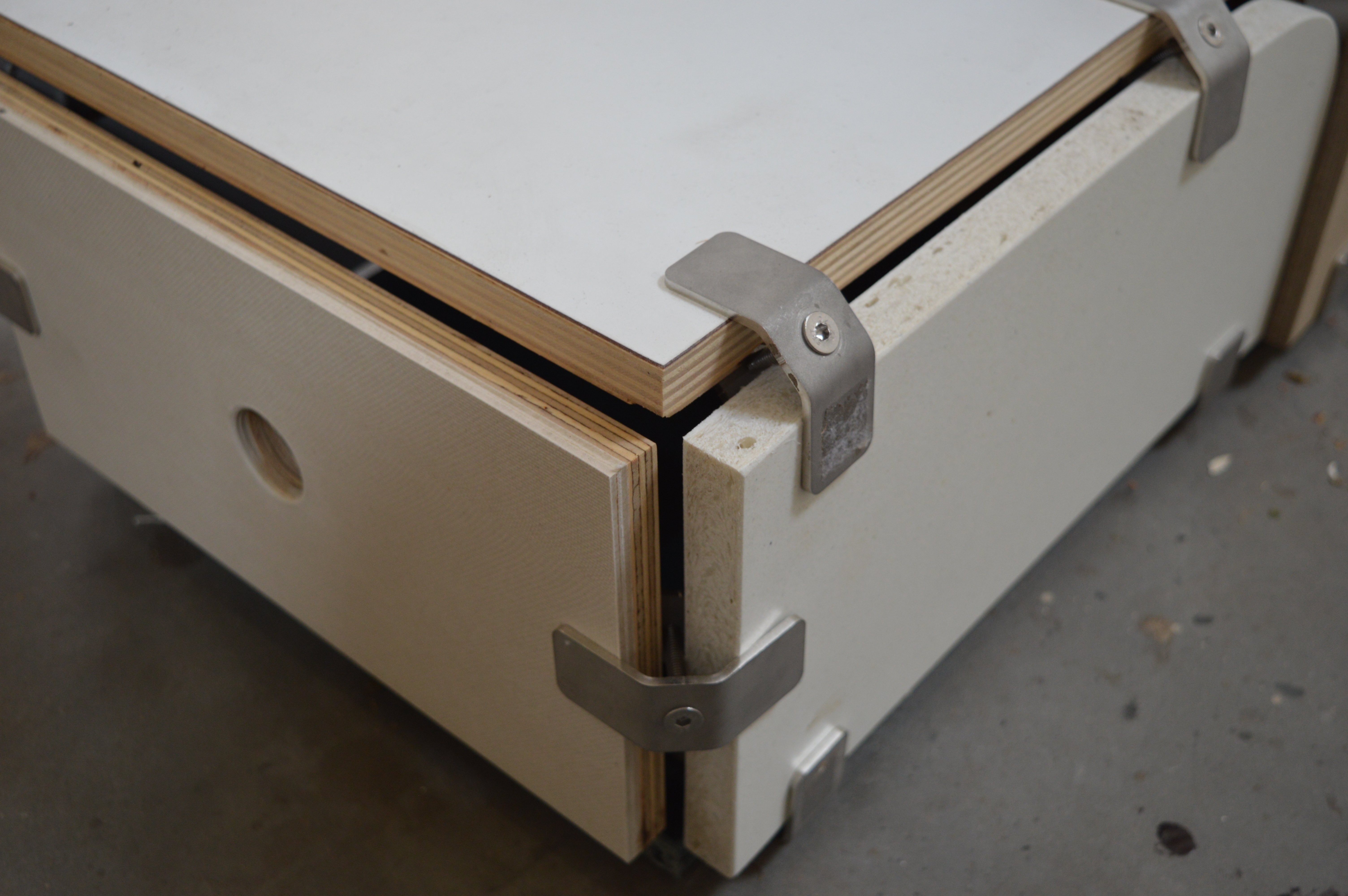
What market are you targeting?
“Meanwhile, we are mainly addressing the B-to-B market. The reusability comes out better on the B-to-B market, on larger projects. In addition, those larger projects are also slightly more profitable and currently more interesting to focus on. Private customers can also always come to us but that is not where our current focus lies given that as a small organization, we do not yet have the resources to provide sufficient follow-up to all of our customers.”
Which projects have you already completed?
“We have already done projects for the Ghent Design Museum where we were allowed to furnish a multifunctional hall. For the reception and networking area, we made a bar. We also made pedestals for an organization that wanted to exhibit all kinds of art projects. For a pop-up store in Antwerp, we made a cash register, counter, and displays. For an individual, we made a desk that he could quickly take apart. We also made a recyclable kitchen for a temporary coworking space and are now working on a demountable call booth for a Ghent office. So plenty busy on various projects”
You also want to collaborate with other knowledge institutions. How about that?
“We are already working with various knowledge institutions, art schools, colleges, students, designers, engineers, and artists under the name HitchLab. By collaborating with universities, we are involving a new generation of students in this circular story and meanwhile, we are gaining a lot of knowledge ourselves. By additionally collaborating with artists, we are seeing what other options are possible for our Hitch tools.”
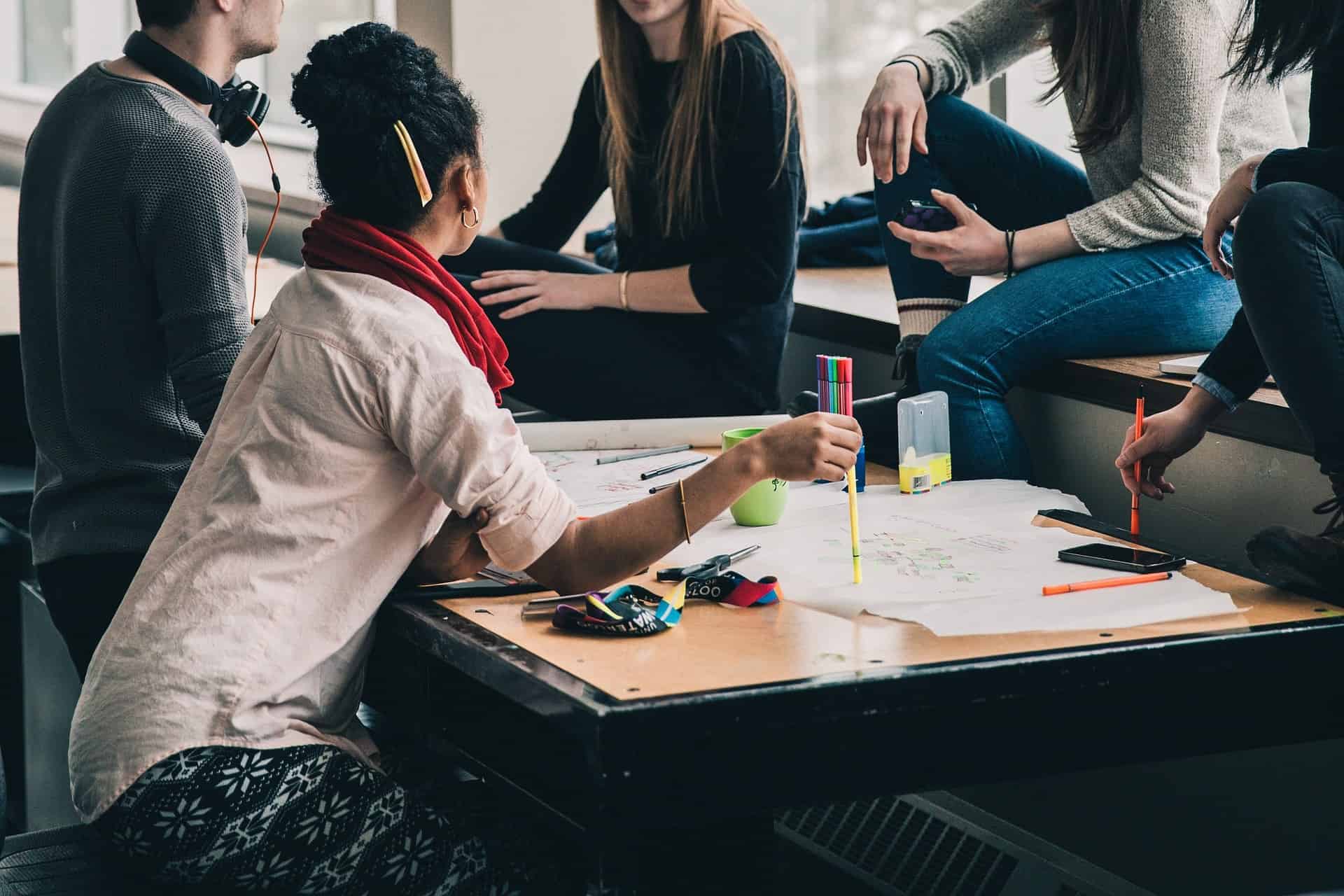
There is a materials scarcity right now. Does that make people more conscious of recycling?
“People are becoming more conscious about dealing with the material. That’s a good approach. We also want to better align the links. For example, many companies have leftover glass and wood, but that is not yet clearly communicated to each other. A lot is thrown away. We are now looking in Ghent at who all those players are and how best to deliver the material to the manufacturing companies. In order to develop this further, we received a nice budget from the City of Ghent last year. This has since led to us receiving a second budget from Vlaio to test out this idea all over Flanders. “
What ideas do you have on that front?
“It would be ideal if there were a kind of library where materials could be exchanged. We want to develop a script for this and copy it to other regions in Flanders. In terms of logistics, it is often unnecessary to bring materials from, say, Ghent to Leuven. While there are also many companies in Leuven that have surplus materials and bespoke companies are waiting for work. We are going to see how we can set up similar clusters in Flanders. To quickly bring materials back into circulation. That way we can avoid unnecessary transport.”
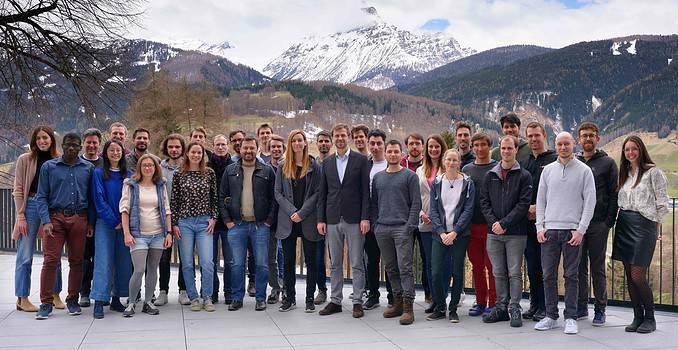