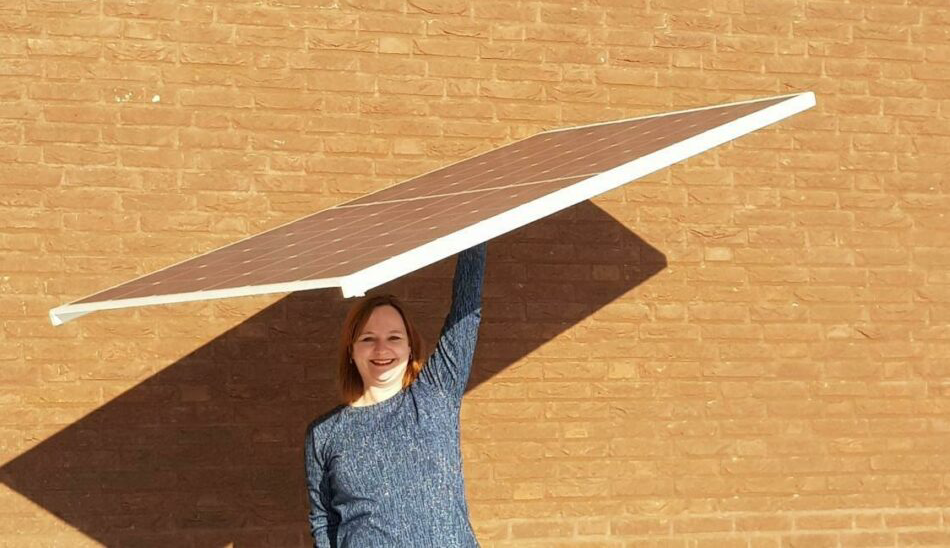
For a long time, this was considered impossible because plastic does not behave in the same way as glass. But with Dutch plastic expertise, it worked. And now the start-up Solarge is on the verge of mass-producing lightweight solar panels. That could be a revolution, especially for rooftop solar. โThere could be an additional hundred square kilometers of solar roof,โ says Solarge.
Here is a solar panel that weighs half as much as a normal one, but otherwise works exactly the same. It is produced entirely sustainably and, because of its lower weight, can be installed on any roof. This also applies to the roofs of businesses such as distribution centers and others that are often not so strong. These panels also emit 80% less CO2.
That may sound too good to be true, but it is exactly what the company Solarge envisions. The twelve people at this start-up in Eindhoven are working hard to have a factory-ready solar panel by Spring 2022 that can produce 500,000 square meters of solar panels annually. Thatโs quite an ambition for a company that has only been around for a few years.
Skepticism about plastic solar panels
When Gerard de Leede, Chief Technology Officer at Solarge, first heard about plastic solar panels, he was skeptical. โThe Dutch part of SABIC, formed from parts of DSM and GE, had developed a plastic that could replace glass in solar panels.โ This was due to a combination of the right plastics and clever additives that made it as transparent and sturdy as glass. De Leede was chief technology officer of the Heijmans construction company at the time. On closer inspection, he came to the conclusion that it was a promising and groundbreaking development. โA lot of homework had been done back then,โ he recalls during an online interview. โThey knew the possibilities, and they wanted to apply it once in practice โ thatโs what they came to Heijmans for.โ
Soon De Leede recognized that a link was missing. The basis for the plastic had been developed by SABIC, Heijmans could apply it โ but who would make the lightweight solar panels from it? Solarge was born.
The technology works and we can produce on a large scale.
Gerard de Leede
De Leede and co-founders Huib van den Heuvel and Jan Vesseur raised venture capital, supplemented by grants and loans. โAfter three years, we are now ready to build a larger factory. The technology works and we can produce on a large scale.โ With that, according to De Leede, we are thus on the eve of a major change in the world of solar panels.
While De Leede was skeptical at first, he is now the biggest advocate of lightweight panels. โYou open up so many possibilities with this. Solar power on roofs is indispensable for generating enough sustainable electricity and many roofs are still unused. By making the panels 50 percent lighter, you can invest an additional 100 square kilometers of roof with panels in one fell swoop. โThose are roofs that donโt have enough solid roof structures for conventional solar panels, as most residential buildings do. Think about commercial buildings that have bitumen as a roof covering. Or plastic roof layers, or buildings with pitched roofs made of curved metal sheets.โ
PFAS in solar panels
This sturdy plastic gives Solarge an edge over the competition, according to De Leede. โThere are other lightweight panels out there. But these are of inferior quality and do not last as long. Plus, some of them, especially from China, contain PFAS. That can cause big problems if it catches fire. Think of a barn fire, where there are panels on the barn. Thatโs very dangerous.โ
But aside from the danger, itโs the quality that should justify the somewhat higher cost of Solargeโs panels. โIn the beginning, they will cost a bit more than conventional panels from China. Fortunately, we have a market where there is hardly any competition: all the existing buildings that cannot accommodate standard solar panels. Weโll be busy investing in those for a while.โ
But what about the future? We are already seeing new commercial buildings being fitted with solar panels as standard. Think of distribution centers and data centers. De Leede says: โFor such panels, you need to install a more solid roof, often with steel reinforcement. Steel creates extra CO2. If you can make your roof light and cheaper and still install solar panels, that saves money.โ
The most sustainable solar panels in the world
Yet De Leede doesnโt necessarily seem to be concerned about the cost. When he talks about Solargeโs future plans, it becomes clear what this Dutch solar manufacturer wants: to make the most sustainable panels on earth. โInitially, we will still get the solar cells from China, after which we will coat them with plastic ourselves. But in time we want responsible, low carbon solar cells. These already exist and are made in Norway using hydropower. Today they are still much more expensive, but in the future, EU rules and border taxes will ensure a more level playing field. Then it will be possible to make solar panels with extremely low CO2 emissions at a competitive price.โ
What is also important in this regard: the plastic is recyclable. โYou can take the layers that the material consists of apart at the end of its life and recycle them separately. We are also working on reusing the solar cell itself as much as possible.โ So the cell is also ready for that other transition, from a linear to a circular economy.
โIf you add all that up, our panel will soon emit 80 percent less CO2 than a standard panel that currently comes from China and is made with coal power.โ That much smaller footprint also means that in terms of carbon impact, youโre more likely to break even. โNow it takes four years to recoup the environmental impact of a solar panel from China. With our panels, it would take four months.โ
Hydropower from Norway
But itโs not that far off. At first, Solarge will also just use Chinese solar cells. Later, the customer can choose between the somewhat more expensive Norwegian or cheaper Chinese solar cells. But the cost of the Chinese cells will also rise if EU plans for a CO2 tax at its external borders go ahead. โAnd if we produce on a large scale with our plastic-based technology, and Norway does the same with their solar cells, then the cost can quickly fall to the level of the Chinese producers or even below.โ
But then there must be a factory. By the first quarter of 2022, De Leede and colleagues want to open their factory. That means they need to raise money this year. In total, the factory is estimated to cost โฌ9.5 million. Part of that has already been financed. For the rest, Solarge is still looking for interested parties. The certification of the panels has already been successfully completed, so it is certain that the plastic-based panels, like those based on glass, will meet strict requirements.
The next few months will be critical. But perhaps by next summer, many an old industrial building will be full of Dutch, feather-light solar panels. And that matters, De Leede knows: โWith the extra hundred square kilometers of roof space that will become available, just as much extra energy can be produced as is currently still being generated from the Groningen gas field.โ
Photo: By using plastic instead of glass, Solargeโs panels fit on many more roofs.
This article is from ChangeInc, with whom Innovation Origins has an editorial partnership.