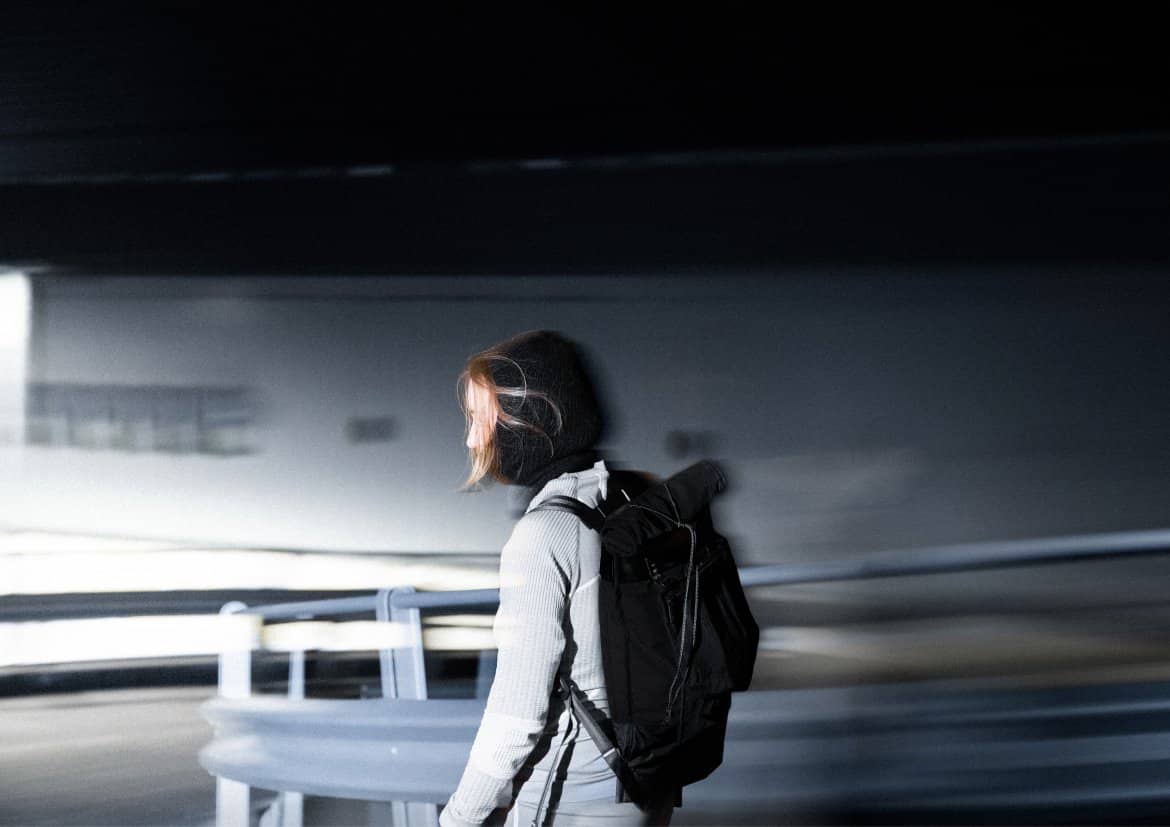
FREITAG is sending its first fully circular backpack into production. To make the recycling process as simple as possible and maximize the actual recycling rate, FREITAG opted for the principle of mono-materiality – the use of a single type of material, says the company in a press release.
- This circular backpack is made from a single material, simplifying recycling and promoting sustainability
- Tests at KATZ Aarau validate the mechanical recyclability of these backpacks
Every part of the backpack, from the fabric to the buckles, is made of just one material: polyamide 6. Thanks to this mono-materiality, as it is called, the product can be recycled entirely in one piece, without the need for complex dismantling. It also means that when all the life-extending options, such as repair and reuse, have been exhausted and the product has reached the end of its life, it returns via the FREITAG take-back service to the open-loop material cycle and can be mechanically recycled into reusable raw polyamide 6.
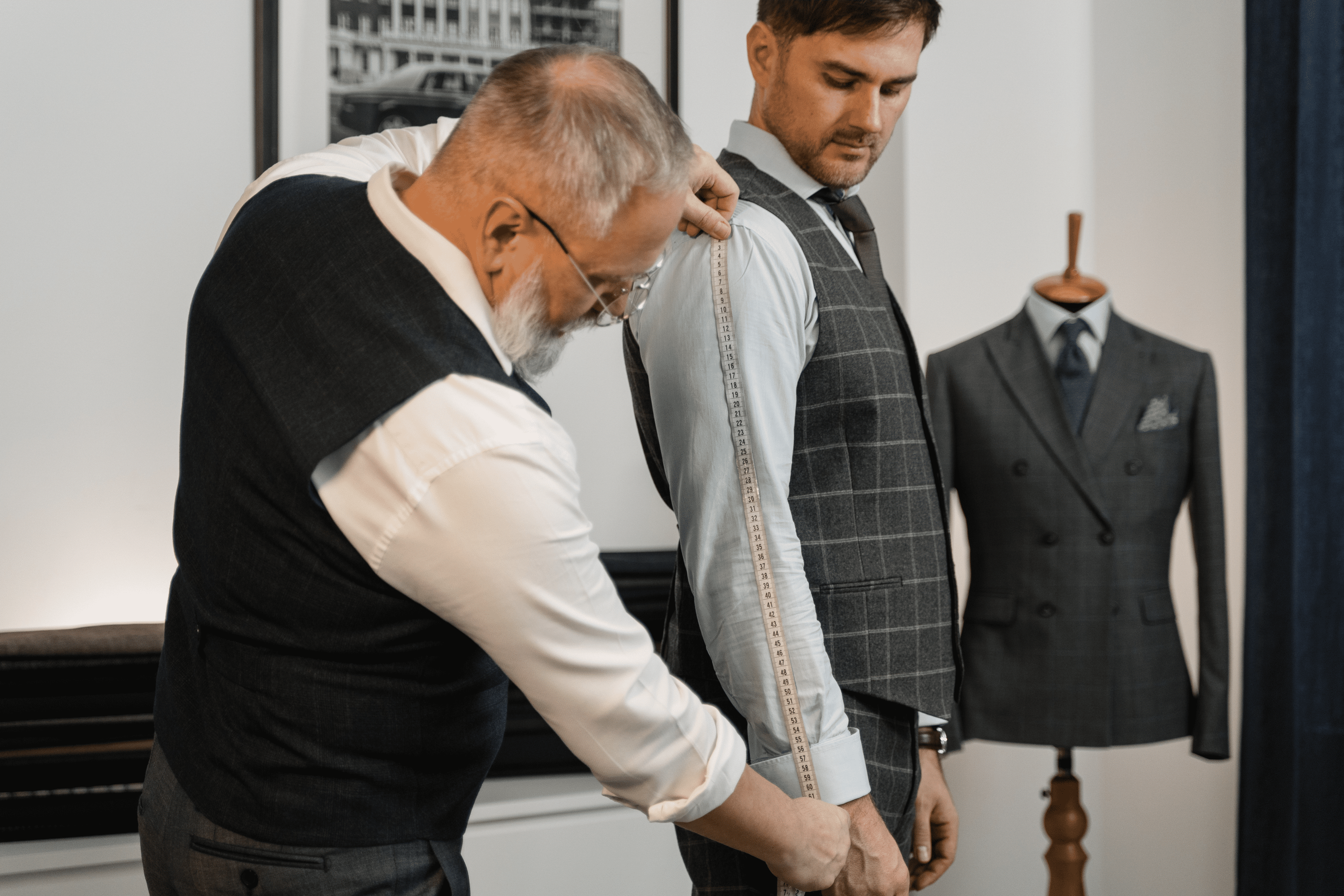
Mechanically recycled
While there are small components like adhesive spots for lamination and printing ink for the inner label that are not made of PA6, and glass fibers are used to reinforce the zipper slide, the amounts of these materials are minimal. As a result, the bags can still be mechanically recycled. At KATZ Aarau, a plastics technology platform in Switzerland, complete prototypes were shredded in a granulator and then transformed into high-quality PA6 granules, therewith proving that the process works.
The first 1500 units of the backpack are expected to be available in spring 2024.