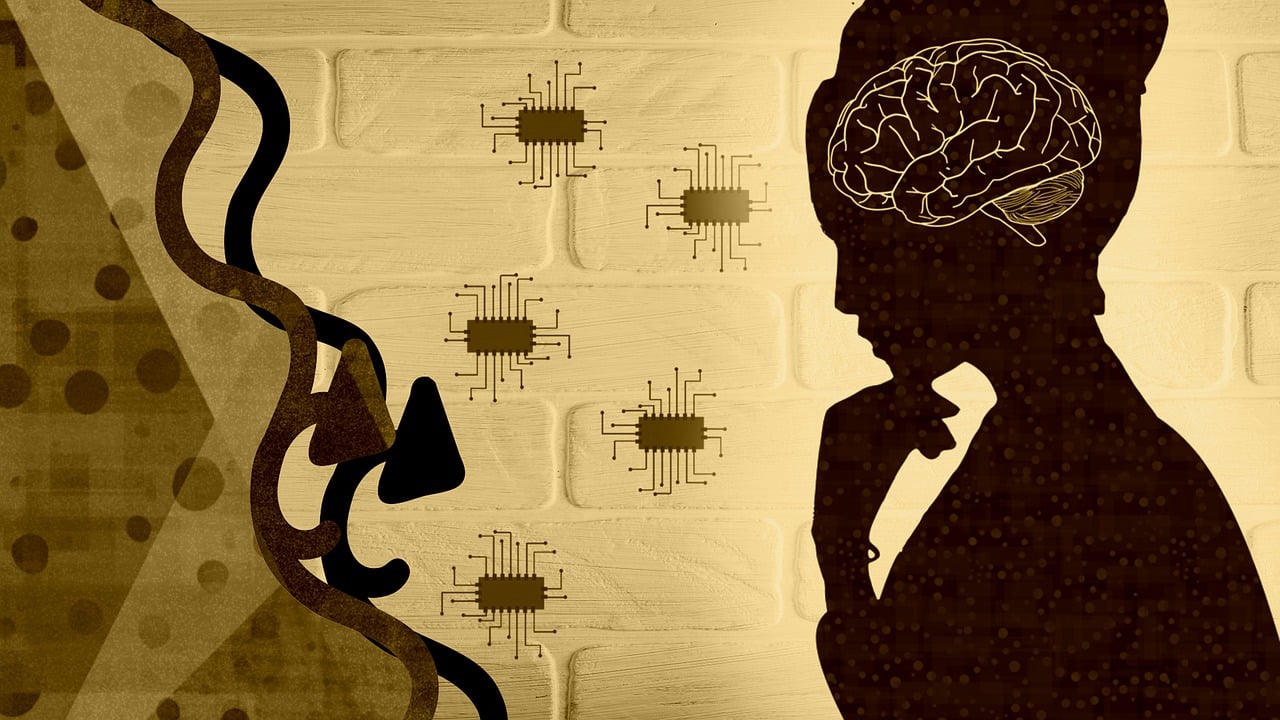
In an ever-evolving world, we are always coming up with new ways to do things. Innovation is important in the manufacturing world to stay ahead of competitors and embrace the change of new technology and trends. We collected some innovative manufacturing examples.
3D printing
Although it can seem like something from a sci-fi film, 3D printing has been in the manufacturing industry for around 40 years. Manufacturers mostly use these printers for prototyping, but more and more also for the ‘real work’. It is a cost-effective way for designers to test new items. It also gives them the ability to produce products on demand rather than manufacture and store them.
3D printing has transformed the expensive process of tooling. Earlier it used to take manufacturers months to create fixtures, molds, and jigs which are needed for mass production of huge equipment. Manufacturers would often depend on these to come from companies overseas. With 3D printing, this can happen on-site, saving both time and money. 3D printing has now become an integral part of the automotive and aerospace manufacturing industries.
Internet of Things
Although it is pretty common now, the Internet of Things has been at the top of manufacturing innovations year after year. IoT is the connection of devices within an internet infrastructure. It has given manufacturers the ability to make more informed decisions as IoT uses live data. Manufacturers are able to reduce costs, improve efficiency, improve safety, and much more.
The pandemic has shown that this technology is even more important than ever, as it allows for remote monitoring and access and has predictive abilities as well. Due to safety reasons, many jobs cannot be carried out in person, and IoT has opened a whole new world where that no longer needs to be the case. This technology allows manufacturers to monitor the performance of equipment remotely and even identify issues before they occur. Technicians also have more understanding of the problems at hand and can come up with solutions even before they arrive at the site, which leads to an increase in efficiency.
GD&T
The manufacturing process relies heavily on GD&T definitions due to its ability to verify parts directly for inspection and reporting. This is a system of symbols, definitions, and rules utilized by engineers to communicate their design through drawings and computer-generated models. It has now become an integral part of the manufacturing process in many places. This is because Geometric dimensioning and tolerancing (GD&T) is supported by both national and international standards that allow functional dimensioning and clear communication design requirements.
Only ten years ago the process of verifying the quality, source and finished parts would have taken hours and was usually impractical. Now, this process takes just a few minutes.
AR + VR
Augmented reality and virtual reality have become a huge asset in the era of COVID-19. This technology has enabled technicians to provide assistance remotely. AR and VR devices can be sent to customers and the technicians can walk them through the repairs or troubleshooting.
For manufacturers, this presents a unique opportunity. Previously, many customers were afraid to use these types of devices and preferred the help of a technician in person. However, due to the current circumstances, a lot of people are opting for this technology. Manufacturers have been able to create new processes with the goal of making these permanent. Both customers and technicians benefit from this as it means reduced health risk and manufacturers benefits by being able to explore new ideas.
ERP
Enterprise Resource Planning has become an integral part of many manufacturing companies. This is because ERP has the ability to streamline processes. ERP does this automatically by providing accurate live information. The pandemic however has altered how manufacturers use ERP. Many now layer agile applications on top of the current ERP systems, rather than having ERP do everything.
There are various options available to transition into using this technology or modifying it to suit the current needs. Some choose to DIY it however this can end in disaster if troubleshooting is needed down the line. Industry experts or implementation experts can also be called in. The industry experts tend to be large firms whilst the implementation experts are smaller firms but offer more personal support.
As the world still reels from the shock of COVID-19, industries all around the world have had to rethink their current processes and strategies. The manufacturing industry has also been affected, but it has also provided new opportunities for innovation and out-of-the-box thinking. In order to survive this era and the aftermath, the industry will need to embrace new technology and innovative change.